大口徑光學元件的精密磨拋與檢測裝備開發及應用
2020-3-4 來源: 廈門大學微納米加工與檢測聯合實驗室 作者:郭隱彪,彭云峰,王振忠,畢果等
摘要:大口徑光學元件超精密加工是一個復雜的系統性工程,涉及精密機床、數控、加工技術與工藝、精密檢測和補償控制等機電控各領域的專業知識,其發展與一個國家的高端制造技術及裝備發展能力息息相關,也是一個國家綜合國力的集中體現。主要介紹了廈門大學微納米加工與檢測聯合實驗室在大口徑光學元件超精密加工技術及裝備方面取得的研究進展,針對大口徑光學元件磨削和拋光兩個加工流程及其配套的精密檢測技術,詳細闡述了磨削裝備及單元技術、可控氣囊拋光機床及相關單元技術、精密檢測裝備及相關單元技術等的研究應用情況。這些技術研究從超精密加工的需求出發,借鑒國內外的研究經驗和成果,通過對裝備、工藝、檢測等各方面整合,形成了具有自主知識產權的集磨削、拋光和檢測裝備及工藝技術的大口徑光學元件超精密加工體系,這些技術與裝備確保了大口徑光學元件的高質量超精密加工。
關鍵詞:大口徑光學元件;超精密加工;磨削加工裝備;氣囊拋光;精密檢測;磨床
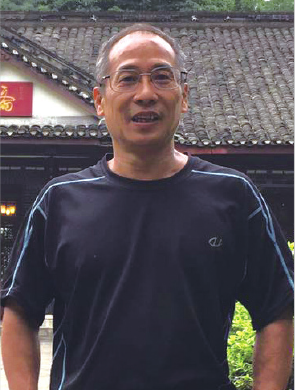
郭隱彪博士、教授、閩江學者特聘教授
主要研究方向為光學超精密加工、先進裝備開發與研制。
光學自由曲面如非球面等具備優越的光學性能,在同等功能要求條件下,可獲得成像質量更優、結構更簡單、成本更低和重量更輕的儀器,是航空航天和軍事國防領域不可或缺的關鍵基礎元器件,廣泛應用于大型天文望遠鏡、激光核聚變裝置、紅外熱成像、醫療影像設備等民用和國防尖端技術領域。在國家大光學工程任務以及光電子消費產品需求日益增長的牽引和推動下,其加工技術日益要求向高效、高精度、高質量方向發展。大口徑光學元件超精密加工技術不僅取決于機床、刀具和工藝方法,還取決于測量和控制技術,即含機、光、電、傳感技術和計算機技術等,它是多種學科新技術成果的綜合應用,但也對許多高新科技的發展與進步起著推動的作用。大口徑光學元件的加工是衡量一個國家先進制造技術水平和綜合國力的重要標志,西方國家在該領域一直對我國實行技術禁運。因此,開展光學元件超精密加工技術的研究有助于確保我國重要技術安全,我國“十二五”發展規劃中尤其做出了相關的指示,即《國家中長期科學和技術發展規劃綱要》中關于“關鍵基礎件制造和批量生產的關鍵技術為制造業的第一優先主題”的精神。
大口徑光學元件超精密加工,一般需要經過粗磨、精磨、拋光和鍍膜等工序,以提高工件面形精度,降低粗糙度和亞表面缺陷。這些工序中,大口徑光學元件的精磨與拋光加工尤其重要,在很大程度上決定了大口徑光學元件的加工質量水平,其中,精密磨削基本確定了大口徑光學元件的面形精度,同時為降低后續的拋光工作量,精密磨削過程中需盡量減少在光學元件表面形成過多的缺陷與破壞,而拋光加工是獲取超光滑低缺陷損傷光學表面的必要保證,因此,從保證大口徑光學元件加工質量的角度,精密磨削與高精度拋光手段是相輔相成,必不可少的,而高精度的機床裝備則是實現精密磨削與拋光的前提保證。受技術瓶頸限制,當前的硬件設計和開發很難開發出絕對高精度的機床裝備,且代價太高,導致精密磨削與拋光加工大口徑光學元件的同時不可避免地形成較大的加工誤差。
