淺談機床主軸的差異化特性
2017-4-27 來源:廣州市昊志機電股份有限公司 作者:聶浩鋒,李德恒
摘要:作為機床最核心的部件,機床主軸的性能直接決定著機床的加工性能。根據機床主軸傳動方式,可分為齒輪式主軸、皮帶主軸、直聯主軸和電主軸。著重通過對比的方式介紹各類主軸的特性,為工程師在設計機床時對主軸選型提供技術支持。
關鍵詞:機床;主軸;電機;特性
1.機床主軸的常用類型
1機床主軸是指機床上帶動工件或刀具旋轉的軸。目前,市面上絕大多數機床主軸為皮帶或直聯主軸。齒輪式主軸已逐漸退出舞臺,在此不做討論,而電主軸以其獨特的優勢正不斷擴大市場份額。皮帶主軸的電機在主軸后上方,通過皮帶、連接座等部件連接主軸,如圖 1 所示;直聯主軸的電機與主軸在同一軸線,通過聯軸器連接主軸,如圖 2 所示;電主軸的電機藏入主軸內部,與主軸結合成一體,如圖 3 所示。
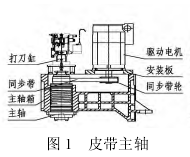
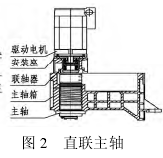
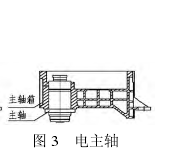
2.機床主軸的特性
由于傳動方式的區別,各類主軸在使用中存在明顯的性能差異。下面我們從占用空間、安裝難度、極限轉速、噪聲、響應速度、振動、扭矩、成本、使加工特點等方面加以介紹,并對比它們的特性。
2.1 皮帶主軸的特性
2.1.1 占用空間
主軸箱上需裝打刀缸、電機、安裝板、同步帶輪、同步帶等,占用空間較大,負載較重。
2.1.2 安裝難度
1皮帶連接為柔性連接,所以對兩軸之間的位置精度、配件的加工精度和裝配要求相對較低,但配件多安裝麻煩。例如,帶輪齒跳需校正至絲級,主軸與電機軸線平行度達絲級,電機安裝帶輪后需動平衡校正,主動輪與從動輪偏擺高點和安裝位置需一致,需通過打刀缸調節刀柄頂出量,皮帶和帶輪處于箱體內腔導致安裝和檢測困難等。
2.1.3 極限轉速
市面上常用的皮帶主軸極限轉速一般只有約 10 000 rpm。受皮帶的影響,很難在保證振動和噪聲合格的情況下提高轉速。
2.1.4 噪聲
有主軸和電機軸承滾動摩擦聲、主軸風切噪聲、電機電流聲、散熱風扇聲、同步帶風切噪聲與齒嚙合噪聲等,其中同步帶引起的噪聲較大。
2.1.5 響應速度
主軸運轉需經過從電機反饋至同步帶再傳到主軸,軸系重轉動慣量大,同步帶傳動摩擦力和變形較大,齒間隙大,所以響應速度較慢。
2.1.6 振動
電機和主軸的不平衡量和兩軸線的平行度,皮帶傳動時的往復變形及齒形嚙合都影響其振動,轉速越高影響越明顯,且越難降低。
2.1.7 扭矩
可通過帶輪實現輸出轉速或輸出扭矩的增減。帶輪傳動比為 1∶1 時,輸出扭矩比直聯主軸稍微降低(摩擦損耗)。
2.1.8 成本
成本=主軸及配件成本+維護成本+人工成本。主軸及配件成本相對較低。柔性連接能有效分離電機和主軸的各自振動。在極端工作狀態時,還會因超出額定負載以同步帶“爬齒”的形式進行緩沖,有效保護主軸及電機,從而避免電機和主軸同時損壞,降低維修成本。但因零件較多,影響因素也較多,裝配耗時較長導致人工成本也較高,如果出現異常,故障點的判斷也較為耗時。
2.1.9 加工特點
重切削能力強,但角度定位精度低,加工精度也低。
2.2 直聯主軸的特性
2.2.1 占用空間
主軸箱上需裝電機、聯軸器、電機安裝座等,占用空間和負載比皮帶主軸少。由于負載降低,滑臺移動的響應速度比皮帶主軸快。
2.2.2 安裝難度
因聯軸器的柔性緩沖性能很弱,所以對零部件之間的形位公差要求比皮帶主軸高很多,否則,不同的軸所產生的附加載荷將造成振動大甚至主軸和電機損壞。裝配時,需保證主軸、聯軸器與電機軸線同軸度達 u 級,主軸軸線與電機安裝面垂直度達 u 級(安裝面一般需鏟配),但零件少安裝會方便點。
