基于精雕系統的七級葉輪加工技術實踐
2024-3-7 來源:北京精雕科技集團有限公司 作者:張歡龍
1. 序言
葉輪是渦輪增壓器最關鍵的零件之一,廣泛應用于航空、船舶、汽車和真空泵等行業的發動機中,其中七級葉片的復雜葉輪是渦輪分子泵內部的核心部件,而渦輪分子泵則廣泛應用于真空鍍膜(PVD)、半導體制造等行業中,這些行業需要在超高真空環境(10-7Pa 以下)中才能工作。
考慮到葉片結構復雜、曲面變化大以及精度高等特點,目前一般采用 Mastercam、PowerMill、UG及CATIA等國外軟件結合五軸聯動機床加工,這些五軸聯動機床一般采用海德漢、西門子等國外高檔數控系統。為打破國外軟件和數控系統在葉輪制造方面的壟斷地位,北京精雕科技集團有限公司(以下簡稱北京精雕)開發了擁有自主產權的 SurfMill 軟件以及北京精雕五軸聯動系統,并采用在線檢測、在線補償功能加工葉輪。
本文采用北京精雕的 SurfMill 軟件造型并采用 JDGR400 五軸聯動精雕機,對七級葉輪的五軸編程、工藝規劃和實際加工進行探討與實踐。
2.七級葉輪結構及加工難點分析
七級葉輪(見圖 1)的基本特點 : 葉片分為7 級,共 249 個葉片,材料為 7075 鋁合金,尺寸f360mm×286mm。該零件上的葉片是由鋁合金整體加工而成,葉片加工完成后整體質量 14kg。
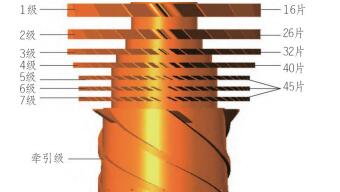
圖 1 七級葉輪
經分析,七級葉輪五軸聯動加工的難點如下。
1)該葉片屬于典型的薄壁件,葉片高度與厚度比> 30:1,葉片剛性差,加工時受力易變形,極易產生振動,彈刀過切風險很大。
2)相鄰葉片間距小,導致加工所需刀具最大長徑比為 14:1(見圖 2),加工時刀具的切削剛性差。

圖 2 刀具長徑比示意
3)葉片數量多達 249 個,葉片間距小,每一級之間距離小,刀具和葉片之間的安全距離最小只有 2mm,加工時極易產生干涉,如圖 3 所示。
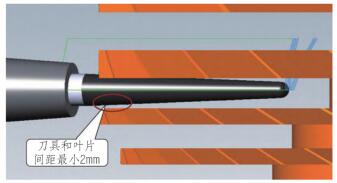
圖 3 刀具與葉片干涉示意
3.七級葉輪五軸加工工藝規劃
3.1 設備及軟件的選用
葉輪加工設備需要有強大的運算能力,且加工時主軸轉速高、擺動角度范圍大、聯動精度高,本次選用北京精雕的 JDGR400_A15SH 機床,配置在機測量系統、激光對刀儀等設備,并采用北京精雕自有的軟件 SurfMill 進行建模和編程。
3.2 刀具的選用
針對薄壁件,刀具的選擇需要從減小切削力的角度出發,因此選擇角度較大的前角和后角、較大的螺旋角(見圖 4)來減小切削力 ; 刀具結構采用短刃刀具(見圖 5),錐度避空,提升刀具剛性 ; 涂層選用 DLC 涂層,涂層厚 1μm,提高刀具鋒利度,減小切削力,提高刀具壽命及長時間加工時的穩定性。
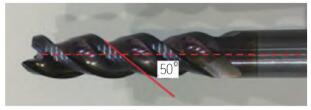
圖 4 大螺旋角

