關于直紋滾壓加工裝置的設計
2017-3-9 來源:齊齊哈爾軌道交通裝備有限責任公司 作者:范俊超
摘要:介紹了一種直紋滾壓加工裝置的設計參數及關鍵技術,并闡述了其結構特點、工作原理、試驗情況及相比傳統工具的優勢等,試驗分析結果表明,該裝置大大提高了效率,提升了質量,到達了設計要求。
關鍵詞:滾壓;直紋;多次成形
1. 滾壓設備現狀
現有的直紋加工方式分為刨床加工、插床加工和滾壓設備等幾種加工方式,其中刨床加工和插床加工效率很低,單件加工耗時長;傳統滾壓設備由固定裝置、滾壓裝置組成,工作時將工件放入固定裝置中固定好,再將滾壓裝置安裝到位,由壓力機壓入,通過滾紋刀具在工件表面滾動使工件變形形成直紋。這種滾壓方式存在以下幾個問題:第一,由于工件外形尺寸誤差,造成一批工件滾壓完成后,直紋深度不一致,有深有淺。第二,當需要增加直紋深度時,將滾壓裝置取下后重新放入工作位置再次滾壓時,由于工件表面已經存在直紋,故無法完全與滾輪上的紋路對齊,造成“雙眼皮”現象。第三,滾壓后的工件在首段和尾段部分,由于與滾輪初期接觸階段工件本身“支撐性”較差,產生了彎曲現象。結構示意如圖1所示。
2. 新型滾壓裝置的結構設計
結合實際加工情況反應出的問題,新型裝置應具備以下特點:①滾壓深度可調整。②能夠實現多次滾壓,多次滾壓時紋路不應改變。③通過改變工藝順序,使工件加工完畢后直紋平整性一致。
(1)滾壓過程
將工件裝入后,通過旋轉調整螺栓使中間楔塊上下運動,進而推動兩側楔塊向左右運動從而調整工件與滾輪相對位置(見圖1中箭頭)。調整完畢后,油壓機進行滾壓,滾壓過程如圖2所示,第一次滾壓結束后,若直紋深度較淺,可用工具繼續轉動調整螺栓到合適位置(此時滾紋刀具位于工件薄壁位置可以很輕松轉動螺栓),再將除底座外的其余裝置整體翻轉180°,以確保工件與滾紋刀具的相對位置不變,用以避免出現“雙眼皮”現象。將裝置放好后進行第二次滾壓,滾壓完成后,可以講工件兩端薄壁部分切除,來保證工件直紋的平整性。
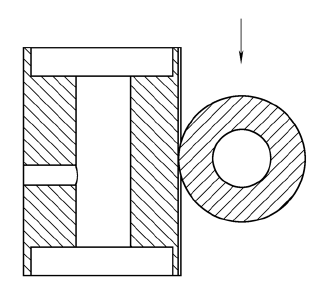
圖1 現有滾壓方式簡要示意
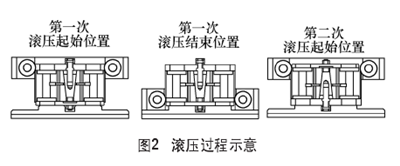
(2)設計理念
使用該裝置滾壓成功的關鍵步驟在于第二次滾壓起始位置,傳統方法存在的問題是第一次滾壓完成時滾紋刀具和工件是分離的,再次滾壓時需將工件重新裝入設備,而新方法則是將其整體翻轉后,在保證滾紋刀具和工件不分離的情況下再次滾壓(設有限位裝置),即保證了不出現“雙眼皮”現象,如圖3所示。
(3)滾輪材料改進
傳統的滾壓方式使用普通材料45鋼制作滾紋刀具,由于滾壓時滾輪受力比較大,滾輪經常損壞,每制作5個左右工件必須更換一次滾紋刀具,導致加工成本上升,加工效率下降。經過多次試驗,最后選用Cr12Mo V作為滾輪的材料,大大延長了滾輪更換周期,每300~400個工件需要更換一次滾紋刀具。
(4)通過該裝置改進工藝順序
傳統的工藝順序,工件滾壓為最后一道工序,無法避免滾壓后帶來的兩端受力不均勻帶來的變形問題,這次我們調整了加工順序,實行滾壓后再對工件兩端進行切除加工的方案,可將多余的變形的部分切掉,保證了滾紋的一致性。
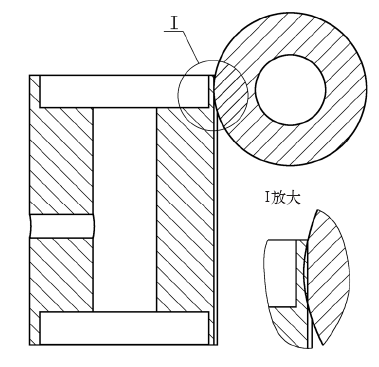
圖3 第二次滾壓起始位置示意
3. 應用前景
目前該裝置已經在我廠大范圍投入使用,各項指標均能達到加工要求。根據該裝置的設計理念,可以逐步推廣至其他零件的加工,以傳統設計方法為基礎,結合creo技術建立模型,利用UG有限元分析思想對該裝置在實際工況進行受力分析,疲勞強度分析等,得出該裝置重要部件在正常工況下的應力云圖和應變云圖,為其安全可靠提供依據。相信該方法在其他加工領域中中可以得到更加廣泛的應用。
投稿箱:
如果您有機床行業、企業相關新聞稿件發表,或進行資訊合作,歡迎聯系本網編輯部, 郵箱:skjcsc@vip.sina.com
如果您有機床行業、企業相關新聞稿件發表,或進行資訊合作,歡迎聯系本網編輯部, 郵箱:skjcsc@vip.sina.com