滾齒機加工系統的剛度、固有頻率和阻尼是影響機床加工精度的重要因素, 也是評定機床質量的重要參數。如何合理地對滾齒機加工系統進行評定, 對機床及其主軸的設計, 以及加工過程中對誤差的補償都具有重要的意義。本文所研究的YK3610數控零傳動臥式滾齒機工件主軸和滾刀主軸都取消了齒輪傳動鏈, 采用了內聯傳動方式, 因此研究零傳動滾齒機加工系統的動態特性成為一項新的研究內容。該滾齒機兩主軸結構的三維圖如圖1所示。這種傳動方式響應時間短, 傳動效率高, 傳動精度遠遠高于齒輪傳動滾齒機, 因此對于今后提高齒輪加工精度具有重大意義。其傳動精度主要決定于反饋裝置的精度, 由于直接驅動只有很少的運動部件, 所以噪聲很小, 系統中唯一的磨損件是軸承, 維護減少, 如果軸承采用定期潤滑, 整體電主軸裝置就能達到零維護。
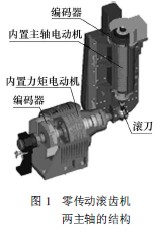
可以看出, 使用零傳動技術, 機床的結構將會得到最大限度的簡化, 它是機床設計和制造技術的一次重大革新, 將大幅提高滾齒機床的加工精度和加工效率。
1 滾齒機加工系統剛度動力學模型
YK3610零傳動滾齒機為臥式加工滾齒機, 在加工過程中工件安裝在芯軸上, 芯軸裝夾在工件主軸上, 工件主軸由力矩電動機(簡稱DDR 電動機)直接驅動, 為了提高加工過程中主軸系統的剛度, 減小由于滾齒切削力作用使主軸變形帶來的加工誤差, 芯軸的末端使用尾座頂尖支撐, 如圖2所示。
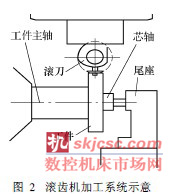
由圖2 可知, 滾齒機在加工過程中, 與工件有直接關系的是工件主軸、頂尖、滾刀主軸和尾座, 這四部分的動態特性將直接影響到工件的加工質量, 為了便于分析, 只考慮影響加工精度的動力響應的水平方向(加工誤差敏感方向)的分量。基于以上分析, 假定各振動都是線性的, 由于整個系統的振幅和阻尼都比較小, 可認為主軸系統各質量都是由質量點構成, 滾齒機加工過程的主軸系統簡化成如下模型: 1)將工件、芯軸和夾具簡化為一體,由于芯軸本身的剛度和刀具對工件徑向切削力在工件加工質量的同一方向產生相同的影響, 所以將兩者簡化為一個單自由度彈簧系統; 2)由于工件主軸本身的剛度在加工過程中對工件加工質量也產生影響, 故將工件主軸本身剛度簡化為一水平的單自由度彈簧系統; 3)尾座頂尖系統的剛度在加工過程中產生水平方向的振動, 是影響工件加工質量的又一大因素, 同樣將其簡化為與工件主軸正交方向的單自由度彈簧系統。對滾齒機主軸系統剛度簡化的動力模型如圖3所示。
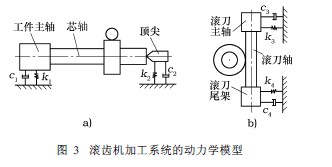
2 加工系統剛度數學模型
211 各振動體的傳遞函數
把刀架、尾座及工件主軸看作單自由度振動體,各振動體的傳遞函數可表示為:
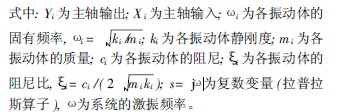
212 加工系統剛度傳遞函數
