曲軸粗車刀崩刃問題淺析
2023-5-8 來源: 上汽通用五菱汽車股份有限公司重慶分公司 作者:張曉剛 許雷明
車刀崩刃是車削加工過程中常見的問題,考慮到曲軸溝槽加工表面要求高、重復定位精度等因素,崩刃件一般無法返工,且目前無其他手段監控崩刃情況,僅能通過目視判斷,造成曲軸的批量報廢,刀具損壞、CPU 增加等情況,存在質量風險。粗車刀崩刃影響因素多樣,我司前期通過人、機、料、法及環多方向分析驗證鎖定設備精度、加工參數、余量分配三點關鍵因素,本文通過對前期攻關過程進行總結,分析關鍵因素對粗車刀崩刃問題的影響,找到癥結,攻克崩刃問題。
生產現狀
某公司一條年產 30 萬件四缸鑄鐵曲軸生產線上,生產 N15/N12 兩種機型,因兩種機型皆存在崩刃問題且表現類似,下文以 N15 機型為例進行分析。OP20 工位負責曲軸主軸頸、法蘭盤、芯軸端及鏈輪端的粗、精加工,采用的裝備是配有自定心中心架的雙刀盤型 5 軸聯動的德國產 Boehringer 車拉機床。
生產中左刀盤負責 A4/A5/HUB/ 法蘭端面、外圓面及溝槽的加工,右刀盤負責 A1/A2/A3/ 鏈輪 / 芯軸相應特征的加工。軸徑外圓粗車刀(以下簡稱粗車刀)分為 A1 粗車刀、A2/A3 粗車刀、A4/A5 粗車刀。加工過程工件姿態如圖 1 所示,面對機床觀看法蘭側靠左,芯軸側靠右,故下文中加工法蘭側粗車刀命名為左粗車,芯軸側粗車刀命名為右粗車。
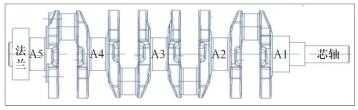
圖 1 加工過程姿態、軸徑命名示意圖
2020 年整年 OP20 工位粗車刀崩刃 59 次,生產過程月均崩刃次數 5.4 次 / 月,相比較于2016-2017 每月平均崩刃頻次為 1.1 次增加了 4.3次 / 月,崩刃頻次明顯變多。統計 2020 年整年粗車刀崩刃于各軸徑的分布情況,繪制如圖 2 所示的柏拉圖。由圖可知 A2/A3 粗車刀崩刃占比最大,A2/A4 左粗車和 A4/A5 左粗車崩刃次數占全年粗車刀崩刃次數的 76.72%,是 OP20 車拉工位粗車崩刃問題的癥結所在。在其他問題不增加的情況下,解決 A2/A3 左粗車及 A4/A5 左粗車問題后,OP20 工位粗車刀崩刃頻次將降低為 1.27 次 / 月,與 2016~2017 年崩刃頻次基本持平。
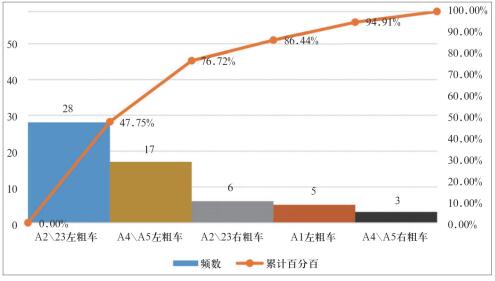
圖 2 崩刃分布
車拉加工工藝曲軸車拉加工主軸頸(A1 無開槽加工)主要工步包含開槽刀加工、左右粗車加工、左右溝槽加工和拉刀修整加工,加工部位及刀具結構如圖 3 所示,整個加工過程中,粗車的粗車刀加工余量最大,需加工側壁和粗車軸徑外圓面。
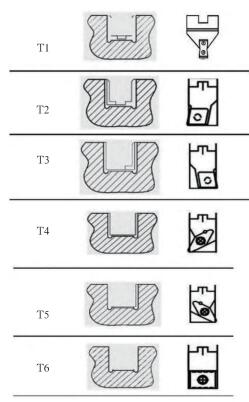
圖 3 工位刀片介紹
崩刃產生的原因
