高速機床直線電動機進給系統熱行為分析
2019-3-13 來源:上海工程技術大學 上海理工大學 作者:吳倩倩 林獻坤
摘 要: 在高速機床中,以直線電動機驅動的進給軸為對象,應用有限元工具對全閉環位置反饋的進給機構的熱源分布進行了分析,給出模型的簡化方法,確定了進給軸熱載荷相關參數,對進給軸 Y 軸的熱變形特性進行了定性分析。在自構建的實驗臺上,對直線電動機驅動進給軸 Y 軸的熱變形特性進行了綜合試驗研究,確定了熱電偶、激光干涉儀、電容式測微儀的熱變形試驗方案和試驗步驟,
分析了直線進給軸穩態溫度分布及其熱變形規律。結果表明:主軸刀具位置熱偏差是由滑臺受熱扭曲熱位移、光柵尺膨脹熱位移和導軌俯仰角偏熱位移的三者綜合作用的結果;短行程的主要因素是滑臺扭曲變形和導軌角偏,長行程的主要影響因素為光柵尺的熱變形。
關鍵詞: 高速機床;直線電動機;熱變形;有限元
效率和加工精度是當代先進制造領域的一個重要課題,高速和高加速度的切削進給軸是實現高速高精密切削加工的重要條件之一。傳統的“旋轉伺服電動機 + 滾珠絲杠”式進給軸的傳動機構存在螺距誤差、反向間隙、磨損、摩擦以及螺桿本身的彈性變形等問題。直線電動機驅動進給軸是一種不需要中間轉換機構的傳動裝置,具有進給速度快、加速度大、響應速度快、定位精度高等優點],直線電動機驅動的進給軸突破了傳統的滾珠絲杠式進給軸在速度和精度方面的限制,在高速高精密機床中得到越來越廣泛的應用。
機床誤差源中,熱誤差原本就是精密機床最主要的誤差源之一,可占到機床誤差的 70%。在高速進給條件下,直線電動機初級線圈發熱量大,溫度可達100 ℃ 以上,由于熱變形因素在一定程度上影響了它在精密機床中的應用。關于直線進給軸的熱變形及其帶來的熱誤差問題,在國外已經得到較大關注,EUNI U研究了隔溫層對直線進給軸熱行為的作用效果;KIM J J 等應用有限動軸的熱行為作用效果; 在國內,對直線電動機驅動機床進給軸及其特性的研究,主要集中在: 進給軸平臺的滑??刂?、直線電動機驅動進給軸的輪廓精度在線補償方法等,但對于機床直線電動機驅動進給軸的熱行為研究還較少。
本文采用有限元分析與試驗測試結果分析相結合的方法,對高速直線電動機驅動進給軸進行的熱行為進行研究。應用 Solid Works Simulation 對機床熱源進行有限元分析,定性地分析高速機床直線電動機驅動進給軸 Y 軸的溫度場分布及其變化規律,以仿真分析結果為基礎,制定合理的試驗方案,對進給 Y 軸的熱源分布和熱變形進行了試驗研究,將模型仿真結果與試驗測試結果進行對比分析,定量分析了由熱變形引起的直線電動機驅動 Y 軸進給誤差的各組成要素及其變形規律,研究成果為直線進給軸的優化設計及其在精密機床中的應用提供重要理論支持。
1 、有限元仿真分析
1. 1 建模對象
實驗對象為自構建的直線電動機驅動龍門結構進給機構,該進給機構具有 X1、X2、Y、Z 多軸聯動結構,本文以 Y 軸進行有限元分析對象,其結構如圖 1 所示,其中 Y 軸依靠 A 與 B 兩端分別固定于 X1、X2 軸上,帶動主軸與 X1、X2 軸聯動,其中 A 端與 X1 軸鉸接,B 端與 X2 軸滑塊連接,進給 Y 軸通過上、下兩根導軌支撐主軸滑臺高速進給運動。
