五坐標龍門加工中心加工零件表面粗糙度差的原因分析
2020-12-14 來源:昌河飛機工業(集團)有限責任公司 作者:林超青
摘要:公司一臺五坐標龍門加工中心在加工時零件表面波紋嚴重,表面粗糙度嚴重超差,無法滿足工藝要求。零件表面粗糙度差的成因比較多,解決難度大,本文對該機床零件加工表面粗糙度差的原因和處理措施進行一些探討。
1、問題分析
某五坐標高速龍門加工中心前期進行了五軸頭翻新大修,機械及電氣部件均有更新,在零件試加工過程中發現,加工的零件表面波紋嚴重(見圖1),表面粗糙度極差,完全無法滿足工藝表面粗糙度的技術要求。
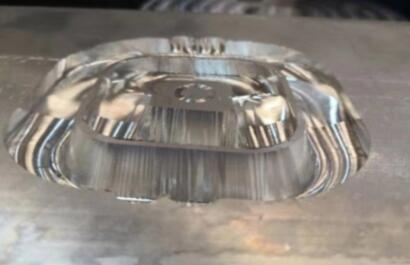
圖1:表面波紋嚴重的零件
零件加工表面粗糙度差的原因比較多,零件加工程序編制不良或機械部件磨損,運動部件的間隙增大,機械剛性下降,龍門同步超差,電氣參數與機械部件的機械特性不匹配,伺服優化不好等因素,都會導致坐標軸運動時無法快速準確定位。機床來回尋找定位位置導致伺服系統振蕩或系統電氣響應速度慢,造成零件加工表面出現波紋,表面粗糙度超差。電氣調試和伺服優化主要是針對機床的三環控制系統進行(見圖2)。
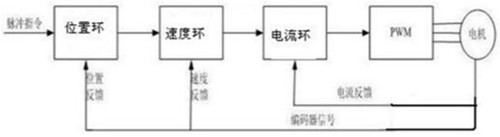
圖2:機床三環控制
從圖2可以看出,機床電氣特性一般包括三環特性,由一系列電氣參數設定,比如速度環、位置環增益等。如果速度環、位置環的增益設定值較大,系統響應就較快,能夠較快達到穩定狀態,機床加工時零件表面質量也會相應提高。但是如果速度環、位置環的增益設定值太高,就會造成系統振蕩,無法達到穩定狀態,機床出現抖動,電機嘯叫,加工時零件表面出現波紋;速度環、位置環的增益設定值過小,則機床響應速度降低,零件加工時表面也會出現波紋。圖3是指令響應及穩定過程。
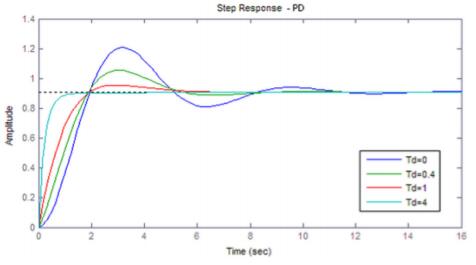
圖3:指令響應示意圖
因此,解決此類問題需要從電氣和機械兩方面綜合分析,才能最終找到問題所在。
2、零件加工程序編制策略不符合機床加工特性
圖1零件是用來檢測機床五軸加工性能是否良好由使用部門自行制定的一個通用試切件,試切加工時沒有針對本機結構及特性進行專門的程序編制和優化,該零件加工程序編制和加工參數是否符合本機特性,零件試切結果是否合適存在爭議。為確認表面粗糙度差的原因是否由于零件加工程序編制策略造成,于是使用五坐標機床驗收標準中通用的NAS試切件和程序、參數進行試切加工,加工結果如圖4所示。從NAS試切件可以看到,零件表面粗糙度有顯著改善,但是表面的波紋依然比較嚴重,所以可以認為零件程序編制和加工參數不是該機床零件表面粗糙度差的主要原因,而是機床自身問題導致零件表面粗糙度嚴重超差。
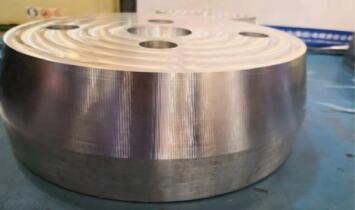
圖4:NAS五軸試切件
3、五軸頭機械特性與原電氣
特性不匹配該機床的五軸頭前期剛進行大修翻新,伺服電機、傳動部件、軸承、編碼器等全部更換,部件裝配面全部進行刮研校正,如果該大修翻新的技術指標達不到要求或電氣特性不匹配,零件加工也會相應出現各種問題。為確認表面粗糙度差是否是由五軸頭造成,可進行一系列測試。
