工具搖動對超聲波加工微孔深徑比的影響
2020-8-13 來源:大連理工大學機械工程學院 作者:雷森旺 周凱 余祖元 李劍中
摘要:微細超聲加工深孔時會出現加工速度太小或加工力過大的現象,導致深孔加工無法繼續。 為此采用輔助工具搖動的方法進行微細超聲微孔加工實驗,成功加工出直徑約為 92 μm、深徑比大于 10 的微孔,且加工效率明顯提高。 同時研究了工具搖動對加工效果的影響。
關鍵詞:工具搖動;微細超聲加工:深孔
隨著科技的不斷發展,航空、醫療、精密儀器等行業對微細零件的需求量與日俱增,在涌現出的諸如微細電火花加工、微細電化學加工、激光加工及微細超聲波加工等特種加工方法中,超聲波加工通過磨粒沖擊脆硬性材料, 可加工導電或非導電材料,且不受材料導熱性的影響,能夠加工出高深徑比和復雜三維型腔的零件[1]。
在前人對微細超聲波加工的研究中,有通過數學建模對工具磨損進行預測[2],有對材料去除模式即對塑性和脆性去除進行探索[3],也有對加工質量、精度影響因素的探究[4],但對微細超聲加工深孔的研究文獻很少。
安成明等在影響微細超聲加工效率的加工參數研究中發現,以加工力反饋控制的恒力進給加工時,加工效率會隨著孔深度的增加而逐漸降低,認為其原因可能是:當孔越深時,加工區域與外界磨粒之間的交換過程越困難,從而降低了材料去除率[5]。 Tateishi 等在用傳統微細超聲加工單晶硅上的深孔時,證明了加工開始產生的邊緣缺陷并非由于加工深度大而造成的,且認為無法加工深孔的
原因是:在恒速加工時,加工深度增加,孔底部無磨粒進入,導致磨粒無法得到交換,且加工力隨著工具向下進給而增大,甚至會使工具折斷而導致加工無法繼續。
基于此,Tateishi 等利用電流變流體輔助超聲加工方法,成功地加工出直徑為 100 μm、深徑比為 10 的孔[6]。 王丹等采用五因素五水平正交試驗方法,分析了不同加工參數對微晶云母陶瓷的微細超聲加工工具體積損耗率的影響,并選擇較優的參數組合在微晶云母陶瓷片上加工出直徑為 80 μm、深度為 530 μm、 孔側壁錐度小于 0.5°的深通孔,其深徑比為 6.625,但加工時間較長,達 4.5 h[7]。
在電火花加工模具實踐中,通過電極搖動可減少切屑在放電間隙的堆積,從而避免了加工過程中的短路和拉弧[8]。 余祖元等用微細電火花輔助電極搖動的方法在不銹鋼上成功加工出深徑比為 18 的微孔[9],并認為利用工具搖動可增加加工屑的活動空間,便于排除加工屑,從而既能提高深徑比,還能提高加工效率和精度。 此外,通過設計不同的工具搖動軌跡,可加工出不同形狀的孔。
然而,在用微細超聲加工深孔時會出現加工速度減小[5]或工具折斷[6]等現象,造成深孔加工無法進行。 對此,本文提出一種結合工具搖動的微細超聲加工方法。 在進行深孔加工過程中,當工具進給到一定深度后,工具搖動增加了空間,便于排除加工屑,促進加工區域的磨粒更新,從而達到提高微細孔加工效率和深徑比的目的。