Y 軸的直線電動機型號為 SIEMENS 1FN3,位置環反饋選用 LC183 型號的光柵尺,在數控系統作用下實現進給軸全閉環位置反饋進給。
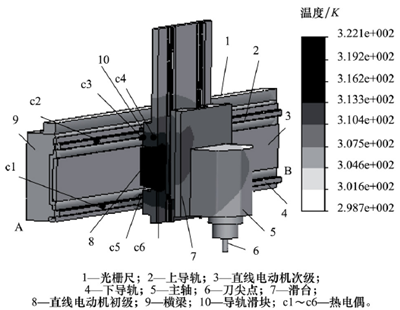
圖1 進給Y軸溫度場分布及溫度測點布置
1. 2 模型假設
直線進給軸所具有的對象存在多個部件,結構較復雜,應用有限元直接進行建模仿真較為困難,簡化對象模型是有限元分析常用方法。因此,在建模過程對模型做了如下假設:
(1) 不考慮外部熱源通過熱輻射對進給軸的影響,進給軸上的熱源也不通過熱輻射影響進給機構部件。
(2) 支撐滑臺運行的所有導軌滑塊直接與滑臺固結一體,兩者之間不存在熱阻,也不產生相對熱位移。
(3) 簡化導軌滑塊內的滾動摩擦為滑動摩擦,假設導軌和運動的滑塊之間熱阻無限大,但有熱流量均勻作用在導軌和滑快的表面上,滑塊的熱變形不施加附加作用力給導軌表面。
(4) 進給軸換熱表面的對流傳熱系數是一個常數,不受進給軸溫度和機構的形狀分布影響。
1. 3 熱載荷參數的確定
定義進給機構的熱載荷分布,包括: 直線電動機初級發熱量 Qm; 初級側的線圈與滑臺之間靠螺栓連接兩者之間存在熱阻,用 Rt表示; 滾動摩擦產生的熱量以及滑臺與導軌溫度差的熱傳導熱量總
和,作用在導軌表面上,用熱流密度 qG表示; 與導軌接觸滑塊表面的熱量包含摩擦熱與熱傳導兩部分,用熱流密度 qs表示,進給機構表面的熱對流系數 αc。
根據數控系統中獲取的直線電動機運行流Ieff,及最終熱穩態溫度 Td,可采用如下公式,計算電動機熱損耗功率:
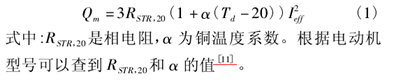
依據文獻,給出的空氣熱對流系數計算方法,可以近似確定熱對流系數 αc; 再根據熱穩態試驗,可以仿真計算得到圖 1 中示意的 c2、c3、c5 點的溫度,依據其溫度和溫度差分布,經過重復仿真模擬,可初步確定熱流密度 qG、qs以及熱阻 Rt的組合值。根據理論分析和重復驗證這種方法,以最大推力 1 470 N 的1FN3 直線電動機進行計算,得到如表 1 所示熱載荷參數。
表 1 熱載荷參數
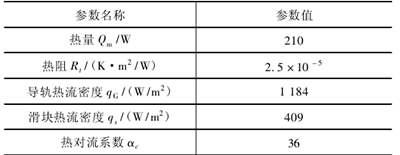
1. 4 模型分析
應用 Solid Works Simulation 有限元分析,對直線進給軸 Y 軸進行建模,選擇合適的網格密度對進給軸進行網格劃分,總共生成 23 813 個單元和 41 081 個單元節點。應用這些熱載荷參數,以 298 K 為環境溫度,計算得到如圖 1 所示的進給軸熱穩態分布。從圖 1 中可以看出直線電動機初級溫度最高,是進給軸中最主要熱源,直線進給軸上、下導軌的溫度場分布基本一致。