2.2.3 極限轉速
市面上常用直聯主軸極限轉速一般達 24 000 rpm。轉速越高,對主軸、聯軸器、電機的同軸度要求越高,如果想在振動合格的情況下提高轉速,則需更高的動平衡精度、裝配精度和聯軸器零件精度,但難度很大。
2.2.4 噪聲
有主軸和電機軸承滾動摩擦聲、主軸風切噪聲、電機電流聲、散熱風扇聲、聯軸器風切噪聲等,噪聲比皮帶主軸要明顯降低。
2.2.5 響應速度
主軸運轉需經過從電機反饋至聯軸器再傳到主軸,軸系重轉動慣量大,但聯軸器柔性很弱,所以主軸運轉的響應速度比皮帶主軸快。
2.2.6 振動
只受電機和主軸的不平衡量,主軸、聯軸器與電機軸線同軸度影響,振動比皮帶主軸低。
2.2.7 扭矩
由電機扭矩確定,不可實現輸出轉速或輸出扭矩的增減。
2.2.8 成本
成本=主軸及配件成本+維護成本+人工成本。主軸及配件成本比皮帶主軸稍高一點;電機和主軸往往會同時損壞,從而提高了維修成本;零件少裝配所需的時間成本降低,若出現異常,故障點的判斷效率也會提高。
2.2.9 加工特點
通過聯軸器連接可以杜絕電機和主軸之間的游離間隙,同時聯軸器的柔性變形也很小,所以角度定位精度較高;沒有皮帶傳動產生的發熱,熱穩定性也相對較好;由于振動低轉速高,所以加工精度比皮帶主軸高。
2.3 電主軸的特性
2.3.1 占用空間
主軸箱上無需加裝其他零件,占用空間和負載比直聯主軸更少,尤其在多軸聯動機床上更有優勢。負載更低,滑臺移動響應速度也更快。
2.3.2 安裝難度
由于主軸箱上無需加裝其他零件,安裝最簡單。但滿足高轉速所需的零件精度要求很高,加上內置電機,對主軸供應商技術要求很高。
2.3.3 極限轉速
沒有中間傳動環節的外力作用和沖擊,更利于轉速的提升。市面上已出現 100 000 rpm 滾珠類電主軸,氣浮電主軸轉速甚至達 400 000 rpm。
2.3.4 噪聲
噪聲有電主軸軸承滾動摩擦聲、主軸風切噪聲、電機電流聲等。噪聲最低。
2.3.5 響應速度
傳動鏈的長度縮短為零,實現了“零傳動”。軸系輕轉動慣量小,可實現更高的加速度,同時準停的精度和速度都能大大提高。
2.3.6 振動
只受內部零件的加工精度、電機質量和軸系的不平衡量影響,且只有一根軸的軸系也便于實現更低的振動。同時,高速運轉能遠離機床系統的激振頻率,避免共振的發生。
2.3.7 扭矩
由于電機內置且安裝空間有限,電機比同規格皮帶或直聯主軸所配的電機小,所以能輸出的扭矩稍低,粗加工能力也會稍差。
2.3.8 成本
成本=主軸+維護成本+人工成本。價格比皮帶和直聯主軸都高很多,但可以省掉外置電機等配件的成本。當其安裝氣缸時,也可為客戶省掉外置液壓站或者增壓缸的成本。因為零件精密,所以維修價格也會提高。其安裝簡單,同時可內置編碼器、刀具檢測傳感器等零件,人工和時間成本都可以降低。
2.3.9 加工特點
由于軸承和電機小導致剛性和扭矩相對較小,所以重切削能力不如前兩者。但低振動的高速加工能使切削力降低,切削產生的熱量降低,熱變形小,殘余應力小,成品光潔度好,同時可以省去精加工工序。
3.總結
通過以上對比分析,皮帶主軸、直聯主軸和電主軸的特性差異歸納為表 1 中的內容。
表 1 特性對比
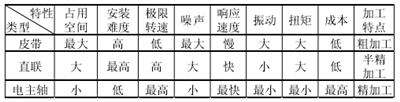
參照表 1 列出的特性,需求者可根據機臺精度、產品要求、成本等方面考慮選擇最適合的產品。值得一提的是,隨著數控技術的發展及市場需求,高速加工技術以其加工效率和精度高等優勢必將成為發展趨勢。
投稿箱:
如果您有機床行業、企業相關新聞稿件發表,或進行資訊合作,歡迎聯系本網編輯部, 郵箱:skjcsc@vip.sina.com
如果您有機床行業、企業相關新聞稿件發表,或進行資訊合作,歡迎聯系本網編輯部, 郵箱:skjcsc@vip.sina.com
更多相關信息