圖 5 錐度平底短刃刀具
3.3 加工工藝方案
針對長徑比大的難題,為了增加刀具的剛性,在深度上采用多把刀具分段加工的方式,以保證切削剛性,提高加工效率。刀具型號及加工參數見表 1。
表 1 刀具型號及加工參數
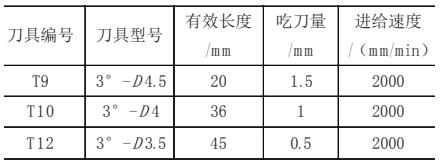
3.4 編程加工方案
七級葉輪葉片數量多、間距小,刀具極易產生干涉和過切。為避免在實際加工中出現問題,采用北京精雕的 DT 編程技術,在軟件中實現過切檢查、干涉檢查和機床模擬,在計算機端確保加工程序的安全,從而避免機床實際加工中的過切、干涉和碰撞等問題,如圖 6 所示。
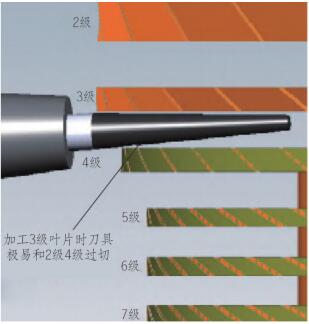
a)刀具與工件干涉示意
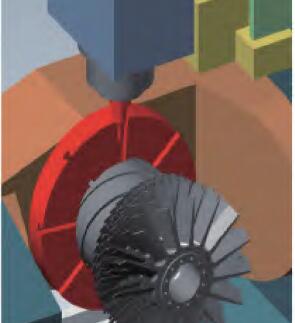
b)DT 仿真加工
圖 6 葉輪加工模擬
DT 編程技術最大的特點就是改變原有的調試模式,將原來需要在機床上進行的操作(包括試切加工、人為觀察過切和碰撞,以及機床行程檢測等),全部加載到計算機中進行,減少人員機床上的操作,減輕調試人員的心理壓力,降低調試出錯的成本,縮短產品調試周期。
4. 加工試驗及方案改進
按照規劃的方案進行加工試驗,試制結果見表 2。通過表 2 數據可看出,試制結果不滿足工藝要求,需要優化改進。
表 2 試制結果
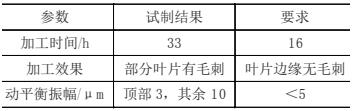
4.1 方案優化改進
經分析,需要從 4 個方面進行優化改進 : ①優化加工效率。②改善表面質量。③改進夾持治具。④管控毛坯精度。
1)利用 CAM 軟件優化葉片間連刀高度。第一階段為保證絕對的安全,將葉片之間路徑安全位置設置在 Z 軸原點位置 ; 優化階段依靠 DT 編程技術,將刀具連刀高度抬至葉片最高高度之上30mm,加工時間縮短了 6.5h。
2)優化 T9、T10 刀具有效長度,增加刀具剛性。試制用的 T9、T10 刀具有效長度過長,刀具剛性差,切削參數無法提升,嚴重影響加工效率。依靠 D T 編程技術,精確計算 T9、T10 刀具所需的最短有效長度,從而提升刀具剛性,增加刀具切削用量,將葉輪加工時間縮短了 55min。
3)優化表面質量,縮短人工處理時間。葉輪加工完成后,其葉片銳角邊留下了大量的毛刺,需要手工清理,工作量較大,并且毛刺會影響工件整體動平衡性能,因此在加工時加入去毛刺程序,節省去毛刺的時間。另外,在機測量刀具錐度,減輕不同刀具間的接刀痕,使用激光對刀儀準確測量刀具錐度和直徑,將刀具偏差補償在加工路徑中,確保各刀具間的接刀痕< 0.008mm。
4.2 解決動平衡問題
對于產品的批量生產,動平衡振幅能否控制在 5μm 以內是生產的關鍵。目前機床精度、溫度管控都是合格的,針對動平衡偏大問題,經過分析判斷,是治具錐面和毛坯錐面配合誤差較大,使得毛坯安裝后毛坯軸線傾斜引起的。毛坯軸向圓跳動> 0.04mm,直接影響葉輪加工后的動平衡。治具夾持如圖 7 所示。
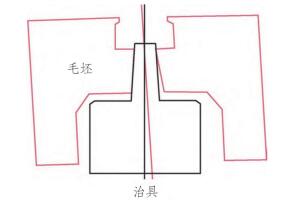
圖 7 治具夾持示意
重新精磨治具,其錐度達到 5° 43′ 9″,毛坯安裝后跳動得到大幅改善,結果見表 3。
表 3 精磨治具后跳動改善結果
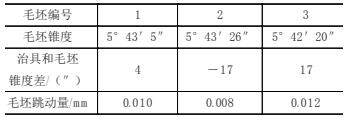
4.3 曲面加工方案
葉片曲面根據曲率可分為自由曲面和直紋曲面,自由曲面采用五軸點銑方式加工,直紋曲面采用五軸側銑方式加工,如圖 8 所示。
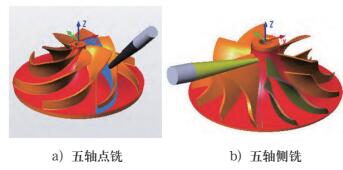
圖 8 曲面加工方式示意
在 SurfMill 中建模和編程。分層粗加工如圖9 所示,流道精加工如圖 10 所示。
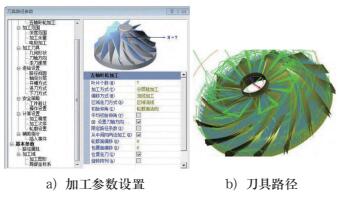
圖 9 分層粗加工
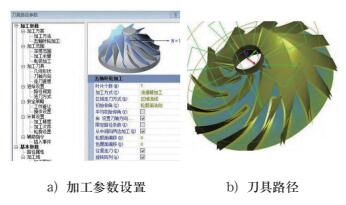
圖 10 流道精加工
4.4 改進后的實際加工驗證
利用 DT 技術和軟件編程,優化了刀路和加工程序,避免了干涉,消除了動平衡,提高了加工效率,同時零件的加工質量得到提升。加工后的零件如圖 11 所示,經檢測,達到了葉輪尺寸精度和表面粗糙度的要求。

圖 11 加工后的七級葉輪
5. 結束語
本文在分析七級葉輪結構特點和加工難點的基礎上,對機床選用、刀具選擇、工藝修正以及治具改進等做了深入分析。為提高效率,避免干涉,采用北京精雕特有的 DT 技術進行模擬校正,并通過試件的研制,優化一系列工藝參數,最后在北京精雕五軸聯動機床上完成七級葉輪的加工,加工精度、表面粗糙度以及動平衡等都符合要求,給類似的葉輪及復雜零件的加工提供了參考。
投稿箱:
如果您有機床行業、企業相關新聞稿件發表,或進行資訊合作,歡迎聯系本網編輯部, 郵箱:skjcsc@vip.sina.com
如果您有機床行業、企業相關新聞稿件發表,或進行資訊合作,歡迎聯系本網編輯部, 郵箱:skjcsc@vip.sina.com
更多相關信息