伺服驅動加工定位控制方式
2015-2-23 來源: 福建船政交通職業學院機械系 作者:林祥勇
摘 要:針對某模塊化生產加工系統生產制造過程中設備定位問題,設計一種采用伺服電機、PLC和觸摸屏為主體,可自動測量并顯示絕對坐標位置,并自動定位的控制系統。加工重復定位精度可達0.01mm,減輕了工人工作強度,提高了勞動生產率。
0 、引 言
在亞龍公司的335BMPS模塊化自動化生產線的生產制造過程中,生產線各單元模塊在組裝成功后需要放置在生產線的指定位置,該位置的的定位往往是工人根據生產圖紙的尺寸進行定位,采用人力搬運并通過人工校準來進行模塊單元安裝調整,由于系統安裝中存在誤差,每臺生產線都必須通過生產線的單步試運行功能將物料逐一通過生產線的各個單元模塊,并再次通過人工調整對單元模塊定位微調,從而保證每條生產線出廠的合格性。這就導致調整時間長、效率低,花費大量的時間,并且通過反復調整以提高定位精度,從而使該生產線的生產周期大大延長。同時,在設計上該MPS模塊化生產線將機械手固定在導軌的初始點,從而通過伺服電機帶動導軌運行達到機械手在各生產線模塊之間的往返的目的。在定位精度上如果機械手與單元模塊之間的精度一旦出現2mm 以上的誤差,在運行時機械手在擺動氣缸的作用下必定在90°旋轉時碰撞上單元模塊的機械部位從而導致事故,因此,在生產過程中的定位又具有至關重要的作用。為減輕工人勞動強度,加快設備精度定位方式,文中在該MPS模塊化生產加工系統硬件的基礎上,設計了一種采用伺服電機、PLC和觸摸屏為主體,可自動定位并顯示絕對坐標的定位測試方法,該方法精確度可達0.01mm,減輕了工人工作強度,同時,在生產任務發生變化時更換不同的加工模塊也可以實現快速、精準的定位,提高了生產線的生產效率。
1 、MPS模塊化生產加工系統及設計思路
目前,浙江亞龍公司的335BMPS模塊化生產加工系統將工作單元分別進行檢測、加工、搬運、安裝、分類等制作過程,各工作單元分工明確又相互協調。MPS模塊化生產線加工系統結構如圖1所示。
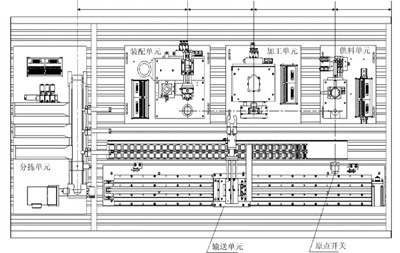
圖1 MPS模塊化生產加工系統
圖中供料、加工、裝配等單元分別完成特定生產內容,輸送單元負責將原料通過供料單元、加工單元、裝配單元進行生產,最后將成品送入分揀單元分揀出合格品。原設計中輸送過程系統通過內置程序進行定位目標單元點,利用導軌控制機械手的擺動用機械手抓緊物料將物料放在各模塊單元的初始位置,若位置誤差略大,則機械手在擺動時必定與模塊單元的機械部分之間發生碰撞,造成損傷及事故,因此,各模塊單元的初始放置點的定位對精度要求很高。特別在設備的大量生產過程中單純依靠人工搬運模塊單元并進行人動調整,不但對工人熟練度及精細度要求很高,同時也使得勞動強度大大加強。
因此,該自動定位測試方式的思路改變以往讓機械手“跟著”單元模塊走的定位方式,而改成通過給定機械手位移坐標,根據不同規格的生產線設計要求,當機械手運行到不同單元模塊的位置,同時在觸摸屏上實時顯示機械手的運行位移,再根據機械手的停放位置直接將單元模塊進行實時放置,實現一次性定位成功。同時,克服了每臺生產線的誤差問題可能造成的機械事故,由于機械手的運行通過伺服電機完成,在位置控制上實現定位精度可達0.01mm。
