基于SYNTEC的螺旋錐齒輪加工機床數控系統開發(上)
2017-1-3 來源:沈陽工業大學 作者:張西棟
摘要
SYNTEC-10B 數控系統是臺灣新代科技股份有限公司研發的一款具有較高性價比的產品,該數控系統具有很好的開放性,是數控系統二次開發的良好平臺。弧齒錐齒輪數控加工涉及到的參數較多,齒輪規格調整后需要重新編制加工程序,而且數控編程不直觀,人機交互性差。為了解決不同弧齒錐齒輪加工的數控編程的繁瑣性問題,提高加工效率,利用 e HMI 軟件對 SYNTEC-10B 數控系統的人機交互界面進行了客制,使其能夠通過屏幕界面直接輸入弧齒錐齒輪的基本參數的形式,即可生成相應的數控加工程序,完成自動化加工。
對螺旋錐齒輪的嚙合原理以及加工過程進行了分析,對相對微分法、嚙合方程的確定、等距共軛原理以及第二共軛曲面的確定等內容進行了描述。分析了螺旋錐齒輪的加工原理和方法、局部共軛原理及齒面數學模型的建立,為后續界面的開發提供了理論基礎。
利用 e HMI 軟件對弧齒錐齒輪加工過程中參數輸入、模擬仿真等相關界面進行了客制與設計。搭建了客制化界面系統的整體框架圖以及弧齒錐齒輪加工系統的人機界面的工作流程圖。通過建立專案,添加相關畫面檔與功能鍵的形式對整個人機界面進行了客制。設計制作了齒制選擇、加工參數輸入、刀具參數輸入等主要畫面檔,將齒輪加工所需要的各種參數信息通過不同組件的形式添加在畫面檔上,使相關的參數輸入界面簡潔明了,便于機床操作者進行相關的數控編程。
為了配合畫面檔的切換、參數輸入等動作,相應地客制設計了與各級畫面檔相對應的功能鍵。通過測試仿真模塊,對開發的多窗體界面中的各級畫面檔與功能鍵相關客制工作進行了仿真檢測,確保了各種參數的正確性。通過整個分析設計過程,最終達到參數的輸入、加工代碼的生成、加工仿真程序的運行整個過程的人性化和快速化。
構建了人機界面的各層級關系框圖,使界面之間的層級關系一目了然;按照操作習慣對數控系統軸群顯示界面進行了設置。基于客制的要求,通過搭建架構圖的形式對客制過程中的新代數控系統內裝型 PLC 進行了總結。將 R 寄存器中允許操作者讀寫的地址分配給客制過程中的各輸入變量,最后將客制的專案進行了軟件封裝。
關鍵詞:新代數控系統,螺旋錐齒輪,畫面檔,測試仿真
第 1 章 緒論
1.1 課題來源及研究背景
1.1.1 課題來源
基于課題組的科研項目《大型螺旋錐齒輪專用數控機床的開發》,提出了本課題。該科研項目是沈陽市科技創新專項資金—工業科技攻關專項(F15040200)支持的項目。項目中的數控機床采用的是臺灣新代科技有限公司開發的,具有較高性價比的SYNTEC-10B 數控系統;該系統操作簡單,開放性較好,能夠滿足弧齒螺旋錐齒輪加工的基本要求。為了提高數控系統的人機交互性,適應不同生產批次的零部件加工要求,滿足數控機床普通操作者的操作要求,對 SYNTEC 數控系統人機界面進行專用化地客制。
1.1.2 課題研究背景
計算機作為 20 世紀人類最偉大的科技發明,推動了整個社會的變革。計算機技術以及相關的控制技術在機械制造領域中的應用促使制造行業生產形態發生了重大轉變。1952 年美國推出了世界上第 1 臺數控銑床,至今已經過了 60 多個年頭,在這段時間里,車床、磨床、銑床、沖壓床、電加工機床、鏜床、加工中心以及各類專用機床慢慢發展起來,逐漸形成一個完備的數控機床家族體系。數控系統經過半個多世紀的發展,先后經歷了硬件數控和軟件數控兩個發展階段[1] 。