應用該穩態熱力算例和所建立有限元網格,進一步建立靜態熱位移算例,參考建模對象的裝配約束方式,定義橫梁 A 端為固定幾何體型約束,B 端為滾柱/滑桿約束。求解靜態熱位移算例可得到熱合位移,經過三維分量獨立分析可知,Y 軸向的熱位移明顯比 Z軸向和 X 軸向的熱位移大,因此 Z 軸向和 X 軸向在熱變形中不再考慮。圖 2 中以 1 776 倍的變形比例表示了 Y 軸向的熱變形圖解示意圖,圖中 Y 軸向的最大熱變形量已達到了 40 μm 以上,主軸刀尖點沿 Y 向的熱誤差值最大。
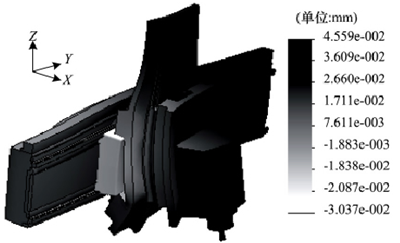
圖2 熱變形示意圖
綜合分析圖中主軸刀尖在 Y 軸進給運動過程中的熱位移,熱位移由光柵尺膨脹熱位移、Y 軸向俯仰角偏熱位移和滑臺本身在 Y 軸向的扭曲熱位移三個部分組成。其中進給軸采用全閉環位置定位反饋,導軌受熱沿 Y 向伸長不會影響刀尖點的軸向定位,但光柵尺膨脹變形在 Y 向的熱位移量則直接決定進給軸的定位精度; Y 進給軸上、下導軌對稱安裝,溫度分布基本一致,上、下導軌在 Z 方向的膨脹量相當,膨脹方向相反,在 Z 向的變形,作用到 Y 向上的位置誤差可以相互抵消不產生軸向旋轉偏差,但在 X 方向上,上下導軌膨脹的方向相同,這種膨脹對刀尖點在 Y 向的定位通過軸向俯仰角偏產生影響,具體作用機理如圖 3所示。圖中進給軸導軌在 X 方向上的膨脹導致進給軸發生角偏,假設大小為 θ,刀尖點也隨之發生 Y 軸向位置偏差 e,可表示為:

式中: L 為刀尖點到 Y 軸導軌的垂直距離; e 為 Y 軸向偏差; θ 為角偏。
由式(2) 可知,Y 軸向偏差 e 受 L 和 θ 兩個因素影響。
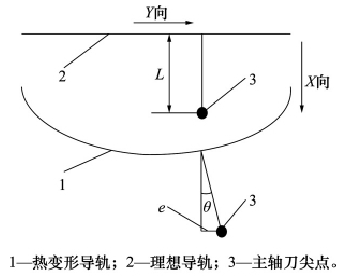
圖3 導軌角偏示意圖
2 、實驗研究
2. 1 試驗測試系統的構建
為了進一步對模型仿真結果做定量驗證,本文通過構建如圖 4 所示的試驗系統進行試驗研究。
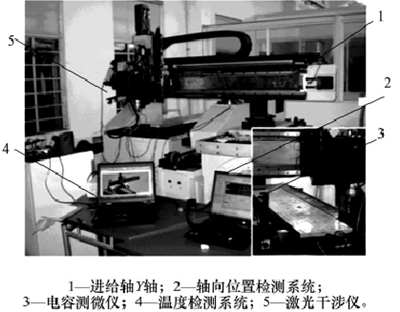
圖4 熱行為實驗系統
圖 4 中溫度檢測系統由熱電偶、XMDA - 16 智能多點溫度巡檢儀與 Visual C + + 開發的溫度數據采集軟件實現,試驗擬采用 8 個熱電偶,其中熱電偶 c1 ~c6 的分布位置如圖 1 所示,熱電偶 c7 位于標尺光柵上,用來測試標尺光柵溫度,c8 用于測試環境溫度,設置溫度采集周期為 15 s。進給 Y 軸定位誤差由 MCV- 500 激光干涉儀測量,該傳感器的測量精度為 0. 1μm,測量行程可達數十米,激光干涉儀配備 X、Y 兩套激光頭組件,為了理清光柵尺變形的影響成分,把 X激光頭組件的反射鏡固定在標尺光柵附近,用來測量標尺光柵位置誤差; Y 激光頭組件的反射鏡固定在主軸上,用來測試主軸位置誤差,試驗中選用 Y 軸向定位自動檢測系統測量位置誤差數據。另外選用 ca-pa NCDT6100 電容測微儀測量滑臺變形。
2. 2 試驗方法