2 、系統組成
系統上采用三菱觸摸屏F940GOT-LWD及三菱FX1N-40MTPLC為主控制器 ,并利用觸摸屏進行模塊單元的位移運行控制,其中三菱PLC為系統核心,完成模擬量輸入、開關量輸入狀態檢測、開關量輸出控制以及整個系統的過程控制。觸摸屏實現人機界面,完成相關數據、信息、狀態顯示和參數設置,與PLC通信進行數據交換和相關控制。
系統控制電源接通后,首先初始化PLC和觸摸屏;然后PLC自動檢測系統的啟動條件,氣壓是否達到有效設定值,輸送單元是否處于原點,非原點則執行原點返回程序;與伺服通信是否正常,觸摸屏通信有無故障,若條件不滿足,系統等待并發出報警信號;若啟動條件滿足,PLC根據位置量要求控制伺服系統運行并將運行位置及運行速度反饋在觸摸屏上,通過觸摸屏輸入不同位置的設定值控制其自動定位。
3、 伺服控制系統
伺服控制系統由伺服驅動器、伺服電機和齒輪傳動機構構成,實現對各工作單元及檢測裝置進行精確定位,是該方法的關鍵部分。通過伺服驅動器控制伺服電機運行,運行到位后通過PLC實時監測得到的運行距離,即實際測量值與自動計算后得到的脈沖量同時顯示在觸摸屏上,操作人員根據得到的實際測量值進行模塊單元的一次性安裝,調整完畢后再進行下一個定位點的自動測試,即使生產任務發生變化,不同的單元模塊進行更換,只要將存儲器內位移量直接改變即可,方便可靠。同時,伺服系統將定位精度控制在0.01mm。控制模式如圖2所示。
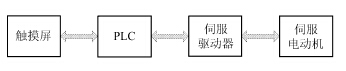
圖2 控制模式
在伺服控制中通過原先生產線自帶的松下MHMD022P1U 永磁同步的交流伺服電機及MADDT1207003全數字交流永磁同步伺服驅動裝置作為運動控制裝置。該交流永磁同步伺服驅動器主要有伺服控制單元、功率驅動單元、通訊接口單元、伺服電動機及相應的反饋檢測器件組成,其中,伺服控制單元包括位置控制器、速度控制器、轉矩和電流控制器等,如圖3所示。
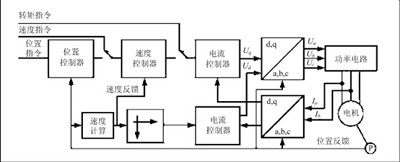
圖3 伺服控制單元
根據該伺服控制單元,將機械手需要的位移運行量換算成伺服驅動器接收的脈沖頻率,同時,由于對位置和速度的精度要求控制在0.01mm,故使用伺服驅動器位置控制模式,位置控制模式采用位置環、速度環、電流環三環控制結構,PLC給定高速脈沖信號n1送到位置控制器,控制伺服電機運行,即進行直線位移,與通過位置反饋得到的電機實際轉動脈沖數n2比較,誤差信號Δn=n1-n2,經過位置調節器PID調節后,輸出轉子轉速給定信號m1,實際轉子轉速反饋信號m2,速度誤差信號Δm=m1-m2送到速度控制器,再經過PID調節后輸出伺服電機交軸電流信號i1,與實際交軸電流i2比較,得出交軸電流的誤差信號Δi=i1-i2,電流控制器輸出PWM 控制信號,使伺服電機按給定脈沖數運行,并控制運行精度。位置控制模式下,電子齒輪等效的單閉環系統方框圖如圖4所示。
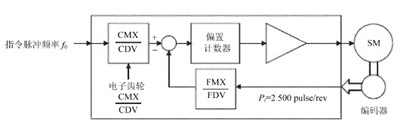
圖4 等效的單閉環位置控制系統方框圖