為獲得更高精度和質量的光學元件,必須進一步補償加工以提高光學元件的加工質量。而目前國內的光學測量與檢測裝備適應范圍有限,一般口徑較小且成本高昂。同時,作為獲取光學元件的加工尺寸與質量信息的必要手段,大口徑光學元件測量裝備與評價技術的開發也同樣重要。可以說,精密磨削與拋光裝備是獲得高精度大口徑光學元件的制造手段,而其精密檢測裝備與評價技術則是整個加工過程順利進行的保障,三者缺一不可,都構成了大口徑光學元件精密制造的必然環節。因此,加強大口徑光學原件精密制造的研究,必須三管齊下,唯有攻克并掌握三者的技術瓶頸,才可真正實現并確保大口徑光學元件的精密制造加工。
在激光核聚變和空天望遠鏡等大型光學工程項目的驅動下,西方發達國家,如美、日等國在大口徑光學元件的超精密制造技術已取得了重大進展。裝備方面,美國 Livermore 國家實驗室開發了 LODTM 單點金剛石切削機床,可加工 Φ1400mm 的光學元件,面形精度可達 PV ≤ 0.025μm,表面粗糙度 Ra≤ 5nm。英國 Cranfield精密工程研究所研制的 OAGM2500超精密磨床,可加工 Φ2000mm 的非球面光學元件,面形精度 PV ≤ 1μm。日本豐田工機研制的 AHN60-3D 復合機床,磨削加工的非軸對稱光學元件 PV 為 0.35μm,表面粗糙度 Ra為0.016μm。加工方法與工藝技術方面,為獲得高質量的光學元件表面形貌,日本理化所的 Ohmori 等提出了 ELID在線電解磨削方法,可實現光學元件的鏡面加工。
在光學表面完整性控制方面,基于小工具加工的數控拋光技術(CCOS)、應力盤拋光技術、氣囊拋光技術、磁流變拋光技術和等離子體法等技術均可有效去除亞表面損傷層,并能有針對性地改善工件表面質量和面形精度。這些先進的超精密加工技術,基本上解決了大口徑光學元件加工問題,但是國外發達國家對我國進行嚴格技術和設備禁運,造成我國大口徑光學元件超精密加工技術發展落后。
同時,國內也充分意識到了大口徑光學元件在民用和國防軍事等領域應用的重要性,明確了加強大口徑光學元件精密制造研究的必要性,并在相關項目的驅動下加緊了相關加工技術及裝備開發等各方面研究。裝備方面,中航精密機械研究所研制了 Nanosys-300 超精密復合加工機床,哈爾濱工業大學研制了大型曲面超精密復合加工機床,均可實現光學非球面的加工。國防科技大學研制的光學數控加工機床(AOCMT),最大加工能力為 650mm,對直徑 116mm 的碳化硅零件,銑磨成型的精度為 8.9μm,研拋后工件面形精度 PV 為(1/20~1/30)λ,表面粗糙度 2~5nm。廈門大學研制了大尺寸矩形光學平面精密磨床。加工工藝方面,廈門大學開發了光學非球面的計算機輔助制造工藝軟件。
光學完整性控制方面,國防科技大學開展了計算機數控拋光技術(CCOS)的研究,哈爾濱工業大學、國防科技大學和中物院等單位均開發了磁流變拋光機床,哈爾濱工業大學、浙江工業大學和廈門大學等研究了氣囊拋光技術并試制樣機。此外,廈門大學還開展了光學精密加工環境控制方面的研究,擬通過非硬件途徑彌補硬件缺陷以提高光學元件的加工精度。
目前,在先進軍事及空間光學系統、激光核聚變、大型天文望遠鏡工程等國家重大光學工程任務的需求牽引下,我國大口徑光學元件制造和檢測技術得到了快速發展。就其關鍵工藝路線的裝備保證方面而言,實現大口徑光學元件超精密加工的前提基礎是要具備高精度磨削與拋光加工設備,而大尺寸的高精度磨床與拋光裝備開發技術一直被公認為是要持續發展的技術、不可公開的技術和不可復制的技術,因此,高精度的磨削與拋光及其配套的檢測設備仍是制約我國超精密加工技術發展的瓶頸。而且,實現大口徑光學元件的超精密加工,除了高精度磨拋裝備之外,還需要一系列關鍵的配套單元技術,這些配套技術包括:超精密磨拋加工工藝與技術、機床精度整合技術、超精密環境監控技術、工具修整和動靜平衡技術、計算機輔助制造和檢測軟件 , 以及檢測路徑規劃和對應的補償加工策略。
