M1040 型無心磨床故障分析及應對措施
2024-4-30 來源: 西藏技師學院 作者:柳 楊
摘要:在鉗工維修裝配專業的學生實習時,需要使用 M1040 型無心磨床,因其生產性質決定機床必須高效率、高精度地工作,所以如何降低無心磨床的故障率和提高其維修精度成了機修工作的重點和難點,該文針對 M1040 型無心磨床故障和磨削質量缺陷分析及其對策作粗淺闡述。
關鍵詞:機床修理;無心磨床;故障分析;對策;修復
M1040 型無心磨床用于對幾何精度和表面質量要求高的圓柱體零件和環形零件的外表面進行通磨,以及對錐度不大的圓錐面和成形表面的半自動或手動切入磨削。廣泛應用于汽車、拖拉機、航空航天、儀表、軸承、工具及紡機等行業的大批量生產企業。江淮動力集團公司是生產柴油機、汽油機的大型企業,M1040 型無心磨床是生產氣門的主要設備。M1040 型無心磨床擔負著氣門桿部的粗磨、半精磨和精磨的加工任務,因其生產性質決定了無心磨床必須高效率、高精度地工作,所以須降低無心磨床的故障率和提高其維修精度。筆者在這些年帶學生到江淮動力集團進行機修實習期間,對 M1040 型無心磨床的多發性故障接觸較多,體會較深。在此對 M1040 型無心磨床在生產中的常見故障和磨削質量缺陷及其對策作如下粗淺闡述。M1040 型無心磨床在生產中的常見故障和磨削質量缺陷如下:①常見故障有砂輪主軸不轉、導輪不轉和砂輪主軸抱死等;②機床部件對產品產生磨削質量缺陷有工件磨削時表面出現螺旋形花紋、工件表面有不規則的擦傷、工件表面燒傷、工件表面產生多角形狀及工件直線度有誤差等。
1、機床故障分析與修復
1.1 故障分析與診斷
按照 M1040 型無心磨床在生產中使用情況和出現的故障,運用故障分析樹的方法,如圖 1 所示,對造成機床系統故障的各種因素進行分析,從而能很快找出機床系統發生故障的主要原因并能立即提出解決措施。
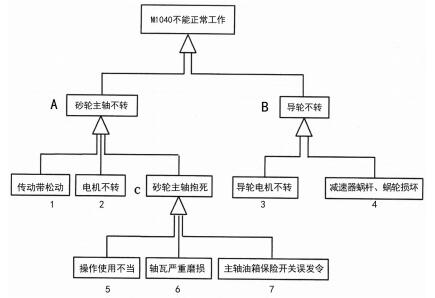
圖 1 M1040 無心磨床故障分析樹
如圖 1 所示,造成 M1040 型無心磨床不能正常工作的中間故障有 A(砂輪主軸不轉)或 B(導輪不轉)。對 A(砂輪主軸不轉) 有影響的原因有 1(傳動帶松動)、2(電機不轉)及中間事故 C(砂輪主軸抱死)。影響B(導輪不轉)的原因有 3(導輪電機不轉)、4(減速器蝸桿,蝸輪損壞)。在日常維修中問題 1(傳動帶松動)、2(電機不轉)、3(導輪電機不轉)、4(減速器蝸桿,蝸輪損壞)可以通過調整、更換損壞件排除故障。中間故障 C(砂輪主軸抱死)產生的主要原因是由 5(操作使用不當)、6(軸瓦嚴重磨損)、7(主軸油箱保險開關誤發令)等因素的影響。原因 5(操作使用不當)可以通過對操作工人進行培訓解決。通過對以上故障分析樹的分析,可以看出 M1040 型無心磨床不能正常工作的主要原因是中間件 C(砂輪主軸抱死),以及基本原因 6(軸瓦嚴重磨損)、7(主軸油箱保險開關誤發令)發生故障。因此要改變 M1040 型無心磨床現有的狀況,應解決主軸油箱保險開關誤發令和主軸軸瓦磨損修復這兩個主要問題。
1.2 解決主要問題的對策
通過 M1040 型無心磨床故障分析樹的分析,已經知道影響無心磨床正常使用的 2 個主要問題為主軸油箱誤發令和主軸軸瓦磨損,其中主軸軸瓦精度對產品的形位公差的保證有重大影響,因而是重中之重,現對這 2 個問題的具體原因和解決方案作如下介紹。
