核電冷卻泵泵體五軸數控加工工藝研究
2021-1-13 來源: 云南機電職業技術學院校企合作辦公室實訓 作者:孫建明,黃曉明,朱蘭,楊曉春,劉春美
摘要: 核電冷卻泵泵體是主回路系統中三大核心部件之一,泵體的制造加工精度對整體設備的運行安全有直接影響。為提高泵體的加工精度,提出用五軸數控加工工藝加工泵體。分析泵體特征,應用尺寸中差建模,并設計專用夾具。基于遺傳算法,研究加工工藝及方法,應用五軸聯動數控加工中心完成核電冷卻泵泵體加工。解決了圓柱倒扣面、90°彎管管道、薄壁件等加工難題。
關鍵詞: 核電冷卻泵; 夾具設計; 中差建模; 五軸聯動
0 、前言
核電冷卻泵泵體是主回路系統中三大核心部件之一,也是核島中的一級安全部件。泵在主回路系統中所起的作用相當于人體內的心臟,泵體負責將主回路的冷卻劑完成熱循環,在反應堆輸出功率之前加熱反應堆裝置。泵體內部管道必須銜接光順,以保證冷卻劑高效完成熱循環。
泵體的制造加工精度直接影響整個設備的運行安全。傳統的鑄造技術很難滿足核電冷卻泵泵體的使用功能要求,五軸數控加工技術在提高泵體內部管道表面質量及精度方面具有很大的優勢。五軸加工的主要優勢:
( 1) 通過調整刀軸矢量避免刀具、主軸與工件及工裝發生碰撞干涉; ( 2) 刀具相對于加工工件的位置可以靈活調整,保證刀具切削時處于最佳姿態,有效提高工件的表面質量。因此,五軸數控加工技術主要應用在航空、航天、水利水電、船舶、軍工等領域的核心產品制造。
1 、泵體分析
泵體工程圖如圖 1 所示,泵體主要由泵心、90°彎管、支撐體組成。泵心呈 R150 mm 倒扣面,管道壁厚為 5 mm,并且要求管道內壁銜接光順、無明顯接痕,管道外壁 R4 倒角面光順。
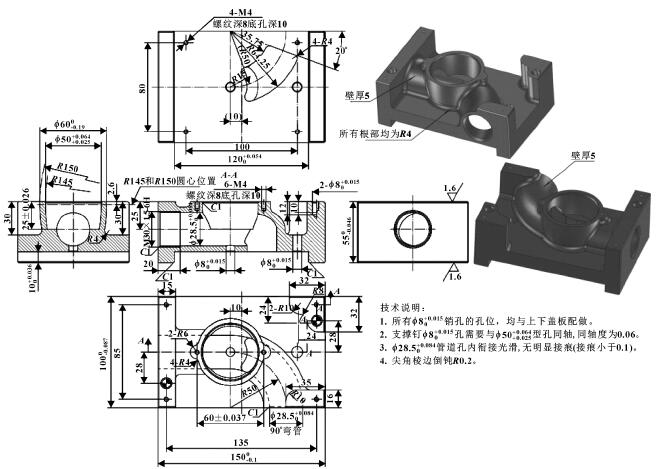
圖 1 核電冷卻泵泵體工程圖
加工難點:( 1) R150 圓柱倒扣面,加工時需合理調整刀軸的角度及刀具切削姿態,才能保證加工完成的倒扣曲面表面質量及精度符合設計要求。( 2) 管道壁厚僅為 5 mm,要求設計合理的加工工藝方案,保證薄壁加工不變形。( 3) 90°彎管內壁要求銜接光順,內外壁曲面呈均勻壁厚管道狀,應用 3+2 軸、4+1 軸任意擺動刀軸均無法滿足彎管內壁銜接光順的設計要求,必須應用五軸五聯動加工工藝技術才能滿足加工設計要求。
2 、中差建模
按照設計人員的習慣建模方式,建模時都以對零尺寸建模,至于實際加工精度是否能夠滿足設計圖紙要求,主要取決于操作機床的工人能否依經驗調整刀具半徑補償值。隨著現代技術不斷發展,機床生產廠家生產的數控機床定位精度已達到 0. 02 ~ 0. 05 mm級,發達國家生產的機床定位精度能夠達到 0. 005mm 級,機床控制系統也越來越先進。通過控制系統的補償,在刀具未磨損的情況下加工出來的產品都能夠達到圖紙要求。