(1)A/C軸定位精度檢測。數控機床坐標軸的定位精度和重復定位精度直接關系到零件加工的質量,該機床五軸頭進行過翻新大修,如果A/C軸定位精度(P)和重復定位精度(Psmax)不好,坐標軸在快速運行中來回尋找定位點將造成機床振蕩抖動,零件表面相應就會出現波紋,粗糙度下降。因此需要對A/C軸進行定位精度(P)和重復定位精度(Psmax)檢測,結果見表1。

表1:A/C軸的定位精度和重復定位精度
從表1可以看到,該機床的A/C軸的定位精度和重復定位精度都滿足機床的出廠精度要求,同時A/C軸的反向間隙也滿足要求。因此表面粗糙度由A/C軸的定位精度和重復定位精度造成的可能性可以排除。
(2)A/C軸圓度測試。圓度誤差是各種誤差中非常重要的一項數據,圓度誤差是回轉體在正截面上的實際輪廓對比于理想圓的變動量,數控機床的圓度誤差對數控機床的功能和精度有直接影響。該機床采用的是FIDIAC20數控系統,利用系統自帶的圓度檢測功能(ERCI)可以對坐標軸進行圓度檢測。
按數控系統要求進行A/C軸圓度測試的相關設置,參數設置好后進行A/C圓度測試,測試結果如圖5所示。
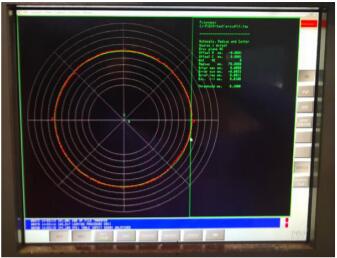
圖5:A/C軸圓度測試
從A/C軸圓度測試結果看,A/C軸進行圓度測試時A/C的圓度曲線均勻,各象限圖形沒有明顯的畸變或過沖,圓度測試滿足要求,A/C軸運動時沒有振動,機械性能沒有明顯缺陷,A/C軸機械性能滿足要求。
(3)A/C軸伺服優化測試。如果速度環、位置環的增益設定值較大,系統響應就較快,能夠較快達到穩定狀態,機床加工時零件表面質量也會相應提高。為測試表面粗糙度超差是否是有A/C軸的速度環、位置環的增益設定值小,響應速度慢引起,可以增加A/C軸的速度環、位置環增益(見表2)。

表2:A/C軸的速度環、位置環增益
A/C軸的速度環、位置環的增益設定值為2.0、2.3時進行加工測試,加工的零件表面粗糙度沒有明顯改善;繼續增加速度環、位置環的增益至2.3、2.8時A/C軸電機開始嘯叫抖動,因此速度環、位置環的增益不能繼續加大,要相應降低增益值,增益值的設定一般是機床軸開始嘯叫抖動時增益值的80%為宜。因此,可以認為零件表面粗糙度問題不是由A/C軸的速度環、位置環的增益引起。
(4)NAS 三軸試件試切。A/C軸的定位精度、圓度和伺服優化測試結果沒有發現問題,為確認零件表面粗糙度超差是否由五軸頭引起,可以進行NAS三軸試件試切,把五軸頭鎖定加工。加工的三軸NAS試件結果如圖6所示。
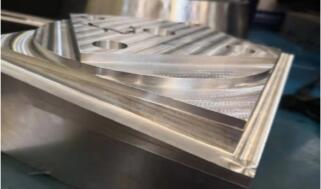
圖6:三軸NAS件
從圖6可以看到,三軸NAS的外圓、正方形的邊波紋嚴重,表面粗糙度嚴重超差。由于三軸NAS加工時A/C軸不參與運行,但試件還是出現表面粗糙度嚴重超差,因此表面粗糙度嚴重超差由五軸頭造成的可能性可以排除,五軸頭的技術性能符合要求,表面粗糙度嚴重超差是由其他坐標軸運動引起。
4、X/X1軸龍門同步超差導致
表面粗糙度差大型數控龍門加工中心的龍門軸由主動軸(X)和從動軸(X1)組成,X/X1通過龍門(橫梁(Y軸)機械連接,應用龍門同步技術進行控制。X/X1的同步誤差一般要控制在0.015mm以內,如果龍門同步誤差過大,X/X1軸運行不同步,會造成橫梁扭曲,X/X1伺服電機過流,機床出現振動等后果。
