模具自動化制造技術的應用
2018-11-29 來源:成都普什汽車模具有限公司 作者:郭宏軍 陳平 堯軍
摘要:本文介紹了成都普什汽車模具有限公司的公司概況,系統化地闡述了公司的典型設備和在自動化制造技術上的應用,并對其中的幾個核心技術進行了較為詳細的論述。
制造業水平是一個國家工業化水平和生產力水平的體現,因此制造業在各經濟大國的國民經濟中占據著重要地位。模具制造素有“工業之母”之稱,它的發展水平是衡量一個國家制造業水平的重要標志之一。近年來,隨著汽車工業的飛速發展,市場對汽車模具制造企業提出了更高的要求,對大型自動化、智能化、高速模具的需求迅速增長,更高、更精、更細、更全面的模具制造技術成為汽車模具制造企業的立企之本。
目前汽車模具數控加工方式已由單一的型面加工發展到型面和結構面的全數字化立體加工,由中低速加工發展到高速加工。在汽車模具制造領域中,以集成化、數字化、網絡化為基礎發展起來的自動化加工和智能化加工的先進制造技術正得到越來越廣泛的應用,大大提高了模具的生產效率和加工精度,使模具制造水平邁入新的里程。成都普什模具有限公司以高技術、大投入為基礎,以現代管理和國際戰略為著力點,利用新興汽車制造業地域優勢,厚積薄發、統籌兼顧、放眼全球,現已形成以汽車覆蓋件沖壓模具、檢具、夾具以及沖壓件為一體的現代化制造企業。
公司消化、吸收各主流車廠標準,形成了獨具特色的“PWS”標準,培養了獨立的研發團隊,目前已經具備開發各類中高檔模具的實力。為日本馬自達、法國PSA、一汽大眾、一汽轎車、神龍汽車、廣汽三菱、長安馬自達、長安PSA等客戶設計和制造各類汽車覆蓋件和結構件產品,覆蓋件包括頂蓋外板、引擎蓋內/外板、門內/外板、翼子板、側圍內/外板、尾門內/外板,結構件包括前/后地板、輪罩、立柱、保險杠及各類加強件等。從結構件模具的技術研發,到高強板、外覆蓋件模具的技術提升,公司已經形成具有自主專利的生產技術和特色產品,其中包括參數化裝配設計、模面間隙設計等自主專利技術以及高速精密浮動落料模、多工位模具、自動化模具、高強板模具、頂蓋模具等特色產品。
一、模具加工設備
根據汽車模具具有結構尺寸大、形狀復雜、表面質量要求高的特點,公司配備了先進的生產設備以滿足生產要求,其中五軸加工機床3臺(SORALOCE機床、RAMBAUDI機床MECOF機床),五面加工中心20余臺,三軸加工中心、數銑、普加等20余臺。
(1)對于有些含有側切、側整形和側翻邊等結構的汽車模具,其擺角加工區域的孔、輪廓或整形精度要求高,這就需要主軸剛性好,精度高的五軸機床加工,SORALOCE機床(如圖1所示)完全能滿足加工的需要。該機床的主要參數如下:固 定 工 作 臺 尺 寸 為 :7000mm×2500mm;旋 轉 工 作 臺 尺 寸 為 :2500mm×2500mm,前后移動量1500mm;主軸:最大伸出量1025mm,上下移動量3000mm; 左右移動量3000mm,轉速最大3000r/min; A軸、B軸和旋轉工作臺范圍為:0°~360°;
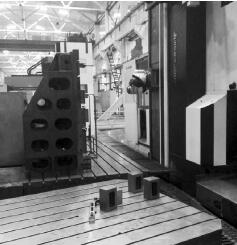
圖 1 SORALOCE機床
(2)對于結構尺寸大、形狀復雜、型面質量要求高的汽車模具,可 采 用 五 軸 聯 動 機 床 進 行 高 速 加工,如RAMBAUDI公司的RAM-speed-H45 PLUS型高速加工中心(如圖2所示)。該機床的主要參數如下:加 工 范 圍 為 :4500mm×2700mm×1500mm;定位精度為:X軸0.025mm、Y軸0.020mm、Z軸0.015mm,A/C軸P≤12”;重復精度為:X軸0.010mm、Y軸0.010mm、Z軸0.010mm,A/C軸P≤8”;主 軸 功 率 為 3 0 k W , 主 軸 轉速 2 4 0 0 0 r / m i n ; 主 軸 用 氮 化 硅(Si3N4)陶瓷球軸承;刀庫容量為:30把;立柱采用龍門式框架結構,精度高,特別適合大型汽車模具高速加工。
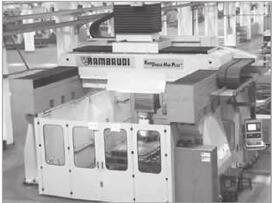
圖 2 RAMBAUDI公司的RAM-Speed-H45 PLUS型高速加工中心
二、模具產品目前采用的主要加工技術
