回轉類工件加工誤差在機測量系統
2017-12-8 來源: 上海大學 機械自動化及機器人重點 作者:王為東 沈南燕 吳耀贊 喻志響
摘 要 :針對回轉類工件輪廓加工誤差檢測,開發了一套用于數控車銑復合加工中心的在機測量系統。利用接觸式測頭,讀取數控機床各軸坐標值獲取測量數據并由以太網上傳至上位機,配合誤差評定算法及相關軟件,實現了回轉類工件尺寸、圓度、圓柱度及同軸度的在機檢測。介紹了測量系統的硬件組成、軟件開發及驗證實驗結果。在機檢測結果可以反饋至數控系統用以補償加工誤差,也可通過車間局域網上傳至車間層用于生產管理,因此該系統在大批量、無人化生產中具有良好的應用價值。
關鍵詞 : 回轉類工件 接觸式測頭 圓度 誤差評定
機械加工是先進制造技術的基層作業,是先進制造系統中最基本最活躍的環節,其基本目標是在低成本、高生產率的條件下保證產品的質量[1]。但在目前的數控車床加工過程中,零件加工精度的檢測主要是采用傳統的手工測量和離線檢測方法,包括回轉軸線法、三點法、投影法等。這些方法都需要將工件轉移到專門的夾具里用專門的測量儀或千分表、卡尺進行測量,顯然這些測量方式需要二次定位與裝夾,不僅效率低,還會產生二次定位誤差,越來越不能滿足車間快速加工生產的需要[2]。
如果能把車床和合適的檢測儀器有機結合起來,這樣車床不僅可以用于工件加工,而且可以直接對剛加工完成的工件進行尺寸測量,再利用 CNC 系統的通訊功能,就可以直接通過上位機實現對工件輪廓誤差的評定。通過這種方法不僅可以有效避免二次裝夾誤差,提高測量精度,解決離線零件檢測中的費時費力問題,而且可以擴大車床的使用范圍,具有很好的應用價值[3]。
因此,針對以上問題,本文圍繞回轉型零件的輪廓檢測,在數控車銑復合加工中心上展開了在機檢測系統的研究。通過集成在機測量系統,實現對回轉型工件輪廓的方便快捷的測量和評定。
1 、在機測量系統的構建
數控系統本身并不具有測量和誤差評定的能力,要實現輪廓的在機測量,必須在數控機床本身能力的基礎上,集成具有測量能力的裝置,并開發具有誤差評定功能的軟件。因此,有效的系統集成是實現在機輪廓測量的關鍵。如圖 1 所示,在 HTC50100車銑復合加工中心上集成了 Marposs 接觸式在線測量裝置,采用以太網經由無線路由器實現上位機和數控系統的連接與通訊。
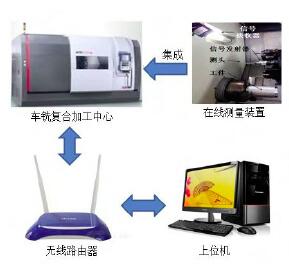
圖 1 在線測量系統組成
1.1 在線測量裝置與數控系統的集成
本次試驗使用的測量裝置為 Marposs E83L 加工中心專用觸發式測量系統[4],主要由信號發射器、測頭和信號接收器組成。其中信號發射器和測頭作為刀具裝在刀塔上,發射器和接收器之間通過紅外傳輸的方式連接。接收器接收發射器發射的紅外信號,并傳送給 CNC 系統,同時通過指示燈的變化,顯示測量系統當前狀態。例如:若程序運行有問題,“Error”指示燈會閃爍;當其接收到觸碰號時,“Probe Status”指示燈會閃爍等[5]。可以根據指示燈的狀態,判斷測量系統的工作情況,并合理的處理異常情況,信號接收器與 CNC 系統具體接線如圖 2 所示。

