0 引言
金剛石砂輪有優良的機械性能, 在陶瓷、石材和玻璃等硬脆性材料加工中得到了廣泛應用。釬焊金剛石砂輪具有磨粒出露高、砂輪表面容屑空間大、不容易發生切屑堵塞、磨料利用率高等優點[ 1] ,在花崗石加工中受到重視。要快速降低磨削加工表面的粗糙度并使砂輪的綜合磨損和加工效率得到平衡, 關鍵問題是確定最佳的單顆磨粒的最大切削厚度, 這不僅關系到單顆磨粒的受力情況, 還關系到材料的去除方式[ 2] 。不同的材料去除方式會影響磨削加工的能量消耗和工件表面質量。單顆磨粒最大切削厚度可以用下式計算[ 3]
式中, r 為切削路徑任一點處切屑寬度與厚度的比, r =2tanH; H為切屑底部夾角的一半; vw 為工件的進給速度; vs為砂輪的圓周線速度; ap 為磨削深度; de 為砂輪的當量直徑, 平面磨削時當量直徑等于砂輪直徑, 即de = ds ; Ca 為砂輪表面單位面積的有效磨粒數。
通常人們用顯微鏡觀察砂輪表面露出的磨粒數目來確定Ca [ 4] , 他們在計算時假設砂輪表面被顯微鏡觀察到的金剛石磨粒的出露高度都一致, 全部參與了磨削。實際上要保證砂輪上所有顆粒的出露高度一致且全部參與磨削是不可能的, 因此這種方法得到的是砂輪的理論總磨粒數, 比實際參與磨削的有效磨粒數要大得多。金剛石砂輪表面實際有效磨粒數占理論總磨粒數的比例是多大, 至今沒有明確的試驗依據支撐[ 5] 。本文通過分析磨削弧區溫度信號特性與磨粒的關系, 確定弧區溫度信號中毛刺狀脈動是有效磨粒的熱沖擊信號, 用統計的方法推算了金剛石砂輪實際參與磨削的有效磨粒數占理論總磨粒數的比例。
1 試驗方案
我們制備了4 個單層釬焊金剛石砂輪及1 個電鍍金剛石砂輪作為磨削工具, 所用高強度金剛石顆粒品級一致, 粒度均為30/ 35。釬焊金剛石砂輪的磨粒排布方式如圖1 所示, 電鍍金剛石砂輪的磨粒為隨機排布, 砂輪的具體參數見表1。磨削試驗在MQ6025A 萬能工具磨床上以干磨削的方式完成。試驗所用工件材料為黑色天然花崗石, 磨床工作臺橫向進給速度為011m/ s, 主軸轉速采用6400r/ min 和3200r/ min 兩檔, 依次用01 01mm、01 02mm 和0103mm 3 種磨削深度進行試驗。磨削過程中, 用薄片式夾絲熱電偶法[ 6, 7] 測量磨削弧區的溫度, 熱電偶的輸出連接到DEWE2010 動態信號采集系統, 檢測系統量程選- 01 1~ 01 1V, 采樣頻率為20kHz, 同時用帶模擬電壓輸出的GX3 型三相功率計測量磨床主軸電機功率的變化, 功率計的輸出由DEWE2010 同步采集。
2 試驗結果及分析
2. 1 磨削溫度信號及分析
試驗所得溫度信號混有噪聲, 采用小波分析理論的給定閾值消噪處理方法對信號進行處理, 可以較好地保留信號的有用成分且去噪效果明顯[ 7] 。圖2 是砂輪2 在主軸轉速vs = 3200r/ min、磨削深度ap= 0102mm、工作臺速度vw = 100 mm/ s時磨削弧區溫度信號在MATLAB 軟件中采用db3 小波
給定軟閾值消噪后的結果。可以看出, 01 05~0110s 以外區域基本上沒有任何噪聲, 但01 05~0107s 區間仍有許多高頻的毛刺狀脈動成分, 毛刺集中在溫升的過程。研究人員普遍認為這是磨粒周期性熱沖擊作用的結果[8] 。文獻[ 7] 提出溫度信號出現毛刺的階段即是砂輪磨削熱電偶絲的過程,因此那些毛刺就是砂輪磨粒磨削工件及熱電偶時所造成的溫度波動。每一個參與磨削的磨粒引起1 個熱沖擊, 則所有磨粒的熱沖擊結果疊加形成了磨削弧區的溫度和溫升。由于磨粒的熱沖擊作用是瞬間完成的, 要準確檢測瞬間的溫度波動, 則溫度傳感器的動態響應速度要足夠快。
2. 2 熱電偶動態響應特性分析