滾齒機在加工過程中, 由于工件主軸、芯軸兩端模態剛度、阻尼和質量不同, 所以在徑向切削力的作用下, 工件主軸發生振動位移, 如圖4a所示; 同理滾刀軸也發生了振動位移, 如圖4b所示。
工件在切削力的作用下發生的振動位移x 12為:
x12 = ( x2 l1 + x 1 l2 ) / ( l1 + l2 ) ??????? ( 2)
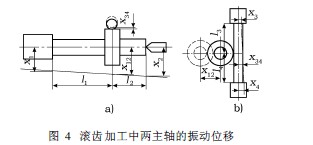
滾刀在切削力的作用下發生的振動位移x 34為:
x34 = ( x4 l3 + x 3 l4 ) / ( l3 + l4 ) ??????? ( 3)
滾齒切削過程中系統發生的振動位移x系統是由工件振動位移和滾刀振動位移兩部分組成的, x系統為:
x系統= x12 + x34 ???????????? ( 4)
由傳遞函數的定義可知:
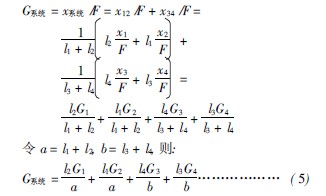
式中: G系統為滾齒機主軸系統的傳遞函數; G 1、G 2、G3、G 4 分別為工件主軸頭、頂尖、滾刀主軸頭、滾刀尾座系統的傳遞函數; F 為切削力在徑向的分量。
式( 5)實際為滾齒機床的平均動柔度, 將式( 1)代入式( 5)并進行整理可得:
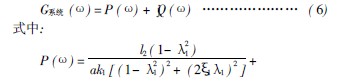
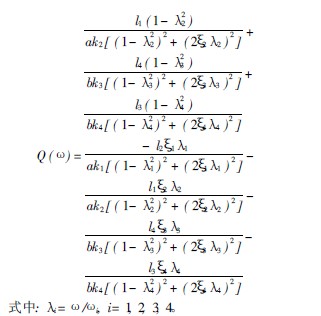
式( 6)是滾齒機主軸系統動柔度的復數表達形式。但是, 此數學模型是在不考慮芯軸和滾刀軸本身剛度、阻尼、質量和固有頻率的前提下建立的。若把這些因素考慮其中, 滾齒機主軸系統動柔度模型將更加復雜。
213 加工系統數學模型
由剛度的定義可知:
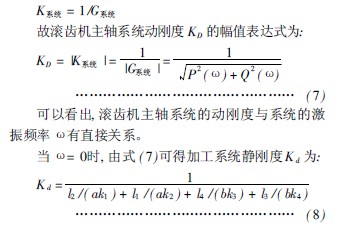
由此可知, 當X= 0時, 式( 8)可作為評定滾齒機床加工系統靜剛度的依據。這證明了滾齒機床加工系統靜剛度K d 是加工系統動剛度KD 在激振頻率為零時的特例。當該滾齒機床處于加工狀態時, 對加工系統各部件進行適當定義, 可預測出加工系統激發出來的頻率成分、振幅和阻尼等。
對各部件的剛度進行測試并定義見表1。
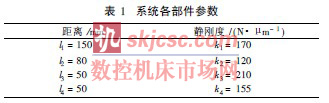
可以得到零傳動滾齒機加工系統的靜剛度K d 為:
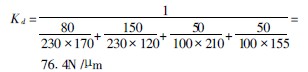
3 零傳動滾齒機加工系統的動態特性試驗
激振試驗是尋找機床動態特性參數的重要手段,對于該零傳動滾齒機激振試驗而言, 以動態特性中的頻率為主要研究對象, 試驗方法如圖5 所示。首先對工件主軸系統和滾刀主軸系統分別進行激振試驗, 對試驗結果進行自譜分析如圖6、圖7所示, 圖6中可以看出, 通過激振試驗, 工件主軸系統在頻率為425H z處有較高的能量譜, 可由此判斷, 工件主軸系統的固有頻率為425H z。同樣從滾刀主軸系統自譜分析圖7可知, 滾刀系統在頻率1806H z處具有較高的能量譜,但是比較圖6和圖7可知, 滾刀主軸系統的能量普基數明顯高于工件主軸系統, 這說明滾刀主軸系統具有較好的剛度和阻尼, 它有利于工件加工精度的提高。