圖 2 信號接收器與數控機床的接線圖
在實現程序跳轉時,利用的是 FANUC 數控系統的高速跳轉指令,即 G31 指令。該指令通常只用于測量功能,需要外部輸入信號,輸入信號地址是X4.7。G31 執行過程中如果沒有 SKIP 信號則和G01 完全一樣,如果在執行過程中 SKIP 信號置“1”,則在 SKIP 信號置“1”的位置清除剩余運動量,直接執行下一個程序段。在 SKIP 信號置“1”時,進給軸的坐標值會儲存在系統變量中,供測量宏程序計算使用。本研究中當測頭觸碰到工件后,信號接收器就可以將觸碰信號傳送給 CNC 系統,以實現程序跳轉。圖 3 所示為跳轉功能示意圖。
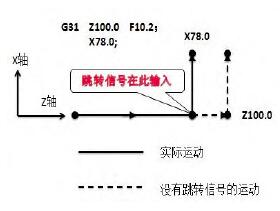
圖 3 G31 跳轉功能示意圖
1.2 上位機與數控系統的集成
隨著科技的發展,數控系統也得到了進一步的完善。現在數控系統不僅具有通信功能,能夠通過以太網實現與上位機連接,而且為用戶提供了許多工具包和函數庫,供用戶更好的開發和使用。
本次試驗通過以太網實現上位機與數控系統的集成,然后利用 FANUC 系統提供的 focas 函數庫cnc_download3(unsigned short Flib Hndl, long *length, char *data)以及 cnc_rdmacro(unsigned short Flib Hndl, short number, short length, ODBM *macro)函數,實現對數控系統內存中宏變量的讀寫,進而通過上位機軟件對工件輪廓作出評價。
2 、輪廓檢測的實現
要實現回轉型零件的輪廓檢測,不僅僅需要硬件的投入,也要軟件的支撐。本次試驗所使用的軟件主要是基于 VC 平臺開發的,其中評定算法是利用 Matlab 語言編寫并編譯成 COM 組件,發布后供上位機軟件調用。軟件功能組成如圖 4 所示。檢測軟件主要分為三個模塊,即數控程序生成模塊、數據采集模塊以及輪廓誤差評定模塊。
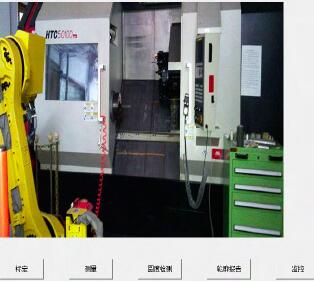
圖 4 輪廓在機檢測軟件界面
2.1 測量程序生成模塊
數控程序生成模塊主要用于生成實現在機測量的數控程序,并通過以太網下載到數控系統。這里采用靈活方便、易于操作的數控宏程序編程,實現輪廓測量中的簡單算術運算、邏輯控制功能[6]。例如,圓度循環測量的宏程序:
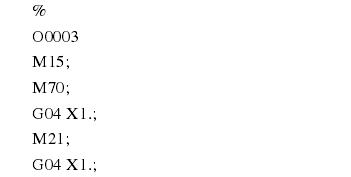
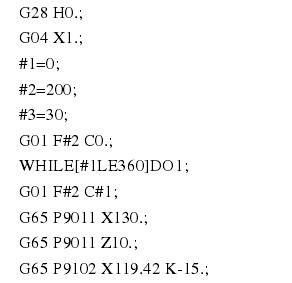
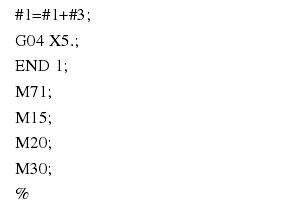
其中 M71/M70 為測頭系統的開關指令,M70為開;M21 為由車銑床狀態轉換,這是因為圓度評定需要在工件圓周上均勻選取 12 個點,C 軸必須可以精確轉到指定角度,故應在銑床狀態下進行;然后是循環測量,其中 P9011 為安全移動宏程序,P9102 為 X 軸方向單一測量宏程序,我們只需輸入必要參數,即可實現我們理想的運動軌跡和要求。測量程序在上位機中生成界面如圖 5 所示。
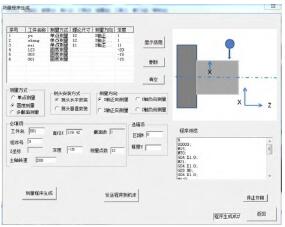
圖 5 測量程序生成模塊
2.2 數據采集模塊
數據采集模塊負責對數控系統宏變量的讀取和設置,采集并保存測頭觸碰工件時工件尺寸。為此我們利用 FANUC 系統提供的 focas 函數庫,在上位機中基于 VC 平臺開發了一個數據采集模塊,利用focas 函 數 庫 中 cnc_download3(unsigned short Flib Hndl, long *length, char *data) 以 及cnc_rdmacro(unsigned short Flib Hndl, short number, short length, ODBM *macro)函數實現對數控系統內存中宏變量的讀寫訪問,最后保存在數據庫中,以便進行處理。具體界面如圖 6 所示

