Cr12Mo V 的電火花線切割加工工藝參數研究
2016-9-12 來源:太原理工大學 作者:啟靜凱 李 文 斌
摘要:隨著人們對工業產品的精度、質量要求越來越高,相關模具的制造精度、表面質量以及模具材料的硬度、耐腐蝕性和耐磨性等也得到不斷提高。Cr12Mo V 滿足了模具材料在硬度、耐磨性、耐腐蝕性方面的要求,作為一種廣泛使用的冷作模具鋼,應用于生產截面面積大、外形復雜的各種冷沖模具。
Cr12Mo V 鋼具有高硬度性能,尤其為提高模具成型精度,經熱處理后的 Cr12Mo V 硬度≥60HRC,利用傳統切削方式很難加工。基于此,利用電火花線切割加工 Cr12Mo V 成為最佳選擇。電火花線切割加工是利用脈沖火花放電蝕除材料,并通過數控系統對工件切割成形,可解決這種模具材料的難加工問題,并能滿足制造精度要求。因此,研究 Cr12Mo V 的電火花線切割加工工藝參數(本文主要以電參數為主,包括脈寬時間、脈間時間、峰值電流以及間隙電壓)對材料去除率和表面粗糙度的影響,以達到對電參數優化選取的目的,從而提高電火花線切割加工 Cr12Mo V 的加工效率和表面質量。
利用單因素試驗法,通過改變電火花線切割機床的電參數,得出各個電參數對電火花線切割加工Cr12Mo V的材料去除率與表面粗糙度的影響規律。在此基礎上,利用有限元分析軟件 ANSYS,依據電火花線切割加工的微觀機理,建立合理的物理模型和數學模型,劃分網格,確定能量在放電通道內分布的形式,施加荷載并求解,得到電火花線切割加工 Cr12Mo V 鋼 的溫度場分布,來預測峰值電流的改變對表面粗糙度的影響。將白層厚度考慮在內并且修正仿真凹坑深度值后,與實際加工的結果進行對比驗證,得出了更為吻合的修正凹坑深度曲線與表面粗糙度曲線,表明可通過ANSYS 仿真電火花加工溫度場進行電參數的合理選擇。
應用正交實驗法,通過合理設置考察因素水平,設計表頭,確定以 L16(45)正交表進行正交試驗,得到試驗結果。對試驗結果分別進行極差分析和方差分析,探索電火花線切割的脈寬時間、脈間時間、峰值電流和間隙電壓對材料去除率和表面粗糙度影響的主次順序和顯著性。以正交試驗結果為基礎應用灰關聯分析法,將材料去除率和表面粗糙度量綱歸一化后進行關聯分析,計算關聯度值,選取關聯值最大的一組電參數為最優參數組合,即:脈寬時間為 10 μs,脈間時間為 20 μs,峰值電流為 2 A,間隙電壓為 3 V,并進行試驗驗證。結果表明,利用經優化后的參數組合切割加工試件,達到了預期的加工效果,解決了參數組合的優化問題。
總之,本文通過一系列試驗和分析方法,研究了電火花線切割加工Cr12Mo V 的電參數的選取和優化問題,為實際生產提供理論指導。
關鍵詞:電火花線切割加工,Cr12Mo V,電參數,材料去除率,表面粗糙度,有限元分析