1952 年發展起來的電子管類數控系統開啟了硬件數控系統階段,該類數控系統是這一階段的第 1 代。由于硬件的限制,早期計算機運行速度較低,不能滿足數控加工實時控制的要求,為此,技術人員將數字邏輯電路嵌入到一臺專用計算機中,組成數控裝置,這種數控裝置即為硬件連接數控,簡稱數控(NC)。 1961 年以晶體管分離組件為基礎發展起來的數控系統取代了以笨重的電子管為組件搭建的數控系統,這使得數控系統的體積得到縮小,促使其在工業生成中的廣泛應用,這就是第 2 代數控系統。 1965 年發展起來一種功耗低,體積更小的集成電路構成的 NC 系統,該型 NC
系統的可靠性更高,數控系統進入第 3 代。
軟件數控階段是以 1970 年小型計算機的應用為標志。同時,數控系統的發展進入到第 4 代,軟件慢慢取代硬件來完成更多的功能,“軟連接”數控時代開始引領數控加工的行業發展。
1974 年采用微處理器芯片的 CNC 系統開始投入使用,數控系統進入了以微機為背景的時代,同時數控系統進入到第 5 代階段。微處理器型的 CNC 系統實現了機電一體化,這大大降低了制造成本,縮小數控系統的體積,提高了數控系統的普及程度。
1990 年發展起來的基于個人 PC 機的數控系統是第 6 代(PC-Based)。這一代是以大容量存儲器、大規模集成電路、CRT 應用為標志。第 6代數控系統具備更完善的控制功能,具有實時精度補償、三維圖形顯示校驗、交互式編程等軟件技術。同時這一代數控系統具有了模塊化、柔性化、系列化、標準化的雛形。
第 6 代數控系統已經具有了明顯的優點。利用 PC 平臺的優勢,數控系統的技術進步以及更新升級都比較快捷。第 6 代數控系統具有較高的元器件集成度,可靠性高,性能更加優越,而且第 6 代數控系統提供了開放式的開發平臺,這更有利于軟硬件資源優勢的發揮,拓寬了數控系統的應用領域。
1958 年由北京機床研究所和清華大學研制的第一代電子管 101 數控機床標志著我國數控機床進入第一代階段,開啟了我國數控系統研制的歷史序幕[2],我國數控系統發展歷史如表 1.1 所示。
表 1.1 數控系統發展歷史
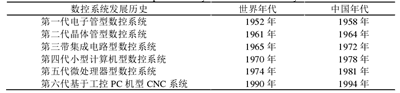
數控技術是一種將機械制造技術、成組技術、現代控制技術、計算機技術、網絡通訊技術、光機電技術、微電子技術、傳感檢測技術、信息處理技術、液壓氣動技術集合在一起的系統技術,是現代制造技術的基礎[3]。數控系統在數控技術中處于核心的地位,其性能的強弱直接影響數控設備加工效能的高低,而且對整個制造系統的升級發展、高效運轉、自動化控制具有重要作用[4]。計算機技術的飛速發展,推動著數控系統向開放式、標準化方向發展,出現了一些不同層次的開放式數控系統[5]。新代科技股份有限公司順應時代發展,推出了開放式的 SYNTEC 數控系統,其開放式的數控系統設計方便用戶進行系統功能的二次開發。 數控是數字化控制(Numerical Control, NC)的簡稱。數控是指利用數字化信息實行的控制,即利用數字控制技術實現的自動控制系統[6],這是數控的廣義含義。從狹義上來說就是利用數字化信息對機床軌跡和狀態進行控制,例如數控車床、數控沖床、數控銑床、數控加工中心等[7]。數控系統嵌入到機床本體中就組成了更具較高附加值的技術密集型產品-數控機床,它可以實現加工過程的自動化控制[8]