圖 6 數據采集模塊
2.3 輪廓誤差評定模塊
輪廓誤差評定模塊負責對采集的數據分析處理并做出評定,實現對回轉型零件輪廓的在機檢測。為此我們基于 VC 和 Maltab 平臺開發了一個輪廓誤差評定模塊,用于評定零件的輪廓誤差[7]。具體過程是首先利用 Matlab 完成圓度、圓柱度、圓錐度等評估算法程序的編寫并編譯成 COM 組件,然后利用 VC 調用編譯好的 COM 組件完成計算和評估。圖 7 為零件輪廓誤差評定界面。
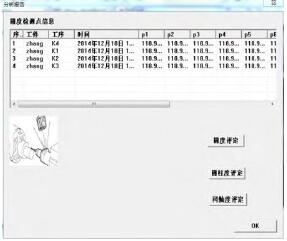
圖 7 輪廓誤差評定模塊
3 、在機輪廓檢測的誤差分析
在機輪廓檢測系統雖然有效的避免了二次裝夾帶來的誤差,但也不可避免的引入了機床、測量裝置等硬件的系統誤差,因此,采取有效的方式減少這些誤差才是保證在線輪廓檢測準確性的有效途徑[8]。
影響在機測量精度的主要包括機床幾何誤差、測頭安裝誤差、測頭系統誤差[9]。首先,對于機床幾何誤差是由制造、安裝不善產生的機床導軌誤差、運動部件誤差、導軌間位置誤差等因素綜合影響的,它直接影響著機床坐標系統的精度,是影響在機測量精度的一個重要因素,這部分誤差主要由機床本身決定;對于測頭安裝誤差,這是影響測量精度最大的可控因素,因為測頭是人為地裝夾在刀塔上的,所以為了最大限度的減小測頭安裝誤差的影響,一方面,我們在對刀后,會用千分表校正測頭位置,使測頭和測桿盡量和 Z 軸重合,另一方面,在執行測量程序前,我們會先運行標定程序,這是由于千分表校正后仍會有誤差存在,通過標定程序可以把這些微小誤差測量出來,并保存在固定的宏變量里,當執行測量程序時,再通過調用這些宏變量將誤差消除掉;對于測頭系統誤差,這是由其測量原理決定的,由于本測量裝置是觸發式的,當測頭觸碰工件后會有一定的預行程,因此,必須保證使每次測量時預行程是相等的,所以標定和測量程序中當測頭觸碰工件時必須具有相同的速度,以減小測頭系統誤差的影響。
4 、實例分析
為了驗證在機輪廓測量的可行性,我們基于以上設施,設計了如下的車削加工及在線測量實驗:首先在車床狀態下對工件進行外圓切削,然后在工件圓柱表面上等間距地取四個截面,并在銑床狀態下進行輪廓測量。通過使用上位機中的測量程序生成模塊生成測量宏程序,并由以太網下載到數控系統內。工件每轉 30°測量 1 次,通過上位機軟件采集和保存測量結果。程序運行完畢,所得的測量結果表 1 所示。
表 1 測量結果
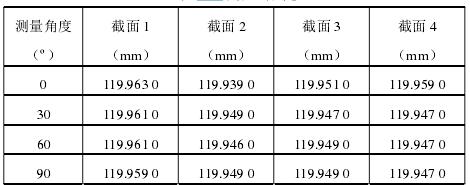
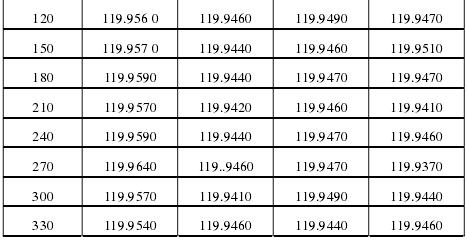
對于以上保存的數據,直接調用輪廓誤差評定模塊進行處理,結果如下:
表 2 圓度誤差評定結果

表 3 圓柱度誤差評定結果

表 4 同軸度誤差評定結果

5 、 結語
通過在車銑復合加工中心上集成在線測量技術,實現了對回轉型工件輪廓的在機測量。雖然文中只是針對圓柱型工件進行的輪廓形狀誤差評定,但相似的測量過程,配合不同的輪廓誤差評定方法,還可以推廣應用在凸輪等具有非圓曲線工件的輪廓檢測中。相比于離線測量,在機輪廓測量不僅能夠避免二次裝夾帶來的誤差,提高測量效率,檢測結果還可以快速反饋至數控系統用以補償加工誤差,或者上傳至車間層用于生產管理,有利于構建無人化、自動化生產車間。
投稿箱:
如果您有機床行業、企業相關新聞稿件發表,或進行資訊合作,歡迎聯系本網編輯部, 郵箱:skjcsc@vip.sina.com
如果您有機床行業、企業相關新聞稿件發表,或進行資訊合作,歡迎聯系本網編輯部, 郵箱:skjcsc@vip.sina.com
更多相關信息