曲軸主軸徑外圓加工粗車刀崩刃原因主要為方法和機床兩個方面 : ①在方法方面包括機床加工參數、各把刀具間的余量分配等因素 ; ②在機床方面包括刀盤垂直度、頂尖圓跳動等設備精度問題和設備原點變動等因素。
設備精度對崩刃問題的影響
對 OP20 車車拉設備刀盤垂直度、卡盤圓跳動進行檢查,檢查結果見表 1。
表 1 設備精度檢查結果
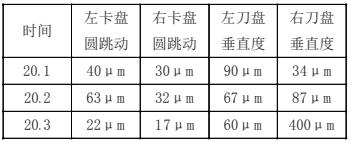
供應商推薦刀盤垂直度及卡盤圓跳動小于20 μm,檢查結果有明顯超差情況,結合設備結構分析,刀盤垂直度、卡盤圓跳動會導致刀片加工過程中局部切削余量變大,瞬時加工應力增加引發崩刃。團隊對設備精度進行調整后,調整過程及精度變化見表 2。調整 OP20 三臺設備刀盤垂直度、卡盤圓跳動至≤ 20 μm,跟蹤生產一個月累計崩刃 4 次,措施有效,精度對問題解決貢獻率為 :1-[4( 次 / 月 )/5.4 次 / 月)]=26%。
表 2 調整前后進度對比
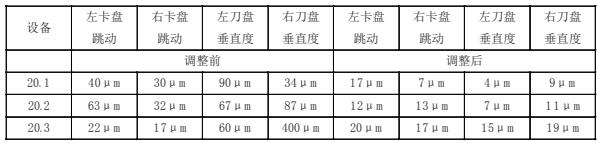
表 3 粗車刀 Z 向加工余量
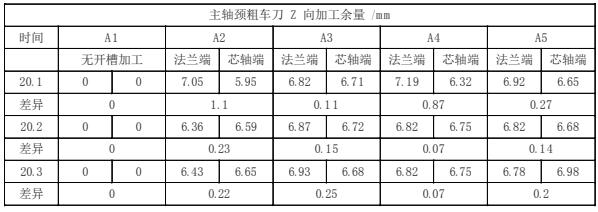
加工余量對崩刃問題的影響刀片的加工余量(圖 4)直接關系到加工過程中刀片受熱、應力變化。結合上文介紹的加工工藝,開槽刀的加工深度、軸向加工位置會影響左右粗車刀的加工余量,粗車刀和拉刀(最終尺寸加工刀)的余量分配也直接影響了粗車刀的加工余量。
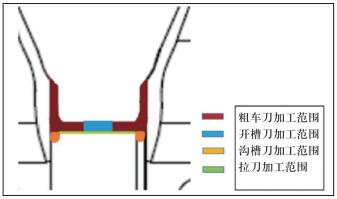
圖 4 工位刀片加工余量示意圖
結合毛坯(圖 5)及 OP20 成品尺寸計算和測量各個軸徑左、右粗車刀在軸向(Z 向)和徑向(X 向)的加工余量如表 3、表 4 所示。
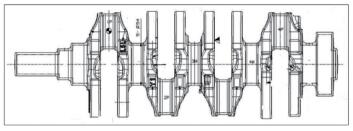
圖 5 產品毛坯尺寸
表 4 粗車刀 X 向加工余量
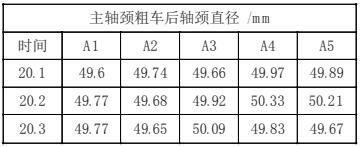
我司通過多次測量收集粗車刀軸向、徑向的加工余量發現 :
(1)OP20.1 設 備 主 軸 頸粗車加工 Z 向余量,A2 左粗車加工余量比右粗車加工余量大1.1mm,A4 左粗車比右粗車大 0.85 mm,其他軸徑最大差異皆小于 0.3 mm,與上文統計信息中左粗車崩刃頻次大于右粗車現象相呼應。
(2)觀察主軸頸粗車后軸頸直徑,三臺設備部分軸徑完成粗車加工后直徑小于 49.7 mm,已經達到 OP20 工位成品尺寸要求(49.6±0.1)mm,并且主要集中 A2/A3 軸徑,與上文統計的粗車崩刃頻次統計相對應。
分析加工程序,主軸徑粗車刀加工毛坯面,將主軸徑從 φ54 mm 加工至 φ49.9 mm(實際加工靠設備原點保證),理論軸 向 加 工 余 量4.1 mm。 拉 刀保證最終成形尺寸,將軸徑由φ49.9 mm 加工至 49.6 mm,理論加工余量 0.3mm。部分軸徑實際加工余量與理論加工余量差異較大,通過重新調整設備原點后解決。
