航空整體葉輪五軸數(shù)控加工仿真及參數(shù)優(yōu)化研究(上)
2016-11-21 來源:天津職業(yè)技術師范大學 作者:盧輝
摘要
航空整體葉輪的加工手段、加工精度和加工表面質(zhì)量直接影響葉輪的工作性能,對發(fā)動機性能有決定性的影響。作為一種典型的通道類復雜高精度零件,其葉片間流道間距較小,葉片扭曲度大,其幾結構復雜對加工造成很大困難,主要采用五軸數(shù)控機床進行加工。雖然目前進行了針對航空整體葉輪較多的加工仿真及參數(shù)優(yōu)化研究工作,但仍存在如下問題:
(1)在參數(shù)優(yōu)化研究方面,未考慮機床穩(wěn)定性問題,在機床穩(wěn)定的前提下開展加工參數(shù)優(yōu)化研究,才能同時保證五軸加工的效率和質(zhì)量。
(2)由于葉片扭曲大,通常CAM軟件生成的數(shù)控程序只考慮刀具與工件的干涉,未考慮機床主軸與夾具、工作臺的碰撞,不能完全確保刀具軌跡的正確性和機床的安全性,因而需要考慮具體工藝系統(tǒng),進行更全面的幾何仿真研究。針對以上問題,本文的主要研究工作如下:
1.基于VERICUT的航空整體葉輪加工數(shù)控仿真建模。
在VERICUT 環(huán)境下建立虛擬的數(shù)控機床實體、控制系統(tǒng)、刀庫、坐標系統(tǒng)等,創(chuàng)建數(shù)控仿真環(huán)境,實現(xiàn)針對具體工藝系統(tǒng)的幾何仿真,有效避免機床主軸、刀具與工作臺、夾具之間碰撞。
2.提出基于齊次變換的航空整體葉輪數(shù)控程序后處理算法。
首先針對海德漢i TNC530數(shù)控系統(tǒng)的傾斜加工面功能,通過對CLSF刀位軌跡進行齊次變換運算,提出了機床運動坐標的數(shù)控程序后處理算法。使用UG NX8.5/Post Builder編寫后處理文件,通過NC代碼分析、VERICUT仿真驗證后處理方法的正確性。
3.基于Cutpro9.0的工藝系統(tǒng)顫振穩(wěn)定域獲取。
首先采用力傳感器和加速度傳感器,通過錘擊實驗來獲取機床-刀具和機床-工件的頻響函數(shù)。然后采用Cutpro9.0的動力學仿真功能,在給定的徑向切削深度(切寬)條件下,進行顫振穩(wěn)定域仿真,獲得表征主軸轉速和軸向切深關系穩(wěn)定域葉瓣圖。
4.基于幾何仿真和動力學仿真的切削參數(shù)優(yōu)化。
在工藝系統(tǒng)顫振穩(wěn)定域仿真的基礎上,以切削時間為優(yōu)化目標,切削深度、主軸轉速、每齒進給量為實驗因素,設計三因素四水平的正交試驗,通過幾何仿真獲得切削時間。根據(jù)極差分析和方差分析,得出三組較短切削時間的加工參數(shù)。對初步優(yōu)化得到的三組切削參數(shù)進一步進行動力學仿真,根據(jù)仿真結果確定最優(yōu)工藝參數(shù)。
關鍵詞:航空整體葉輪,幾何仿真,動力學仿真,參數(shù)優(yōu)化,正交試驗
第 1 章 緒論
1.1 課題研究背景
航空整體葉輪是典型的通道類復雜零件,其葉片間流道間距較小,葉片扭曲度大,其幾何結構復雜對加工造成很大困難。加工方法、加工精度和加工表面質(zhì)量直接影響葉輪的工作性能,對發(fā)動機性能有決定性的影響。航空整體葉輪因其曲面的復雜性和加工精度高,使其成為典型的難加工零件[1-4]。
目前航空整體葉輪的加工一般采用數(shù)控多軸技術、電解技術、放電技術、鑄造技術等加工方法。鑄造加工整體葉輪的特點是成本較低,適用于大批量的葉輪生產(chǎn)。這種加工方法的不足之處在于會產(chǎn)生內(nèi)部結構缺陷,如砂眼、氣孔等。這可能導致葉片強度差,并最終影響成型零件的工作性能。電火花和電解加工可應用于各種難加工材料,加工穩(wěn)定性高,零件質(zhì)量較好。放電加工的缺點是加工效率低,成本高;而電解加工效率較高,但精度較低。數(shù)控多軸技術可以加工多種類型的葉輪,加工精度高,表面光潔度好,因此航空整體葉輪加工常采用數(shù)控多軸技術[5]。
