一款背包塑料扣模具的設計與加工
2021-4-27 來源: 廣東東莞理工學校 作者: 陳瑞兵
摘要 : 本文根據該背包塑料扣的結構特點 與生產要求,較為詳細地介紹了塑件的成型工藝 方案 ; 包含塑件的工藝分析、型腔排布、分型面 的選擇、模仁的加工方法及參數分析。同時探討 如何有效降低成本和縮短生產周期。
關鍵詞 : 分析、分型、鑲塊、參數
1.引言
隨著模具行業的發展,市場競爭日趨激烈。 縮短模具的生產周期并降低生產成本已經成為每 個加工企業的追求目標。背包塑料扣由六個小塑料 件組成,如果把每件分開制作,就需要六套模具才 能完成,既加大了生產成本和生產周期,也達不到 客戶的要求。故采用六件一套模的方式加工。
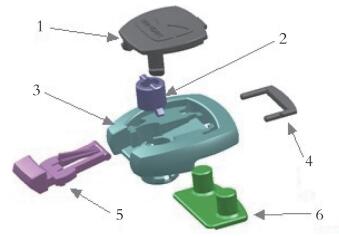
圖 1 產品三維裝配圖
1. 塑件面蓋 2. 連接件 3. 基座 4.插銷 5. 固定插件 6. 固板
2.塑件工藝分析
塑件結構及裝配情況如圖 1 所示,材料是 ABS,收縮率為 5‰ 。因六個塑件有裝配關系, 故外表面要求光滑平整,不得有扭曲、飛邊、毛刺、 氣泡、缺膠等注射成型缺陷 ; 這樣就增加了以下 設計及加工難度。 1) 塑件形狀各異、大小不一,且有許多通 孔,這樣就要考慮塑件在模具中如何合理分布。 固定插件和連接件組合后插入基座內,如圖 2(a) 所示。
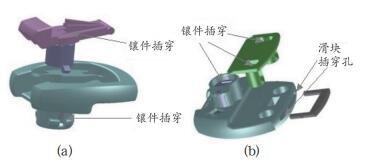
圖 2 組合裝配示意圖
2) 因為固板和插銷都要從兩個不同方向插 入基座配合,基座兩邊的孔設計方式如圖 2(b) 所示,采用前模碰穿后模加鑲件的機構。由于基 座側面是固定塑件的兩個插穿孔,必須設計滑塊 機構 ; 設計制作滑塊時,要考慮滑塊脫離塑件后 塑件對滑塊的包緊力是否過大,會否造成塑件變 形、損傷等情況。因插穿孔是扁平型,并且是出 兩件產品,出于節省材料并降低加工及裝配難度 考慮,把滑塊拆分為兩個部分,前面插入模芯部分以螺絲固定。這樣在加工及裝配過程中,只要 保證兩部分各自相配合便能達到要求。
3.塑件排布與分型
3.1 型腔排布
根據產品要求對模具的結構綜合考慮后,選 擇模仁鋼材為 718,該鋼材硬度為 HRC57-60, 經過熱處理后氮化層具有組織致密、光滑等特點, 模具的脫模性及抗腐蝕性能高,使用壽命可達到 100 萬次以上。 設計尺寸為 260*170mm,采用 6 模 2 腔 來排布,如圖 3 所示。
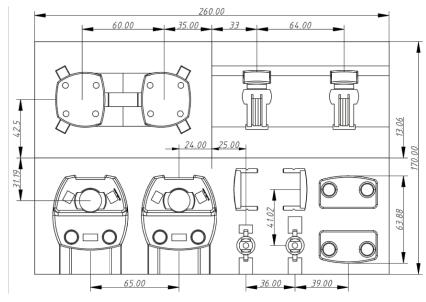
圖 3
模具的型腔數目確定后,接著便設計型腔的 布局。主流道設于前模的中心軸上,至于分流道 出于多方面考慮應該滿足如下要求 : 盡量保證各 型腔的充模壓力相近,充模時間大致相同,并且 能均勻補料,這樣才能保證塑件的尺寸及形狀精 度,同時也能保證其力學性能。故采用以上排布 方式,既解決了充模問題,又可優化模具結構。