機床運行中出現振動,加工的零件表面就不可避免會出現波紋等問題。為確認該機床的龍門同步是否在要求的誤差范圍內,進行龍門同步檢測。利用數控系統的龍門同步功能,檢測龍門同步情況,結果發現該機床的X/X1同步誤差只有0.009mm,同步誤差在容許的誤差范圍內。因此,該機床加工零件表面粗糙度超差的問題不是由龍門同步誤差引起。
5、機械部件磨損,機械剛性
下降導致機床振動,零件表面粗超度差由于該機床的A/C軸情況良好,同時X/X1龍門同步誤差很小,不會造成零件加工出現波紋,因此出現表面粗糙度差的原因可能是由X/Y軸的問題導致。為檢測X/Y的插補運動情況,可以進行X/Y軸圓度測試,參數設置如下:進給速度:F=4000mm/min,圓半徑R=100mm,插補軸:X、Y。X/Y進行圓度測試后,測試結果如圖7所示。
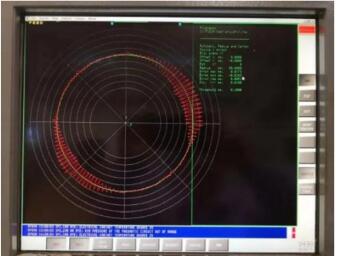
圖7:X/Y軸圓度測試
從X/Y圓度測試的結果可以看到,在一、三象限(即X軸方向)有明顯的振蕩,同時在X軸運行時用手觸摸機床,可以感受到機床有輕微的抖動,因此可以認為零件表面粗糙度超差是由X軸的問題導致。該機床各軸采用的機械傳動是滾珠絲杠傳動,滾珠絲杠是機械傳動的關鍵部件,如果磨損大,將導致滾珠絲杠和絲母間隙增大,超過一定的范圍就會導致坐標軸精確定位困難。當機床采用全閉環位置反饋時,數控系統是根據光柵尺的位置反饋進行數據處理,如果絲杠間隙過大,機械接觸剛性下降,主軸加工受力后,那么機床無法精確定位,就會在定位的位置附近來回尋找位置。機床在高速運行狀態下來回尋找定位位置必然會導致振動,形成系統振蕩,表現在零件上就是零件表面出現波紋等。為確認X軸絲杠的磨損程度,可以人為地讓X/X1的龍門同步誤差加大,使橫梁稍微扭曲,絲母和絲杠接觸緊密,消除絲杠和絲母間隙。讓X/X1軸同步誤差分別是0.015mm、0.025mm、035mm進行測試,在同步誤差在0.035mm時X/X1軸的振動消除,進行圓度測試(見圖8),結果如下:
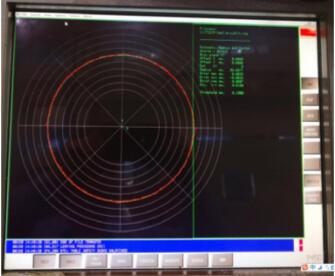
圖8:X/Y圓度測試
從圓度測試的圖形結果可以看到,人為使橫梁(龍門)扭曲以后,消除絲杠與絲母間隙,圓度測試正常。因此可以最終確認該機床零件表面粗糙度超差是由于X/X1軸的絲杠磨損,間隙加大導致機械剛性下降導致。根據以上測試的結果,更換X/X1絲杠,速度環和位置環參數重新優化,使機床電氣特性與新絲杠的機械特性匹配。同時因為更換了絲杠,絲杠與坐標軸的定位精度直接相關,所以要進行激光螺距定位精度校正和補償。在做完X/X1絲杠更換、速度環、位置環優化調整以及定位精度激光螺距校正、補償后,機床進行試加工,加工結果如圖9所示,零件表面光滑,波紋消除,表面粗糙度符合要求。
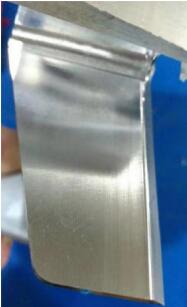
圖9:試切件
6、結束語
造成零件加工時表面粗糙度差的原因比較多,解決問題難度較大,需要從編程、加工方法、加工參數、電氣和機床機械結構分析入手,根據具體情況,分別對機床電氣、機械、數控系統進行測試和調整,才能找到問題的根源,取得比較好的效果
投稿箱:
如果您有機床行業、企業相關新聞稿件發表,或進行資訊合作,歡迎聯系本網編輯部, 郵箱:skjcsc@vip.sina.com
如果您有機床行業、企業相關新聞稿件發表,或進行資訊合作,歡迎聯系本網編輯部, 郵箱:skjcsc@vip.sina.com