加工中心主軸箱體制造工藝可靠性保障方法的研究 (中)
2017-6-30 來源:吉林大學 作者: 譚壯
第 3 章基于模糊評判的加工中心主軸箱體制造工藝
FMECA 工藝 FMECA 方法能夠對加工中心主軸箱體制造工藝中各個工序的工藝故障模式進行分析,尋找引發工藝故障模式的原因,并針對各個工藝故障模式進行風險優先數評分,對風險優先數不符合規定要求的加工中心主軸箱體制造工藝故障模式制定改進措施,跟蹤改進措施的有效性直到其風險優先數降低到符合規定要求為止,達到保障加工中心主軸箱體制造工藝可靠性的目的。當缺少加工中心主軸箱體生產過程中相關統計數據時,將無法客觀計算出工藝故障模式的風險優先數,進而無法判別出風險優先數不符規定要求的工藝故障模式。為了解決上述問題,本章采用梯形模糊評判的方法對不同原因引起的工藝故障模式進行排序,并對加工中心主軸箱體整個工藝流程進行綜合評判,為是否對整個工藝流程實施改進措施提供參考。通過實例分析,驗證了該方法的可行性。
3.1 加工中心主軸箱體制造工藝 FMECA
FMECA 是故障模式、影響及危害性分析(Failure Mode,Effects and Criticality Analysis)的簡稱,是用于歸納分析系統單元產生的故障模式、故障模式發生概率、嚴重程度及其影響后果的一種方法[68]。FMECA 由故障模式及影響分析(Failure Mode and Effects Analysis,FMEA)和危害性分析(Criticality Analysis,CA)兩部分內容組成。上世紀五十年代初,美國一家飛機公司在產品研發階段首先采用了 FMECA 方法,隨著相關標準的制定,FMECA 方法在美國的航空航天以及船舶等領域得到了廣泛的應用。上世紀八十年代,我國將 FMECA 理論引進了國內,經過研究與學習后,制定了一系列的標準并將其應用到了多個行業領域。 根據 FMECA 分析的對象不同可以分為功能 FMECA、硬件 FMECA、軟件FMECA、過程 FMECA 等。通過工藝 FMECA 對加工中心主軸箱體制造過程中每道工序所有可能發生的故障模式、故障原因、故障模式產生的影響、發生概率以及被檢測難度進行分析,根據風險優先數評分確定出薄弱工序并制定改進措施,對改進措施執行后的故障模式風險優先數進行預測或者跟蹤,使各個工序的所有工藝故障模式風險優先數滿足規定要求,從而達到保障加工中心主軸箱體制造工藝可靠性的目的。 根據國家軍用標準的要求[69],加工中心主軸箱體制造工藝 FMECA 的分析步驟如下:
(1)對待分析的加工中心主軸箱體特點、功能及相關要求等進行分析; 繪制“工藝流程表”(用于分析加工中心主軸箱體每道工序的功能和要求)及“零部件-工藝關系矩陣”(對加工中心主軸箱體工序按各個特性進行分類),上述兩個表格是工藝 FMECA 的前期準備工作;