編程工程師只需嚴格按照中差建模及編程,機床運行加工一次,零件尺寸就能達到圖紙要求。
例如文中冷卻泵泵體尺寸 60+0-0. 19,如果建模時不計算尺寸中差,還是按對零尺寸建模,加工完成的零件尺寸偏大,操作機床的工人需反復修改刀具半徑補償值并運行機床再加工,直到零件尺寸符合圖紙要求為止,這種做法費時費力耗能,并且容易出錯。故中差建模是保證產品零件尺寸精度的關鍵。

3 、夾具設計
五軸聯動加工時,工作臺 A、C 軸都要轉動,當A 軸擺動角度大于等于 90° 時,工作臺與主軸容易發生碰撞。為了避免此類事故發生,工件裝夾時應抬高裝夾位置,需要設計五軸專用夾具來實現。根據EMCO LM600 五軸聯動加工中心工作臺直徑、主軸直徑,設計夾具。夾具安裝在工作臺中心,充分利用五軸聯動機床的行程,同時保證 A 軸擺動角度大于等于 90°位置時,主軸與轉臺保持一定的安全距離。
工件裝夾示意圖如圖 2,L 代表 A 轉臺直徑,L1代表最小安全間隙,L2代表主軸半徑,H1代表三爪卡盤高度,H2代表夾具高度。經分析可得 H2計算公式。

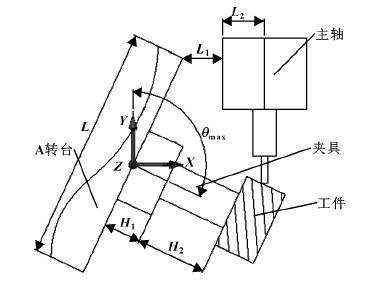
圖 2 裝夾示意圖
為了方便裝夾及拆卸工件,設計如圖 3 所示的夾具,夾具上 3×8. 2 的通孔用于 M8 螺栓鎖緊工件。
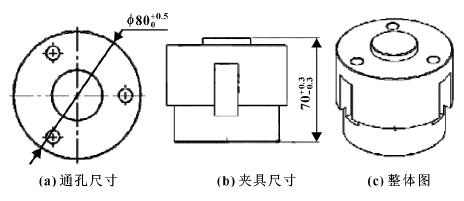
圖 3 夾具設計圖樣
4 、加工工藝方案
4. 1 基于遺傳算法優化加工工藝
核電冷卻泵泵體加工有多種加工工序,一種加工工序有多個加工策略,一個加工策略又有多個加工參數。例如: 加工 28. 5+0. 084+0彎管外管面工序有 4 種:
( 1) 先把外管面粗加工、精加工到尺寸,然后再粗加工、精加工內管道; ( 2) 先粗加工、精加工內管道,再粗加工、精加工外管面; ( 3) 先粗加工外管面,然后粗加工內管道,再精加工外管面,最后精加工內管道; ( 4) 先粗加工內管道,然后粗加工外管面,再精加工內管道,最后精加工外管面。
精加工外管面時可以應用 Power Mill 最佳等高精加工策略,也可以應用 Power Mill3D 偏置精加工策略。加工工藝包括 8 個關鍵參數: 加工工序、加工策略、切深 ap、切寬 ae、主軸轉速 S、進給量 F、加工時間、表面粗糙度。應用遺傳算法優化加工工藝,既能保證加工精度和表面質量又能縮短加工時間。遺傳算法優化加工工藝流程如圖 4 所示。