1 、實驗準備
1.1 實驗設備
圖 1 是微細超聲立式加工裝置的示意圖。 該裝置包括微細工具電火花制備模塊、精密伺服進給模塊、微細超聲加工模塊及加工力監測模塊,其實物照片見圖 2。
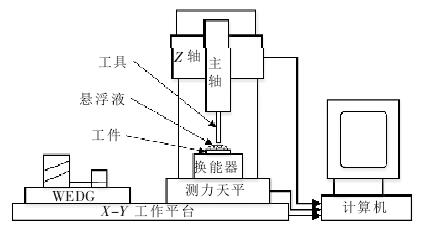
圖 1 微細超聲加工裝置結構示意圖
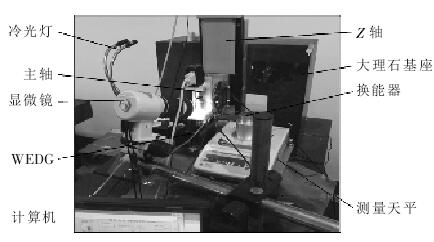
圖 2 微細超聲加工裝置實物圖
微細工具電火花制備模塊由 RC 脈沖電源、放電狀態檢測和 WEDG[10]走絲機構組成,主要用于微細工具的在線制備。 精密伺服進給模塊采用高精度運動平臺,其定位精度為 1 μm,精密旋轉主軸的徑向跳動小于 1 μm,最高轉速達 40 000 r/min。 微細超聲加工模塊主要由超聲波發生器、 超聲波換能器、加工力狀態監測裝置及磨粒懸浮液組成,其中,超聲波發生器的振動頻率約為 35 k Hz,振幅可調節范圍為 0.3~3 μm;加工力監測裝置采用稱重范圍為1100 g、感量為 0.001 g 的精密電子天平對加工力進行實時測量;磨粒懸浮液由金剛石粉末與去離子水按一定質量比配制而成。
1.2 實驗條件
實驗采用恒力加工、工件振動[11]的方式進行,實驗條件見表 1。 實驗過程中,每一個搖動半徑對應一系列的搖動速度, 當搖動半徑和搖動速度均為 0時,即工具不搖動;振幅通過調節超聲波發生器的輸入電壓大小進行控制;懸浮液由金剛石磨粒和去離子水配制而成,其質量分數為 3%。
表 1 實驗條件
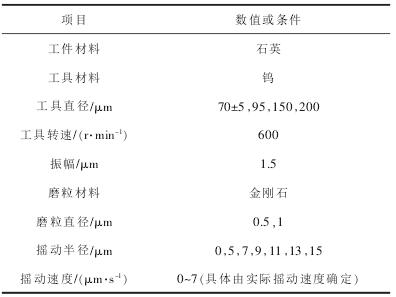
本實驗為圓孔加工,工具的搖動運動示意見圖3。通過 X-Y 雙軸聯動實現圓形搖動軌跡,即工具在轉動進給的同時,沿著圓形搖動軌跡運動。
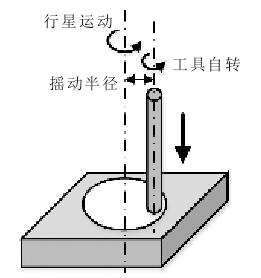
圖 3 工具搖動運動示意圖
1.3 實驗方法
將大小合適的石英片通過強力雙面膠粘在換能器振動頭上,并在石英片上滴加懸浮液。 工具的磨損長度通過加工前后對工件上同一點進行探測的 Z 軸坐標之差得到,測量的加載力值為 0.01 g,
其計算示意見圖 4。 為保證測量值的準確性,加工前后采用多次探測并取其平均值。
本文設置加工力的最大值為 3 g。 在實驗過程中,通過改變進給速度保持加工力在一定范圍內波動(恒力加工)。
圖 5、圖 6 分別是正常加工和無法繼續加工的力信號曲線。 當加工無法繼續時,工具與孔底部之間的磨粒較少或沒有磨粒,工具將直接撞擊工件,導致力信號曲線波動劇烈,同時也沒有產生正常去除材料的力信號(圖 5 所示虛線框中的曲線)。 當進給速度小于 0.2 μm/s 且力信號曲線波動迅速時則停止加工,此時的進給深度作為最終進給深度,再減去工具磨損量,即可得到加工孔的深度。