3.2 塑件分型
根據塑件幾何形狀等特點,開模時盡量使塑 件留在后模,有利于側面分型和抽芯。該模具采 用 UG 模具設計軟件進行分型,首先做好分型面 然后用抽取幾何體這個功能,選擇區域的方式把 整個前模和后模的面提取出來 ; 接著再跟分型面 結合成一個整塊的片體,用該片體去切割鑲塊實 體便得到前、后模仁 ; 具體如圖 4 所示。 根據型腔排布確定模具的前、后模非常重要, 因為其決定了型腔的朝向、進料方式、進料位置、擺放位置等塑料模具的設計要點。選擇前后模可 采取如下原則,產品外觀要求很高的一般作為前 模,反之則作為后模。經分析對六件塑件采用以 上最合理的分型方式最便于后期加工。
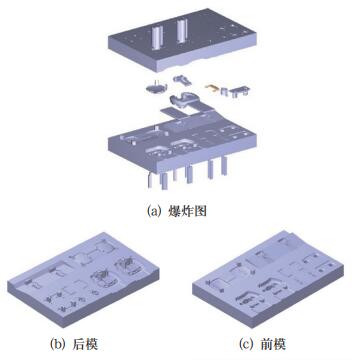
圖 4
4.型腔與型芯制作
分型完成后型腔與型芯是一個整體,由于固 定插件的分型面有斜面和角度,如果采用 CNC 直接加工則要設計多個銅公進行清角,這樣在材 料的的選用上就加大了成本,同時也加大了工期, 故采用拆分型芯方式。分拆后用線切割進行加工, 為了節省材料、縮短加工時間及維護方便,把前 后模各分拆成三塊,這樣就要解決以下難點。 1) 前后模的分型面采用分拆方式加工,加工 時要采取合適的加工工藝。 2) 多處的分型面設計采用了前后模碰穿結 構,在前后模型芯上形成了多個凸凹臺,加工較 為困難。3) 加工時前后模型芯前部缺口處很難進行 清角,可采用小直徑刀具,盡可能清除加工余量。 加工完畢后,可進行人工打磨或設計小銅公進行 清角。4) 模具型腔中間的臺階孔碰穿位在前后模 型腔中形成了多個孤島,孤島和前模型腔直角相 交,很難清角加工,這里采用了線切割鑲件加工。
表 1 前模加工參數
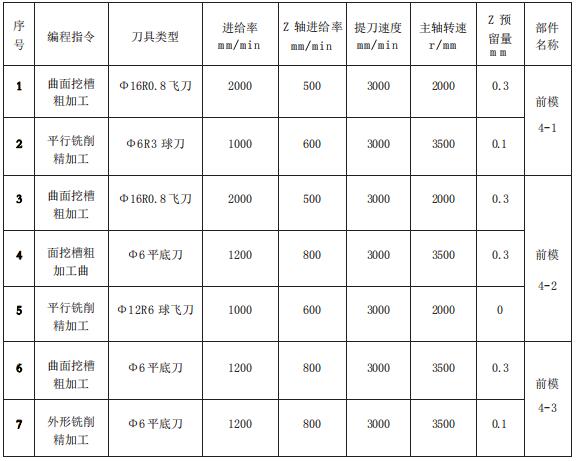
表 2 線切割加工參數
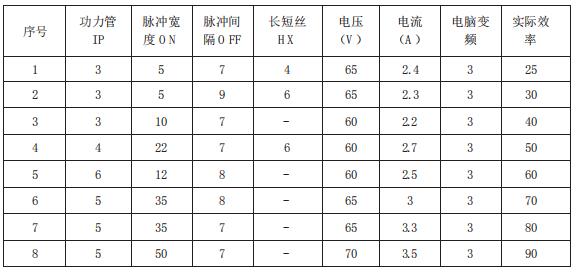
5) 前模要設計多個銅公進行清角,為節約 成本,各款銅公只設計加工了一個銅公(精公), 這樣前模型腔的精加工余量盡可能小,以減少銅 公的損耗,如圖 5 所示。
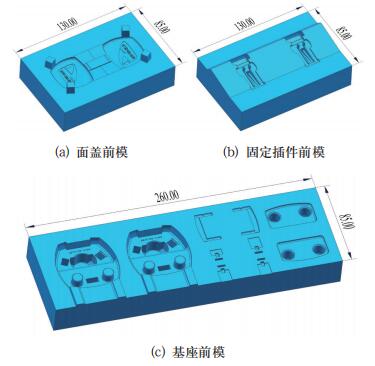
圖 5
4.1 前模型腔加工
首先使用普通銑床和磨床加工兩塊 130*85*40mm 鋼料,分別用于圖 5(a)和圖 5(b), 再 加 工 一 塊 260*85mm 為 圖 5(c) 使 用。 圖 5(a)為專用塑膠扣的中心面蓋,上面 有兩個倒扣,一般需要做斜頂才能完成。這里采 用更合理的插入式脫模斜度方式加工。如圖 5(a) 所示 4 個方形柱子,用來插入后模,三面都要封 膠,所以這里的加工精度要求較高,加工時要留 0.1mm 的余量做配模時用。