金屬材料激光增材制造技術及在航空發動機上的應用
2016-2-3 來源:中航商用航空發動機有限責任公司 作者:劉業勝 韓品連 胡壽豐 柴象海 曹源
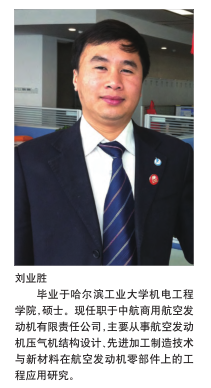
隨著增材制造技術的不斷發展及技術的不斷突破,研制零件的力學性能、疲勞性能等不斷提高,其在工業領域,特別是航空航天領域必將具有非常廣闊的應用前景。
金屬材料增材制造技術及其特點
金屬材料增材制造技術,又稱3D 打印技術、激光快速成型技術,主要以金屬粉末(尺寸小于 1mm 的金屬顆粒群)、顆粒或金屬絲材為原料,通過 CAD 模型預分層處理,采用高功率激光束熔化堆積生長(“增材制造” ),直接從 CAD 模型一步完成高性能構件的“近終成形”。金屬材料增材制造技術,可分為激光直接化制造技術(Laser Melting Deposition, LMD)和選擇性激光熔化技術(Select Laser Melting,SLM)。與傳統的金屬零件加工技術相比,金屬材料增材制造技術有著無法比擬的優點,具體如下:
(1)零件室溫綜合力學性能優異;
(2)復雜零件制造工藝流程較傳統工藝大大縮短;
(3) 無模具快速自由成型,制造周期短,小批量零件生產成本低;
(4) 零件近凈成型,機加余量小,材料利用率高;
(5)可實現多種材料任意復合制造;
(6) 激光束能量密度高,可實現傳統難加工材料如 TC4、Inconel7117-4PH、38CrMnSiA 等的成型。金屬材料增材制造技術是一門融合了計算機軟件、材料、機械、控制、網絡信息等多學科知識的系統性、綜合性技術。采用離散化手段逐點或逐層 “堆積”成型原理,依據產品三維 CAD 模型,快速“打印” 出產品零件,徹底改變了傳統金屬零件,特別是高性能難加工、構型復雜等金屬零件的加工模式,在航空航天等裝備預研與生產中具有廣闊的應用前景,成為當前材料制備科學和先進制造技術學科領域國際前沿研究和競爭熱點之一。
金屬材料增材制造基本原理
1 LMD 技術基本原理
LMD 技術作為增材制造技術的一種,是通過快速成型(Rapid Prototyping,RP) 技術和激光熔覆技術有機結合,以金屬粉末為加工原料,采用高能密度激光束將噴灑在金屬基板上的粉末逐層熔覆堆積,從而形成金屬零件的制造技術。整個LMD 系統包括激光器、激光制冷機組、激光光路系統、激光加工機床、激光熔化沉積腔、送粉系統及工藝監控系統等。
LMD 快速成型技術的基本原理為:首先,利用切片技術將連續的三維 CAD 數模離散成具有一定層厚及順序的分層切片;第二,提取每一層切片所產生的輪廓并根據切片輪廓設計合理的激光器掃描路徑、激光掃描速度、激光強度等,并轉換成相應的計算機數字控制程序;第三,將激光溶化沉積腔抽真空,并充入一定壓力的惰性保護氣體,防止粉末熔化時被氧化;第四,計算機控制送粉系統向工作臺上的基板噴粉,同時激光器在計算機指令控制下,按照預先設置的掃描程序進行掃描,溶化噴灑出來的粉末,熔覆生成與這一層形狀、尺寸一致的熔覆層;最后,激光陣鏡、同軸送粉噴嘴等整體上移(或工作臺下移)一個切片厚度并重復上述過程,逐層熔覆堆積直到形成 CAD 模型所設計的形狀,加工出所需的金屬零件。
2 SLM 技術基本原理
SLM 技術作為增材制造技術的另外一種實施方式,由粉床選區激光燒結技術 (SLS)發展而來,以金屬粉末為加工原料,采用高能密度激光束將鋪灑在金屬基板上的粉末逐層熔覆堆積,從而形成金屬零件的制造技術。整個 SLM 設備包括激光器、激光陣鏡、粉末碾輪、粉末儲存室、零件成型室等。