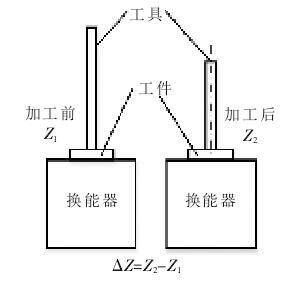
圖 4 工具磨損計算示意圖
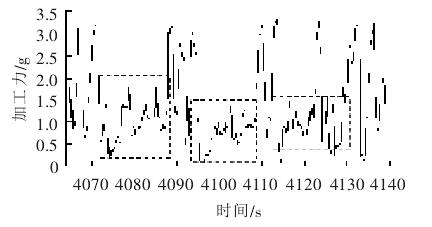
圖 5 正常加工時的力信號曲線
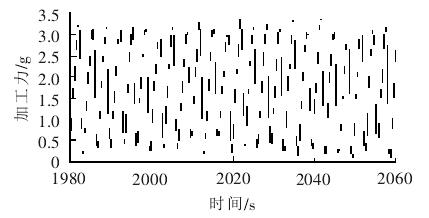
圖 6 無法繼續加工時的力信號曲線
2 、實驗結果及分析
2.1 無工具搖動加工實驗
在進行無工具搖動微細超聲深孔加工實驗時,記錄工具進給一定深度所用的時間,以驗證文獻[5]中的現象是否為共性。 如表 2 所示,1#~6# 是無工具搖動時各孔的加工參數。 在實驗中發現
,未使用工具搖動進行深孔加工時, 達到一定進給深度后,工具只能以很小的速度向下進給,耗時長。
根據實驗數據繪制進給深度與加工時間的關系曲線, 由圖 7可見,當工具進給到一定深度后,其進給速度會逐漸減小,即加工速度減慢,加工效率降低,與文獻[5]描述的一致, 其中 1# 工具所對應的曲線的減小趨勢最明顯。
此外,4# 工具加工的孔,其深徑比最大,為 6.38,孔徑為 107.7 μm;但耗時較長,約 49 min。
表2 各孔的加工參數
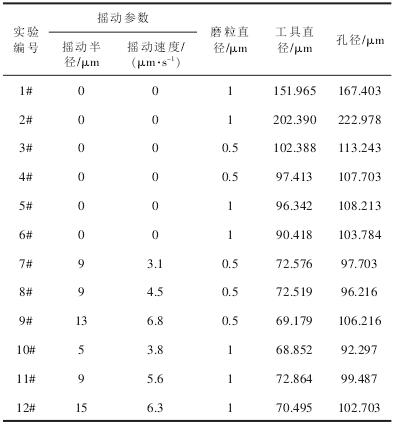
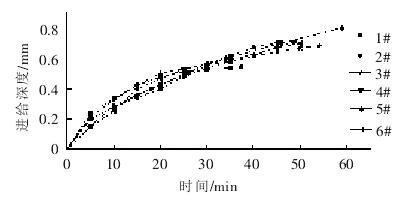
圖 7 無工具搖動加工時的進給深度與加工時間的關系曲線
2.2 工具搖動加工實驗
以 100 μm 作為微孔的目標直徑進行工具搖動微細超聲深孔加工實驗,并與無工具搖動加工進行比較(以 6# 工具為代表)。
表 2 所示 7#~12# 是工具搖動時各孔的加工參數,根據實驗數據繪制進給深度與加工時間的關系曲線,對比 6# 工具可發現,使用工具搖動加工時,達到一定進給深度后,工具仍能以較大的速度進給, 且加工力波動在設定范圍內,用時也較短。 如圖 9 所示,10# 工具加工的微孔直徑約為 92 μm,深徑比為 10.1,耗時 25 min。
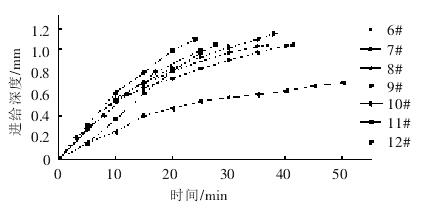
圖 8 工具搖動加工時的進給深度與加工時間的關系曲線
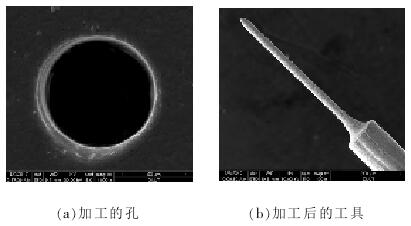
圖 9 深徑比為 10.1 的孔及加工后的工具
2.2.1 工具搖動對深徑比的影響
圖 10 是工具搖動加工微孔和無搖動加工微孔的深徑比。 分析可知,1#、2# 工具的直徑較大,分別為 152、202 μm, 所加工孔的深徑比最小;3#~5# 工具的直徑均為 100±5 μm,6# 工具的直徑為 90 μm,所加工孔的深徑比均在 6~7 之間;7#~12# 工具的直徑為 70±5 μm,且采用搖動加工后,存在搖動半徑,所加工孔的深徑比均大于 9。 因此,使用工具搖動進行微孔加工,可使孔的深徑比有較大的提高。