對于航空鋁整體葉輪來說,使用五軸機床進行高速切削是最佳的加工方法。但當前航空整體葉輪五軸加工過程仍存在很多工藝問題,比如葉輪粗加工效率低,薄壁件加工易出現(xiàn)顫振導致葉片表面光潔度差,切削參數(shù)選取不當導致刀具折斷等。此外,到目前為止,切削參數(shù)的選擇尚未有一個完善的方法理論進行指導,實際生產(chǎn)加工中切削工藝參數(shù)往往取決于工藝人員的經(jīng)驗。對于高速高精加工來說,尤其是葉輪具有復雜曲面薄壁類零件,往往很難獲得預期的加工質(zhì)量。其根本原因在于設定高速切削參數(shù)中沒有考慮機床的動力學特性,沒有考慮刀具振動對工件質(zhì)量的影響,沒有考慮機床各軸的行程極限和加速度方面的差異[6]。
1.2 課題的目的及意義
五軸加工航空整體葉輪過程中,刀軸變化頻繁易發(fā)生碰撞,且葉片厚度薄容易發(fā)生顫振,這些因素制約著航空整體葉輪的高效高精加工。因此,本文通過建立VERICUT仿真環(huán)境檢查刀具軌跡避免機床與刀具發(fā)生碰撞,使用cutpro9.0軟件進行顫振穩(wěn)定域分析和切削過程仿真,預測刀具振動、工件振動、切削力、表面粗糙度、主軸功率等,為合理地選擇加工參數(shù)避免發(fā)生顫振,能夠使五軸機床實現(xiàn)高速高精加工。本文研究內(nèi)容有助于指導葉輪實際加工的切削參數(shù)的選擇,能夠為同類零件的加工提供參考,具有重要的工程應用價值。
1.3 國內(nèi)外研究現(xiàn)狀
1.3.1 高速切削技術研究現(xiàn)狀
20 世紀 30 年代德國 Salomon 博士提出高速切削加工(HSM 或 HSC)概念,隨著切削速度提高到一定峰值后,切削溫度反而下降[7]。此后幾十年高速切削加工的研究處于停滯狀態(tài)。從 1950 年開始世界各國開始對高速切削加工展開大規(guī)模研究,主要是歐美發(fā)達國家、蘇聯(lián)、澳大利亞、日本等國家[8-10]。這一時期稱為高速切削理論研究的探索階段。到了 20 世紀 70 年代,高速切削加工進入應用基礎研究階段。1972 年到 1978 年美國洛克希德導彈與空間公司研究小組主要研究高速加工應用于生產(chǎn)加工的可行性[11]。1980 年代高速切削加工研究開始進入應用研究階段。1979 年美國高級研究工程局開始對高速切削工藝系統(tǒng)做全面的研究,包括高速刀具、高速機床、高速工藝等方面[12]。1984 年至 1988 年德國研究技術部對高速切削金屬和非金屬材料、高速切削電主軸系統(tǒng)等研究,為高速切削技術應用于實際加工打下結實的基礎[13]。進入 20 實際 90 年代后,隨著直線電機,機床電主軸、高速切削刀具的出現(xiàn),高速切削加工機床不斷出現(xiàn)在國際市場,高速切削加工進入到工業(yè)應用階段[14-17]。
相對于國外,國內(nèi)對高速切削研究起步比較晚,從 1980 年國內(nèi)各大研究機構和大學開始對高速切削進行全面研究。1980 年山東大學開始對高速切削中切削溫度、切削力、切屑、刀具壽命等研究[18]。20 世紀 90 年代后,北京理工大學研究了高速切削的刀具與切削力[19],廣東工業(yè)大學研究了高主軸轉速的電主軸技術、直線電動機進給系統(tǒng)[20],天津大學和大連理工大學從切削原理方面入手研究高速切削加工[21]。盡管國內(nèi)的高速切削技術與西方工業(yè)發(fā)達國家還有很大差距,但是經(jīng)過國內(nèi)大學的研究者努力和奮斗,國內(nèi)也出現(xiàn)了一批高速切削機床,如大連機床廠生產(chǎn)的高速加工中心。
高速切削與傳統(tǒng)加工相比具有以下優(yōu)點,1)高速切削主軸轉速高,切削速度快,單位時間內(nèi)去除材料體積增大,縮短切削時間,提高加工效率。2)高速切削時,切削深度小,進給速度快,故其切削力小。3)高速切削時,切屑以很快地速度排除,帶走大部分的熱量,工件熱變形小。4)高速切削中隨著切削速度提高,切削力逐漸減小,而切削力是切削過程中振動的主要來源,因而減少切削振動,提高表面粗糙度。5)高速切削可加工淬硬材料,減少電火花放電加工。正是由于高速切削具有以上特點,高速切削技術廣泛應用于航空航天、汽車、模具等行業(yè),尤其是在航空行業(yè)應用最多。航空制造中大部分是輕合金材料,且大都是薄壁類零件,切削中容易變形。高速切削技術切削速度快,切削力小,特別適用于航空類零件加工。