編寫機床 G 代碼,使進給軸 Y 軸帶動主軸滑臺在坐標 Y( 200,800) 區間作高速往復進給,設置進給速度為 60 m/min,進給加速度為 3 m/s2。為了配合激光干涉儀測試進給軸位置誤差,每隔
30 min,設置進給軸在Y( 200,800) 區間沿 Y 正向等步長間歇進給,步長為 30mm,每進給一個步長暫停 4 s,測試過程的進給速度為500 mm / min。具體的試驗步驟如下:
步驟 1 采用激光干涉儀對主軸刀尖點和 Y 軸光柵尺,進行一次機械安裝偏差對位置影響的測定,作為機床的初始偏差;
步驟 2 控制機床使主軸停在起點 Y200 處,用電容測微儀測試機床主軸刀尖點位置一次;
步驟 3 編寫機床工作 G 代碼,驅動 Y 軸在 Y( 200,800) 區間連續作高速往復運動,30 min 后中止;
步驟 4 編寫測試 G 代碼,驅動滑臺沿 Y 軸正向作30 mm 等步長間歇進給,同時激光干涉儀采集 Y 軸位置誤差數據一組;
步驟 5 重復步驟 3 和 4,直至各測點溫度上升曲線趨平緩,達到熱平衡,最后采集一組位置數據。
整個測試過程歷時 270 min,共采集 8 個 測 點1 243個時間點的溫度數據、9 組主軸位置誤差數據、9組標尺光柵位置誤差數據和 2 組滑臺扭曲變形數據。
3、 結果分析
3. 1 溫度場分析
采用上述的試驗方案完成對 Y 軸的溫度測試,各測點的時間 - 溫度曲線如圖 5 所示。圖中曲線表明,在高速重復進給過程中,機構的各個測點溫度均呈逐步上升趨勢,在 180 min 后,曲線變得平緩,說明測點達到了熱平衡。由圖 5 可知,直線電動機初級附近測點 c5、c6 的溫度明顯高于其他測點溫度,說明直線電動機初級是機床直線進給系統的主要熱源,c5 比 c6更靠近熱源,所以 c5 比 c6 的溫度高。
上、下導軌測點 c1、c2 及兩個滑塊測點溫值相差不大,說明作用在上下導軌摩擦產生的熱量基本一致。通過分析比較熱電偶所有測量點的溫度與有限元仿真得到的溫度,二者基本吻合,其中最大的偏差小于 1℃ ,所用的有限元模型較好地仿真了進給軸溫度分布。另外,溫度曲線存在周期性的毛刺,毛刺發生的時間點對應測試位置誤差的時間點,主要原因是低速進給造成對流換熱表面的傳熱系數降低導致溫度升高。
3. 2 熱變形分析
在機床產生熱變形前,采用激光干涉儀對主軸刀具位置和光柵尺進行一次測定,用以排除機械安裝誤差。如圖 6 所示,圖中曲線 1 和曲線 4 分別為激光涉儀測量的熱變形前光柵位置偏差和滑臺沿 Y 方向移動的主軸刀具位置偏差。為了消除機械安裝誤差的影響,利用最小二乘法擬合光路直線,將測量曲線減去擬合直線,得到光柵尺和主軸位置軸向機械偏差,為圖6 中的曲線 2 和曲線 3 所示。

圖5 時間-溫度曲線
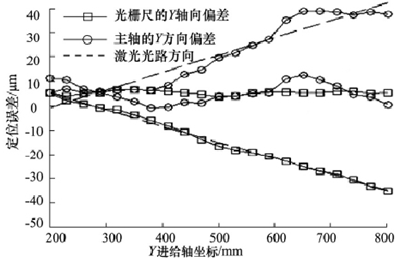
圖6 Y軸安裝誤差的測量