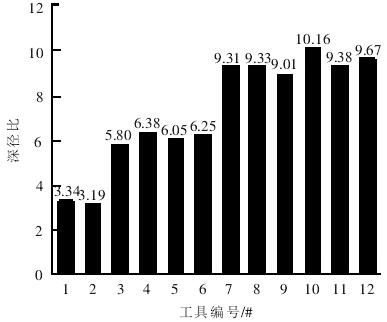
圖10 工具搖動對孔的深徑比的影響
2.2.2 工具搖動對加工效率的影響
由圖 8 可知,使用工具搖動進行加工,在提高孔的深徑比的同時,還縮短了加工時間,提高了加工效率。 由于工件材料去除率反映了微孔直徑、加工深度、工具損耗和加工時間等情況,因此能綜合反映出超聲微孔加工效率和綜合性能。 本文通過計算各孔的材料去除率來對比加工效率。 材料去除率vw的計算公式為:
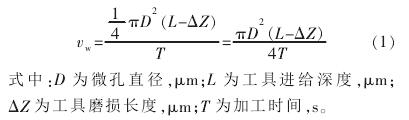
由圖 11 可見,1#、2# 工具加工的材料去除率較大,主要是由于工具直徑較大,故加工能力強;3#--6# 工具的直徑相差不大 , 故材料去除率差別也較小; 在使用工具搖動加工后,7#~12#
工具加工的材料去除率均有所提高, 其提高程度與搖動參數有關。
為了探究工具搖動參數對材料去除率的影響,在相同的搖動半徑下,選用不同的搖動速度進行超聲微孔加工實驗,并取相同的進給深度為 1.05 mm,工具直徑為 71±3 μm,其他實驗條件同表
1。
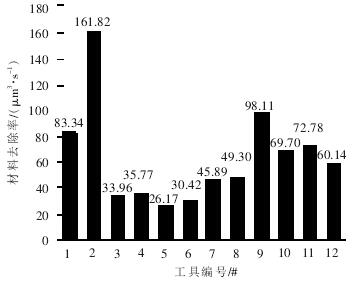
圖 11 工具搖動對孔的材料去除率的影響
由圖 12 可看出,當工具搖動半徑一定時,材料去除率隨著搖動速度的增加而增大。 分析原因:搖動速度增加時,處于工具端部下方的加工區域移動速度加快,孔底部的材料更快地被去除,從而提高了材料去除率;同時,工具與加工孔側壁間的懸浮液流動加快, 促進加工屑的排出和孔底磨粒的交換。
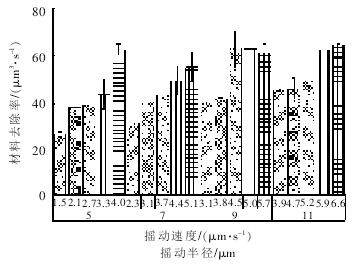
圖 12 材料去除率隨工具搖動速度的變化(粒徑 1 μm)
另外,搖動半徑為 9 μm 時,材料去除率先增大、后減小,這可能是由于隨著搖動速度增加到一定值并超過了該加工條件下的加工能力后,加工效率隨之降低。
由圖 13 可看出,材料去除率均隨著搖動速度的增加呈先增大、后減小的規律。 這可能是由于使用直徑為 0.5 μm 的磨粒時,加工能力減小,隨著搖動速度增加,更快地達到加工能力的最大值。
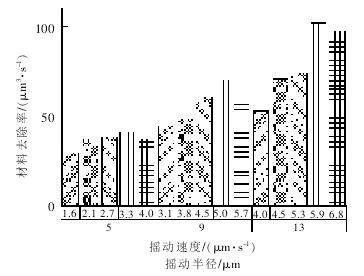
圖 13 材料去除率隨工具搖動速度的變化(粒徑 0.5 μm)
由于實際搖動速度與給定搖動速度存在很大差異,故未進行相同搖動速度、不同搖動半徑下的加工實驗,但對此種情況下的材料去除率做了如下猜測:隨著工具搖動半徑的增加,去除的材料體積將增多,材料去除率隨之會減小;當搖動半徑增加后,工具與孔側壁間的距離將增大,便于加工屑的排出和孔底部磨粒的交換,這會促使材料去除率增大。