1.3.2 數(shù)控加工仿真技術研究現(xiàn)狀
用于數(shù)控仿真和切削參數(shù)優(yōu)化方面的系統(tǒng)軟件主要有以下兩類:幾何仿真軟件和動力學仿真軟件,幾何仿真是完成數(shù)控程序的幾何仿真、進行刀具與機床、夾具的碰撞檢查以及對數(shù)控代碼的優(yōu)化。目前,關于數(shù)控加工幾何仿真的研究已經(jīng)很成熟了,并且有很多幾何仿真軟件應用于實際生產(chǎn)中。幾何仿真軟件最具代表性的軟件是CGTEC公司的VERICUT軟件[22]。VERICUT是交互仿真的NC程序數(shù)據(jù)去除材料過程。VERICUT軟件仿真可以替換昂貴的NC數(shù)據(jù)驗證過程,并且可以優(yōu)化材料去除率。VERICUT通過仿真NC程序,可以減少或消除傳統(tǒng)費時費力的數(shù)控程序試切驗證過程。到了90年代很多CAD/CAM集成軟件推出幾何仿真模塊,比如英國的Power MILL,美國的Master CAM, 德國西門子公司的UG NX等軟件。這些CAD/CAM集成軟件只能進行前置代碼仿真,不能進行后置代碼仿真。在國內(nèi),1994年6月哈工大研發(fā)的三維動態(tài)圖形仿真器NCMPS[23]。1994年11月由清華大學和華中科技大學合作研發(fā)的HMPS[24]。北京航空航天大學開發(fā)的集成在CAD/CAM系列軟件中的仿真模塊。
動力學仿真則須通過仿真切削過程中的主軸功率、切削力等預測加工精度和加工表面質(zhì)量,為調(diào)整和優(yōu)化切削參數(shù)提供依據(jù),最終達到優(yōu)化結果。隨著計算機仿真技術的發(fā)展和對切削原理的研究越來越深入,目前以優(yōu)化切削參數(shù)為目的動力學仿真系統(tǒng)研究進展也很快。國外有加拿大UBC大學MAL實驗室[25]開發(fā)的Cutpro9.0、英國的Meltal Max,其中Cutpro9.0軟件可以利用虛擬現(xiàn)實和仿真技術對高速加工過程中的切削力、功率、扭矩、切屑厚度、振動情況等進行預測,以確定無顫振條件下的主軸轉速、進給量和切深,在保證良好表面質(zhì)量的前提下提高材料的去除速率。這些軟件已在包括波音、加普惠等數(shù)十加跨國公司得到了廣泛的應用,并取得了很好的效果。國內(nèi)目前主要有北航自主開發(fā)的銑削加工動力學仿真系統(tǒng)Simu Cut和數(shù)控機床動力學特性參數(shù)測試與分析Dyna Cut系統(tǒng)。該系統(tǒng)功能與Cutpro9.0基本類似,且已在國內(nèi)軍工口幾十家企業(yè)得到初步應用,不足之處是目前僅限于銑削加工仿真[26-27]。
1.3.3 切削顫振研究現(xiàn)狀
切削過程由于主軸的旋轉運動和刀具切削工件產(chǎn)生的切削力不可避免會出現(xiàn)振動情況。尤其是當切削參數(shù)選取不當或切削量過大時,刀具的振動會更加激烈。切削過程中產(chǎn)生的振動,會影響加工質(zhì)量和生產(chǎn)效率,嚴重時甚至會導致刀具斷裂,因此通常都是對切削加工不利的。切削振動主要表現(xiàn)在影響加工的表面光潔度、切削效率、刀具壽命、機床精度。多年來,國內(nèi)外很多研究者對切削振動進行深入的研究,取得了可喜的成效。
在國外,Tobias[28]和Tlusy[29]通過對切削過程中的顫振現(xiàn)象的研究,提出了有關于主軸轉速和切削深度的穩(wěn)定臨界切削深度表達式,并對銑削穩(wěn)定性進行了時域分析。Y.Altintas[30]通過切削過程仿真建立動態(tài)銑削力的模型,提出了球頭銑刀進行穩(wěn)定切削的方法,從而得到了切削深度與主軸轉速的顫振穩(wěn)定分析解。該方法僅需要獲取整個工藝系統(tǒng)的傳遞函數(shù)(FRF),切削力系數(shù),徑向切深及統(tǒng)刀齒數(shù),通過較少量的計算得到較精確的穩(wěn)定性曲線。由于該方法對方向系數(shù)做傅里葉變換后僅取零次諧波分量,因此該方法被稱為零階求解方法(Zero Oder solution, ZOA)。Sata T等[31]在機床-刀具和機床-工件等動力學模態(tài)參數(shù)對切削穩(wěn)定性影響分析的基礎上,給出了切削速度、每齒進給量和刀軸切削角度的控制策略,得出了一種預測和控制顫振的方法。Gagnol等[32]通過采用與速度無關的頻響函數(shù)來實現(xiàn)顫振穩(wěn)定域預測,提出的顫振穩(wěn)定域預測模型中考慮了主軸轉速對刀尖點頻響函數(shù)的影響。