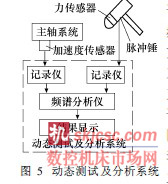
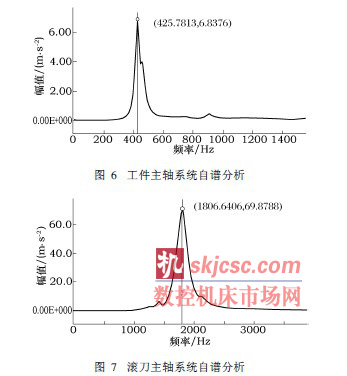
但是根據零傳動滾齒機的動力學模型和數學模型可知, 處于加工過程中的滾齒加工系統整體動態特性將會處于滾刀主軸系統和工件主軸系統之間, 即加工系統激發出來的頻率成分應該處于兩者固有頻率成分之間, 圖8所示為加工過程中加工系統試驗結果。該試驗中零傳動滾齒機的滾刀主軸轉速為535r/m in,滾刀齒數為12, 可知加工中理論上切削頻率應為107H z, 而試驗中能量譜值最高處的頻率10714H z即可確定為切削頻率, 而頻率50716H z、61512H z、71219Hz都可能為該零傳動滾齒機加工系統激發出來的頻率。
為了進一步找出加工系統的固有頻率, 在主軸轉速、滾刀齒數等因素不變的前提下, 改變進給量, 可以明顯發現, 加工系統在頻率為50718H z處能量幅值明顯增大, 可進一步證明, 該頻率即為加工系統的頻率,試驗結果如圖9所示。
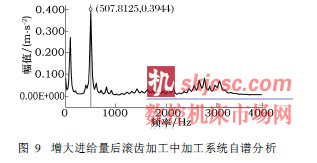
試驗不但證明了該動力學模型的正確性, 而且可以從試驗中發現, 該頻率處于滾刀主軸系統與工件主軸系統的固有頻率中間, 而且該頻率在數值上更接近于工件主軸系統的固有頻率, 因此在低速加工時該零傳動滾齒機容易引起工件主軸的較大振動而影響加工精度。試驗表明, 進一步改善工件主軸系統和滾刀主軸系統都能改善零傳動滾齒機的動態特性, 但是提高工件主軸系統的剛度更有利于改善加工系統的動態特性。
4 改善零傳動滾齒機動態特性的措施
1)芯軸與工件主軸的連接采用螺栓連接, 螺栓的剛度和連接表面的粗糙度直接影響加工系統的剛度, 因此可提高工件主軸和芯軸之間的連接剛度。2)芯軸與頂尖之間的連接也直接影響加工系統的剛度, 為了提高工件的加工精度, 頂尖要稍稍偏向加工敏感方向。3)滾刀芯軸與滾刀主軸的連接和芯軸與工件主軸的連接有相同的要求, 方可提高滾刀系統的剛度。4)滾刀芯軸與尾座的連接也是提高滾刀系統剛度的關鍵因素, 通過增加墊片縮短尾座與主軸之間的距離, 可提高滾刀芯軸的剛度。5)提高工件主軸和滾刀主軸本身的剛度有助于提高滾齒加工的動剛度。如在改變工件主軸軸承的間距或布置方式、在工件主軸上附加慣性阻尼器都有利于提高零傳動滾齒機的剛度, 改善加工系統的動態特性, 提高齒輪加工精度。
5 結語
對機床加工系統中各部件的參數進行合理的定義, 運用這種動力學模型可以很好地預測機床切削力激發出來的頻率成分, 甚至可以預測到動態性能給機床加工精度帶來的影響, 這為加工中主軸轉速的選擇和進給量的選擇提供了參考; 為改善機床結構設計,提高機床加工系統剛度提供了合理的理論基礎; 為進一步研究機床動態特性提供了依據。
如果您有機床行業、企業相關新聞稿件發表,或進行資訊合作,歡迎聯系本網編輯部, 郵箱:skjcsc@vip.sina.com