在實際的數控生產中,經常會遇到同一系列不同尺寸規格的零件,這需要每一個規格的零部件單獨編制一個數控加工程序,編制程序的工作量就會很大,十分煩瑣不便[9]。在西門子數控系統中,雖然自身帶有某些固定循環功能可供機床操作者使用,但是它的界面不直觀,不友好,且對應用場合的限制較多[10];而在發那科系統中,雖然可通過二次開放 G 功能的方式實現固定循環,但是其界面也不夠直觀,不完善,對操作者的技術要求較高[11]。
1.2 弧齒錐齒輪加工現狀
1.2.1 國外研究現狀
英國人 Hum Phris 在 1970 年最早提出了圓弧齒形的設計思路[12],以這個思路為基礎,慢慢發展到了后來的弧齒錐齒輪。該型齒輪的齒面計算公式是非線性方程組,所以齒面形狀較為復雜[13],加工要求比較高。螺旋錐齒輪具有重合度大、傳動平穩、承載能力高等直齒錐齒輪不具備的性能優點,因而這促使了該型齒輪在相交和交錯軸傳動場合中的廣泛應用。基于該型齒輪優越的性能,對螺旋錐齒輪進行相關研究的重要性在世界范圍內得到廣泛的認同。而美國
Gleason 公司的 E.威爾德哈泊以及 M. L.巴斯特爾初步提出了弧齒錐齒輪理論[14],以此為基礎,Gleason 公司通過對弧齒錐齒輪的深入研究,形成了特有的弧齒錐齒輪相關技術,奠定了其在世界上的壟斷地位。圖 1.1是弧齒錐齒輪嚙合傳動示意圖。
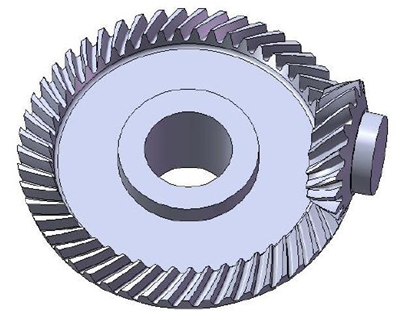
圖 1.1 弧齒錐齒輪嚙合傳動示意圖
曲齒錐齒輪分為延伸外擺線(Oerlikon 和 klingelnberg)和準雙曲面(Gleason)兩種齒制[15],曲齒錐齒輪的加工制造技術要求比較高,目前世界上只有三家公司具有相關的技術,分別是美國 Gleason(格里森)、瑞士 Oerlikon(奧利康)和德國 Klingelnberg(克林根貝爾格)[16]。準雙曲面齒輪在軸線相交時即為弧齒錐齒輪,其應用最廣泛,這種齒輪采用間歇分齒法銑齒加工而成,調整加工的過程復雜。
國內外學者對曲齒錐齒輪進行了深入的研究。60 年代初 Gleason 公司的 Baxter 和Wildhaber 通過對局部共軛齒面副的齒面接觸過程分析,提出了準雙曲面錐齒輪節面數學模型理論,這提高了Gleason 公司弧齒錐齒輪理論的成熟度[17,18]。由于格里森公司在弧齒錐齒輪技術上的進步,以局部共軛原理作為弧齒錐齒輪設計和加工的基礎,形成了一系列格里森制錐齒輪的設計和加工方法,鞏固了其在弧齒錐齒輪加工領域的壟斷地位。由于弧齒錐齒輪的加工過程是一個反復調整機床參數,反復試切的過程,加工效率比較低, Baxter 提出了弧齒錐齒輪的齒面接觸分析(Tooth Contact Analysis,簡稱 TCA)方法。這種方法是基于計算機平臺運行的,以加工機床的調整參數為依據,建立嚙合齒輪的齒面數學方程,利用數學理論研究齒輪在不同安裝形式下的齒面接觸情況和傳動誤差,通過研究齒面接觸區,對機床調整參數進行修正。美國的著名教授 Litvin 提出“局部綜合法”[19-24]的切齒加工方法,首先給出決定齒輪嚙合區寬度和位置、接觸軌跡方向等傳動質量的相關條件,然后利用微分幾何的數學理論,推算小輪齒面在參考點處的主方向和主曲率,進而得到小輪加工的機床調整參數。Litvin 教授提出的預置拋物線型誤差傳遞函數是這種方法的基礎[25],由于安裝誤差所造成的線性傳遞誤差可以通過這種方法自動吸收掉,這對于齒輪傳動中振動、沖擊以及噪聲的降低是有利的。