4、電火花線切割加工 Cr12Mo V 的仿真分析研究
4.1 引言
研究電火花線切割加工Cr12Mo V的加工工藝參數,利用單因素試驗可以很好地得出各個電參數對材料去除率和表面粗糙度的影響,但是這一系列的試驗需要大量的前期準備、試驗過程以及后期數據采集分析,還要耗費一定的人力和物力。因此,科學經濟地提高電火花線切割加工Cr12Mo V模具鋼的加工質量顯得尤為重要。
ANSYS在熱分析方面強大的功能滿足了這一要求,通過仿真模擬電火花線切割加工Cr12Mo V鋼的溫度場分布,來預估電參數的改變對表面粗糙度的影響,由單因素試驗可知,脈寬時間、脈間時間、峰值電流和間隙電壓都對表面粗糙度有影響,如果將這些變量都考慮在內,這樣模型無法建立,不能進行模擬。因此,本研究利用ANSYS仿真模擬是在單脈沖條件下進行的,這樣可以不考慮脈間時間這些因素,其次單脈沖是研究電火花線切割加工的基礎,以此得到其他電參數對整個加工過程的影響。
本章通過仿真模擬電火花線切割加工Cr12Mo V鋼的溫度場分布,來預測峰值電流的改變對表面粗糙度的影響,并將白層厚度考慮在內修正仿真凹坑深度值,與實際加工的結果進行對比驗證,希望得出較為吻合的修正凹坑深度曲線與表面粗糙度曲線,證實利用ANSYS模擬電火花加工溫度場進行電參數的合理選擇,以此改善加工質量的可行性。
4.2 模型的建立
4.2.1 物理模型的建立
本研究的試驗平臺是 FW-1 型高速走絲電火花線切割機床,其采用 Φ0.18 mm 的鉬絲作為電極絲,試驗材料為經過高溫淬火的 Cr12Mo V 鋼。為便于分析所建立的電火花線切割加工物理模型如圖4-1 所示。
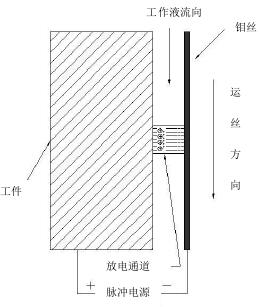
圖 4-1 電火花線切割加工物理模型
1)放電通道的形成
由等離子體組成的放電通道中包括中性離子、原子或分子以及帶正電和帶負電的的正離子和電子。電火花線切割加工過程中,極間施加一個脈沖電壓形成電場。在電場的作用下,處于負極的電極絲逸出電子并且高速向正極運動,與工作液中的分子或原子碰撞,形成帶正電的粒子,導致帶電粒子雪崩式增多,當工件與電極絲之間的脈沖電壓增大到大于工作介質之間的擊穿電壓時,形成放電通道。
2)放電通道半徑
由于現有觀察設備和計量設備的限制,放電通道的半徑很難確定。不少學者對此作了研究,總結得出了一些經驗公式。放電通道的半徑與峰值電流,脈寬時間有關系。
Dibitonto,Eubank[22]等人研究發現,每一個峰值電流,都有一個對應的最佳脈寬時間,他們得到的經驗公式為:
Tb=-0.00002I4+-0.0025I3-0.0122+2.7292+1.2881 (4-1)
式中:Tb—最佳脈寬時間,μs;
I —峰值電流,A。
樓樂明[23]在此基礎上對放電通道進行了研究,并總結出了放電通道半徑的經驗公式:

上海交通大學的薛瑞[24]總結前人研究,認為通道半徑為:

式中:R(t)—通道半徑,m;
I,Tb與(4-1)式相同;
t—時間,s。
通道半徑是隨時間變化而逐漸增大,形狀大致是圓柱體[25]。本研究采用式(4-3)來確定通道半徑。
3)熱源形式
電火花線切割加工蝕除材料的過程是高溫熔化、氣化工件材料的過程,對于這一過程中產生高溫的熱源的形式有兩種:一種是體積熱源,一種是表面熱源。兩種熱源形式的作用效果也是不同的。
體積熱源作用于導電性差的電火花加工或者是放電加工開始階段,此時處于形成電場初期,工作液中所形成的帶電粒子沒有雪崩式增多,電流密度較小,溫度較低,溫度變化發生在工件內部,對于去除材料作用有限。因此,體積熱源對于電火花線切割加工過程作用很小,基本忽略不計。表面熱源作用于電子與工作液碰撞產生電離,造成帶電粒子迅速增多,形成放電通道的過程中。此時由于帶電粒子相互撞擊,產生大量的熱,通道溫度急劇上升。這樣大量的熱傳遞到工件表面,并且向工件內部傳導,達到工件熔點,使得工件熔化,甚至氣化達到蝕除材料的目的。
綜上所述,本次研究的電火花線切割加工 Cr12Mo V 鋼的溫度場分布中熱源形式為表面熱源。體積熱源的作用很小,在模擬仿真的過程中忽略不計。
4.2.2 數學模型的建立
模擬電火花線切割單次脈沖放電加工,這一過程在幾十微秒的時間內即可完成。在幾十微秒內產生大量的熱量并且集中在很小的區域內,所以該過程屬于瞬態非線性傳導問題,對于非線性瞬態分析可得到圓柱坐標系下的傳導方程:

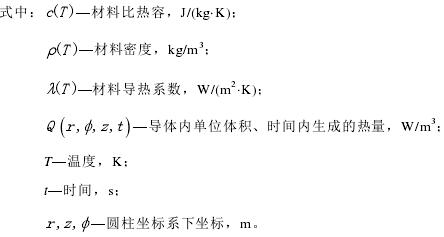
4.3 仿真分析
4.3.1 建模與劃分網格
電火花線切割加工過程是復雜且難以觀察的,模擬電火花線切割蝕除材料比較困難,因此在建立模型時,需要簡化一些次要因素,達到優化并且保證分析正確的目的,故假設下列條件:
1)模型是軸對稱圖形;
2)放電通道是圓柱形的,且映射到工件表面為圓形;
3)忽略熱輻射的作用;
4)忽略焓的作用;
5)熔化材料被全部排出。
通過仿真前的分析可知,電火花放電蝕除材料的范圍很小,一般在幾十微米以內,因此合理的建模很重要。由于分析的模型是軸對稱的,所以建立半徑為 80 μm 的 1/4 圓形。
網格的劃分是 ANSYS 仿真分析過程中占用工作時間最長且最為關鍵的一步,其劃分的好壞對仿真分析結果的正確與否造成直接影響。電火花線切割加工溫度場在很小的范圍內溫度急劇變化,因此在放電點周圍的網格需要劃分的較細。基于對工作效率的考慮,在遠離放電點的區域,其網格相對可以大些[26]。本研究仿真分析劃分網格大小為 5 μm,并且在局部進行細化。圖 4-2 為劃分網格后的二維模型,單元類型采用 4 節點的PLANE55。
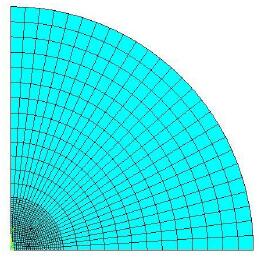