加工余量過大是導致崩刃的直接因素,綜合我司多年的加工情況,極少發生拉刀崩刃情況,故團隊通過多次調整優化將粗車刀加工尺寸由 φ49.9修改為 φ50.2(增加拉刀加工余量 0.3mm),優化后跟蹤粗車刀崩刃頻次明顯好轉。
加工參數對崩刃問題的影響
加工參數主要指切削速度、加工進給,切削速度對刀具壽命有很大的影響,切削速度過高時,導致切削溫度上升,刀具壽命大大縮短 ;相反切削速度過低,切削易產生振動,切削過程中刀具和工件不停敲擊使刀尖產生微小裂紋
和崩刃,刀具壽命縮短。
調整加工參數,在滿足生產節拍的情況下驗證加工參數對粗車刀崩刃的影響。我司多次調整設備加工參數,跟蹤驗證粗車刀崩刃頻次,粗車刀崩刃次數明顯改善,表 5 為參數優化情況。優化設備粗車加工切削速度,G97S1100(1100 r/min)調 整 為 G96 S180(180 mm/min),G96 為恒線速度加工,加工過程中自動調整主軸轉速保證切削線速度不變(多用于外圓直徑加工)。G97 為恒轉速加工,加工過程中主軸轉速一致(多用于端面加工),G97 隨著工件軸徑直徑變小,切削線速度會變低,考慮粗車加工過程將曲軸軸徑由 φ54 mm 加 工 至φ50.2 mm,切 削 線 速度 將 由 186.5 mm/min 降 低 為 172.3 mm/min,下刀位置切削線速度過大,且與毛坯面(氧化層)接觸,加工應力大,易崩刃。參考刀具耐用表要求(線切削速度 Vc ≤ 185 mm/min),采用恒線速加工方式 G96 S180。
表 5 設備加工參數優化
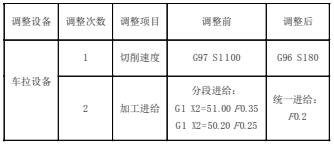
當刀具進給量增大時,刀具與工件之間的接觸面積增大,導致摩擦力增大,從而引起切削力穩態分量增大,增加崩刃風險,故在滿足生產節拍要求的前提下,粗車加工過程中的進給 F0.35、F0.25 降低為統一的進給 F0.20,跟蹤生產崩刃頻次顯著降低。
結論
我司進行曲軸車拉加工工位加工過程中粗車刀崩刃頻繁,比正常加工情況多 4.3 次 / 月。通過人、機、料、法及環分析,鎖定設備精度、加工參數及加工余量,并對其進行優化驗證。最終通過調整刀片余量分配、機床加工參數及調整設備精度將曲軸線 OP20 車拉工位粗車刀崩刃頻次降低為 1 次 / 月以內。為預防問題再發生,優化維修 PM,定期檢查、調整設備精度及原點位置,更新 PCP,要求定期監控OP20 粗車余量并寫入經驗教訓。
投稿箱:
如果您有機床行業、企業相關新聞稿件發表,或進行資訊合作,歡迎聯系本網編輯部, 郵箱:skjcsc@vip.sina.com
如果您有機床行業、企業相關新聞稿件發表,或進行資訊合作,歡迎聯系本網編輯部, 郵箱:skjcsc@vip.sina.com