在國內(nèi),師漢民等人[33-35]提出切削中發(fā)生顫振時,振幅大到一定值之后趨于穩(wěn)定,這是因為切削用量有限,當?shù)毒哒穹容^大時刀具有一部分已經(jīng)脫離工件不參與切削。機床顫振振幅穩(wěn)定模型主要受到兩個非線性因素影響,第一刀具切削中脫離工件不參與切削,第二切削力的非線性特性。熊國良等[36]采用廣義傅里葉級數(shù)法分析圓柱立銑刀的顫振問題,研究了主軸的陀螺效應對工藝系統(tǒng)穩(wěn)定性的影響。石莉等[37]采用小波分析法對切削力信號進行分析,根據(jù)切削力的波動來預測切削顫振,得到產(chǎn)生顫振的切削力信號范圍,從而給避免顫振提供一個參考。劉安民等[38]通過分析加工噪音來判斷是否發(fā)生顫振,從分析顫振噪音中得到顫振頻率,從而不需要測量機床-工件和機床-刀具的傳遞函數(shù),就可以建立動態(tài)切削力模型,得到主軸轉速和切削深度的穩(wěn)定曲線。
1.3.4 切削參數(shù)優(yōu)化研究現(xiàn)狀
在國內(nèi),閆國琛[39]對S50C模具鋼高速切削加工進行工藝參數(shù)優(yōu)化研究,采用正交試驗得出模具鋼表面粗糙度影響因素的規(guī)律情況,并基于BP 神經(jīng)網(wǎng)絡和遺傳算法進行工藝參數(shù)優(yōu)化。陳展翼[40]通過高速銑削試驗對鈦合金TC4材料進行正交試驗得到切削參數(shù)對表面粗糙度的影響規(guī)律,并利用遺傳優(yōu)化算法實現(xiàn)了銑削加工參數(shù)優(yōu)化。黃豪[41]基于不同切削方式的切削原理是相同的理論,針對不同的切削方式建立統(tǒng)一的數(shù)學模型,在遺傳算法中加入模擬退火算法算子,提出混合遺傳算法并對其進行測試和驗證。莊光法[42]對油管接箍內(nèi)壁的車削加工中易發(fā)生變形超差,加工效率低下等問題,采用Deform軟件和正交試驗進行切削力預測得出切削因素對切削力影響的主次因素,并基于粒子群算法以最小圓度誤差和最大生產(chǎn)率為目標進行切削參數(shù)優(yōu)化。
在國外,H. Kurtaran[43]通過耦合響應曲面法(RSM)與開發(fā)的遺傳算法(GA)以最小表面粗糙度為優(yōu)化目標進行切削參數(shù)的優(yōu)化。首先使用RSM建立表面粗糙度值的數(shù)學模型,再通過遺傳算法進一步優(yōu)化切削參數(shù),最終得到最佳切削參數(shù)。Franci Cus[44]基于神經(jīng)網(wǎng)絡對切削參數(shù)進行多目標進行優(yōu)化,通過充分考慮技術、經(jīng)濟等因素多目標優(yōu)化。為了達到更精確的預測結果,該神經(jīng)網(wǎng)絡優(yōu)化算法能夠?qū)崿F(xiàn)對重要的切削參數(shù)簡單、快速和高效的優(yōu)化。該方法適用于快速確定最佳切削參數(shù)的加工。Petropoulos[45]等提出使用幾何規(guī)劃方法進行數(shù)控車切削參數(shù)優(yōu)化,該優(yōu)化方法綜合考慮機床的最大主軸功率和切削速度等因素,以最小生產(chǎn)成本為優(yōu)化目標。但該模型約束條件多,計算量大,效率低下。Eskicioglu和Jha考慮了這個問題[46],提出了基于幾何規(guī)劃法和拉格朗日乘數(shù)法的算法,以減少約束數(shù)目,減少運算量。1.4 本文主要研究內(nèi)容 航空整體葉輪的加工手段、加工精度和加工表面質(zhì)量直接影響葉輪的工作性能,對發(fā)動機性能有決定性的影響。