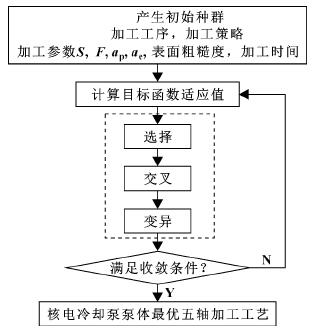
圖 4 遺傳算法最優解流程圖
4. 2 加工策略
4. 2. 1 刀具選擇
選擇合適的刀具材料和刀具類型不僅可以提高加工效率,而且能夠保證零件的加工精度。刀具的選擇可遵循以下原則:
( 1) 粗加工時在尺寸允許條件下盡量采用大直徑刀具,提高生產效率,降低刀耗。
( 2) 在保證產品零件尺寸的情況下,為使刀具有足夠的剛度,其懸伸長度應盡可能短。核電冷卻泵泵體毛坯材料為 2AL2,屬于易加工材料。在綜合考慮核電冷卻泵泵體的形狀、材料等各個方面的因素后所選刀具的參數如表 1 所示。
表 1 選用刀具參數
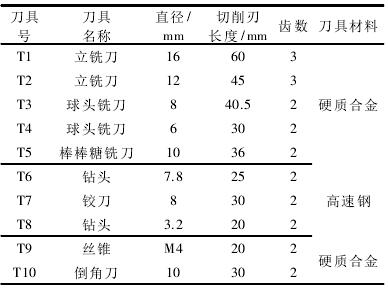
4. 2. 2 關鍵重要工序過程
( 1) R150 倒扣型腔及彎管外管面半精加工粗加工后外管面留有大量臺階余量,如圖 5 所示。
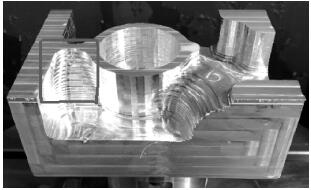
圖 5 泵體外管面粗加工成品
如果直接精加工,精加工余量大并且不均勻,加工后的外管面表面質量較差。應將外管面大部分余量除去后再進行精加工,去除大部分余量可以應用模型殘留區域清除策略,也可以應用最佳等高精加工策略,還可以應用等高精加工策略。應用遺傳算法優化加工工藝后采用等高精加工策略。優化后的刀路軌跡如圖 6 所示,提刀 301 次,加工時間 24 min4 s。
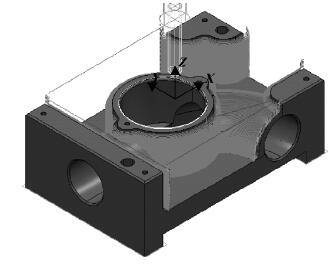
圖 6 優化后的刀路軌跡
沒有優化前的刀路軌跡如圖 7 所示,提刀 781 次,加工時間 50 min23 s。
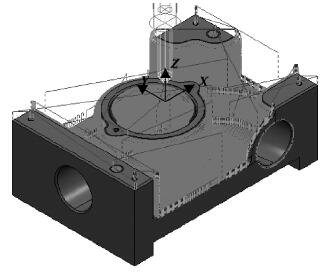
圖 7 優化前的刀路軌跡
( 2) 內管道粗加工
為了保證內管道銜接光順,外管面粗加工后加工內管道。如果外管面精加工完成后再加工內管道,內管道加工時工件會產生振動,導致內部管道面產生振紋,表面不光順。粗加工內部管道面應用 Power-Mill2016 等高精加工策略從兩端分別加工,比應用常規的模型區域清除策略開粗加工節省時間 23 min50 s,減少提刀 89 次。
( 3) 內管道半精加工應用
Power Mill2016 管道加工策略半精加工內管道,其刀路軌跡計算有 2 種方式:
①只需設置中心參考線,根據參考線的變化截取管道,完成刀路軌跡的計算,這種方式適合截面變化規律的管道; ②需要設置中心參考線、管道上下面坐標系,根據上下坐標系確定加工范圍,用平行等距的方式截取管道,中心參考線作為刀軸的傾斜曲線,從而計算刀路軌跡,這種方式適合截面變化不規律的管道。此次加工的管道呈90°,總長為 115 mm,通過刀路軌跡計算,測得有效切削刃 95 mm 才能完成該管道加工,查閱山高刀具樣本,最長的棒棒糖銑刀有效切削刃為 60 mm。由此可知,想用一個加工策略完成整個管道加工是不可行的。仔細分析內部管道面,有 65 mm 管道面是直管道面,應用 3+2 軸就能把該部分加工完成,為了保證內部管道面銜接光順、無明顯接刀痕,計算直管加工深度 W,W = 65-25+6+0. 5= 46. 5 mm。加工部位及
刀路軌跡如圖 8 所示。
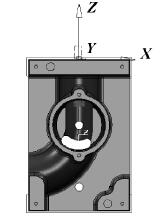
圖 8 3+2 直管加工刀路軌跡
另一端長度為 64. 25 mm 的彎管面應用 3+2 軸定軸加工,應用管道粗加工策略配合直徑 10 mm 的棒棒糖銑刀加工內管道彎管部位。中心參考線從管面到型腔中心位置,軸向余量為0. 35 mm, 行距為 3 mm, 下切步距為 0. 3 mm, 刀軸方向為自動,傾斜角度為 15°,順序自末端均勻螺旋方式,快進高度為幾何形體安全區域方框,打開自動碰撞模塊,夾持間隙為 0. 5 mm
,刀柄間隙為 0. 5 mm。刀路軌跡、中心參考線、加工位置如圖9 所示。
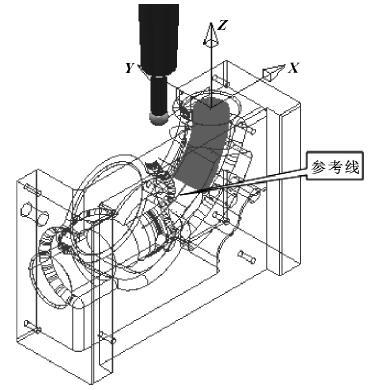
圖 9 彎管加工參考線及刀路軌跡
( 4) 內管道精加工
內管道加工的精度影響到核電冷卻泵主回路系統冷卻劑的熱循環效率,加工精度至關重要。長 46. 5mm 直管道面加工應用等高精加工策略加工,3 + 2 軸定軸加工方法,最小下切步距為
0. 9 mm,螺旋下刀方式。
彎管部精加工有 2 種精加工策略:
①管道插銑精加工策略,適合加工管道內部截面變化的管道; 管道螺旋精加工策略,適合加工管道內部截面一致的管道。文中加工的內部管道面屬于截面一致的管道,應用管道螺旋精加工策略加工,行距為 5 mm、下切步距為 0. 3 mm、合并點為 60,提刀高度開始為 10mm,重疊為 8 mm,提刀高度為 0. 3 mm,打開自動碰撞 模 塊,夾 持 間 隙 為 0. 5 mm,刀柄間隙為 0. 5mm,刀軸方向為自動,快進高度為幾何形體安全區域方框,切入切出延伸移動方式,距離為 1. 5 mm。
( 5) 外管面精加工外管面精加工有 3 種加工策略:
