鈦合金舵芯高效加工技術研究
2021-11-2 來源:首都航天機械有限公司 作者:戰祥鑫,張玉強,李涵,蘇曉,楊春月等
摘要: 舵芯組件采用難加工材料鈦合金制造,整體由舵芯骨架與舵芯蒙皮焊接而成,外形為一種靠空間復合面組成的楔形結構。針對多個型號舵芯加工過程中反復裝夾、找正、測量與切削導致加工周期長和加工效率低等問題,通過對加工方法進行機理分析,從設計通用性較強的組合工裝、完善加工流程以及合理選用刀具參數三方面出發,進行高效加工技術研究,大大縮短了舵芯產品的加工周期,進一步提升了產品加工質量穩定性。
關鍵詞: 鈦合金; 空間復合面; 組合工裝; 高效加工技術
1、引言
舵芯是航空航天飛行器結構中的重要零件,在控制飛行姿態上起至關重要的作用,因此,其加工精度直接影響產品飛行的精度。鈦合金舵芯憑借輕質化、高剛度的優勢被廣泛應用于航空航天領域。但是由于該材料硬度高、熱傳導率低,且產品結構復雜、不易裝夾,在加工過程中局部余量去除大且易變形,難以保證較高的精度要求。為保證零件的加工精度,傳統工藝采用反復加工的方法,導致其加工工序多、生產周期長,無法滿足生產需求。
針對上述問題,本文從加工流程、工裝和刀具等方面入手,優化原有的舵芯加工工藝,通過實際生產驗證優化后的工藝方法大幅縮短舵芯的加工周期,成功解決了多項綜合性難題,進一步提高了零件的加工質量穩定性。
2、 結構特點和加工難點
某型號舵芯產品零件如圖 1 所示。舵芯結構形狀特殊,是一種復雜的結構件,由舵芯骨架與舵芯蒙皮焊接而成,內部骨架上分布著一系列環向和輻射狀的加強筋。兩側的蒙皮是由兩個不同角度組合而成的復合型面,同時舵面兩端厚度差大,整體呈楔形結構,對裝夾定位造成了極大的困難 。
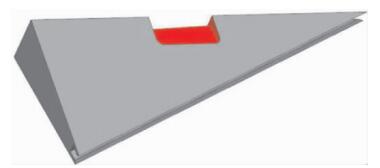
圖1 舵芯結構
鈦合金舵芯產品中骨架材料為鑄造 ZT4 鈦合金,蒙皮材料為鍛造 TC4( Ti-6Al-4V) 鈦合金,盡管鈦合金存在諸多優點: 包括高比強度遠超過強度高而密度大的鋼,密度小但強度較低的鋁合金; 抗腐蝕性強,多數情況下不需要附加表面保護層; 耐熱性遠高于鋁合金,工作溫度范圍較大。但鈦合金產品給機械加工帶來極大地挑戰: 熱傳導率低,僅15. 24W/( m·K) ,加劇刀具磨損; 彈性模量低,載荷作用下發生變形后產生極大的回彈,造成讓刀現象;化學活性高,親和作用大,在切削溫度高時,切削及被切削表層與刀具材料咬合而產生嚴重的粘刀現象,引起劇烈的粘結磨損 。
舵芯的加工精度將直接影響飛行器的飛行精度,因此對產品配合安裝面的加工精度有較高要求:兩側斜面的平面度和對稱度要求較高,下陷尺寸公差為 0. 01 ~ 0. 025。加工過程中局部去除余量大且
不均勻,切削熱不易散出,原材料殘余應力較大,易變形; 同時受零件厚度不均、裝夾不易和薄壁網格結構的影響,切削時易振動,造成打刀現象,難以保證舵芯的高精度加工要求。
3、工藝措施優化
針對上述加工難點,從全流程對產品輔助工裝、加工流程及刀具切削參數進行了三方面的改進。
3.1工裝優化
由于舵芯產品的外形面為復合結構,在銑削、陷時無法通過外形復合面來進行定位,傳統工裝在設計時考慮通過虎鉗夾緊利用零件下陷定位,如圖2 所示。
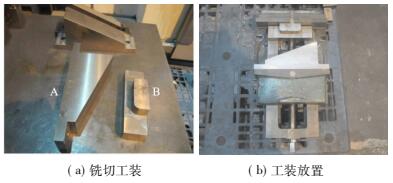
圖 2 傳統輔助工裝
在加工下陷特征的過程中,需保證兩側的對稱度,每次粗加工完成后都要反復測量外形不同位置的對稱度并重新裝夾找正。零件每裝夾一次,銑切工裝 A 也需要重新安裝一次,以保證與零件斜邊一致,整個加工過程中零件和工裝裝夾次數較多,過程繁瑣,加工周期長。同時,不同型號產品對應的舵芯角度不同,在實際生產中需要針對不同角度設計各自專用的工裝,導致輔助工裝的通用性較差,無法進行互換,降低生產成本。
基于上述問題,從零件結構特點出發,設計了如圖 3 所示的舵芯批產通用組合工裝[4,5]。定位塊兩個面和舵芯兩個面相互貼合,夾具體底面和舵芯底面貼合從而實現舵芯的快速定位。舵芯的夾緊主要是通過楔形壓緊塊和固定塊共同完成的,通過定位銷將固定塊定位于夾具體上,并利用壓板完成固定塊的固定,將楔形壓緊塊沿固定塊導槽放入,楔形壓緊塊另一面和舵芯實現緊密貼合,通過螺栓和螺母將壓緊塊連接到夾具底座上。由于舵芯與楔形壓緊塊接觸面為斜面,受力分解得到三個方向的作用力,分別指向三個定位面,從而實現舵芯的壓緊。改進后的工裝見圖 4。