倒扣留在后模型芯 用電極來加工完成。使用 MasterCAM 來編程, 用數控銑或加工中心進行加工,用 Φ16R0.8 鑲 方合金刀粒圓鼻刀,進給率 1200mm/min,下 刀速率 500mm/min,抬刀速率 3000mm/min, 主軸轉速 S=2000 轉 / 分。用 3D 曲面挖槽刀路 對前模型腔曲面進行粗加工。采用相對尺寸,最 小加工深度和最大加工深度都設置成 0.2mm, 加工余量為 0.3mm; 采用螺旋下刀,下刀處為前 模型腔的中心,切削方式選擇環繞方式 ; 加工完 成后需要做電極加工。

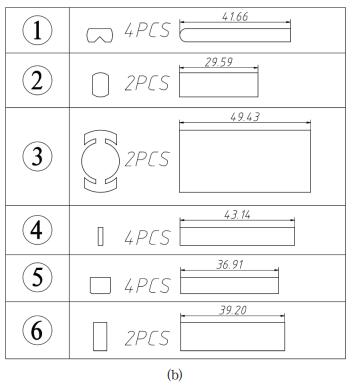
圖 6
圖 5(b)固定插件前模同樣采用如上方法, 用 Φ16R0.8 鑲方合金刀粒圓鼻刀粗加工,再用 Φ12R6 鑲球頭合金刀粒圓鼻刀(球飛刀)進行 精加工完成。(也可使用線切割加工分型面)后 用 Φ4 銑刀對型腔開粗,單邊留 0.3 余量。具體 加工參數如表 1 所示。 圖 5(c)基座前模,先鉆線切割孔,再用 Φ6 銑刀對型腔進行粗加工,單邊留 0.3mm 余量。 型腔要做多個電極和線切割鑲件切割加工,如圖 6 所示。圖 6(a)為線切割加工的關鍵尺寸標注, 所有需要線切割加工的位置先用鉆床或銑床鉆 孔,以作線切割穿絲孔用。切割孔位數量與鑲件 數相同,采用線切割四邊分中加工,按所示尺 寸加工型腔與型芯,要求加工完成后的鑲件與 型腔、型芯孔的配合為過盈配合,公差范圍為 0.01~0.02mm。 圖 6(b)為線切割所需鑲塊數量,①號處 是后模插穿位置鑲件,共 4 件 ; ②號是后模插穿 位置鑲件,共 2 件 ; ③號處是后?;宕┪恢?鑲件,共 2 件 ; ④號處是前模插穿位置鑲件,共 4件;⑤號處是前模基座插穿位置鑲件,共4件;⑥ 號處是前?;宕┪恢描偧?2 件。具體線 切割加工參數如表 2 所示。 線切割加工難點是鑲件的表面光潔度要求 高,這樣加工時參數的選擇就要求合理。在功力 管、脈沖寬度和間隔之間要根據機床當時的情況 而定,適時調整。 圖 6(a)型芯上總共分布四件產品,較為 復雜的是塑料扣基座,其包含有滑塊和插穿,其 三件則比較簡單。
4.2 后模型芯加工
先用普通銑床和磨床加工兩塊 130*85*35mm 鋼料,分別用于圖 7(a)和圖 7(b),再加工一塊 260*85mm 圖 7(c)使用。 當然前、后模仁鋼料一般是一起加工好的,只是 鋼料的厚度不一而已。 圖 7(a)后模仁先采用數控銑加工,采用 Φ12 R0.8 鑲方合金刀粒圓鼻刀粗加工,再用Φ12R6 鑲球頭合金刀粒圓鼻刀進行精加工。由 于倒扣出在后模,插穿孔要和前模方柱碰穿,精 度要求較高,加工有一定的難度。其工序為先 用 Φ4 合金刀開粗,單邊留 0.3mm 余量,再做 電極用火花機加工后進行人工打磨即可達到加工 要求。