圖中指令脈沖信號和電機編碼器反饋脈沖信號進入驅動器后,均通過電子齒輪變換進行偏差計算。電子齒輪可以用來任意設置每單位指令脈沖對應的電機速度和脈沖當量,由于FX1N-40MT 作為上位控制器最高脈沖輸出頻率為100kHz,受其限制,使用電子齒輪功能,以減小給伺服驅動器發送脈沖的頻率。
對應脈沖計算公式為
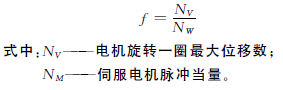
設伺服電機旋轉一周移動60mm,松下MINASA4系列AC伺服電機驅動器,電機編碼器反饋脈沖為2 500pulse/rev。由于伺服電機脈沖當量為0.01mm,減速比為1,則電機運行一圈所需的脈沖數為:
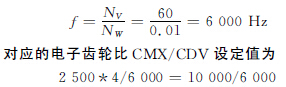
伺服驅動器與PLC及伺服電機的接線圖如圖5所示。
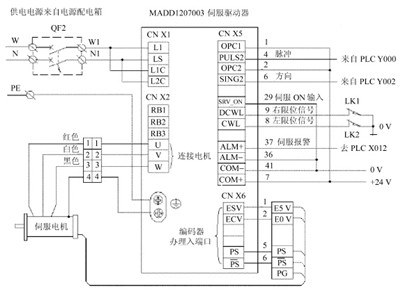
圖5 伺服驅動器接線圖
4、 系統軟件
通過原位行程開關作為原始點定位,通過PLC相關復位程序進行上電初始位置檢測,PLC在復位后等待PLC相關檢測程序對各輸入單元及故障報警進行診斷,并配置報警指示燈。PLC的I/O端口資源分配表見表1。
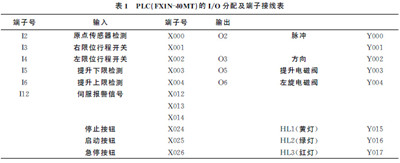
在系統正常運行后,等待觸摸屏發出控制指令,通過觸摸屏上由調試人員輸入運行距離,啟動運行按鈕,使伺服電機自動移動到目的地。同時,在觸摸屏上設置絕對位置位移顯示框可以實時得到電機運行的實際距離,從而確定絕對位置的精度,還可以根據需要改變伺服電機的運行速度。所設計的軟件流程如圖6所示。
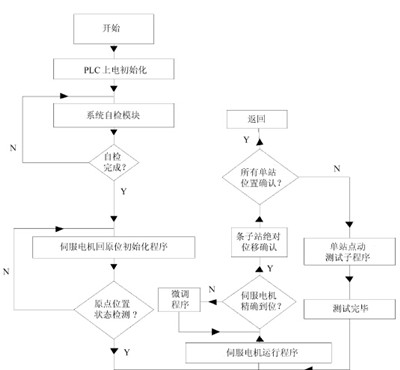
圖6 軟件流程圖
在控制過程中,核心為觸摸屏組態程序和PLC控制程序,其中,觸摸屏組態程序主要負責實時監控機械手的運行速度、運行距離,并可實時微調。PLC控制程序主要是輸出脈沖當量進而通過伺服驅動器來控制伺服電機運行,從而起到精確定位的作用。相關控制程序如圖7所示。
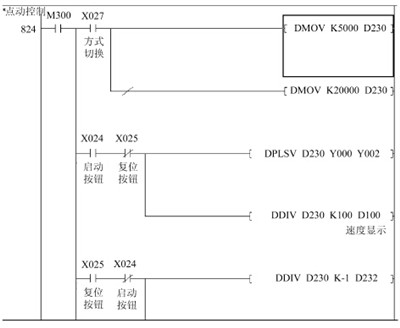
圖7 相關控制程序
通過三菱觸摸屏設置啟動及暫停按鈕進行測試控制,并同時在線可看到機械手當前運行位置,使安裝人員直接根據系統反饋的位置量進行單元模塊的精確定位,避免了系統誤差。控制界面如圖8所示。
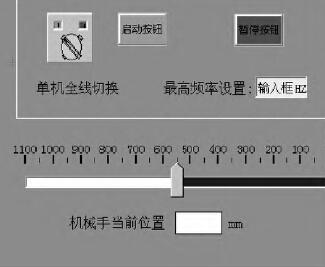
圖8 控制界面
5 、結 語
采用伺服電機、PLC和觸摸屏為主體,通過系統給定值自動測量并顯示絕對坐標值,同時自動定位,并且將定位精度控制在0.01mm;在實際生產過程中,替代原有的人工測量、定位,減輕了設備安裝過程中工人反復安裝的工作強度,節省安裝時間,提高了勞動生產率。實踐證明,該方法定位可一次性定位、速度快、精度高,杜絕了機械碰撞損壞等問題,保證系統運行可靠。同時,在類似系列的生產線上都可以通用,且具有易修改、易實現的特點。
投稿箱:
如果您有機床行業、企業相關新聞稿件發表,或進行資訊合作,歡迎聯系本網編輯部, 郵箱:skjcsc@vip.sina.com
如果您有機床行業、企業相關新聞稿件發表,或進行資訊合作,歡迎聯系本網編輯部, 郵箱:skjcsc@vip.sina.com