SLM 快速成型技術的基本原理為:首先,利用切片技術將連續的三維 CAD 數模離散成具有一定層厚及順序的分層切片;第二,提取每一層切片所產生的輪廓并根據切片輪廓設計合理的激光器掃描路徑、激光掃描速度、激光強度等,并轉換成相應的計算機數字控制程序;第三,將激光溶化沉積腔抽真空,并充入一定壓力的惰性保護氣體,防止粉末熔化時被氧化;第四,計算機控制可升降系統上升,粉末碾輪將粉末從粉末儲存室推送到零件成型室工作臺上的基板,同時激光器在計算機指令控制下,按照預先設置的掃描程序進行掃描,溶化鋪灑在基板上的粉末,熔覆生成與這一層形狀、尺寸一致的熔覆層;最后,粉末儲存室上移而零件成型室下移一個切片厚度并重復上述過程,逐層熔覆堆積直到形成 CAD模型所設計的零件。
金屬材料增材制造發展現狀
1 LMD 技術發展現狀
1.1 LMD 技術國外發展現狀
增材制造技術發展經歷了 3 個階段,1892~1988 年的技術孕育期、1988 年開始的快速原型技術及 20世紀 90 年代初期以來的直接增材制造。1979 年,UTRC 提出激光立體成形技術概念并制作出航空發動機渦輪盤模擬件1994 年起,Rolls-Royce探索航空發動機零件激光成形,另外英國利物浦大學和美國密西根大學、加拿大國家研究委員會集成制造技術研究所、瑞士洛桑理工學院、美國Sandia 國家實驗室、美國 Los-Alamos國家實驗室、美國 Aeromet 公司、美國賓州大學、英國伯明翰大學等都相繼開展研究。由于LMD 同軸送粉效率高,材料致密性好,因此,越來越多的用于大型零件的增材制造及零件修復工作。
國外有關大型零件增材制造技術的研究主要集中在美國。
1995~2005 年間,在美國國防部先進研究計劃署及海軍研究辦公室等部門的巨額資助下,美國約翰哈普金斯大學、賓夕法尼亞州立大學及 MTS公司等對飛機鈦合金結構件激光快速成形技術進行了大量研究并取得重大進展,在此基礎上,1998 年由MTS 公司獨資成立了專門從事飛機鈦合金結構件激光快速成形制造技術研發和工程化應用的 AeroMet公司,與波音、洛克希德·馬丁及諾斯羅普·格魯曼等美國三大軍用飛機制造商合作,在美國空軍“鍛造計劃” (Air Force s Forging Initiative)、陸軍制造技術計劃(Army’s Mantech rogram)、國防部“軍民兩用科技計劃” (Dual Use Science and Technology Program)等資助下,致力于飛機鈦合金結構件激光快速成形技術研究及其在飛機上的應用關鍵技術研究。2000 年 9 月在波音和洛克希德·馬丁公司完成了對激光直接成形鈦合金全尺寸飛機機翼次承力結構件研究,構件靜強度及疲勞強度達到飛機設計要求;2001 年為波音公司 F/A-18E/F 艦載聯合殲擊 / 攻擊機驗證機小批量試制了發動機艙推力拉梁、機翼轉動折疊接頭、翼梁、帶筋壁板等飛機鈦合金次承力結構件,其中F/A-l8E/F 翼根吊環滿足疲勞壽命譜4 倍要求,隨后靜力加載到 225% 也不破壞; 2002 年實現激光快速成形鈦合金次承力結構件在 F/A-18 驗證機上的裝機應用。此外,美國還將應用于 F-22 接頭的制造,試驗結果表明其疲勞壽命高出壽命譜的兩倍。
在 LMD 技術取得一定突破的時候,國外還將該技術廣泛用于損傷零件的修復,包括飛機零部件腐蝕零件、航空發動機磨損等零件的修復。美國 AeroMet 公司采用激光成形技術完成了 F15 戰斗機中機翼梁的檢修;美國 Optomec Design 公司,采用激光成形技術進行了 T700美國海軍飛機發動機零件的磨損修復;瑞士洛桑理工學院采用激光成形技術修復單晶渦輪葉片。