基于大口徑光學元件的發展需求,廈門大學微納加工與檢測聯合實驗室課題組長時間以來深入地開展了大口徑光學元件的精密磨拋裝備、加工工藝技術及計算機輔助制造軟件、配套的精密檢測裝備與工藝等方面的研究,并取得了較突出的科研成果。本文以大口徑光學元件加工的關鍵磨拋工序為主要論述對象,介紹了廈門大學課題組在實現大口徑光學元件高精度、高效率與高度自動化精密加工的裝備開發及相關單元技術方面的研究情況。大口徑光學元件精密磨削機床及單元技術大口徑光學元件一般采用脆性材料,且具備較大口徑和復雜面形等特點,這為其精密加工帶來了較大的困難和挑戰。
目前,硬脆性材料大口徑光學元件的精密加工步驟和程序一般為先毛坯銑磨加工去除多余的材料,然后粗磨到一定面型精度,再通過精磨加工得到滿足其設計面型精度的半成品,最后再拋光去除表面 / 亞表面損傷層獲得超光滑的光學表面,整個加工過程較為復雜,需通過精密的工藝控制和檢測及補償加工實現。因此,為滿足大口徑光學元件的精密加工,具備高剛度和高精度及穩定性等性能特點的機床不可或缺,其中大口徑精密磨床則首當其沖。目前,在精密磨床制造方面,美國、日本、英國和德國等工業發達國家在國際上享有極高聲譽,代表產品如:英國 Granfield 大學精密工程研究所研制的 OAGM2500 六軸數控超精密磨床,可用于超精密車削、磨削和坐標測量;日本 Nagasei 公司擁有 SGC/SGE/N2C/NIC/RG 等系列的超精密磨床,可用于各種尺寸的非球面(自由曲面)、平面超精密鏡面加工;除此之外,Moore 公司的 Nanotech、Precitech 公司的 Freeform 系列、德國 Satisloh公司開發的 GII 系列、保寧機床公司的 ProfimatMT 系列和瑞士美蓋勒機床公司的 MFP 系列也達到了很高的加工精度。國內方面則稍顯落后,廈門大學微納米加工與檢測聯合實驗室以國外先進的制造技術為借鑒,從我國大口徑光學元件超精密加工需求出發,研制了多臺大口徑高精度臥軸矩臺平面磨床,本文將以開發的一臺 2MK7160 平面磨床及其單元技術為例進行說明。
1 、大口徑精密磨床的方案設計與樣機研制
為確保開發的大口徑平面磨床具備結構簡單、總體剛性好、磨削效率高等性能特點,研發首先通過綜合分析,將機床的整個開發工作分解為關鍵部件、關鍵技術、輔助配套與電氣及數控系統等部位進行模塊化研究。機床整機確定為立柱移動式數控臥軸矩臺平面磨床結構,外圍加鈑金全防護罩防護。改變傳統平面磨床導軌結構形式,床身底座采用 T 形布局和分體鑄件形式,提高工藝合理性。采用人工時效與自然時效相結合的辦法來保證基礎大件的長期穩定性。采用數字化設計和工程分析對設計方案進行充分論證,進行整機方案的結構靜力學和動力學設計和分析,保證樣機整機性能。為提高工藝系統剛性,采用液體動靜壓軸承支撐的砂輪主軸,實現高回轉精度和運動平穩性,各軸傳動系統由伺服電機帶動高精度滾珠絲杠,XY 方向采用液體靜壓導軌,并通過納米級分辨率的線性光柵構成全閉環控制回路,導軌采用拼塊結構,工藝性更加合理、剛性足,能實現高加工精度,從而保持高直線運動精度和高剛性。數控系統選用PANUC 31i 高端系統,基于 windows操作平臺,操作簡單、靈活,易掌握。