作為一種典型的通道類復雜高精度零件,其葉片間流道間距較小,葉片扭曲度大,其幾何結構復雜對加工造成很大困難,主要采用五軸數(shù)控機床進行加工。雖然目前進行了針對航空整體葉輪較多的加工仿真及參數(shù)優(yōu)化研究工作,但仍存在如下問題:(1)在參數(shù)優(yōu)化研究方面,未考慮機床穩(wěn)定性問題,在機床穩(wěn)定的前提下開展加工參數(shù)優(yōu)化研究,才能同時保證五軸加工的效率和質(zhì)量。(2)由于葉片扭曲大,通常CAM軟件生成的數(shù)控程序只考慮刀具與工件的干涉,未考慮機床主軸與夾具、工作臺的碰撞,不能完全確保刀具軌跡的正確性和機床的安全性,因而需要考慮具體工藝系統(tǒng),進行更全面的幾何仿真研究。針對以上問題,本文的主要研究工作如下:
1.基于VERICUT的航空整體葉輪加工數(shù)控仿真建模。在 VERICUT 環(huán)境下建立虛擬的數(shù)控機床實體、控制系統(tǒng)、刀庫、坐標系統(tǒng)等,創(chuàng)建數(shù)控仿真環(huán)境,實現(xiàn)針對具體工藝系統(tǒng)的幾何仿真,有效避免機床主軸、刀具與工作臺、夾具之間碰撞。
2.提出基于齊次變換的航空整體葉輪數(shù)控程序后處理算法。首先針對海德漢i TNC530數(shù)控系統(tǒng)的傾斜加工面功能,通過對CLSF刀位軌跡進行齊次變換運算,提出了機床運動坐標的數(shù)控程序后處理算法。使用UG NX8.5/Post Builder編寫后處理文件,通過NC代碼分析、VERICUT仿真驗證后處理方法的正確性。
3.基于Cutpro9.0的工藝系統(tǒng)顫振穩(wěn)定域獲取。首先采用力傳感器和加速度傳感器,通過錘擊實驗來獲取機床-刀具和機床-工件的頻響函數(shù)。然后采用Cutpro9.0的動力學仿真功能,在給定的徑向切削深度(切寬)條件下,進行顫振穩(wěn)定域仿真,獲得表征主軸轉速和軸向切深關系穩(wěn)定域葉瓣圖。
4.基于幾何仿真和動力學仿真的切削參數(shù)優(yōu)化。在工藝系統(tǒng)顫振穩(wěn)定域仿真的基礎上,以切削時間為優(yōu)化目標,切削深度、主軸轉速、每齒進給量為實驗因素,設計三因素四水平的正交試驗,通過幾何仿真獲得切削時間。根據(jù)極差分析和方差分析,得出三組較短切削時間的加工參數(shù)。對初步優(yōu)化得到的三組切削參數(shù)進一步進行動力學仿真,根據(jù)仿真結果確定最優(yōu)工藝參數(shù)。
第 2 章 葉輪五軸數(shù)控加工幾何仿真
2.1 概述
由于航空整體葉輪五軸加工過程中刀軸變化頻繁,容易產(chǎn)生刀具干涉或過切現(xiàn)象。隨著主軸的擺動或工作臺的旋轉,如果考慮不周全,主軸與工作臺或主軸與夾具之間極易發(fā)生碰撞。為了解決這一問題,本節(jié)在VERICUT 環(huán)境下建立虛擬的數(shù)控機床實體、控制系統(tǒng)、刀庫、坐標系統(tǒng)等,創(chuàng)建數(shù)控仿真環(huán)境,實現(xiàn)針對具體工藝系統(tǒng)的幾何仿真,有效避免機床主軸、刀具與工作臺、夾具之間碰撞考慮機床刀具與夾具、工件之間的碰撞,檢查過切現(xiàn)象。
2.2 VERICUT軟件簡介
2.2.1 VERICUT簡介
美國CGTEC公司的VERICUT軟件是最具代表性的幾何仿真軟件。其主要功能是完成數(shù)控程序的幾何仿真、進行刀具與機床、夾具的碰撞檢查以及對數(shù)控代碼的優(yōu)化。VERICUT可以與世界上主流的CAM軟件進行對接,主要解決模型轉換、NC程序傳輸?shù)葐栴},提高加工過程仿真的效率。隨著數(shù)控技術在實際生產(chǎn)應用越來越多,VERICUT軟件也得到了廣泛應用。目前,國外很多大的航空公司汽車公司比如加拿大的龐巴迪公司、德國的大眾汽車公司、美國的波音公司等都已經(jīng)把VERICUT軟件應用到生產(chǎn)實踐中,在國內(nèi)使用VERICUT的公司有青島海爾股份有限公司、天津汽車模具股份有限公司、沈陽飛機制造公司[47]。