1.2 LMD 技術國內發展現狀
我國在金屬材料增材制造領域研究起步較早,技術研究及應用方面具有良好的基礎,特別是在國家自然科學基金“重點項目” 、國家 “973”項目、國家“863” 等重要研究計劃重點支持下,增材制造技術得以快速發展。整個研究工作主要集中于北京航空航天大學、西北工業大學、 北京有色金屬研究總院、華中科技大學、清華大學等單位。其中在 LMD 技術領域上主要以北京航空航天大學、西北工業大學等少數幾家單位。
在“十五”期間,北京航空航天大學突破了飛機鈦合金次承力結構件激光快速成形工藝及應用關鍵技術,構件疲勞、斷裂韌性等主要力學性能達到鈦合金模鍛件水平,2005年成功實現激光快速成形 TA15 鈦合金飛機角盒、TC4 鈦合金飛機座椅支座及腹鰭接頭等 4 種飛機鈦合金次承力結構件(如圖 1 所示)在 3 種飛機上的裝機應用。

圖1 TC4鈦合金座椅上下支座(上)和TA15腹鰭接頭(下)零件實物照片
“十一五”期間, 北京航空航天大學在飛機鈦合金大型整體主承力結構件激光快速成形工藝研究、工程化成套裝備研發與裝機應用關鍵技術攻關等方面取得了突破性進展,提出了大型金屬構件激光直接成形過程 “內應力離散控制” 新方法,初步突破大型金屬構件激光快速成形過程零件翹曲變形與開裂 “瓶頸難題” 突破激光快速成形鈦合金大型結構件內部缺陷和內部質量控制及其無損檢驗關鍵技術,飛機構件綜合力學性能達到或超過鈦合金模鍛件,例如,激光快速成形 TA15 鈦合金缺口疲勞極限超過鈦合金模鍛件 32~53%、高溫持久壽命較模鍛件提高 4 倍(500℃ /480MPa 持久壽命由鍛件不足 50h 提高到激光成形件230h 以上),特別是經后續特種熱處理新工藝獲得“特種雙態組織”(圖2 所示)后,其綜合力學性能進一步顯著提高,疲勞力紋擴展速率降低一個數量級以上(圖 3)。
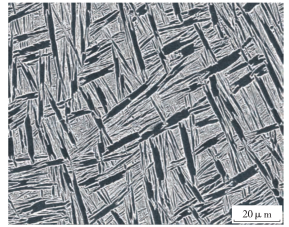
圖2 TA15鈦合金特種熱處理“特種雙態顯微組織
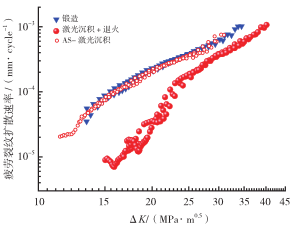
圖3 特種熱處理對疲勞裂紋擴展速率的影響
此外 激光快速成形出 TA15、TC4、TC21、TC18、TC2 等鈦合金先進飛機大型整體主承力關鍵結構件、A-100 等超高強度鋼起落架等飛機關鍵構件、TC11、TC17、Ti60 等鈦合金整體葉盤等航空發動機關鍵部件并在飛機研制和生產中得到成功應用。
西北工業大學自1995 年開始,在國內首先創造性地提出以獲得極高力學性能為目標的金屬增材成形技術構思,賦予“激光立體成形” 之名,依托凝固技術國家重點實驗室開展了系統的研究工作,建立起了包含材料、工藝和裝備技術的完整的技術體系。經過近 20 年的研究,針對大型鈦合金構件的激光立體成形,解決了大型構件變形控制、幾何尺寸控制、冶金質量控制、系統裝備等方面的一系列難題,并試制成功 C919 大飛機翼肋 TC4 上、下緣條構件,該類零件尺寸達 450mm×350mm×3000mm(圖 4),成形后長時間放置后的最大變形量小于1mm,靜載力學性能的穩定性優于1%,疲勞性能也優于同類鍛件的性能。此外,在 LMD 技術零件修復方面也取得了重大進展。TC4 激光修復試樣在低應變區的疲勞壽命高于鍛件,在高應變區低于鍛件,經過噴丸處理后及匹配修復后,高應變區疲勞壽命已非常接近鍛件;圖 5所示為航空發動機軸承后機匣激光修復,通過激光修復軸孔徑向缺陷,成形前安裝邊,恢復零件設計結構及尺寸,為該發動機首次裝機試車提供合格零件;此外,還成功的應用于鋁合金導向葉片、不銹鋼機匣、鈦合金壓氣機靜子葉片、鎳基合金高壓一級渦輪葉片等修復。