磨床的輔助系統包括冷卻系統、過濾裝置、潤滑系統,油水霧凈化裝置等。其中關鍵配套技術均為自主開發,砂輪修整采用綠碳杯形砂輪修整方法并開發專用修整器,工件檢測以機床運動帶動高精度接觸式 /非接觸式傳感器實現,加工控制與工藝技術融合進計算機輔助制造軟件開發中,采用工作流設計方法,實現人與機床活動的自動化處理,采用視圖 / 文檔的設計模式,實現數據處理和用戶界面的分離。基于工控機的軟件開發模塊包括工件檢測、砂輪修整、加工監控,動平衡等系統。砂輪修整采用兩軸精密杯形修整技術可保證金剛石砂輪形狀精度和平面、圓弧砂輪修整,實時現場動平衡檢測,減少主軸系統引入誤差,從而提高工件加工精度。加工監控消除機床振動影響,最大限度地消除加工表面 / 亞表面損傷。采用高壓冷卻水帶走磨削過程中的磨削熱量和切屑,提高加工表面性能,并采用油霧凈化器消除霧化的磨削液以凈化機床加工空間。同時獨立于高精度設備、技術人員及技術水平之外的外部環境的加工環境控制技術,保證高精度加工不受環境限制,最終實現了精密溫控系統、多層次消振技術、超精密凈化相關技術。設計后的磨床參數為:工作臺加工范圍 800mm×600mm,各軸分辨率0.1μm,主軸采用動靜壓支承技術,最高轉速 3000r/min,X 軸移動速度最大 20m/min,Y、Z 兩軸移動速度最大 5m/min,數控系統采用 FANUC 31i 系列,砂輪修整器采用 GC 杯形砂輪修整器。圖 1 為設計開發的2MK7160 大口徑臥軸矩臺平面磨床。
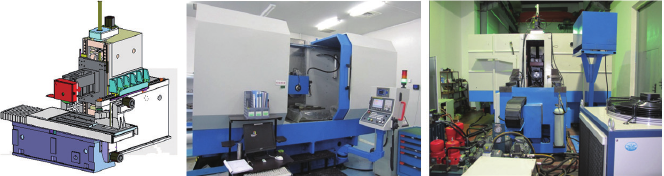
圖1 大口徑臥軸矩臺精密磨床2MK7160及其輔助配套系統
2 、液體靜壓支承技術
液體靜壓具備動靜摩擦系數相差級小、運動平滑、高剛度、可吸收振動、承受大負載和動態響應快等特點,為保證工藝系統的剛度和運動精度,磨床采用了閉式的液體靜壓支承技術,并開發了拼塊式靜壓導軌結構,該結構簡單且剛性好,極大地降低了常用閉式靜壓導軌的加工和裝配調試難度,且拆裝更為方便。開發的拼塊式導軌技術首先應用于第一臺開發的 MK7160 大口徑平面磨床的水平 X 軸上,并在成功后將其首次應用于 2MK7160 大口徑磨床的垂直Z 軸上,研究發現應用于垂直 Z 軸上的拼塊式導軌支承性能良好,優于傳統的接觸式導軌結構。圖 2 是開發的拼塊式液體靜壓導軌結構及應用實例。
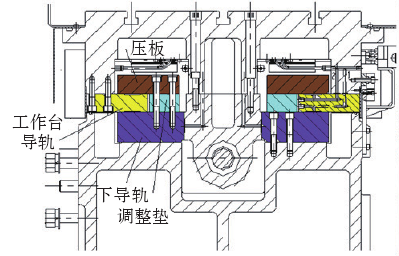
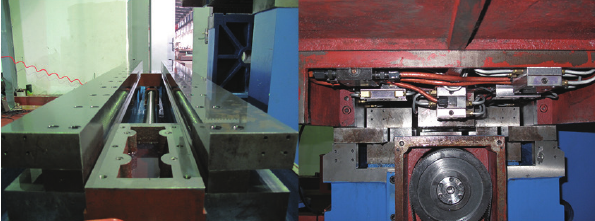
圖2 拼塊式液體靜壓導軌
3 、砂輪修整技術及裝置
光學元件一般為硬脆性材料,加工難度大,砂輪極易磨損而喪失加工能力。為保證金剛石砂輪磨粒尖銳性和面型精度,必須開發適應用于圓弧金剛石砂輪的修整技術,從而實現圓弧金剛石砂輪的修形和修銳以保證其加工能力。課題組提出了如圖 3 所示的圓弧金剛石砂輪的杯形圓弧包絡修整方法,通過杯形砂輪的包絡運動實現圓弧金剛石砂輪的修形和修銳。技術的實施上,機床提供修整運動所需的橫向往復運動和金剛石砂輪主軸的回轉運動,修整裝置提供杯形砂輪的擺動、修整進給和杯形砂輪回轉運動。修整過程中,杯形砂輪上脫落的磨粒將對金剛石砂輪磨粒與結合劑產生沖擊和研磨作用,從而完成對圓弧金剛石砂輪的修整。輔助工藝與系統方面,開發集砂輪面形精度測量、誤差建模、半徑補償、修整工藝等關鍵單元技術在內的杯形砂輪包絡修整計算機輔助加工軟件,并可實現圓弧金剛石砂輪修整裝置與機床的多軸聯動控制。圓弧金剛石砂輪的杯形砂輪包絡修正方法及裝置的開發,極大地保證了圓弧砂輪的加工性能并提高了其加工效率。該修整技術的最大特點是其修整的對象不局限于金屬結合劑圓弧金剛石砂輪,也適合于樹脂結合劑砂輪和陶瓷結合劑砂輪的修整。
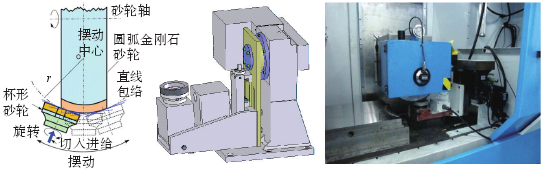