(1)Gleason 公司錐齒輪加工系統準雙曲面錐齒輪加工機床是美國 Gleason 公司的主要經營產品,是格里森公司具有自主知識產權的機床,但是它采用的是齒輪傳動機構,其機械傳動機構比較復雜[26],由傳動鏈較長引起的制造誤差比較明顯。二十世紀八十年代,格里森公司以鳳凰系列螺旋錐齒輪加工機床為標志,掀起了該類機床的重大改革創新。這種機床是一種五軸聯動的多功能機床,可加工多種齒制的螺旋錐齒輪,除了需要手動更換夾具、刀盤、工件以外,其余的加工過程均是自動化完成的,相對機床來說,加工精度能夠高出 1-2級,而且重復精度較好。格里森公司與德國 Zeiss 公司合作開發了誤差分析和三座標測量系統,將這個系統連接到鳳凰系列機床上,構成誤差閉環系統:G-AGE。該系統在準雙曲面加工中可以通過一次試切的方式獲得滿意的嚙合配對。
在 CIMT-99 展會上,SRS405 型數控剃齒刀磨床和 450G 型數控螺旋錐齒輪磨齒機被格里森公司以鳳凰系列主力機型的形式推出了。450G 型磨齒機可以按照 3-4 級精度精磨嚙合的硬齒面螺旋錐齒輪小輪和大輪,其加工工件的最大模數為 12mm,最大加工直徑達到了 450mm,聯軸節齒面或者弧齒鼠牙盤也囊括在其加工范圍之內,表現出了優異的加工性能。450G 型數控機床可以實現包括砂輪修整運動在內的八軸聯動,它用其中的五軸聯動實現了錐齒輪加工中的磨齒運動[27]。目前格里森公司生產的較為成熟的數控磨齒機有 200G、450G、800G 以及銑齒機 Phoenix116CNC、175HC、275HC、450HC、100HC 等系列產品。
(2) Oerlikon 公司錐齒輪加工系統 瑞士 Oerlikon(奧立康)公司在 CIMT-99 展會上展出了一臺可實現干切削的型號為 C28 的六軸五聯動的數控螺旋錐齒輪銑齒機[27]。為了排屑的方便,該型機床將刀盤主軸箱的滑鞍安裝在了傾斜床身的導軌上。我國湖北省某車橋有限公司曾于 1997 年引進了 Oerlikon 公司的 C28 型銑齒機,該車橋公司成為中國第一家采用該型數控銑齒機的用戶。隨著生成的發展,這種環保型數控銑齒機以其優異的加工性能受到各企業的青睞,慢慢發展成為汽車后橋主從動螺旋錐齒輪加工的關鍵設備。
(3)Klingelnberg 公司錐齒輪加工系統 Klingelnberg(克林根貝爾格)公司開發出一種型號為 KNC/S35 的萬能數控弧齒錐齒輪切齒機床,該型機床把齒輪測量技術內嵌到機床中,精簡了機床機構,改善了機床的剛性;提高了機械的響應速度,保證了 NC 指令的可靠性,齒輪加工的精度得到提高。將計算機技術應用于齒輪加工機床可以提高加工精度,降低生產成本,增大負載能力和降低噪聲。Klingelnberg 公司采用新的計算機技術之后推出 HPG、HPG-S 兩種型號的錐齒輪加工機床。
1.2.2 國內研究現狀
為了打破格里森公司在弧齒錐齒輪加工領域的技術壁壘,前蘇聯和日本等國的科學家對格里森制齒輪進行了研究和學習,相關的研究學習雖然推動了弧齒錐齒輪理論的發展,但是始終沒有突破弧齒錐齒輪的嚙合理論問題。我國的相關技術人員從 70 年代開始對弧齒錐齒輪嚙合理論的數學基礎進行了系統的研究。為了推進該技術的研究進展,我國原機械工業部于 1972 年將“格里森成套技術的研究”列為重點攻關的科研項目,同時得到了許多知名學者、高等院校的支持。我國科研人員通過不懈的努力,在弧齒錐齒輪嚙合理論方面取得了重大進展[28]。龔道香教授等相關學者通過研究計算,得到了螺旋錐齒輪的齒形精密測量以及相應的誤差處理方法[29],為了求得實際齒面和理論齒面之間的偏差函數,先用誤差補償的方法求得齒形誤差,再用該齒形誤差作為全齒面比較法的初始值來求解。鄭昌啟教授利用嚴謹的數學解析法對共軛齒輪嚙合理論中的基本原理進行了研究[30,31],以此為依據,推算揭示了 Gleason 螺旋錐齒輪的機床調整、齒坯設計、刀具參數的計算和輪齒檢驗原理以及方法。曾韜教授提出了節面分析法[32],利用該方法對準雙曲面齒輪的節點曲率和節點參數進行計算,將相關的計算結果推送給螺旋錐齒輪的切齒計算和輪坯設計,推算出格里森調整計算卡的相關公式。