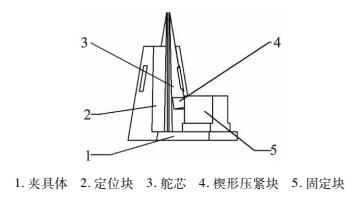
圖3 舵芯組合工裝結構
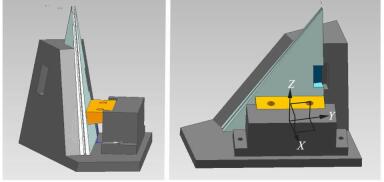
圖 4 改進后的工裝
工裝結構主要由定位機構、夾緊機構和輔助支撐機構三部分組成,結構設計緊湊,操作方便,可靠性高。和傳統的工裝相比,改進后的工裝不受零件復合面及斜邊角度的限制,一套工裝可完成多個型號舵芯的加工,通用性強,能滿足多個型號舵芯批量生產的需要。
3.2 加工流程優化
舵芯產品是復雜結構件,在加工兩側下陷特征時,由于余量較大,精度要求高,需要進行粗銑和精銑,使用傳統工裝定位,邊加工邊測量校對,整個產品需完成 20 道工序,多次裝夾找正導致整個產品生產周期長,加工效率低。而且過多的人為裝夾、拆卸等操作使加工誤差增大,降低了產品的一次加工合格率,經常需要返修,浪費大量人工和機床成本。
在新輔助工裝的配合下,取消加工兩側下陷時的粗銑和精銑之分,在一次裝夾狀態下利用五軸設備的 C 軸回轉功能完成對兩側下陷特征的精加工。改進后的方法不需要通過原有的兩次協調來保證對稱度,只需要通過機床 C 軸的精度來保證對稱度,排除人為誤差,保證產品一致性。合并傳統流程中的多道重復工序,最終將加工流程優化為如圖 5 所示的 11 道工序 。
3. 3 刀具及切削參數選擇
刀具的選擇不僅影響到數控加工的效率,還直接影響零件產品的質量。針對鈦合金這種難切削材料,大多采用 PCBN( 聚晶立方氮化硼) 刀片、金剛石刀片、陶瓷刀具和硬質合金刀具等,都具備較高的硬度、耐磨性、耐熱性及足夠的強度和韌性。但是,前三種材料的刀具價格昂貴,且在加工薄壁零件時易產生振動現象,綜合考慮經濟性和切削穩定性等情況,最終選擇 Y330( K30) 的硬質合金銑刀為刀具材料,其屬于鎢鈷類硬質合金,亞細晶粒合金強度高韌性好、耐磨性適中且通用性強,適用于精加工高溫合
金及鈦合金等 。
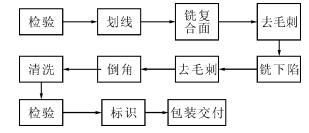
圖 5 優化后的加工流程
由于鈦合金材料自身的特性,使刀片刃口極易磨損,刀具磨損后會增大刀 - 件摩擦力,不僅影響工件表面粗糙度質量,還會使切削溫度升高,導致零件變形,大大降低了刀具的壽命[9]。刀具磨損后需立即更換新刀片,易造成浪費。為了進一步提高加工效率,節省成本,采取對磨損刀片的重新刃磨方法,將同一把刀體上安裝的若干刀片同時刃磨,保證刃口幾何尺寸及精度的一致性,從而使得磨損后的刀片再次利用。通過大量試驗確定的加工刀具參數見表 1。
表 1 加工刀具參數
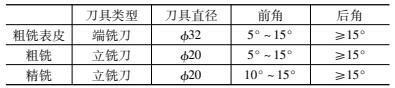
采用順銑可以最大限度降低加工切屑瘤對銑刀的破壞以及切屑與切削刃的焊合程度,使用大量水溶性油以及氣相亞硝胺型防銹液作為切削液可以達到較好的冷卻效果。考慮到零件內部的薄壁網格結構,切削過程中沖擊力較大時易產生振動造成打刀現象。經過多次試驗得到鈦合金切削參數見表 2。
表 2 鈦合金切削參數
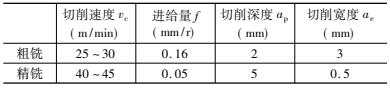
4、 結語
針對多種型號舵芯產品加工過程中的難點,基于加工全流程設計出了一種通用性較強的組合工裝,節省了大量裝夾、找正和測量時間; 針對鈦合金內部薄壁網格結構的焊接件,優化工藝流程,合理選用刀具參數,有效提高了舵芯批生產效率,縮短生產周期,降低了工人的勞動強度,實現了產品高效、高精度的生產。結果表明,該方法不僅能夠解決舵芯產品生產面臨的諸多難題,而且對類似產品工藝流程設計具有重要參考價值,對新型產品的研制及批產提供了借鑒。
投稿箱:
如果您有機床行業、企業相關新聞稿件發表,或進行資訊合作,歡迎聯系本網編輯部, 郵箱:skjcsc@vip.sina.com
如果您有機床行業、企業相關新聞稿件發表,或進行資訊合作,歡迎聯系本網編輯部, 郵箱:skjcsc@vip.sina.com
更多相關信息