獲得機械本身的安裝偏差后,對進給軸 Y 軸達到熱平衡時的變形進行測量,得到圖 7 所示的變形趨勢。圖 7 中曲線 1 是主軸刀具進給位置去除機械偏差之后的 Y 軸向定位熱變形偏差,曲線 2 是光柵尺去除機械偏差之后的 Y 軸向定位熱變形誤差,為了比較分析熱變形的分量,圖中引入有限元仿真的變形結果并作對比。圖 7 中曲線 4 是有限元仿真計算得到光柵尺膨脹熱變形,曲線 5 是導軌俯仰角偏帶來了主軸位置 Y 軸向偏差分量,曲線 3 是 Y 軸滑臺熱變形、光柵尺膨脹熱變形和導軌俯仰角偏帶來的主軸刀具位置 Y 向偏差三者變形的總和。
綜合分析圖 7 中的比較結果可見,曲線 3 和曲線 1基本接近,最大偏差不超過 10 μm,且曲線 1 都落在偏離實際測量的 Y 軸向偏差帶范圍( 圖中兩虛線之間) 之內; 曲線 2 和曲線 4 兩者之間偏差更小,在 800 mm 處的偏差也只有 3. 2 μm; 由電容測微儀測得的 Y 軸滑臺熱變形 9. 1 μm,而用有限元分析的 Y 軸滑臺熱扭曲變形在刀尖點處的偏差是 8. 8 μm,這些比較表明,有限元仿真分析過程所采用的熱載荷參數是準確的。
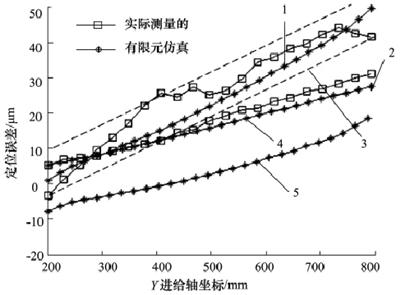
圖7 Y軸變形測量與仿真比較
對比曲線 1 和曲線 2,光柵尺熱變形是影響進給軸誤差的關鍵因素,因此在設計中減少對光柵尺傳熱量對于提高定位精度具有重要作用。另外,曲線 3 和曲線 1 的偏差較小,進一步表明: 光柵尺熱膨脹變形、滑臺熱扭曲變形和導軌俯仰帶來的進給偏差是共同導致主軸刀具定位位置熱誤差的主要因素。圖 7 中曲線2 可知,由于受到熱膨脹的影響,光柵尺的定位發生偏差,行程越長,偏差越大,且偏差基本是線性。
為了對進給系統熱變形進行定量的分析,取機床Y 坐標 800 mm 處的點,進行對比分析,因熱膨脹光柵尺變形引起的偏差 26. 9 μm,導軌角偏引起的偏差13. 5 μm,滑臺受熱扭曲變形 9. 0 μm。由此可見,在重復短行程的定位中,主要熱誤差是滑臺受熱扭曲變形和導軌角偏引起的; 在超過 600 mm 的長行程重復進給中,光柵尺的熱變形影響主軸刀具位置的比例將大于 50% ,光柵尺的熱膨脹變形是引起進給軸 Y 軸熱誤差的關鍵因素。
4 、結語
(1) 通過試驗和理論分析相結合,應用有限元模型可以較好地分析直線進給軸熱穩態溫度分布和進給軸熱變形趨勢。
(2) 直線電動機初級線圈發熱是導致機床進給系統熱誤差的主要原因。為減小直線電動機驅動進給系統熱誤差,可以優化機床結構設計,采取良好的冷卻和隔熱系統。
(3) 直線進給系統熱變形引起的主軸刀具位置定位誤差主要是由光柵尺受熱膨脹變形誤差、導軌俯仰角偏差帶來的進給偏差和滑臺熱扭曲變形偏差三個部分組成。
(4) 熱誤差的主要影響因素,根據行程的長短有所不同,短行程的主要因素是滑臺扭曲變形和導軌角偏,長行程的主要影響因素為光柵尺的熱變形。
投稿箱:
如果您有機床行業、企業相關新聞稿件發表,或進行資訊合作,歡迎聯系本網編輯部, 郵箱:skjcsc@vip.sina.com
如果您有機床行業、企業相關新聞稿件發表,或進行資訊合作,歡迎聯系本網編輯部, 郵箱:skjcsc@vip.sina.com
更多相關信息