李左章、王延忠等教授學者采用三次 B 樣條函數的數學理論對齒面采樣數據點進行數值擬合[33],由此得到齒面的擬合函數,歸納出了基于齒面離散數值點的接觸分析理論。蘇智劍教授利用齒面接觸跡線、齒面 NURBS、傳動比函數等已知條件對準雙曲面齒輪齒面的數學模型進行了描述[34,35],豐富了螺旋錐齒輪的設計計算方法和理論。
1.3 課題研究的目的與意義
以我單位引進的新代 SYNTEC 數控系統為平臺,針對弧齒錐齒輪的數控加工過程,對其進行二次開發,通過編程,將現有的先進控制思想應用到數控系統中,完善其控制算法,優化數控加工的參數輸入界面、模擬仿真界面,使其能夠通過屏幕界面直接輸入弧齒錐齒輪的一些基本參數,生成相應的數控加工程序,然后進行自動化加工。 數控系統是衡量一個國家制造業發展水平的重要指標,在制造業中處于核心的位置。作為我國國民經濟的核心以及工業化的原動力,制造業的總產值大約占全國國民生產總值的百分之四十左右。雖然制造業是我國國民經濟的支柱產業,但是數控技術的發展水平較國外發達國家相比差距較大,這限制了我國制造業的發展[36]。
裝備制造業在世界范圍內蓬勃發展,信息技術在裝備制造業相關技術產品的升級換代中表現出的積極作用越來越得到大家的重視與認可。數控技術與控制技術、計算機技術、應用軟件相結合,推動了數控系統的開發,樹立了傳統制造業信息化改造的典范。而先進控制技術的主要任務是使數控機床具有最大化的加工速度、加工速度平滑性以及較小的加工誤差,通過與先進的制造技術結合,縮小了國內與國外在硬件技術和軟件技術上的差距,這對于完善我單位項目中引進的新代 SYNTEC 數控系統的功能,總結數控系統開發過程中的經驗,提升國產數控系統性能和品質具有重要意義。
研究采用計算機仿真、優化的虛擬加工技術,實現了從加工編程到加工仿真的全程虛擬化,可以有效的縮短產品生產周期,減小生產成本。基于新代 SYNTEC-10B 數控系統平臺的弧齒螺旋錐齒輪加工機床人機界面設計,能夠提高錐齒輪加工的人機交互性,提高齒輪的加工效率。新代數控系統人機界面的客制能夠適應螺旋錐齒輪系列化生產中由于生產批次與型號的變更,對數控編程提出的便捷性要求。因此,本課題的研究內容對加快產品研發,縮短制造周期,促進螺旋錐齒輪的應用范圍以及整個機械行業的發展都有著很高的現實意義。
1.4 課題研究內容
臺灣新代科技股份有限公司順應行業發展的需要,推出了便于用戶二次開發的SYNTEC 系列的數控系統,它是一個良好的開放式平臺,通過二次開發可把客戶需要的各功能模塊集成到系統中,這樣既可以將操作者工作經驗的優勢發揮出來,又可以簡化工作流程,提高系統的可維護性。 本課題以新代 SYNTEC 數控系統為開發平臺,以螺旋錐齒輪加工機床為研究對象,針對弧齒錐齒輪的加工進行了數控系統的二次開發。通過 e HMI 軟件對螺旋錐齒輪加工過程中參數輸入、模擬仿真等相關界面進行設計與客制。設計開發的界面系統主要包括齒輪參數輸入、刀具參數設置以及加工參數設置等內容,客制的人機界面簡潔友好,便于操作。通過整個分析設計過程,最終達到界面參數的輸入、加工代碼的生成、加工仿真程序運行整個過程的虛擬化和快速化,初步總結數控加工中參數的優化和加工仿真過程的一般方法。圖 1.2 是 e HMI 的軟件工作界面,圖 1.3 是螺旋錐齒輪加工機床樣機,圖 1.4 是弧齒錐齒輪數控銑齒機示意圖。