①平行精加工策略; ②3D 偏置精加工策略; ③最佳等高精加工策略。平行精加工策略計算刀路軌跡的原理是計算出 2D 刀路,然后沿著 Z 軸方向投影到曲面上,采用該策略計算的刀路軌跡有一個弊端,如果加工的曲面較陡,投影到該區域的刀路就稀疏,加工出來的曲面不光滑,刀路軌跡如圖 10 所示; 等高精加工策略計算刀路軌跡的原理是根據設定的下切步距把曲面按照層切方式分割,得到曲面加工刀路
。
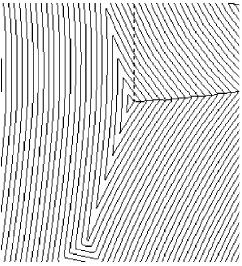
圖 10 平行精加工刀路軌跡局部截圖
該策略計算生成的刀路軌跡只能按照 U、V 方向排列,不能按照彎管的彎曲率均勻生成刀路軌跡,存在多處零點切削,加工后的管面也不光滑; 3D 偏置精加工策略計算刀路軌跡的原理是根據曲面的法向線投影計算,計算生成的刀路軌跡無論是陡曲面還是平緩曲面行距均一致。設置參考線及參考線方向后,可以按照參考線方向計算生成刀路軌跡,這樣生成的刀路軌跡能有效減少刀具零點切削問題,加工出來的曲面表面質量較好,刀路軌跡及參考線如圖 11 所示。
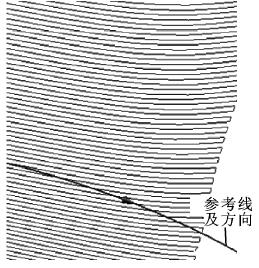
圖 11 3D 偏置精加工刀路軌跡及參考局部截圖
( 6) 底部 R4 倒角精加工中心型腔兩側 R4 倒角呈倒扣負角面,需要旋轉工件把負角轉化為正角才能加工。
文中加工方法是通過新建編程坐標系來控制工件旋轉的方向及角度,復制 G54 坐標系得到 G54-1 坐標系,該坐標系繞 X 軸旋轉 30°得到編程坐標系。加工 R4 倒角負角面應用清角精加工策略,按照默認的加工策略計算生成的刀路軌跡像縫衣服一樣加工倒角面,如圖 12 所示。
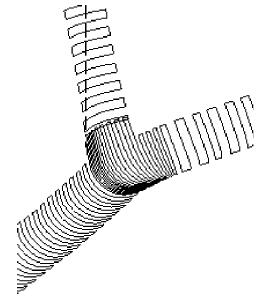
圖 12 縫衣式刀路
加工出來的倒角面不光順,有一道一道的接刀痕。為了倒角面光順,應改變刀路軌跡的加工方向,通過把清角精加工策略中的方式設置為自動方式,重新計算生成的刀路軌跡沿著倒角面平滑走刀,如圖 13 所示。
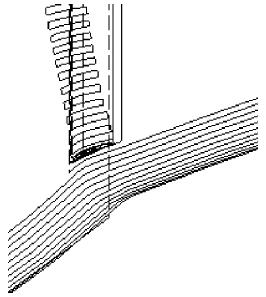
圖 13 光順式刀路
泵體左右兩側支撐體 R4 倒角面應用原 G54 坐標系編程,加工存在 2 個弊端: ①刀具懸伸長; ②刀桿擦到已加工面。刀具伸出夾持刀柄的長度要大于 30 mm,刀具伸出長度過長,切削時刀具會振動并存在讓刀現象。切削過程加工倒角特征的刀具直徑只有 6 mm,直徑為 6 mm 的球體銑刀有效切削刃只有 18 mm,刀桿會把已加工表面擦傷。
為了避免上述弊端,加工兩側支撐體時均要旋轉工作,讓刀具和刀桿與側面呈5° ~ 10°角度,如圖 14 所示。