VERICUT是交互仿真的NC程序數(shù)據(jù)去除材料過程。VERICUT軟件仿真可以替換昂貴的NC數(shù)據(jù)驗證過程,并且可以優(yōu)化材料去除率。VERICUT通過仿真NC程序,可以減少或消除傳統(tǒng)費時費力的數(shù)控程序試切驗證過程。它還可以優(yōu)化程序中進給速度和主軸轉速提高加工效率。這些能夠為企業(yè)以較低的成本進行生產(chǎn),創(chuàng)造更高的利潤。VERICUT能夠核實NC程序的準確性,能夠確保加工完成的產(chǎn)品與設計的產(chǎn)品相匹配[48]。
2.2.2 VERICUT系統(tǒng)功能模塊
1.驗證與仿真模塊
VERICUT模擬仿真可以進行5軸銑削,鉆孔和線切割,以及車銑復合等仿真。類似加工零件的要求,VERICUT仿真也需要NC程序數(shù)據(jù),毛坯模型,以及加工中所需的刀具模型。VERICUT幾乎可以仿真任何格式的數(shù)控程序,比如G、M代碼數(shù)據(jù)以及APT文件。驗證處理的結果是加工完成的實體模型和錯誤信息報告的日志文件。仿真結果得到實體模型可以進行檢測,查看零件的過切或欠切情況,還可以保存用作另一個NC程序的毛坯模型。日志文件記錄著在模擬過程中任何加工誤差和錯誤。VERICUT驗證模塊可以簡化傳統(tǒng)的試切驗證過程,減少產(chǎn)品的生產(chǎn)周期,提高生產(chǎn)率。
2. 數(shù)控程序優(yōu)化
VERICUT優(yōu)化模塊有自動和用戶自動義兩種方式,可以最大限度地提高材料去除率。VERICUT有恒定體積去除率和恒定切削厚度這兩種優(yōu)化方法。恒定體積去除率的原理是通過設定一個切削體積(Vol)來調(diào)節(jié)進給速度,

,其中ap為切削深度,ae為切削寬度,F(xiàn)為進給速度。當切削體積為零時,說明機床正在空走刀,沒有切削工件,這樣可以適當提高切削速度;當切削體積大于優(yōu)化庫中設定的值時,適當減少切削速度;當切削體積小于優(yōu)化庫中的值時,增加切削速度。恒定切削厚度的優(yōu)化原理為通過變化進給速度來保持恒定的切削厚度,這種方法主要用于精加工。
2.2.3 VERICUT機床加工仿真過程
要在 VERICUT 中實現(xiàn)加工仿真,首先需要建立虛擬機床,選擇控制系統(tǒng),建立加工中所需的毛坯和加工刀具,然后輸入 NC 數(shù)控程序,設置工件坐標系,開始仿真。仿真結束后,對仿真結果進行分析。仿真操作流程如圖 2-1 所示。
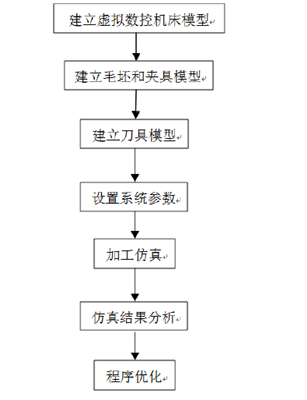
圖 2-1仿真操作流程圖
1.建立虛擬數(shù)控機床模型
VERICUT軟件中機床模型庫中有許多常見的機床模型,包括了數(shù)控車床,三軸加工中心,五軸機床,電火花機床等。如果機床模型庫中,沒有所需的機床模型。可以通過三維建模軟件或VERICUT軟件進行建立機床模型,再通過VERICUT定義其機床的運動關系,這樣就可以建立自己所需的機床。
2.建立毛坯和夾具模型
通過測量實際毛坯和夾具建立三維模型,導入到VERICUT軟件中。建立夾具模型主要是檢查機床刀具或主軸與夾具的碰撞情況。毛坯模型是VERICUT軟件進行加工仿真的必備條件。
3.建立刀具模型
VERICUT仿真與實際加工一樣也是需要刀具的。VERICUT軟件中有建立刀具和刀柄的專用模塊。
4.設置系統(tǒng)參數(shù)
在進行切削仿真之前,還需要設置一些系統(tǒng)參數(shù),如工件坐標系,刀具換刀位置等。
5.加工仿真
建立完機床模型、夾具模型、刀具模型等,就可以導入NC數(shù)控程序進行加工仿真。
6.仿真結果分析
對于仿真結果,可以通過自動對比分析毛坯模型與設計模型的差值,從而得到過切與欠切的情況。還可以通過查看仿真日志文件,檢查切削過程中機床與工件之間發(fā)生的碰撞情況。通過分析仿真結果對數(shù)控程序或裝夾方案進行修改,以達到無錯誤的仿真結果。
7.程序優(yōu)化
通過分析仿真結果,得到無碰撞無過切的數(shù)控程序后,使用VERICUT優(yōu)化模塊進行切削速度的優(yōu)化,提高加工效率。VERICUT優(yōu)化不會改變數(shù)控程序原有的刀具軌跡,只會改變進給速度和主軸轉速。