由于上述兩個原因,材料去除率可能隨著工具搖動半徑的變化而不呈現出明顯的規律。
2.2.3 工具搖動對工具磨損的影響
在微細超聲加工過程中, 特別是長時間加工,工具磨損較嚴重。 工具磨損與加工時間、工具直徑、磨粒大小、靜壓力、振幅等有直接關系[12]。 本實驗中,加工深孔的時間較長, 對工具磨損的影響較大;同時使用了工具搖動, 其對工具磨損的影響尚不明確。 在實際生產中,衡量工具是否耐磨損,不只考慮工具磨損速度,還要考慮相應的加工速度,故采用工具相對磨損率作為衡量工具耐磨損的指標。對上述實驗中不同工具的相對磨損率進行了比較,工具相對磨損率 θ 可表示為:
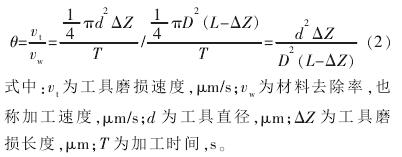
圖 14 是工具 1#~12# 的相對磨損率。 可見,使用工具搖動后,工具磨損加快。 分析原因:工具搖動促進了加工屑的排出和孔底部磨粒的交換,同時加快對工件和工具材料的去除,導致工具磨損增大。
2.2.4 工具搖動對加工間隙的影響
在超聲加工微孔過程中,加工區域與外界磨粒會隨著懸浮液的流動進行交換,且高速運動的磨粒對側壁也會造成很大的沖擊,因此孔的尺寸相比于工具尺寸有所增大,在孔壁與工具之間會形成加工間隙,間隙的大小將影響所加工孔的尺寸。
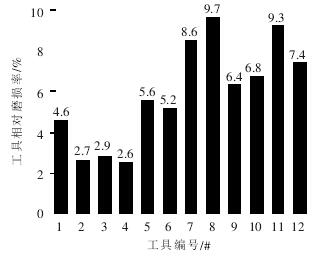
圖 14 工具搖動對工具相對磨損率的影響
通過對上述實驗中單邊加工間隙的計算和比較,分別得出了無工具搖動和工具搖動時的單邊加工間隙 Dg的表達式:
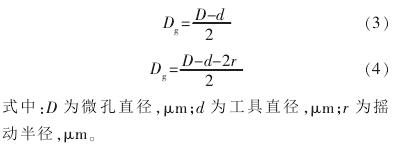
圖 15 是不同的工具加工孔的單邊加工間隙。由 7#~12# 對應的工具搖動后的實驗數據可見,單邊加工間隙有減小的趨勢。 分析原因:當工具搖動后,磨粒與外界的交換通道加大,對孔側壁的沖擊作用減小,故加工間隙減小。
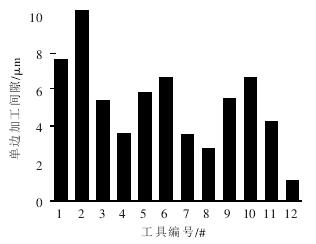
圖 15 工具搖動對單邊加工間隙的影響
4 、結束語
本文提出了輔助工具搖動的微細超聲深孔加工方法。 通過工作平臺 X-Y 軸的聯動進行圓周運動,實現圓形搖動軌跡,結合傳統微細超聲加工,成功加工出深徑比為10 的微孔, 且加工效率明顯提高。
在研究搖動參數對加工效率的影響時,發現材料去除率會隨著搖動速度的增加而增大,有時搖動速度增加到一定程度后會使材料去除率減小,并猜測搖動半徑變化對材料去除率的影響無明顯規律。同時,使用工具搖動進行微孔加工時,會使工具磨損增加,而加工間隙減小。
投稿箱:
如果您有機床行業、企業相關新聞稿件發表,或進行資訊合作,歡迎聯系本網編輯部, 郵箱:skjcsc@vip.sina.com
如果您有機床行業、企業相關新聞稿件發表,或進行資訊合作,歡迎聯系本網編輯部, 郵箱:skjcsc@vip.sina.com
更多相關信息