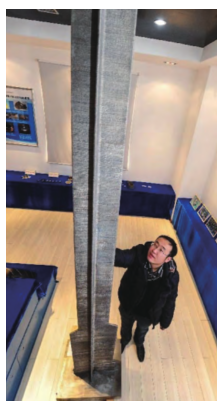
圖4 C919飛機中央翼緣條
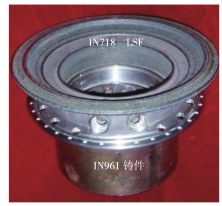
圖5 軸承后機匣激光修復
2 SLM 技術發展現狀
2.1 SLM 技術國外發展現狀
SLM 技術由 SLS 技術發展而來,技術較為成熟且已研制出了商用的設備。目前,對 SLM 技術的研究主要有德國、日本、比利時、美國等國家,并研制出了可商用的設備,如美國的 PHENIX 公司;德國的TRUMPF、EOS、MCP 等公司、日本的 MATSUUR 公司等。
1995 年德國 Fraunhofer 研究所首次提出 SLM 增材制造技術,經過近 7 年的技術研究,于 2002 年成功利用 SLM 工藝制造出了組織致密、成形精度高、力學性能良好的金屬零件,并進行了商業推廣。目前,在德國已有多家公司及單位推出了 SLM設備。如德國的 ILT 與 TRUMPF 公司合作開發的 SLM 設備。該設備采用半導體泵浦Nd :YAG250W 盤形激光器,激光波長為 1030nm,光斑大小可變范圍在 20~40μm[18]。德國EOS 公司推出的 EOS M 400 設備。該設備采用 Yb-fibre 激光器,功率為1kW,最小光斑為90μm,最大掃描速度可達 7m/s。德國MCP公司推出的MCP Realizer設備,該設備采用固體光纖激光器,功率為 100W,加工層厚度可達到 30μm[19-20],可應用于金屬片擠壓工具、壓鑄模具、噴射模具和部分金屬的快速成型。
日本Osakada 實驗室研制的SLM 設備采用Nd :YAG 激光器,峰值功率3kW,平均功率50W,頻率為50Hz,光斑直徑為0.75mm。SLM鋪層厚度為0.1mm,陣鏡掃描速度3~4m/s。研制的金屬零件致密度為92% ;抗拉強度較高,但抗疲勞性能較差。另外,MATSUURA公司制造的SLM設備采用500W 脈沖式CO :激光器,激光波長10640nm,能量峰值達1.5kW,頻率可達100kHz。激光器光斑大小60μm。
比利時魯汶大學對SLM 技術進行了深入研究,研發的SLM 裝備采用300W 連續波或Q調Nd-YAG激光器,激光波長為1064nm,振鏡掃描速度最高可達5000mm/s ;SLM最小鋪粉層厚可達10μm。
2.2 SLM 技術國內發展現狀
在 SLM 技術研究方面,在國家的項目支撐下,國內很多高校都開展了相關的研究,如華中科技大學、華南理工大學等,并取得了可喜的成績。
華中科技大學材料成形與模具技術國家重點實驗室及武漢光電國家實驗室是國內最早從事 SLM 技術的研究工作的單位之一。隨著 SLM關鍵技術的不斷突破及在 SLM 系統制造技術上不斷創新,目前兩個國家實驗室都已成功研制出了自己的 SLM 設備,并生產出了高精度的零件。成形與模具技術國家重點實驗室先后推出了兩套 SLM 設備:HRPM-I 和 HRPM-IIA。HRPM-I 設備采用 IPG 連續模式 200W 激光器,三維動態聚焦掃描陣鏡,成形空間尺寸為250mm×250mm×250mm ;HRPM-IIA 設備采用 IPG 連續模式500W 激光器,三維動態聚焦掃描鏡,成形空間尺寸為 250mm×250mm ×250mm。