試驗使用夾絲熱電偶法測量接觸弧區溫度, 熱電偶節是由夾在工件間的兩金屬薄片的頂部在磨削弧區被砂輪磨粒磨削后搭接而形成的。根據文獻[ 9] , 薄片熱電偶的時間常數可以推算為
式中, D為片狀熱電偶的厚度; A為熱電偶的熱擴散系數。因此, 要提高熱電偶的動態響應速度, 就必須盡量減小熱電偶的厚度。熱電偶的幅頻特性和相頻特性分別為
試驗使用的砂輪對應熱電偶寬度的圓周位置上, 單位長度的磨粒個數為01 35 個/ mm, 當砂輪以轉速6400r/ min 對工件進行磨削時, 假設經過熱電偶的磨粒有80% 磨削到工件及熱電偶并產生熱沖擊, 則熱沖擊的角頻率Xmax U 46 000rad/ s。由式( 3)可得熱電偶的厚度D[ 01 008mm, 本文試驗使用的薄片熱電偶厚度為01 008mm, 能在5%誤差范圍內檢測到磨粒瞬間熱沖擊信號。
2. 3 溫度信號中毛刺個數的統計
如果磨過工件及熱電偶的每一個有效磨粒都形成1 個熱脈沖, 表現為溫度信號里的1 個毛刺,則1 個完整磨削溫度信號中的毛刺總個數就是實際磨過熱電偶的有效磨粒的總個數。基于這個前提, 可利用溫度信號中的毛刺數量來確定砂輪有效磨粒數。那么, 各種磨削參數下所測溫度信號的毛刺數量在理論上應該隨磨削深度的增大而增多; 與砂輪轉速、砂輪圓周表面上的磨粒密度成正比。為了證明這個推論, 必須做大量磨削試驗, 并對所測溫度信號中的毛刺數量進行統計分析。試驗中, 磨床工作臺橫向移動速度保持不變, 分別改變砂輪轉速及磨削深度, 用5 個不同的砂輪磨削石材, 在各試驗參數條件下分別采集多個溫度信號。統計各參數所測磨削弧區溫度信號的毛刺個數, 計算平均值, 結果如圖3 所示。可以看出, 磨床主軸轉速為3200r/ min 時, 各砂輪磨削弧區溫度信號中的毛刺個數隨磨削深度的增大而增加; 當磨床主軸轉速調到6400r/ min 時, 除了兩個直徑為80mm 的砂輪在切深為0102mm 時的毛刺數量偏多外, 其余砂輪磨削溫度信號的毛刺個數也呈現隨磨削深度增大而增多的趨勢。這個結果與前面提到的1 個毛刺代表1 個有效磨粒的熱沖擊的推論是相符的。此外, 同1 個砂輪在采用相同磨削深度而主軸轉速提高一倍時, 理論上參與磨削的磨粒個數應增加一倍, 毛刺個數也應增加; 試驗結果顯示信號中的毛刺個數隨主軸轉速的提高而增多。綜合以上分析的毛刺數量與砂輪磨粒數的相關性, 可以認為熱電偶測得的磨削溫度中的毛刺狀脈動信號就是砂輪有效磨粒產生的熱脈沖。
2. 4 砂輪表面上的理論總磨粒個數計算
由于釬料對金剛石磨粒的把持力高, 釬焊金剛石砂輪在加工過程中幾乎沒有發生金剛石磨粒直接脫落的現象。隨磨削過程的進行, 磨粒被平穩地磨損, 因此在整個試驗中, 各個金剛石砂輪上的總磨粒個數不變, 單位面積上的理論總磨粒個數C 也不變。
金剛石砂輪上的磨粒按圖1 規律排布, 砂輪轉速為n, 磨床工作臺以速度vw 帶著工件經過磨削區, 則熱電偶片被砂輪磨過的時間為式中, bu 為
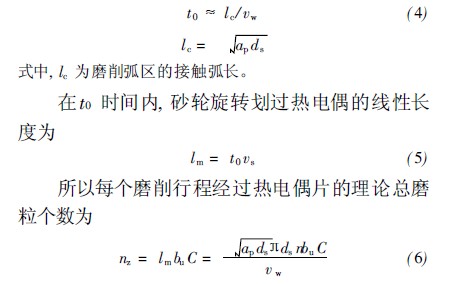
薄片熱電偶的寬度。根據式( 6) , 理論上nz 應該隨ap 增大而增大,并與砂輪轉速n 成正比。實際加工中, 磨削弧區接觸狀況復雜, 砂輪本身存在圓度誤差, 每顆磨粒的出露高度不可能都一樣, 同時受磨床主軸剛度限制, 磨削中存在一定振動, 所以熱電偶片2mm 寬度對應的砂輪圓周上的磨粒不可能全部參與磨削, 文獻[ 10] 指出在鋸切試驗中實際參與切削的磨粒數只是金剛石砂輪表面總磨粒數的一部分。實際參與切削的顆粒數nm 小于理論上參與磨削的總磨粒個數nz , 兩者的比值即有效磨粒比為
2. 5 有效磨粒比計算