2.3 建立VERICUT虛擬數(shù)控仿真環(huán)境
2.3.1 VERICUT虛擬機床的建立
VERICUT虛擬機床的建立過程就是對實際機床進行測量在三維軟件中建立機床各部件的模型,導入到VERICUT軟件中按照實際運動邏輯關系進行“裝配”。VERICUT構建機床流程:第一建立機床各部件間運動關系;第二建立機床組件模型;第三設定機床相關參數(shù)。
本文選用的是DMG公司的HSC75 linear五軸高速加工中心,控制系統(tǒng)是海德漢i TNC530。該五軸機床屬于刀具擺動與工作臺回轉類型,如圖2-2所示。其機床主要參數(shù)如表2-1 所示。
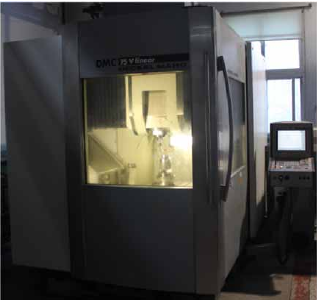
圖 2-2 德瑪吉 HSC75 機床
表 2-1 德瑪吉 HSC75 機床主要參數(shù)
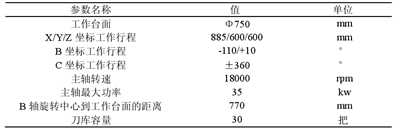
建立虛擬機床模型必須要了解機床各部件間的運動關系以及它們的依附關系,再將機床進行運動分解。通過分析機床的結構可知HSC75有兩大運動鏈,主軸運動鏈和毛坯運動鏈。主軸運動鏈:Y軸依附于Base(床身),Y軸運動不影響B(tài)ase的狀態(tài)和位置變化;Z軸依附于Y軸,并會隨著Y軸的移動而改變位置;B軸依附于Z軸,并會隨著Z軸的移動而改變位置;主軸依附于B軸,并會隨著B軸的移動而改變位置;刀具依附于主軸,并會隨著主軸的移動而改變位置。即Base→Y→Z→B→Spindle→Tool。毛坯運動鏈:X軸依附于Base,X軸運動不影響B(tài)ase的狀態(tài)和位置變化;C軸依附于X軸,并會隨著X軸的移動而改變位置;夾具依附于C軸,并會隨著C軸的移動而改變位置;毛坯依附于夾具,并會隨著夾具的移動而改變位置。即Base→X→C→Fixture→Stock。建立的機床組件樹如圖2-3所示。
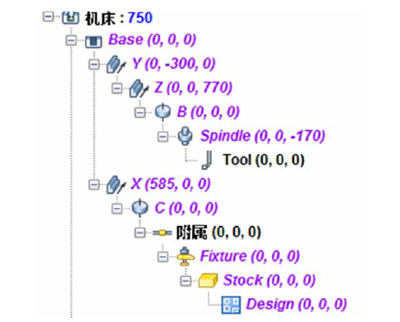
圖 2-3 HSC75 機床組件樹
建立完機床組件樹后,下面就需要添加機床各部件的3D模型。為了建模方便,本文將在UG軟件中建立機床各部件的三維模型,然后導出STL格式的機床模型文件,添加到VERICUT中。在UG中建立機床模型的坐標系要和VERICUT中的機床坐標系一致,建立各個軸的模型時,須按照機床位于零點位置時各坐標軸的位置及狀態(tài)來建模,這樣能有效減少后續(xù)機床調(diào)試難度和時間。由于HSC75五軸機床的B軸旋轉是機床主軸擺動,因此機床主軸在擺動過程中很容易與工作臺、夾具等發(fā)生碰撞。這就要求機床各運動軸的位置關系一定要與實際位置相一致。而其他機床部件比如機床面板、機床外殼等可以進行簡化建模或者不需要建模,這樣可以減輕工作量提高VERICUT仿真速度。 導入機床部件模型文件后,還需要進行機床參數(shù)的設定,如機床機械原點、機床換刀位置、機床各軸行程范圍等。打開“配置”——“機床設定”,按順序進行設定碰撞檢測、表、行程極限、軸優(yōu)先、子程序、機床備忘錄等參數(shù)。通過以上設置,就完成HSC75機床仿真模型建立如圖2-4所示。
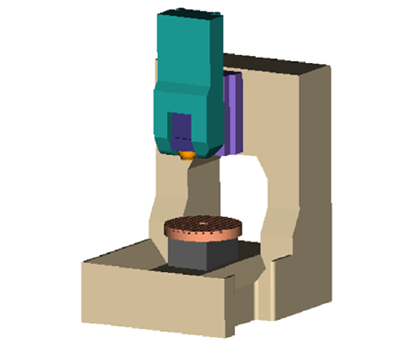
圖 2-4 HSC75 機床仿真模型
2.3.2 VERICUT虛擬刀具庫的建立
VERICUT軟件中有專用于建立刀具和刀柄的模塊,可以建立與生產(chǎn)加工一致的刀具和刀柄文件,如可以建立立銑刀、球頭銑刀、盤銑刀、鉆頭等。選擇“項目”→“刀具”命令,系統(tǒng)彈出圖2-5所示的“刀具管理器”對話框。該對話框主要有4部分顯示區(qū)域:刀具號、刀具參數(shù)區(qū)、圖形顯示區(qū)和信息提示區(qū),每個不同的區(qū)域可相互作用。
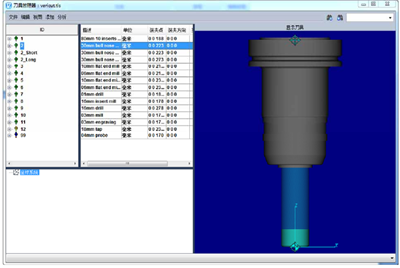
圖 2-5 刀具管理器對話框
在VERICUT系統(tǒng)中的“刀具管理”對話框中,用戶可以根據(jù)具體應用場合定義不同的刀具類型,包括銑刀、車刀、鏜刀、探針、線切割刀具共5種類型。本文研究用到的刀具都是銑刀,按形狀可分為平底銑刀、面銑刀、球頭銑刀、牛鼻銑刀和鉆削銑刀。