1.2.1 主軸油箱保護開關誤發令問題的解決
如圖 2 所示,砂輪主軸保護切換機構被安裝在砂輪主軸潤滑槽的上部,其工作原理是從砂輪主軸上的回油將浮筒提起,并通過浮筒帶動操縱桿,使砂輪主軸的保護開關開啟,從而使砂輪主軸中的潤滑油液體保持在一定壓力下。因為原機床的浮體材質為尼龍或塑膠,浮體在使用一段時間后會發生老化、變形,浮體在工作時會出現漂浮現象。這樣,砂輪的主軸不能充分注滿潤滑油,而砂輪的主軸保護開關也是開啟的,因為這樣的情況常常會出現,因此,出現了砂輪主軸的抱死失效。為此,在修理時,對浮筒的材質進行了改進,采用了一層厚(約 0.8 mm)的銅皮焊接,以消除浮筒的老化和變形,解決了砂輪主軸保護開關的誤啟動問題。
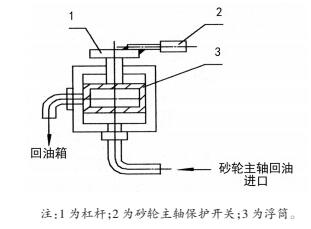
圖 2 砂輪主軸保護開關裝置
1.2.2 主軸軸瓦的修復
M1040 型無心磨床主軸軸承屬多瓦式滑動軸承,由于自然磨損或潤滑不良,而引起的“抱瓦”現象,往往會使設備無法正常工作。主軸在軸瓦中的運動精度直接影響工件的精度,因而軸瓦修復工藝很重要。在實際操作中對多瓦式滑動軸承修復的工藝方案介紹如下。
如圖 3 所示,M1040 型無心磨床主軸軸瓦為 5 瓦結構,其長度直徑之比一般為 1.2~1.5。其中 l 號瓦和 2號瓦為底瓦,由磨架軸承孔支承軸瓦的外表面母線,不可調節。3、4、5 號瓦為可調節瓦,可作軸承間隙調整。軸瓦的橫斷面呈內外表面不等厚形狀,支承中心為最厚尺寸,向兩側呈漸薄形減小。此軸承結構的瓦軸加工工藝較復雜,在調整間隙時,要求調整的技術水平較高,故在新產品中已不再采用此種形式。
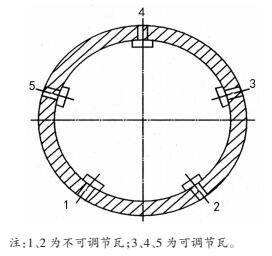
圖 3 M1040 型無心磨床主軸軸瓦結構圖
在修復過程中,需要對瓦軸的 2 個軸套進行反復刮磨。2 塊底瓦的高度要相等,底瓦兩端的高度要相等,誤差約為 0.01 mm。修復時,首先要對主軸的 2 個軸頸進行認真檢查,如果在檢查中發現裂紋等情況,就應該考慮再檢查一次或換一次;如果沒有裂縫,就要認真地測量 2 個軸頸的大小;進行精密研磨,將 2 個軸承的軸頸磨到相同的大小。
在模具夾具(圖 4)中,固定墊圈 3 和 5 上銑出了很大斜度,因為板瓦通常都是在外圓端面上有很大倒角,所以可以通過這種大的斜角和墊圈的內錐面,使 4塊板瓦牢固地固定在芯子上,確保了板料的精確定位。
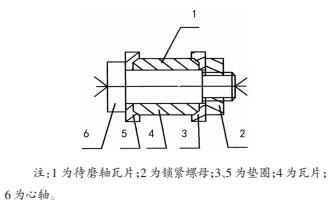
圖 4 模具夾具結構
其他 3 個軸承套是可以調整的,沒有特別要求,可以不進行研磨,但是如果有很大變形,就需要進行研磨。在修復好軸瓦后,把瓦依次放進襯套或特殊模具中,調整前后軸承螺絲,使其松緊均勻;調整好后,沿著主軸的旋轉方向旋轉 5~8 次進行磨點,然后卸下,進行精刮,如此反復;直到磚面上的斑點分布均勻,達到精度要求(20 點/25 mm×25 mm 或更大)。最后在瓦片上涂抹藍油粉,反復進行上述工序,可增加軸瓦的數量和范圍;通過對每一部件的認真清潔,對其進行正確組裝,并用百分表對軸承的直徑間隙進行 0.01~0.02 mm 的測量,這樣就完成了軸承的維修。