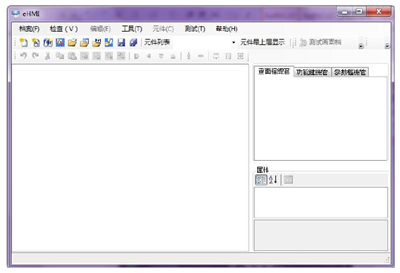
圖 1.2 e HMI 工作界面
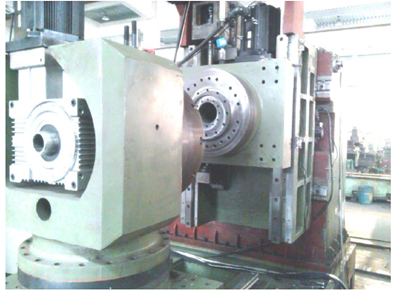
圖 1.3 螺旋錐齒輪加工機床樣機
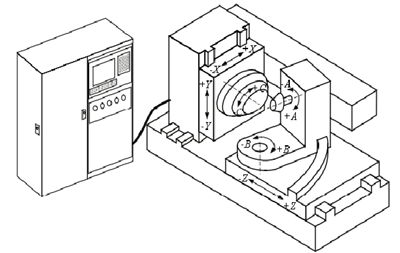
圖 1.4 弧齒錐齒輪數控銑齒機示意圖
1.5 本章小結
本章對課題來源及背景進行了闡述,通過對 Gleason 公司錐齒輪加工系統、Oerlikon公司錐齒輪加工系統以及 Klingelnberg 公司錐齒輪加工系統的分析,引出了對項目中的新代數控系統進行客制化改造的必要性,提出了課題研究的目的意義以及課題研究的主要內容。
第 2 章 弧齒錐齒輪加工原理
弧齒錐齒輪的數控加工過程涉及到的參數比較多,各參數之間的關聯性比較大,導致相關計算過程比較繁瑣;為了配合 SYNTEC-10B 數控系統的人機界面開發的項目需要,對弧齒錐齒輪的嚙合加工原理作簡單分析。
2.1 弧齒錐齒輪嚙合原理
弧齒錐齒輪嚙合原理以嚙合中運動曲面接觸傳動關系為主要研究內容,如圖 2.1所示。局部共軛理論以及相對微分法是研究嚙合原理的主要方法理論,首先以嚙合方程為起點,然后通過相對微分的數學理論,以節點為計算參考點,確定完全共軛時瞬時嚙合點處的撓率和曲率,最后推算計算參考點處的曲面參數[14]。
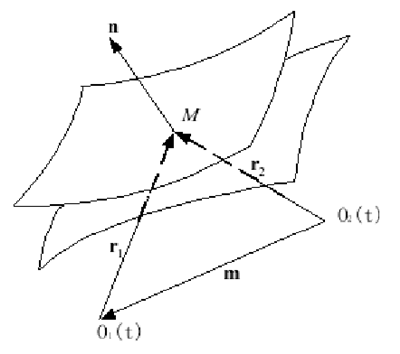
圖 2.1 運動曲面的接觸傳動
2.1.1 相對微分法
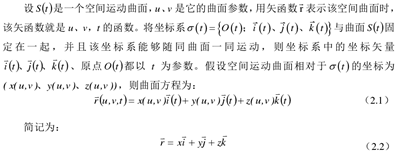
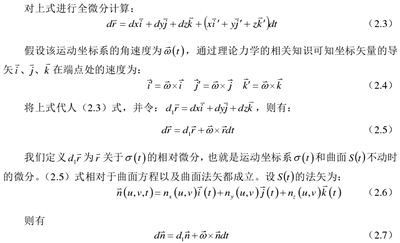
通過上述分析得知:相對微分法能夠兼顧運動中曲面的幾何問題以及運動問題,是研究齒輪嚙合問題的有效工具。
2.1.2 嚙合方程
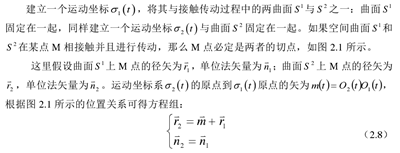
式子中的第一個方程是接觸條件方程,第二個方程是相切條件方程。這是齒輪傳動的基本方程式。
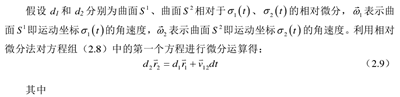

式(2.11)即為嚙合方程,它表示兩運動曲面持續嚙合的前提條件是兩曲面在法線方向的分速度必須相等。
如果兩運動曲面在任何時刻都沿著嚙合方程所確定的曲線接觸,則稱它們為線接觸共軛曲面,即完全共扼曲面;如果兩運動曲面在任何時刻的接觸狀態是在線上,則稱它們為點接觸共軛曲面,即不完全共軛曲面[37]。這兩種嚙合形式在嚙合位置處都滿足嚙合的基本方程(2.8)和(2.11)。
2.1.3 確定第二共軛曲面
在齒輪嚙合原理中經常會遇到求解某一共軛曲面的問題,即根據一對共扼曲面中的第一共軛曲面s1和兩個曲面之間的相對運動關系,求解第二共軛曲面s2 。如果兩個曲面能夠正常嚙合,那么曲面S 2必定是嚙合方程所確定的接觸線在運動坐標系
中的軌跡,所以曲面S2滿足方程組[37]:

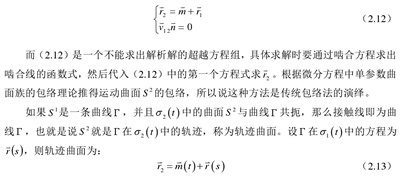

2.1.4 等距共軛曲面原理
(1)等距曲面