模具自動化制造技術體現了企業整體制造的技術水平,是由許多技術環節串聯而成的,公司在幾年前就提出發展汽車模具自動化加工戰略目標,并組建了相關的技術攻關團隊,采用TRITOP掃描技術、模擬仿真和在線檢測環節進行了一系列的優化和改進,在汽車模具自動化加工技術方面取得了良好的效果。
(1)TRITOP技術是利用特有的數碼點和參考點來構建一個完整的坐標定位系統,利用光學拍照定位技術和光柵測量原理,可在極短的時間獲得復雜工件表面的完整點云的一種
技術。采用TRITOP技術對模具鑄件毛坯進行掃描,從而獲得加工前模具的真實狀態,為汽車模具自動化制造的安全性提供了保障。
(2)汽車模具的結構復雜,側切、側整形和側翻邊的模具比較多,為了保證汽車模具自動化制造的安全性,需對側切、側整形和側翻邊部分的程序進行機床加工模擬仿真。目前我們結合公司的機床設備參數,建立了相應的機床數據庫,確保了汽車模具自動化制造的安全性。
(3)汽車模具在自動化制造過程中,加工精度主要取決于加工刀具的測量與精度補償。在機檢測系統就是在機床上利用工件測頭對工件進行檢測的一種測量方式,對模具加工全過程的監測和補償,防止人為誤操作,保證了汽車模具自動化制造的精度。
1.典型模具產品——頂蓋的制造技術
汽車模具中頂蓋是最大的沖壓件之一,頂蓋質量的好壞直接影響到汽車的外觀品質,因此,頂蓋除了分析、設計和調試環節外,制造環節也非常重要。公司在頂蓋零件加工制造方面積累了豐富的技術經驗,主要有以下幾個方面:
(1)型面加工時采用圓弧進退刀方式,提高頂蓋的加工質量,如圖3所示。
(2)型面加工中采用點銑方式加工,減少刀片的磨損,提高了切削速度,精加工采用主軸傾斜10°的方式進行加工,如圖4所示。
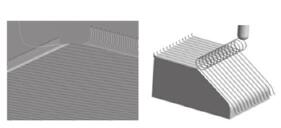
圖 3 采用圓弧進退刀方式
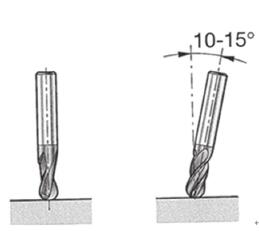
圖 4 點銑加工方式
(3)為保證型面的加工精度、減少刀片磨損,型面精加工前先對淬火區域的R留0.05mm進行預精加工,最后再進行全面精加工,如圖5所示。
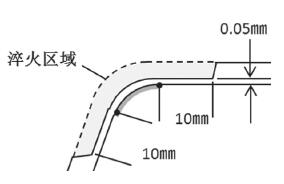
圖 5 淬火區域加工方式
(4)頂蓋后序模具加工中,為保證型面的進度和加工效率,優化了程序,保證了主軸Z向沒抬刀,且避空區域的進給值設置為最大速度,如圖6所示。
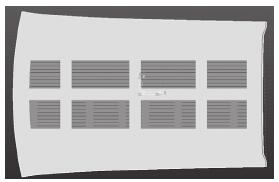
圖 6 加工區域和避空區域的加工方式
2.新裝備在模具加工制造中的應用
在汽車制造領域,大批量和高精度的生產要求決定了耐用性成為汽車模具的基本要素。為了提高汽車模具的使用壽命,汽車成型模具都要進行表面處理。汽車模具表面處理仍以火焰淬火為主,我國大部分廠家還處于人工淬火階段,由于火焰淬火質量很大程度取決于操作者的經驗,經常出模具表面淬火后硬度低或者開裂問題。因此,尋求一種淬火質量高,而且穩定的模具淬火方法非常重要。數控激光淬火機床可以通過程序的控制,不但能有效地保證模具表面淬火的要求,而且還提高了模具表面淬火效率。目前,我公司使用激光淬火機床對模具進行淬火已進入實際應用階段,已能完成非深拉延和非深腔模具的淬火, 模具型面使用激光淬火,淬火層均勻,淬火硬度和質量大大優于手工淬火,如圖7所示。
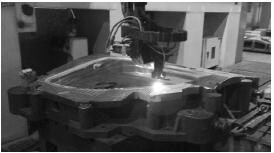
圖 7 采用數控激光淬火機床對汽車模具淬火
三、結束語
隨著汽車模具制造技術的日臻完善,數字化、集成化、自動化是汽車模具制造領域發展的必然趨勢。從加工技術、加工工藝的規范與創新,工裝設備、加工設備的完善與革新,自動化技術都將全面覆蓋、系統連接生產制造的各個環節,提升品質,降低成本,形成一套自動化、標準化、完整化的制造理論,打造一批高產、高效、高質的制造企業。立足高遠,放眼未來,隨著新興科學技術的進步與發展,同時伴隨著我國制造業產業升級的大潮,多種新理論、新技術將應用到汽車制造業中來,數字化、網絡化、智能化逐步同自動化技術相互融合、優勢互補,共同開拓汽車模具制造的新領域。
投稿箱:
如果您有機床行業、企業相關新聞稿件發表,或進行資訊合作,歡迎聯系本網編輯部, 郵箱:skjcsc@vip.sina.com
如果您有機床行業、企業相關新聞稿件發表,或進行資訊合作,歡迎聯系本網編輯部, 郵箱:skjcsc@vip.sina.com