設備制造的鎳基高溫合金致密度可達到99% 以上;最大拉伸強度超過 100MPa,超過同質鍛件標準;零件表面粗糙度Ra達到20μm。另外,還生產出了多孔零件(長136mm×寬20mm×高25mm壁厚0.1mm)、發動機葉片、旋流器噴嘴等樣件。武漢光電國家實驗室自主設計和制造了NRD-SLM-Ⅰ、NRD-SLM-Ⅱ等設備。其中 NRD-SLM-Ⅰ型設備成形尺寸范圍:80mm×80mm×60mm ;NRD-SLM-Ⅱ型設備成形尺寸范圍:320mm×250mm×250。生產的零件最小壁厚可達 0.13mm,表面粗糙度Ra為5~10μm,尺寸精度為±0.05mm,材料的致密度近乎 100%。利用 SLM技術,武漢光電國家實驗室成功實現了多種薄壁網格結構、流道變截面零部件、多層復合整體葉輪、單葉輪零部件等樣件 3D 打印,如圖 6 所示。華南理工大學與北京隆源自動化成型設備有限公司及武漢楚天工業激光設備有限公司合作,在國內選擇性激光燒結設備的基礎上進行改進,開發了一種 SLM 快速成型設備。該設備采用了額定功率 200W、平均輸出功率 100W 的半導體泵浦YAG 激光器,通過透鏡組將激光束光斑直徑聚焦到100μm 左右。采用高精度絲桿控制鋪粉,鋪粉厚度控制精確,誤差在±0.01mm 以內。采用整體和局部惰性氣體保護的方法。所用軟件包括 AT6400 電機控制軟件、Arps2000 掃描路徑生成與優化軟件、Afswin240 操作系統軟件等。該設備的成型空間為80mm×80mm×50mm,制件尺寸精度達到±0.01mm。表面粗糙度 Ra為30~50μm,相對密度接近100%。
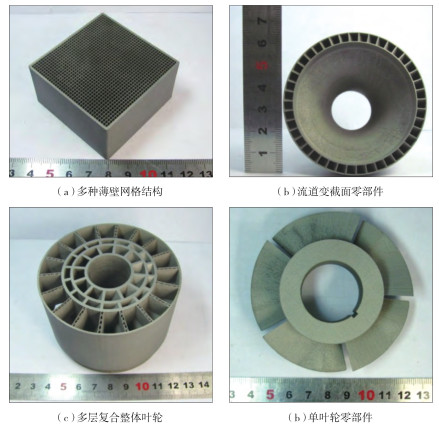
圖6 采用SLM技術打印的樣件
金屬材料增材制造在航空發動機上應用及發展趨勢LMD 和 SLM 技術具有高柔性化、設計制造一體化、高度自動化等特點,大大縮短零件的制造周期。材料使用廣泛,可用于鋁基、鐵基、鈷基、鎳基、鈦基、鈮基材料;錸、銥、鉭、鎢等難熔金屬;銅 - 鋁、TiAl 等金屬間化合物;NiTi 等高加工硬化率材料,給傳統的零件加工開辟出了一條嶄新的道路。目前,增材制造技術已廣泛應用于飛機零部件制造及零件修復。在飛機零部件制造上,已完成 F/A-18E/F 艦載聯合殲擊/攻擊機驗證機發動機艙推力拉梁、機翼轉動折疊接頭、翼梁、帶筋壁板等,F/A-l8E/F 翼根吊環 F-22 接頭,C919 大飛機翼肋 TC4 上、下緣條、機角盒、飛機座椅支座及腹鰭接頭等試制及部分零件裝機應用。在零件修復上,成功用于 F15 戰斗機中機翼梁的檢修、T700 美國海軍飛機發動機零件的磨損修復、單晶渦輪葉片修復、鋁合金導向葉片修復等。
隨著金屬材料增材制造技術的不斷發展和突破,該技術必將應用于零件復雜程度更高、零件工作環境更苛刻、可靠性要求更高的航空發動機上。目前,世界航空發動機壟斷巨頭 GE、PW、RR 等公司都已將目光鎖定在了該技術上,并增大在增材制造方面的研制投入。GE 公司打出了“給我打印一臺噴氣發動機” 的口號并進行了相關的研究工作。GE 公司利用 LMD 技術對相關零件試制進行了技術驗證。在復合材料風扇葉片金屬加強邊試制方面,先利用激光立體成形制備金屬加強邊毛坯件后再進行機械加工。整個加強邊長約 101.6mm,壁厚 0.8~1.2mm,最終加工變形僅為 0.12mm,如圖 7 所示。