設有兩個曲面 S 和Sh,若對曲面 S 上任意一點 M,在曲面S h上都能找到一點 Mh和它相對應,曲面 S 上M點的法矢和曲面nS 上 Mh點的法矢都與MMh平行,而且MMh=h是一個常數,那么曲面S h稱為曲面 S 的等距曲面[37]。如圖 2.2 所示,若曲面 S 的方程為 r ,單位法矢為 n ,則曲面Sh 的方程可以表示為:

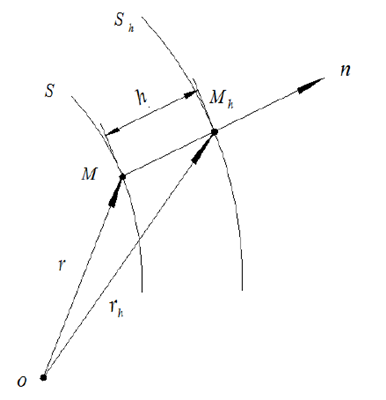
圖 2.2 等距曲面樣圖
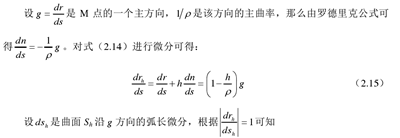
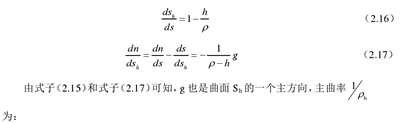
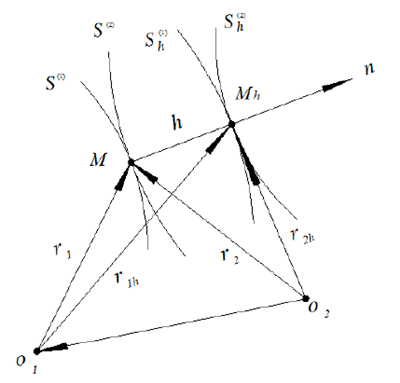
圖 2.3 等距共軛曲面樣圖
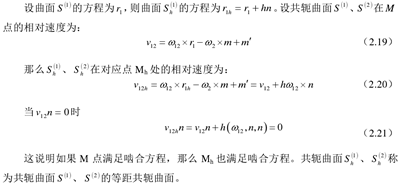
2.2 弧齒錐齒輪加工分析
2.2.1 弧齒錐齒輪加工原理和方法
項目中的弧齒錐齒輪加工采用的是平頂產形輪原理,其中大輪是右旋,它在加工時采用的是雙面銑刀盤;小輪是左旋,它在加工時采用的則是單面銑刀盤。
弧齒錐齒輪與準雙曲面齒輪的加工都是在準雙曲面銑齒機上完成的。該型機床的設計加工原理如圖 2.4 所示,機床的搖臺機構模擬齒輪,而安裝在搖臺上的刀盤的切削面則是模擬齒輪的一個輪齒。當被加工齒輪輪坯與刀盤按照規定的傳動比繞各自的軸線旋轉時,刀盤就會在輪坯上切出一個齒槽。整個切削過程就像一對準雙曲面齒輪的嚙合過程一樣,刀盤的切削面與輪坯的輪齒曲面是一對完全共軛的齒面,稱這種加工方法為展成法[37]。
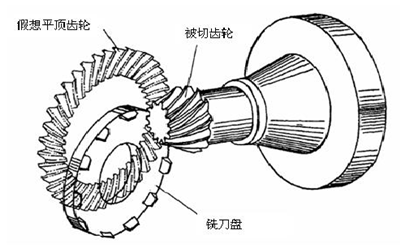
圖 2.4 螺旋錐齒輪加工原理圖
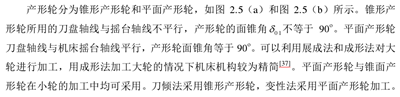
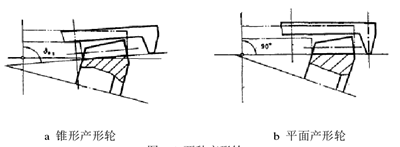
圖 2.5 兩種產形輪
為了能夠在弧齒錐齒輪的齒面展成加工中完成齒根曲面的加工,應該保證工件的根錐與刀盤的刀尖平面相切。圖 2.6 是大小輪嚙合時的刀盤位置圖,通過圖 2.6 可以發現刀盤軸線不平行,這決定了實際加工時既不能像用展成法加工大輪一樣將小輪加工用的刀盤切削面做得和小輪切削面一樣,也不能使大輪刀盤切削面和小輪刀盤切削面相互吻合,而用間接展成法完成加工。所以弧齒錐齒輪不能通過間接展成法和直接展成法完成加工,需要局部共軛原理來加工[37]。

圖 2.6 齒輪嚙合時刀盤的相對位置
2.2.2 局部共軛原理
根據成形法或展成法加工完成的大輪齒面,結合齒輪嚙合原理,求出與大輪共軛的相應小輪的齒面。求出的小輪齒面不能在銑齒機上完成加工,為了得到一個與理想齒面相切并且可以被銑齒機加工出來的實際齒面,需要將小輪齒面上選擇的某點 M 四周的齒面刮去一層,如圖 2.7 所示,完成對理論齒面的修正。這樣處理之后,與大輪齒面相嚙合的實際接觸區就會是一個以 M 點為中心的局部接觸區,這就是齒輪嚙合的局部共軛原理[30]。
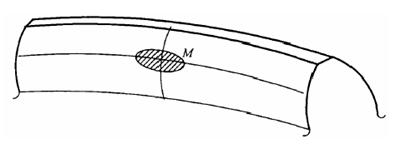
圖 2.7 局部接觸區示意圖
完全共軛的齒輪副具有承載能力大、噪聲低、運動平穩等優點,但是該型齒輪副也存在可調性差的缺點,對相關零件制造、安裝誤差的要求較高,如果制造安裝的過程中出現的誤差較大,輪齒邊緣就會在嚙合傳動過程中出現載荷集中而使破壞的問題。局部共軛的齒輪副能夠克服該缺點,即使在安裝位置存在誤差的情況下,也能夠保證接觸區只能在中點附近移動,避免載荷在輪齒邊緣集中[37]