(2)分析加工中心主軸箱體各個制造工序的工藝故障模式,常見的工藝故障模式有:尺寸超差、形狀超差、變形、斷裂等;
(3)對工藝故障原因進行分析,常見的工藝故障原因有:刀具磨損、夾具磨損、熱處理時間不當等;
(4)對工藝故障影響進行分析,工藝故障影響包括對下道工序或者后續工序的影響、對部件或者整機的影響,常見的工藝故障影響有:無法加工表面,部件不合格、整機可靠性低等;
(5)對風險優先數( RPN )進行分析, RPN 值越大表明該工藝故障模式風險性越大,該工序越薄弱,RPN ?S ?O?D,其中 S 表示工藝故障模式的嚴酷度等級,O 表示工藝故障模式的發生概率等級,D 表示工藝故障模式的被檢測難度等級;
(6)對于風險優先數或者 S 、 O 、 D 指標不符合規定要求的工序制定有效改進措施,降低 S 、O 、 D 指標和風險優先數 RPN ;
(7)預測或跟蹤改進措施,直到風險優先數 RPN 滿足規定要求為止; 將分析結果歸納整理,生成工藝過程 FMECA 報告,其主要內容包括:加工中心主軸箱體特征概述、工藝 FMECA 表格、結論及建議、相應的附表(如“工藝流程表”、“零部件-工藝關系矩陣”)等。 圖 3.1 為加工中心主軸箱體制造工藝 FMECA 分析步驟的流程圖。
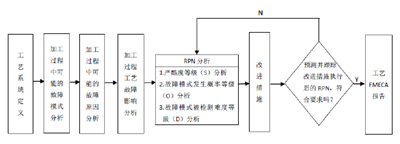
圖 3.1 加工中心主軸箱體制造工藝 FMECA 步驟
風險優先數( RPN )中的S 、O 、D 指標可參照國家軍用標準[69]的評分要求進行打分,但是需要生產過程中的統計數據作為評分參考。當生產統計數據充足的時候,可以直接按照國家軍用標準[69]對加工中心主軸箱體應用制造工藝FMECA 方法,對風險優先數不合規定要求的工藝故障進行改進并跟蹤,直到其風險優先數降低到符合規定要求為止,達到保障制造工藝可靠性的目的。由于企業對制造工藝可靠性的重視程度不夠或者某些型號加工中心主軸箱體屬于小批量生產類型等原因,在執行風險優先數( RPN )中的 S 、O 、D 指標評分時會出現生產過程統計數據不足的情況,從而無法判別哪些工藝故障模式風險優先數不符合規定要求。為了解決數據不足的問題,本文提出梯形模糊數評判與工藝FMECA 相結合的方法。
3.2 梯形模糊數評判方法
3.2.1 相對風險程度梯形模糊數評判方法
相對風險程度梯形模糊數評判方法是將專家組對加工中心主軸箱體各個工藝故障模式的定性比較轉化為定量計算的一種方法。梯形模糊數評判是一個向量,而不是單一的具體數值點,因此具有較高的判斷準確性。本文定義梯形模糊數為M ,其隸屬函數 μ(x) : R-[0,1] 如下[70-71]:
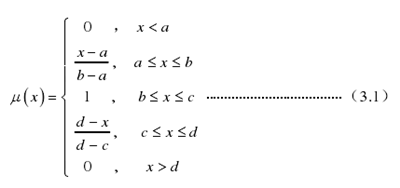