圖3 2軸杯形砂輪修整裝置
4 、計算機輔助制造(CAM)軟件
大口徑非球面屬于典型的面型復雜工件,加工難度較大,磨床各運動軸需協同控制運動才可完成。此外,機床機械系統特性均存在一定極限,在其性能不能進一步改善時,則需通過工藝的優化。為保證磨削的加工精度同時保證充分發揮數控磨床精度特性,需根據不同類型工件和具體磨床結構方式,選擇合理有效的加工工藝和加工規劃,優化磨削加工參數以提高面形精度和減小磨削亞表面損傷。其中加工補償控制方法是關鍵。為此,課題組提出了一系列的非球面面型插補方案和控制策略,并對其進行優化,建立了基于誤差檢測評價數據的建模補償技術;同時為延緩砂輪磨損,保證砂輪的加工能力,深入分析了圓弧砂輪的磨損機制,針對性地提出了砂輪均勻磨損與速度控制技術,有效提高砂輪壽命;針對非球面加工中的圓弧半徑誤差,提出分離檢測誤差成分并進行補償加工以提高加工精度;為提高砂輪修整效率,提出砂輪修整參數優化技術。基于上述的工藝優化方案,合理制定了加工工藝,配合計算機技術,特別是利用計算機輔助制造和測量,實現對加工過程信息自動處理及控制,提高加工過程自動化和加工效率;并研究數控伺服系統及微位移控制,進行不同工件加工方法分析、軌跡規劃及編程優化,確保加工中對機床的正確使用、數控加工特點的發揮和工件的加工精度。
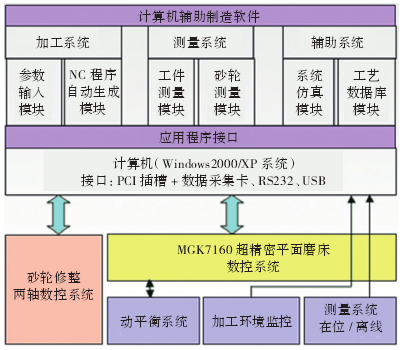
圖4 大口徑非球面精密磨削加工計算機輔助制造軟件
如圖 4 所示是課題組開發的用于實現超精密磨削的計算機輔助制造(CAM)系統軟件,其功能模塊包括磨削加工、面形測量、磨削補償、面形擬合和環境監控等,輔助制造系統軟件的應用可使整個磨削過程更加高效、便捷。CAM 軟件的開發可使大口徑光學非球面的精密磨削加工數控編程自動化,同時集成了磨削加工過程關鍵技術,包括工藝分析設計、參數輸入、加工軌跡數學處理、程序編制、工件測量、砂輪修整、加工監控、機床通信等功能模塊,各功能模塊的聯系和功能如圖5 所示。
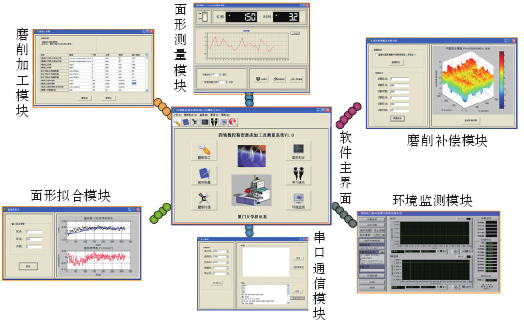
圖5 計算機輔助制造軟件功能模塊關系圖
光學元件可控氣囊拋光機床及單元技術
硬脆性材料在去除過程中,極易發生脆性斷裂破壞從而使加工表面較為粗糙。常規而言,大口徑光學元件在精密、超精密磨削成形加工后常需進行拋光等光整加工,目的是去除前道工序形成的表面變質層和損傷,并使工件表面超光滑化。但拋光加工易破壞工件的面型精度,因此常需采用后續的修正拋光加工以獲得高面型精度的大口徑光學元件。傳統的光學元件面形修正方法由于加工周期長、面形收斂慢等缺點很難適應現代光學系統的發展需求,故出現不少先進的現代拋光方法,例如小磨頭數控研拋、應力盤拋光、離子束拋光、磁流變拋光和可控氣囊拋光等確定性拋光技術。
在新出現的幾種確定性拋光技術中,小磨頭數控拋光是采用最廣泛的一種。該技術具備可拋光修正復雜自由曲面工件面型的優點。為降低拋光盤與工件表面間干涉對工件精度的影響,小磨頭數控拋光的工具尺寸一般較小,導致其在采用規律性的加工路徑時易在元件表面形成中高頻誤差。美國亞力桑那大學提出的應力盤拋光技術能克服這個問題,但其修形能力較弱,控制復雜,且小磨頭和應力盤均屬于接觸式加工方法,加工中盤面和元件的接觸易導致元件發生彈性形變使元件面形難以加工到較高精度。離子束拋光技術雖可實現局部修正拋光加工,但是其拋光效率極低,且對加工環境要求極高,成本高昂。相比之下,磁流變拋光和可控氣囊拋光技術屬于柔性拋光技術,能夠實現很高的加工精度,但磁流變拋光成本很高,導致其很難應用于凹曲面以及大口徑高陡度工件的加工。基于上述分析,課題組有針對性地開發了可控氣囊拋光技術及其機床。