在圖2-5所示的“刀具管理器”對話框中選擇“添加”→“新”→“銑削”命令,系統(tǒng)將彈出圖2-6所示的對話框。在“組件類型”下拉列表框中選擇不同的選項,對話框中需設置的內(nèi)容也不一樣。當“組件類型”下拉列表框中選擇“旋轉型刀具”時,可創(chuàng)建平頭銑刀或球頭銑刀等,按要求輸入刀具切削刃結構尺寸即可。通過這種方法,創(chuàng)建本文研究所需的刀具。
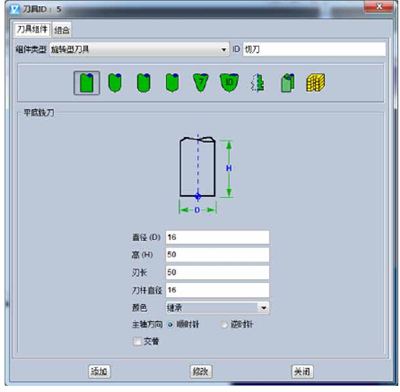
圖 2-6 旋轉型刀具對話框
2.3.3 VERICUT其他參數(shù)的設定
建立完機床和刀具庫后,需要設定數(shù)控程序加工基準,也就是實際加工中所說的對刀。VERICUT提供的對刀方式有“基于工作偏置”、“機床零點”、“工作偏置”、“程序零點”、“輸入程序零點”、“RTCP旋轉點偏置”及“RPCP旋轉點偏置”。本文使用程序零點對刀,打開G代碼偏置對話框如圖2-7所示。一般情況下主軸上不帶旋轉軸的機床對刀時,選擇Spindle組件,如果主軸上有旋轉軸,選擇主軸上的旋轉軸來對刀,主軸上有兩個或兩個以上的旋轉軸,選擇主軸分支上線性軸下連續(xù)的旋轉軸對刀。
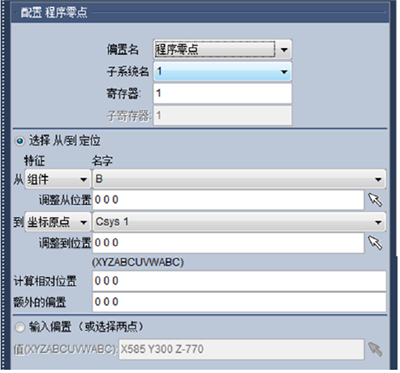
圖 2-7 G 代碼偏置對話框
2.3.4 VERICUT虛擬仿真環(huán)境驗證
構建好了機床模型后,下面添加已經(jīng)實際驗證過無碰撞的數(shù)控程序來進行數(shù)控加工仿真,驗證HSC75虛擬機床的正確性。操作步驟如下:
(1)右擊項目樹中“控制”→“打開”→“hei530.ctl”,加載hei530.ctl控制文件。
(2)在組件模型樹中添加已經(jīng)創(chuàng)建好的夾具和毛坯模型文件。
(3)設置加工坐標系,右擊“坐標系統(tǒng)”→“添加新的坐標系”,創(chuàng)建一個Csys 1的坐標系,然后將坐標系移動到毛坯上表面的中心,使Csys 1與編程加工坐標系重合。
(4)設置G—代碼偏置,在偏置名中選擇“程序零點”,子系統(tǒng)名為“1”,點擊添加。選擇“從”特征為“組件”,名字為“B”,選擇“到”特征為“組件”,名字為“Csys 1”。
(5)加載之前所創(chuàng)建的刀具庫
(6)添加數(shù)控程序
(7)在VERICUT主窗口中,點擊右下角的“重置模型”按鈕,再點擊“仿真到末端”,開始數(shù)控加工過程仿真,仿真結果和自動-比較報告如圖2-8所示。
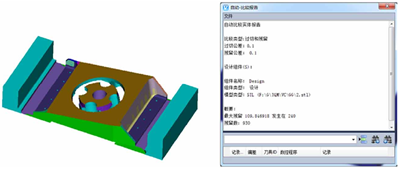
圖 2-8 仿真結果和自動-比較報告
仿真結果圖沒有顯示紅色區(qū)域,說明刀具沒有與夾具、工作臺等發(fā)生碰撞;自動—比較分析報告只顯示最大殘留部分,無過切信息,說明工件無過切現(xiàn)象。這就驗證了數(shù)控仿真環(huán)境 HSC75 虛擬機床的正確性。
2.4 本章小結
本章節(jié)中,在 VERICUT 建立虛擬的數(shù)控機床實體、控制系統(tǒng)、刀庫、坐標系統(tǒng)等,創(chuàng)建一個數(shù)控仿真環(huán)境,檢驗機床各部件之間、刀具與夾具之間及刀具與毛坯之間的干涉和碰撞,為后續(xù)檢查葉輪加工干涉做準備。同時,總結出幾點利用VERICUT軟件進行虛擬數(shù)控機床建模的關鍵技術。第一,根據(jù)實際數(shù)控機床各個運動坐標軸和主要部件的運動邏輯關系來建立正確的機床運動組件拓撲關系;第二,在UG中創(chuàng)建機床三維模型,需要注意建模坐標系與VERICUT中的機床坐標系相重合,方便后續(xù)裝配機床;第三,設置G—代碼偏置時需要考慮機床的結構,不同的機床結構對應不同的G—代碼偏置。
投稿箱:
如果您有機床行業(yè)、企業(yè)相關新聞稿件發(fā)表,或進行資訊合作,歡迎聯(lián)系本網(wǎng)編輯部, 郵箱:skjcsc@vip.sina.com
如果您有機床行業(yè)、企業(yè)相關新聞稿件發(fā)表,或進行資訊合作,歡迎聯(lián)系本網(wǎng)編輯部, 郵箱:skjcsc@vip.sina.com
更多本專題新聞
專題點擊前十
| 更多