由于倒扣膠位出在碰穿位下方,直徑小的 刀具無法加工,故要做兩個電極加工 : 一個粗銅公單邊留 0.2mm 余量,一個精銅公留 0.08mm 余量,分別進行電火花加工。 具體后模加工參數如表 3 所示。 圖 7(b)后模型芯中間有兩處要插入前模中, 同前模型腔加工基本相同。先用 Φ16R0.8 鑲方 合金刀粒圓鼻刀,進給率 1200mm/min,下刀 速 率 500mm/min, 抬 刀 速 率 3000mm/min, 主軸轉速 S=2000 轉 / 分。用 3D 曲面挖槽刀路 對前模型腔曲面粗加工。采用相對尺寸,最小加 工深度和最大加工深度都設置成 0.2mm。加工 余量 0.3mm。采用螺旋下刀,在前模型腔的中 間下刀,切削方式選擇環繞方式。粗加工后再用 Φ12R6 鑲球頭合金刀粒圓鼻刀進行平行銑削精 加工 ; 最后用 Φ6 平底刀進行塑件膠位的粗加工, 加工余量 0.3mm,完成后需要做電極加工。 圖 7(c)后模型芯上有四個塑件產品,最 難加工的部件是塑件基座,首先采用線切割加工 凸出區域,如果整體式加工,CNC 加工的工作 量就很大,模仁材料也要加厚購買,清角比較麻 煩,且尖角過多也不便于加工,如果用多個電極 清角則增加了加工成本和時間,所以考慮采用線 切割方式加工該藍色區域。用 Φ10 合金刀 3D 曲 面挖槽刀路對前模型腔曲面粗加工,接著用 Φ4 平底刀等高外形清角粗加工,后續用 Φ6R3 合金 球刀進行平行銑削精加工,留余量 0.3 mm 做電極加工。因鑲件上有臺階要加工,故電火花加工 完成后,裝上鑲件再進行臺階加工,且臺階處也 要做電極清角。
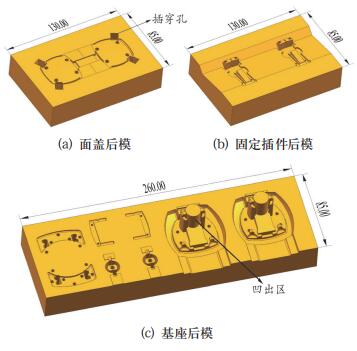
圖 7
表 3 后模加工參數
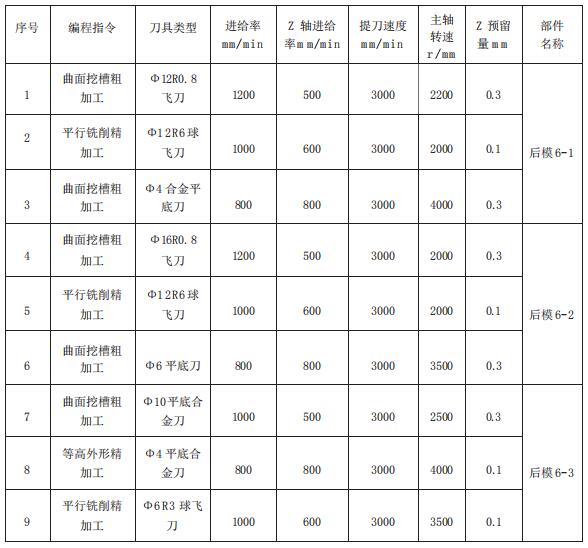
后模型芯加工完成后,經過后期制作便完成 了整套模具的加工。加工完成后的模具成品圖如圖 8 及圖 9 所示。
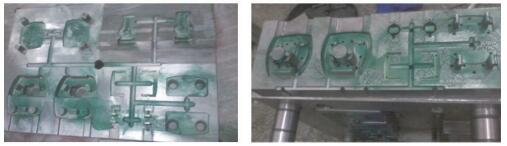
圖 8 前模 圖 9 后模
5.結束語
這套模具經生產驗證,塑件質量達到設計要 求??v觀該模具的設計及制作過程,可見一套模 具的開發首先要對塑件結構進行分析,然后提出 幾種可行的成形方案,在確保質量、減少投資的 前提下,根據生產要求選擇最優方案 ; 同時也要 對模具零件的加工工藝進行推敲,并對模具后期 維修的便利性提前考慮。
投稿箱:
如果您有機床行業、企業相關新聞稿件發表,或進行資訊合作,歡迎聯系本網編輯部, 郵箱:skjcsc@vip.sina.com
如果您有機床行業、企業相關新聞稿件發表,或進行資訊合作,歡迎聯系本網編輯部, 郵箱:skjcsc@vip.sina.com
更多相關信息