圖 4-2 二維模型與網格劃分
為便于分析,建立圖 4-3 所示的 1/4 三維模型并進行網格劃分,單元類型采用 8 節點的 SOLID70。
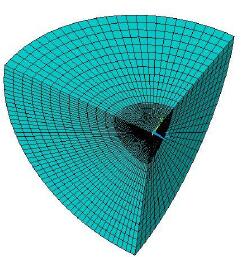
圖 4-3 1/4 三維模型與網格劃分
4.3.2 定義材料屬性
Cr12Mo V 鋼的導熱系數與比熱容是隨溫度變化的。電火花線切割加工過程中溫度急劇變化,最高溫度可達 10000℃,利用 ANSYS 中 Add Temperature 功能將這些離散的參數輸入,系統會自動進行插值。表 4-1 所示為 Cr12Mo V 鋼的物理性能參數。
表 4-1 Cr12Mo V 鋼的熱物理性能參數
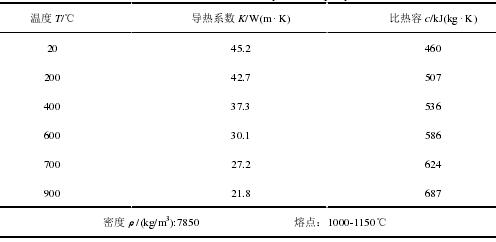
4.3.3 初始條件與邊界條件
1)初始條件
模擬電火花線切割加工 Cr12Mo V 鋼的溫度場是一個瞬態熱分析的過程,它的溫度是隨著時間變化而變化的。由于條件限制,所模擬溫度場是單次脈沖寬度時間內產生的。因此,需要設置的初始條件為 t=0 時的溫度。t=0 是指帶電粒子雪崩式增多,表面熱源作用于工件表面,即將形成放電通道的時刻。所以初始條件即 t=0 時,溫度為室溫T0=20℃。
2)邊界條件
準確模擬電火花線切割加工的溫度場,需明確熱的作用形式。在單次脈沖作用下,放電通道映射到工件表面的圓形區域為熱流密度作用區域,與工作液接觸的表面為熱對流區域,其他表面及內部為熱傳導區域。如圖 4-4 所示。
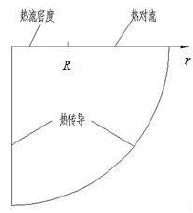
圖 4-4 熱載荷施加示意圖
建立邊界條件的數學模型時,除熱流密度輸入區域與熱對流區域,需假設模型大小為無窮大,因此其他面都為 20℃。其數學模型為:

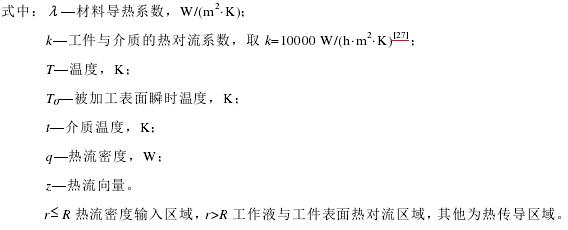
4.3.4 荷載施加
當放電通道形成后,電子與離子碰撞產生高溫。由于圓柱形通道中心處發生的碰撞最多,沿徑向碰撞逐漸減少,因此通道的能量分布與高斯分布相符[28],如圖 4-5 所示。
帶電粒子相互碰撞產生大量的能量,其中有一部分是被工作液帶走或者以熱輻射的形式散失[29],大部分能量以熱能形式分配到正負極上,由于極性效應,正負極所得到的能量分別占到 40%和 20%[30]。
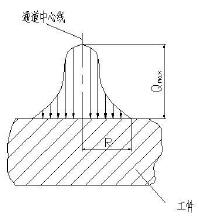
圖 4-5 高斯熱源
ANSYS 中對于熱分析提供下列幾種載荷形式:
1)溫度:是一種自由度約束作用于溫度已知的邊界上。
2)對流:是一種面載荷作用于模型的外表面。
3)熱流密度:是一種面載荷作用于模型的外表面或表面效應單元。