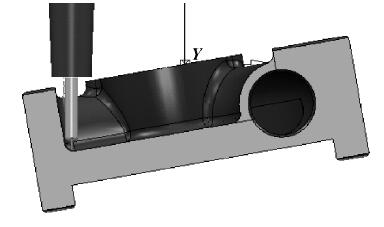
圖 14 刀具與側面夾角示意圖
4. 2. 3 關鍵工藝參數
根據工序過程,分析零件各加工區域幾何特征,結合加工過程,應用遺傳算法得到最佳工藝參數,如表 2 所示。
表 2 加工工序及關鍵工藝參數
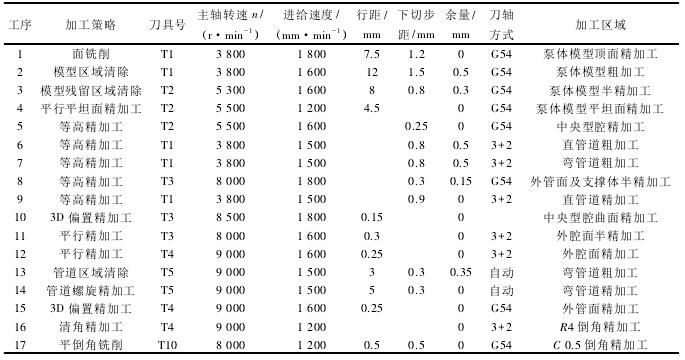
5 、五軸聯動加工
5. 1 裝夾方式
用三爪卡盤夾持夾具,然后用螺釘固定待加工的毛坯,如圖 15 所示??ūP用 4 塊壓板壓緊在工作臺上,卡盤壓緊固定前裝夾圓柱度小于等于 0. 005mm 的環規,用百分表校正三爪卡盤與機床工作臺軸心線 同軸度,調整三爪卡 盤位 置,保 證 同 軸 度 在0. 02 mm 跳動范圍之內,如圖 16 所示。
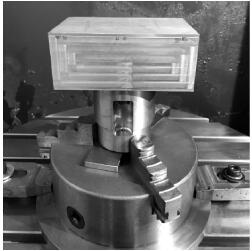
圖 15 毛坯裝夾
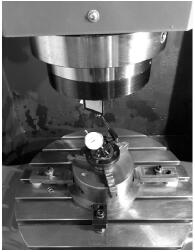
圖 16 校正三爪卡盤
5. 2 機床運行加工
嚴格按照刀具參數表表 1 夾持刀具長度,按照刀具參數表序號依次把刀具裝入機床對應刀庫刀號。應用 EMCO LM600 定制后處理器,處理生成的刀位軌跡,轉化成 NC 程序。通過 DNC
把加工程序輸入機床控制系統,按照加工工序運行程序,加工過程中注意觀察。加工過程如圖 17 所示,加工完成泵體如圖 18 所示。
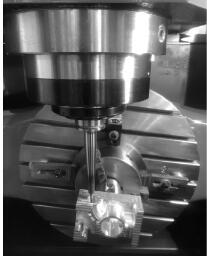
圖 17 五軸聯動加工過程
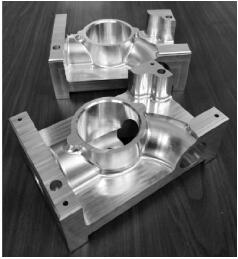
圖 18 產品零件泵件
6 、結束語
核電冷卻泵泵體作為具有代表性的五軸加工零件,本文作者應用 Power Shape 2016 尺寸中差建模,Power Mill 2016 編程,應用遺傳算法,獲得最優核電冷卻泵泵體加工工藝方法; 利用
EMCO LM600 五軸聯動加工中心加工完成,經 HEXAGON GLOBAL SDL07 10 07 三坐標測量機檢測,尺寸精度及表面質量均到達要求; 解決了圓柱倒扣面、90°彎管管道、薄壁件等加工難題。該加工工藝可為企業生產,學員培訓提供參考。
投稿箱:
如果您有機床行業、企業相關新聞稿件發表,或進行資訊合作,歡迎聯系本網編輯部, 郵箱:skjcsc@vip.sina.com
如果您有機床行業、企業相關新聞稿件發表,或進行資訊合作,歡迎聯系本網編輯部, 郵箱:skjcsc@vip.sina.com
更多相關信息