1 、可控柔性氣囊拋光機床的開發
柔性氣囊拋光技術首先由英國倫敦光學實驗室的 Walker 教授提出,后由英國 ZEEKO 公司開發成系列的產品。課題組在消化吸收其產品的基礎上,開發了國內首臺可控柔性氣囊拋光機床及單元技術。如圖 6 所示,氣囊拋光機床整體采用龍門結構,分別由工作臺底座、立柱橫梁、中溜板與主軸箱結構組成。兩氣囊拋光機床的核心部件,在結構設計中不僅要保證整個機構的運動精度還要為滿足附加功能而預留足夠的位置空間。氣囊拋光采用進動式的加工方式,即拋光加工過程中氣囊主軸始終與工件局部法線成固定的進動角。為了方便控制氣囊自轉軸的空間位姿,兩軸氣囊拋光工具由兩個旋轉軸 Z1和Z3來控制氣囊主軸 Z2在空間位姿的變化,同時兩軸氣囊拋光工具的 Z1、Z3和 Z2軸相交于氣囊頭的球心。通過對運動空間的理論分析計算當 Z1軸和 Z3軸在空間成 45°時,即整個機構的空間角度為 45°,整個氣囊拋光工具的空間運動范圍與剛度最合適。
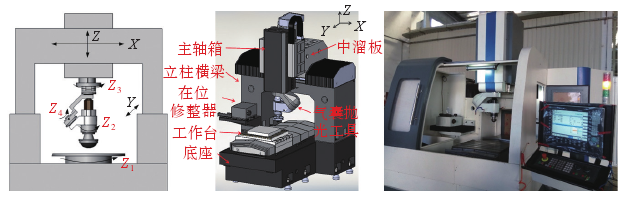
圖6 可控氣囊拋光樣機模型和實物圖
2 、柔性可控氣囊設計及其修整技術
為避免剛性拋光頭損傷自由曲面面型,氣囊拋光機床采用具有一定充氣壓力的球冠形氣囊作為拋光工具,這樣不僅可以保證拋光頭與被拋光工件表面吻合性好,而且可以通過調節氣囊內部壓力控制拋光效率和被拋光工件的表面質量。為此,柔性氣囊拋光方法是一種極具發展潛力的拋光方法,尤其適用于非球面和自由曲面的拋光。柔性氣囊拋光加工采用一種獨特的進動運動方式,即拋光過程中,氣囊自轉軸始終與工件局部法線呈固定角度 ( 稱進動角 ) 進行拋光,通過特定的加工軌跡與路徑控制,可以在接觸區形成雜亂的加工痕跡,生成接近高斯分布的去除函數,這種加工方式有助于降低拋光表面中頻誤差的形成,正是基于這個特點,氣囊拋光加工技術具備廣泛應用于大口徑自由曲面元件的去中頻誤差修正加工。
為確保氣囊加工可適用于不同的加工對象,課題組研究了不同結構形式的氣囊拋光頭,以獲得不同變形模式和剛度的拋光頭,包括純橡膠氣囊頭、內置鋼網橡膠氣囊頭和內置薄鋼板氣囊頭等多種形式,并有針對性地研究了各種氣囊頭的變形特性和去除函數。圖 7 所示是其中開發的內置鋼網的柔性氣囊拋光頭。
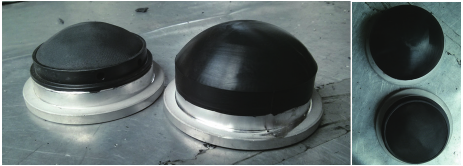
圖7 設計的柔性氣囊及其結構
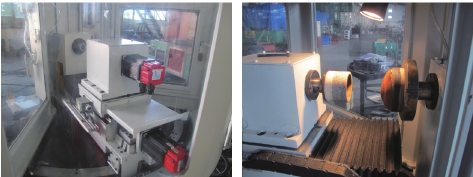
圖8 離線氣囊修整裝置
為了進一步提高加工效率,減少氣囊拋光頭修整耗時,課題組將氣囊頭修整工序分離,設計并增加了離線氣囊修整裝置,開發了如圖 8 所示的離線氣囊修整裝置,該裝置由底座、擺動電機、擺動底座、擺動導軌、進給電機、導軌、砂輪底座、砂輪主軸電機、修整砂輪、拋光頭電機、防護裝置等部分組成。擺動電機固定在底座的底部,通過減速機與擺動底座相連,導軌固定在擺動底座上,進給電機與進給主軸通過導軌帶動砂輪底座完成進給運動,砂輪主軸電機通過聯軸器帶動修整砂輪旋轉,完成修整砂輪的運動。拋光頭部分底座通過螺釘固定在底座的一端,氣囊拋光頭由皮帶輪與拋光頭電機帶動旋轉。
在氣囊頭離線修整加工中,氣囊頭的修整由橡膠氣囊頭的旋轉、砂輪主軸的旋轉、進給軸進給運動和擺動軸的擺動運動共同完成。同時,在防護罩的頂部安裝有氣囊頭動平衡裝置,檢測氣囊頭在旋轉過程中的振動與轉速,方便對氣囊頭的平衡調整,提高修整精度。