本次研究中分配到正極即工件表面的能量以熱流密度形式輸入,表 4-2 為加工參數,熱流密度的輸入半徑即放電通道半徑值列于表 4-2,它的值隨峰值電流的改變而改變。熱對流與熱傳導區域在圖 4-4 中表示。熱流密度 q 的表達式為:

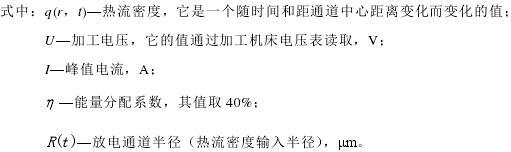
電火花線切割加工時,極間產生的通道的直徑很小,因此為簡化計算,假設通道圓形截面上的能量是均勻的,即熱流密度輸入是均勻的,將(4-6)式簡化后的表達式為:

簡化后的熱流密度是一個關于時間的函數,利用 ANSYS 中的函數編輯器編輯函數并通過加載器施加一個隨時間變化的熱流密度到模型表面。
表 4-2 加工參數
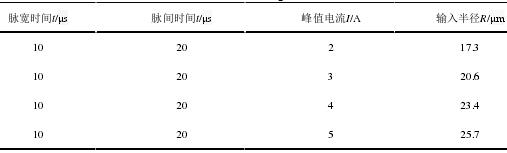
4.4 結果與驗證
4.4.1 求解
保持其他電參數不變,通過改變峰值電流的大小,仿真分析其對表面粗糙度的影響,表 4-2 中為其參數范圍。如圖 4-6 中(a),(b),(c),(d)分別為峰值電流 I=2,3,4,5A 時溫度場的分布云圖。由圖中可知,中心區域的溫度可達近 10000℃,并且隨著峰值電流的增大,中心區域的溫度也不斷增加。Cr12Mo V 鋼的熔點在(1000-1150)℃,在近達 10000℃的高溫下,工件材料迅速熔化氣化,達到蝕除材料的目的。
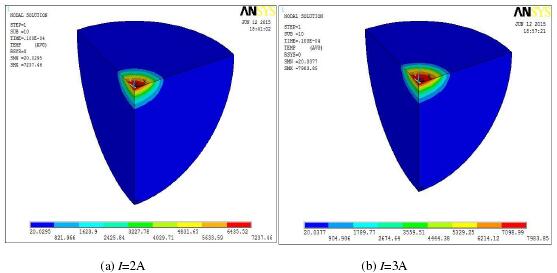
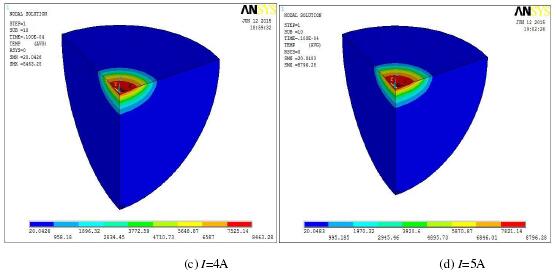
圖 4-6 不同峰值電流下的溫度場分布云圖
單個脈沖能量增大,則材料蝕除率增加,但是表面質量會變差,因此峰值電流的改變必然會影響表面質量。圖 4-7 中(a),(b)),(c),(d)所示為在峰值電流 I=2,3,4,5A 時,溫度沿深度方向變化的曲線。由圖可知沿著遠離熱流密度輸入表面的方向,溫度逐漸降低。由于 Cr12Mo V 鋼的熔點為 1000-1150℃,故將 4 個不同峰值電流情況下,沿深度方向溫度大于 1150℃的長度認為是放電加工完全蝕除工件材料形成凹坑的深度,表 4-3 中為不同峰值電流下得到的凹坑深度值的記錄。
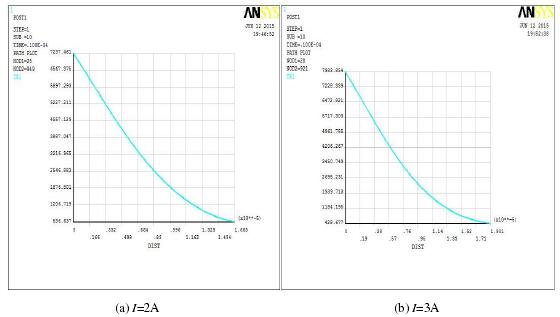
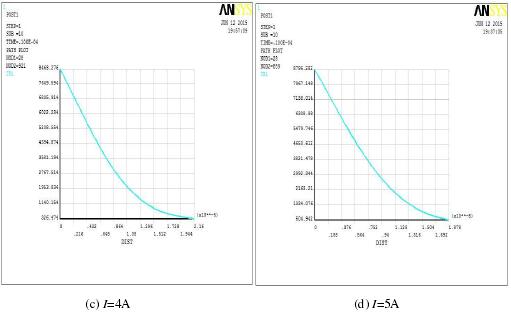
圖 4-7 沿深度方向的溫度分布曲線
表 4-3 凹坑深度
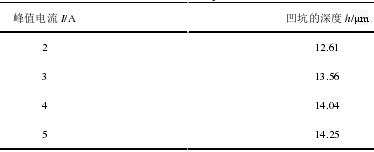
4.4.2 試驗驗證