瓦片經磨削和刮研后,厚度減小,在裝配過程中,其余相關件要做校正處理或修復。2 機床相關部件對產品產生磨削質量缺陷的分析和對策由于影響無心磨削加工的因素很多,應用 M1040型無心磨床磨削加工氣門桿部外圓時,機床部件對產品產生磨削缺陷及其消除的方法作如下總結。
(1)工件磨削時表面出現螺旋形花紋劃傷,產生此現象可能的原因很多,歸納起來大概有如下幾點:①導輪上嵌有硬粒或砂輪的出口端“外凸”,消除的方法是修正導輪,直至消除。②托板已經碎裂產生銳邊或是表面粗糙、有拉毛,消除的方法是修磨或更換新的托板。③砂輪結合劑硬度不均,此時必須更換新砂輪。④輸出和進給工件的速率不正確。此時適當調整送料滾輪的轉速,以保證工件進、出料轉速與磨削區的一致性。⑤砂輪與導向輪之間的相對軸位置發生了偏移。須根據需要再對齊。
(2)工件表面有不規則的劃痕,這種劃痕是由切削液造成的。①切割液體不清潔。②切削液的潤滑性較差。如果是前者,可以更換新的切削液或者添加一個過濾器;如果是后者,應更換具有良好潤滑的切削液。
(3)工件表面灼傷,其主要原因為在切削過程中,由于溫度太高,不能及時將研磨熱量排出,導致工件表面灼傷。有可能是由于切割深度太大、進刀太快、磨削太硬、磨削太慢及冷卻不足。通過減少切割深度、降低切割速度和選擇柔軟砂輪進行磨削加工;通過對冷卻設備的結構進行改造,可以將冷卻水送至磨削區,并在冷卻系統中加入冷卻設備,提高冷卻速度。
(4)工件表面形成三角形、五邊形及七邊形等多個角形,這是由于下列因素造成的。①由于工件的中心高度不夠高,使得砂輪的研磨力向托板、導輪的分力增大,造成工件與托板之間的摩擦,從而阻礙了工件的旋轉,造成了研磨時工作表面形成多個角形;這時應該增加工件的中心高度,但是要注意,工件的中心高度太高,會造成工件在研磨過程中的跳動,同時也會造成加工誤差;嚴重時,研磨不能進行。所以在選用中心高度時要特別小心。②導向輪的傾斜角度太大,在加工過程中會造成工件的工作性能下降。解決這一問題的辦法是降低導向輪的傾角,這時要想讓進給速度不變,就必須提高導向輪的轉速。③坯料的圓度偏差過大,通常不允許有 50%以上的偏差。解決方法是在進行無心磨削之前,添加一次加工,提高毛坯的圓度,或在不注意的情況下,多做幾次。④導向輪的工作狀態不佳,導致工件的工作狀態不佳。這時,為了保證導向輪的正常工作,必須對導向輪進行修整,并對導向輪軸承進行檢查,使其與軸承保持良好的接觸。
(5)工件直線度有誤差,產生工件直線度誤差的原因是砂輪修正器修正砂輪不平整,解決措施為:①檢查修正器是否有松動,如有松動后及時調整。②檢查仿形模板是否有磨損,如有磨損及時更換。③檢查主軸是否有松動,如有松動必須及時調整。
3、結束語
以上是筆者根據自己的機修實踐和與同行的經驗交流,總結出的 M1040 型無心磨床在日常生產中常見故障和解決方法。經驗證,以上措施可以在生產及實習過程中,能夠迅速解決 M1040 型無心磨床的故障,提高其加工精度,降低機床故障率,保證機床正常穩定工作,保質保量地投入生產,為企業創造出更大的經濟效益。同時也在鉗工生產實習教學中,提供了一個完整、可行的機修教學案例,在產教結合上邁出一小步。
投稿箱:
如果您有機床行業、企業相關新聞稿件發表,或進行資訊合作,歡迎聯系本網編輯部, 郵箱:skjcsc@vip.sina.com
如果您有機床行業、企業相關新聞稿件發表,或進行資訊合作,歡迎聯系本網編輯部, 郵箱:skjcsc@vip.sina.com