把圖3 統計的各磨削加工參數下溫度信號的平均毛刺個數nc 作為砂輪參與磨削的實際有效磨粒個數nm, 與用式( 6) 計算的t0 時間內經過熱電偶的理論總磨粒個數比較, 計算各個砂輪的有效磨粒比G= nm / nz = nc / nz , 得到結果如圖4 所示。可以看出, 砂輪轉速為3200r/ min 時, 3 號砂輪在磨削深度為01 01mm 和0102mm 時的G比較小, 其余砂輪在不同磨削深度下的有效磨粒比均為20% ~30%; 砂輪轉速為6400r/ min 時, 有效磨粒比在5%~ 20%范圍內波動。
比較電鍍砂輪與釬焊砂輪的試驗數據, 發現采用不同工藝制造的兩種砂輪磨削產生的溫度信號形態和特征是相似的, 有效磨粒比也很接近。電鍍砂輪磨削弧區的平均磨削溫度和磨削溫度峰值比釬焊砂輪略低, 但差別不大。
主軸轉速提高使電鍍金剛石砂輪和釬焊金剛石砂輪的有效磨粒比幾乎降低了一半。主要是因為受主軸剛度和砂輪圓度誤差的限制, 同時磨削過程中存在振動, 當主軸轉速提高, 磨削振動加大, 磨削狀態變得惡劣, 使能夠參與磨削的有效磨粒數比慢速時有所減少, 造成有效磨粒比下降近50%。
2. 6 單顆金剛石磨粒最大切削厚度計算
假設熱電偶片2mm 寬度對應的砂輪圓周表面上的顆粒在經過熱電偶片時都進行了有效磨削, 產生了熱沖擊, 即砂輪的有效磨粒比為100%, 則可以用表1 中砂輪單位面積的金剛石顆粒數C 作為Ca , 當切屑底部夾角的一半H取60b, 根據式( 1) 分別計算出5 個砂輪在主軸轉速為3200r/ min 時單顆金剛石磨粒的理論最大切削厚度, 結果如圖5a所示。
根據有效磨粒比G及表1 砂輪單位面積上總的金剛石顆粒數C, 用Ca= GC 來計算砂輪表面單位面積參與磨削的有效顆粒數, 代入式( 1) 可得到單顆磨粒最大切削厚度hmax , 如圖5b 所示, 可以看出, 除了3 號砂輪外, 其余的幾個砂輪對應的點基本上很接近。圖4 所示的有效磨粒比的結果也顯示3 號砂輪在磨削深度為0102mm 處的數據有異常。其余4 個砂輪的計算結果與圖5a 比較, 可以看出, 總體趨勢是一致的。采用有效磨粒比G推算出來的最大切削厚度比按100% 有效磨粒比計算的結果大, 特別是在磨削深度比較小的情況下, 差別更明顯。
2. 7 單顆金剛石磨粒磨削時消耗的功率
把試驗所測砂輪主軸電機穩定磨削工作狀態時消耗的功率值減去空轉時消耗的功率值便得到磨削過程中主軸電機消耗的凈功率值P, 則平面磨削中單顆金剛石消耗的磨削功率為
計算結果如圖6 所示, 釬焊砂輪和電鍍砂輪磨削時, 單顆金剛石顆粒所消耗的功率均隨磨削深度的增大而成比例增大, 隨砂輪轉速的提高而變大。磨削深度較小時, 砂輪轉速的提高對單顆金剛石磨粒消耗的功率影響較小; 當磨削深度增大到01 03mm 時, 砂輪轉速的提高使單顆金剛石消耗的功率急劇增加。因此, 從提高磨削效率、減少能量消耗和提高有效磨粒比這幾個方面綜合來考慮, 應該采用較大的磨削深度及較低的砂輪主軸轉速進行磨削加工。
3 結論
試驗結果及分析表明, 薄片式熱電偶可以檢測磨削過程磨粒周期性的高頻熱沖擊信號; 通過磨削弧區溫度信號中的毛刺狀熱脈沖的個數確定金剛石砂輪實際參與切削的顆粒個數, 推算實際有效磨粒比是一種可行的方法; 通過分析金剛石砂輪有效磨粒比與砂輪速度的關系, 發現提高砂輪轉速會使有效磨粒比大大降低。在確定實際有效磨粒比的基礎上計算了單顆金剛石的實際最大切削厚度及其在磨削中消耗的功率, 提出優化磨削加工參數的有效方法。本文試驗結果對金剛石砂輪的設計、磨削加工參數的優化及花崗石平面磨削加工理論的深入研究具有參考價值。
如果您有機床行業、企業相關新聞稿件發表,或進行資訊合作,歡迎聯系本網編輯部, 郵箱:skjcsc@vip.sina.com