利用仿真分析的試驗平臺電火花線切割機床,設定與模擬過程中相同的電參數進行加工。將切割得到的試件測量其表面粗糙度值,同樣將不同峰值電流下表面粗糙度的變化趨勢在圖 4-10 中表示,從圖 4-10 可以看出,通過仿真預測的表面粗糙度趨勢與試驗結果相符。但是數值上有一定的偏差,這是由于白層的影響。在放電加工過程中,溫度急劇變化,一部分熔化材料來不及被排出使得冷卻后重新凝結與基體上,這一層也就是白層[31]。關于白層的厚度,它不僅與電參數(峰值電流、脈寬時間),還與走絲速度有關系[32]。利用三維超景深顯微鏡可以觀察到白層在最表層,接下來是熱影響層,還有基體。圖 4-8 為峰值電流 I=4A 時的工件表面形貌,圖 4-9 是峰值電流 I=4A 時工件側面觀察到白層、熱影響層以及基體的分布。
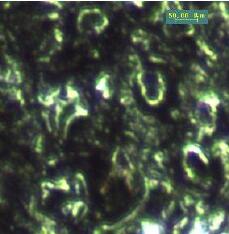
圖 4-8 I=4A 放大 500 倍 Cr12Mo V 試件表面形貌
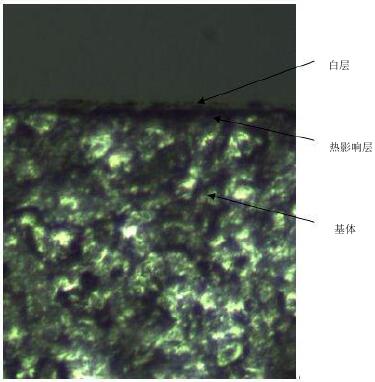
圖 4-9 峰值電流 I=4A 條件下試件結構分布
因此,修正后的凹坑深度應為仿真凹坑深度減去白層的厚度,表 4-4 中所示為利用三維超景深顯微鏡觀察并測量峰值電流 I=2,3,4,5A 時白層的厚度。將得到的修正值的變化趨勢在圖 4-10 中表示出來,從圖 4-10 中可以看出修正后的值與實際表面粗糙度已經很接近了。
表 4-4 白層厚度與修正值
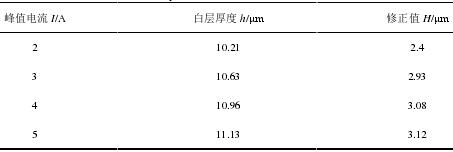
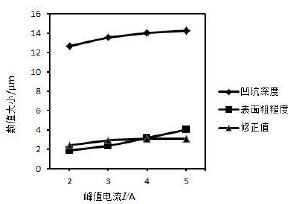
圖 4-10 凹坑深度、表面粗糙度和修正值趨勢圖
4.5 本章小結
本章在單因素試驗的基礎上,通過建模、劃分網格、加載、求解分析,證實了利用ANSYS 仿真分析電火花線切割加工 Cr12Mo V 鋼的溫度場分布能夠很好的預測峰值電流對表面粗糙度的影響。
1)對比高速走絲電火花線切割加工 Cr12Mo V 的過程,建立合理的物理模型,是成功模擬溫度場分布的基礎。
2)科學構建實體模型,考慮到分析效率,劃分網格的過程中,其他區域網格稍微大些,而將放電點周圍網格進行細化。
3)通過分析高速走絲電火花線切割加工 Cr12Mo V 的微觀過程,掌握放電通道的形成過程,能量在放電通道的分布形式,計算得出放電通道半徑,將熱流密度準確加載于工件表面。
4)通過分析產生白層的原因,利用顯微鏡觀察驗證了這一結構的存在。在仿真分析的過程中將白層厚度的影響考慮在內,可以得到更加吻合的曲線。
綜上所述,利用相同的方法也可以研究其他電參數對表面粗糙度的影響,對改善加工和增加經濟效益有重要作用。
投稿箱:
如果您有機床行業、企業相關新聞稿件發表,或進行資訊合作,歡迎聯系本網編輯部, 郵箱:skjcsc@vip.sina.com
如果您有機床行業、企業相關新聞稿件發表,或進行資訊合作,歡迎聯系本網編輯部, 郵箱:skjcsc@vip.sina.com
更多本專題新聞
專題點擊前十
| 更多