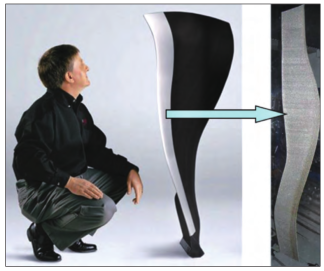
圖7 金屬包邊
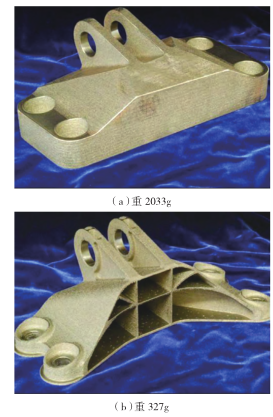
圖8 發動機支架結構
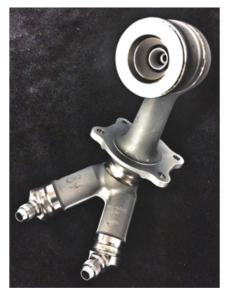
圖9 離心式燃油噴嘴
在發動機支架結構設計試制方面,利用該技術進行了減重設計加工,原零件重約 2033g,最后試制的零件重量僅為 327g,如圖 8 所示。另外,GE 公司還利用增材制造技術實現了 Leap-X 發動機離心式燃油噴嘴的“打印” ,如圖 9 所示,大大節省了零件的生產成本及周期。該項技術被評為全球 2013 年十大技術突破之一,技術成熟度 TRL>8,并且已經通過了 FAA 適航認證。據預測,截2020 年,GE 公司將利用該技術生產超過 100000 個零部件。PW 公司也在增材制造技術方面進行了大量的研究。2013年5月,PW 公司的COO Paul Adams 表示,“我們 (PW 公司)已經在用增材制造技術精密的構建最新的齒輪驅動商用發動機的復雜零件”,并投資了超過 450 萬美元用于PW 公司增材制造研究中心的技術研發。此外,RR 公司也利用該項技術進行了發動機零部件的相關試制,包括機匣零件、蜂窩結構件、異型管等零件的試制并進行了可行性驗證。因此,增材制造技術在航空發動機上的應用之前并未被行業知曉,并不代表該項技術不可行,而是在于如 “薄紗”的技術工藝信息上的封鎖。GE、RR、PW 在該項技術上的重視程度和其在研發上的資金投入及其最新產品的應用即是最好的證明。
航空發動機零件主要以盤類零件和葉片為主。盤類零件雖然結構單一,但零件尺寸較大;葉片尺寸雖然較小,但型面復雜。傳統的機械加工工藝實現了盤、葉片類零件的高精加工,但加工的周期長,經費高,材料利用率低;且由于機械加工技術存在一定的局限性,零件結構形式的設計受到了限制。而增材制造技術可實現不規則型面(包括外部內部的構件加工),實現無模具小余量零加工,大大縮短了零件的試制周期,提高了材料的利用率,減少了零件的試制經費。此外,增材制造技術可實現設計引導制造、功能性優先的設計、最優化設計等,大大提升了零件設計的自由度;在傳統加工工藝時代被認為是必須突破的關鍵技術,在現代將會逐漸演變成通用性的加工要求。因此,增材制造技術可廣泛應用于航空發動機中的空心風扇葉片、空心風扇輪盤、整體風扇葉盤、風扇機匣、增壓級葉片、整體葉盤、壓氣機機匣、燃燒室噴嘴、渦輪葉片等零件研制。
結束語
金屬材料增材制造技術以金屬粉末等為原料,以激光束作為刀具,通過激光逐層熔化沉積,實現了零件的 “近終成形” 。增材制造技術實現了零件的無模具制造,具有材料利用率高、機械加工量小、數控加工時間短、生產成本低、制造周期短、柔性高效等點,給機械加工帶來巨大變革,將傳統的“制造引導設計、制造性優先設計、經驗性設計” 的設計加工思路引領到全新的 “設計引導制造、功能性優先設計、最優化設計” 設計加工領域,給未來的零件設計加工帶來了更寬廣的明天。隨著增材制造技術的不斷發展及技術的不斷突破,研制零件的力學性能、疲勞性能等不斷提高,其在工業領域,特別是航空航天領域必將具有非常廣闊的應用前景。
投稿箱:
如果您有機床行業、企業相關新聞稿件發表,或進行資訊合作,歡迎聯系本網編輯部, 郵箱:skjcsc@vip.sina.com
如果您有機床行業、企業相關新聞稿件發表,或進行資訊合作,歡迎聯系本網編輯部, 郵箱:skjcsc@vip.sina.com
更多相關信息