。基于局部共軛齒輪副在實際生成應用中的優良性能,準雙曲面齒輪以及其他可以用直接、間接展成法加工的齒輪副,越來越多地開始采用該方法加工。
2.3 弧齒錐齒輪齒面建模
2.3.1 坐標系及參數

(1)工件位置基本參數
1)垂直輪位E02垂直輪位是指被切齒輪的中心線與搖臺中心線的相對垂直偏置量。
2)床位BX2 工件箱沿搖臺中心線方向相對于標準位置前進或后退的距離即為床位。它對被切齒輪的切齒深度具有直接影響。
3)軸向輪位修正值X2 工件箱在轉動底座的水平軌道上移動的距離就是軸向輪位修正值X2,它用來調整齒輪在機床上的軸向位置。
(2)刀具位置基本參數
1)徑向刀位S2
刀盤中心02O 到大輪加工坐標系原點 O 的距離即為徑向刀位S2。
2)參考點 M 的相位角

參考點 M 點相位角
是用來表示參考點在坐標系中角相位置的參數。該參數可以完成刀盤在齒長方向的切削加工運動的控制。

3)角向刀位q2 刀盤中心O02和大輪加工坐標系原點 O 的連線與 i 軸的夾角即為角向刀位q2 。刀盤在齒高方向的切削加工運動就是由該參數控制完成的。除了工件位置參數以及刀具位置參數之外,還有大輪與產形輪的傳動比,即滾比02i參數,這也是弧齒錐齒輪齒面模型建立的重要參數。

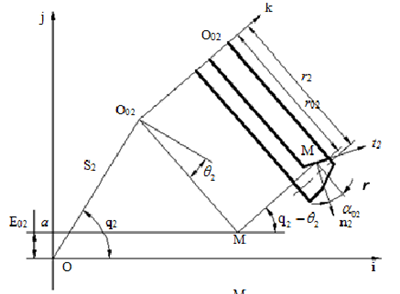
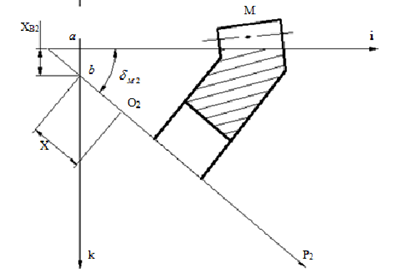
圖2.8 大輪加工坐標系
2.3.2 弧齒錐齒輪齒面方程
以螺旋錐齒輪右旋大輪為例,論述齒面方程的建立過程。圖 2.9 為展成法加工螺旋錐齒輪大輪時所用的雙面刀盤的軸截面,圖中a1為雙刀面內刀面齒形角,a1 為雙刀面外刀面齒形角,r0為大輪刀盤的名義半徑,W2為刀刃的刀頂距。通過式子(2.22)推算加工大輪凸面的內刀和加工大輪凹面的外刀的刀尖直徑[14]。
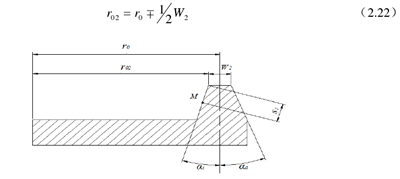
圖 2.9大輪加工用雙面刀盤
大輪齒面與刀盤切削面是共軛的,可以通過共軛曲面的方法求得大輪的齒面方程。
假設切削面為第一曲面,大輪為第二曲面,采用第二共軛曲面的求解方法建立大輪的齒面方程。
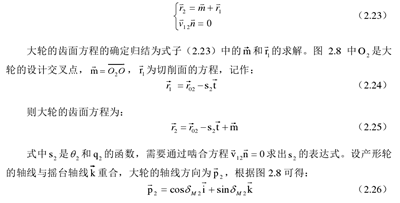
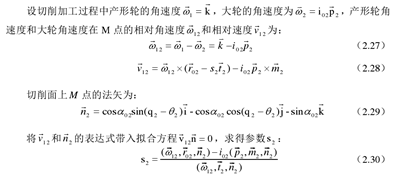
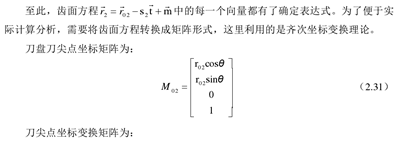
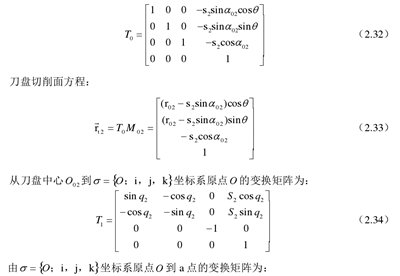
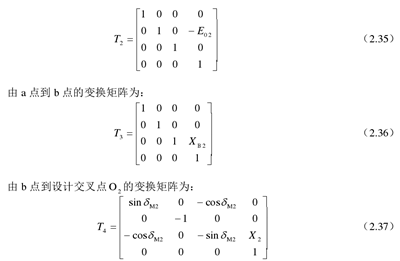
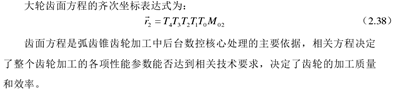
2.4 本章小結
本章主要對螺旋錐齒輪加工理論的相關知識進行了介紹。闡述了嚙合原理,分析了能夠解決齒面幾何問題和運動問題的相對微分法,通過嚙合方程的建立得出運動曲面持續嚙合的前提條件是兩曲面在法線方向的分速度必須相等。對弧齒錐齒輪的加工原理和方法進行了研究,分析了齒輪嚙合的局部共軛原理以及弧齒錐齒輪齒面建模的過程。相關嚙合理論是數控系統后臺計算處理工作的主要依據,為后續章節人機界面的開發設計提供了理論支撐。
投稿箱:
如果您有機床行業、企業相關新聞稿件發表,或進行資訊合作,歡迎聯系本網編輯部, 郵箱:skjcsc@vip.sina.com
如果您有機床行業、企業相關新聞稿件發表,或進行資訊合作,歡迎聯系本網編輯部, 郵箱:skjcsc@vip.sina.com
專題點擊前十
| 更多