3 、氣囊拋光仿真與運動控制軟件
為確保氣囊拋光加工可實現預期功能,課題組充分研究了可控氣囊拋光的加工機理,將試驗與仿真相結合,確定不同工藝條件對拋光接觸區的影響,以及不同條件下氣囊拋光的靜態和動態去除函數,并研究了基于去除函數的拋光駐留時間算法。在研究基于運動學理論的氣囊拋光過程中進動控制方法的基礎上,得出最高效的進動控制算法。研究特別對連續進動拋光模式下的氣囊加工進行了深入的研究,尤其在壓力控制和位姿控制的基礎上分別研究了如圖9 所示最優效率算法、剛度可控算法和四軸聯動控制算法等,并在此基礎上編制了柔性氣囊可控拋光的仿真與運動控制軟件,該軟件具備手動和自動控制兩種模式,如圖 10 所示為開發的軟件界面。該仿真與運動控制軟件極大地方便了氣囊拋光的運動規劃和運動控制,有效地促進了氣囊拋光加工的高度自動化。
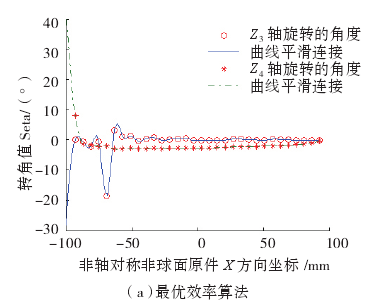
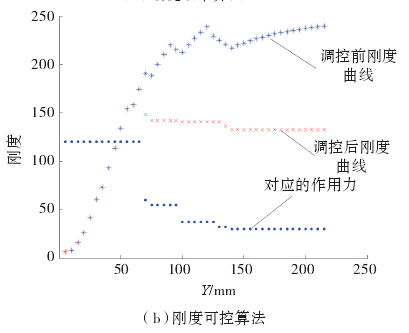
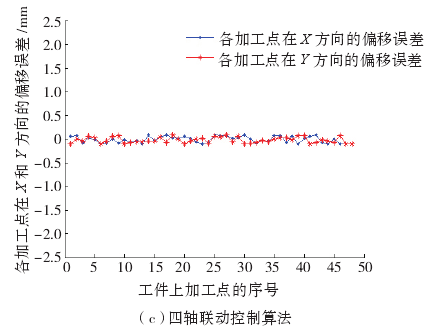
圖9 開發的幾種氣囊拋光控制算法
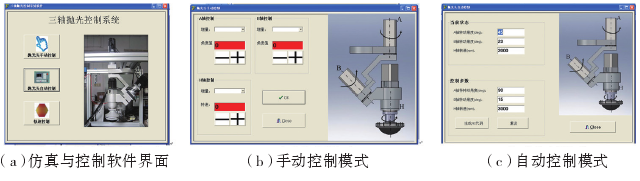
圖10 氣囊拋光的仿真與運動控制軟件界面
大口徑光學元件精密檢測裝備及單元技術
大口徑光學元件的加工一般經歷銑磨、磨削、拋光 3 個階段,為保證每道工序的加工余量和精度,每個加工階段都需要匹配對應的精度測量檢測技術。大口徑光學元件的加工過程中,磨削加工階段主要是為了獲得較為接近設計要求的形狀精度,該階段獲得的面型精度將在很大程度上決定后續面型收斂加工的工作量,因此其面型精度的檢測至關重要。一般而言,大口徑光學非球面磨削加工階段面型誤差檢測裝置的精度要求介于數十微米到亞微米之間。基于此,課題組有針對性地開發了大口徑光學元件面型誤差的檢測技術。圖 11 所示是課題組開發的在位檢測系統,該檢測系統將激光位移傳感器放置于磨削主軸上,利用磨床各軸的運動完成大口徑非球面元件的面型檢測,可實現大口徑光學元件的全口徑測量。該種檢測方式屬于在位式的,其特點是可以避免工件離線測量引入裝夾、定位等誤差,實現對工件加工表面精度進行測量,并可為補償加工提供加工誤差數據。圖 12 所示為利用在位檢測系統檢測大口徑非球面光學元件初始加工和補償加工后的面形精度圖,經過 3 次補償加工后面形精度 PV 值由 7.77μm 下降到4.67μm。
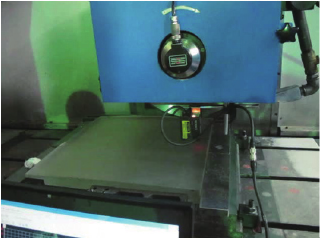
圖11 在位檢測系統
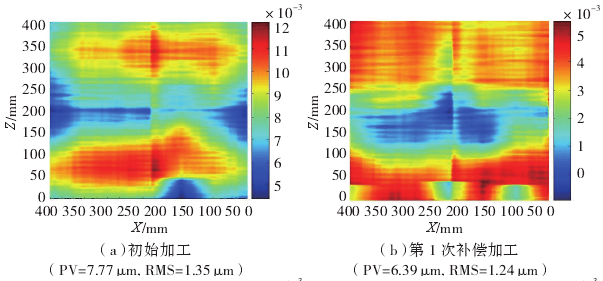
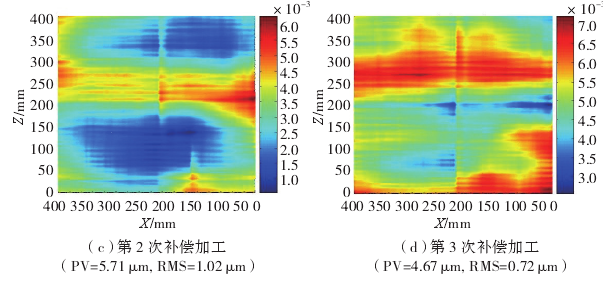
圖12 初始加工的補償加工面形精度
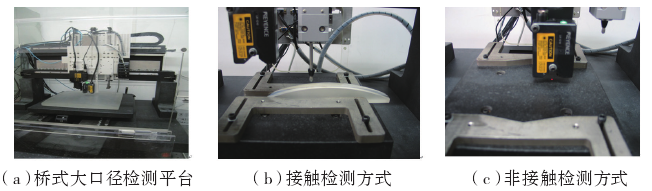
圖13 大口徑光學元件檢測裝置
此外,課題組還分別開發了中大口徑(200mm×200mm)和大口(400mm×400mm)光學元件的三維輪廓測量離線精密檢測平臺。圖 13為其中的大口徑離線精密檢測平臺,該平臺采用固定橋式結構,XYZ 軸行程分別為 400mm×400mm×150mm,各軸定位精度為 ±1μm,整體設計測量精度目標為 ±3μm。檢測平臺采用一種上下位機的多 CPU 結構,上位機實現系統管理、數據處理及人機界面等功能。下位機由運動控制和數據采集兩個模塊組成,實現實時的運動控制和數據采樣、分析及處理功能。平臺采用接觸式和非接觸式雙探測系統,可針對不同工件需求實現工件面形數據的實時采集,采集后的面形原始數據通過相關數據擬合算法和誤差分析,可擬合出實際加工后的工件面形,將擬合后的工件面形與理想的非球面面形比較,從而求出非球面面形誤差和各種像差等參數,為后續加工提供加工補償數據。
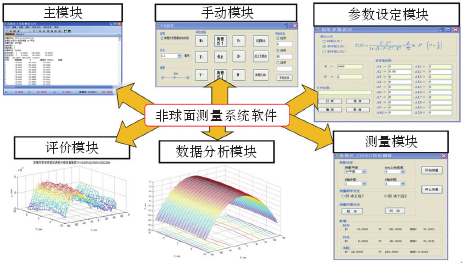
圖14 非球面檢測軟件及功能模塊
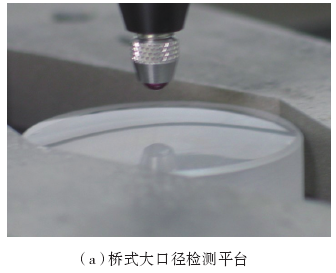
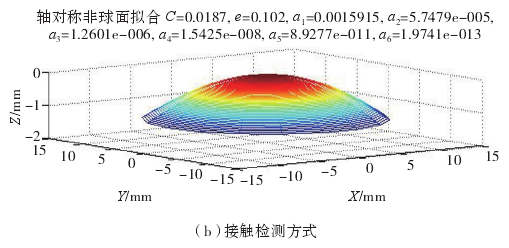

圖15 非球面光學元件的檢測結果
為使檢測平臺在大口徑非球面元件檢測中更為便利,課題組還開發了適應于大口徑非球面元件檢測的非球面測量系統軟件,該軟件包含如圖 14 所示的參數設定模塊、測量模塊、數據分析模塊和評價模塊,具備非球面頂點查找、定位誤差補償、直線度與垂直度和平面度誤差補償、測桿變形誤差補償等功能,該軟件設有手動和自動兩種工作模式。圖 15 是利用開發的大口徑光學檢測平臺和軟件測量得到的非球面光學元件面型及擬合偏差。該檢測裝置和配套軟件的開發成功地為大口徑光學元件的精密加工提供了強有力的精度測量和補償加工保證。
結論
大口徑光學元件的精密制造加工屬于一個復雜的綜合性系統工程,其精密加工涉及難加工材料的去除機理與控制、精密超精密機床開發、數控技術、精密檢測、加工工具及修整、材料、加工狀態及環境控制、誤差評價及補償和加工技術與工藝等方面,其中的每一項均是一個重要的研究方向,對其深入系統的研究任重而道遠。在相關大光學工程項目的資助下,廈門大學微納米加工與檢測聯合實驗室在大口徑光學原件的精密制造與檢測裝備方面進行了較多的探索,取得了一些實用的科研成果,主要體現在:
(1)開發了“T 型”布局的大口徑四軸精密磨床,該機床采用液體靜壓支承導軌、動靜壓主軸及動平衡技術,配置針對圓弧金剛石砂輪修整的杯形砂輪修整器,針對大口徑非球面光學元件的精密加工需求,開發了與該磨床配合使用并包含多個關鍵單元功能模塊的計算機輔助制造(CAM)系統。
(2)開發了大口徑柔性氣囊拋光機床,拋光機床采用 AB 擺五軸構,“T”型龍門布局,拋光頭采用柔性氣囊結構,具備壓力和姿態控制兩種加工模式。研究設計了多種拋光加工路徑與駐留時間算法,并開發了精密拋光機床的計算機輔助拋光(CAM)系統。
(3)研制了中大口徑光學非球面檢測平臺,測量平臺具備接觸式與非接觸式兩種測量工具與手段,并開發了大口徑非球面的測量與評價軟件,該軟件具備自動測量、數據分析、評價和補償等功能,可實現較高精度大口徑非球面的精密測量與評價。綜合分析當前的技術發展現狀可見,雖然我國已經能加工出較高精度的大口徑光學元件,但相比國外先進水平仍然存在較大的提升空間,未來需要相關部門與研究機構及高校創新性的探索研究相關新加工技術與方法、新的工藝、新的檢測技術,以期在此基礎上實現大口徑光學元件的高精度與高質量加工,確保我國相關大工程項目和國防軍事等領域的建設與實施。在相關高端裝備及數控領域方面的攻關工作,也將幫助我國最終突破國外技術封鎖,全面提升我國的精密制造技術及其裝備水平,確保我國的技術安全。
投稿箱:
如果您有機床行業、企業相關新聞稿件發表,或進行資訊合作,歡迎聯系本網編輯部, 郵箱:skjcsc@vip.sina.com
如果您有機床行業、企業相關新聞稿件發表,或進行資訊合作,歡迎聯系本網編輯部, 郵箱:skjcsc@vip.sina.com
更多相關信息