式 3.1 中a<b<c<d a 表示梯形模糊數 M 的上界,d 表示梯形模糊數 M 的下界,閉區間[b,c]表示梯形模糊數 M 的中值,當b ?c 時,梯形模糊數 M 也被稱為三角形模糊數,(d? a)的值越大表示梯形模糊數 M 的模糊程度越強,通常用 M?(a,b,c,d) 表示梯形模糊數。 本文邀請了一組加工中心主軸箱體生產領域的專家,專家組應由工藝設計人員,質保人員、車間檢測人員等組成。以風險優先數( RPN )為指標對加工中心主軸箱體制造工藝過程中所有可能發生的工藝故障模式進行評價,專家組進行評價時需采用本文規定的以下語義詞:“沒有風險”、“很小風險”、“較小風險”、“一般風險”、“較大風險”、“很大風險”。梯形模糊數 M?(a,b,c,d) 可以對上述語義詞進行定量表示,為便于計算,本文將模糊數 M 中 a、b、c、d 四個分位數的取值局限于? ?0,1 區間內,具體數值由專家組確定,即上述每個語義詞的四個分位數a、b、c、d 都是通過專家組加權平均的方法得到,本文所規定的語義詞所對應梯形模糊數如表 3.1 所示。
表 3.1 語義詞對應的梯形模糊數

表 3.1 中的各個語義詞模糊數隸屬函數圖像如圖 3.1 所示,圖中的折線代表了相應語義詞的隸屬函數。
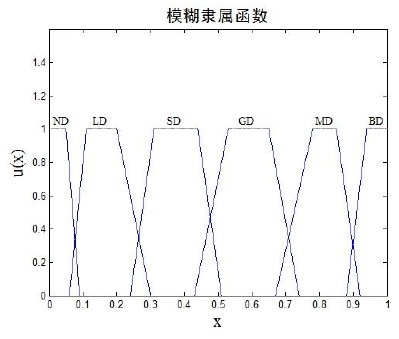
圖 3.1 語義詞對應的梯形模糊函數圖像
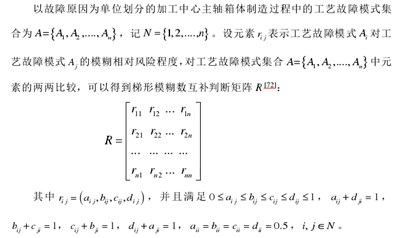

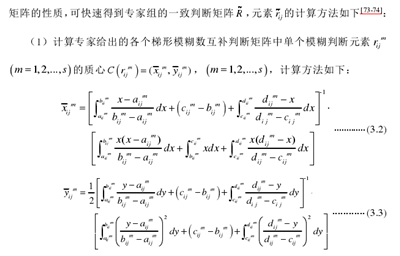
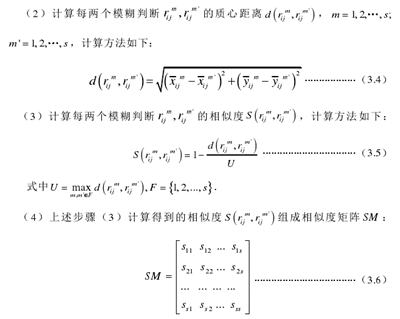

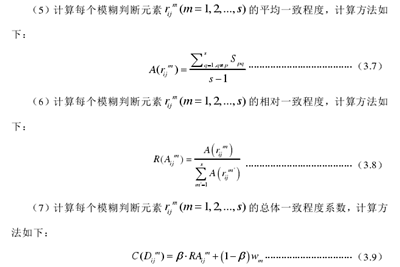
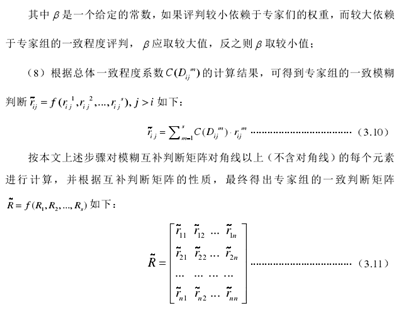

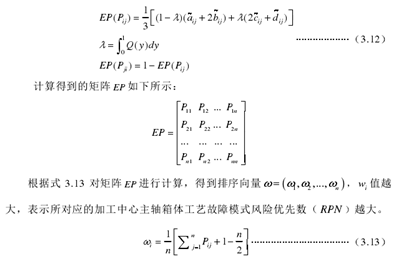
3.2.2 工藝系統模糊綜合評判方法
對加工中心主軸箱體的整個制造工藝系統實施模糊綜合評判,可以為是否對薄弱工序實施改進措施提供參考,具體方法如下所示[76]:
(1)建立制造工藝系統綜合評價的評判等級,等級V 是對加工中心主軸箱體工藝故障模式狀態的 h 個評價決斷即 ? ?1 2, ,...,hV ?v v v ;
(2)以上述評判等級為標準,專家組對加工中心主軸箱體工藝故障模式集合? ?1 2= , ,....,nA A A A 中各元素進行評判,并根據各個專家的權重得到評判矩陣 PA ,? ?1 2 ,...,i i i ihPA ?? ? ? 表示工藝故障模式iA 的評判集iPA ,集合中ij? 表示工藝故障
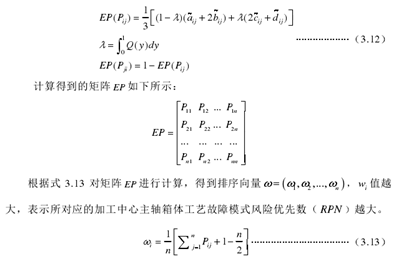
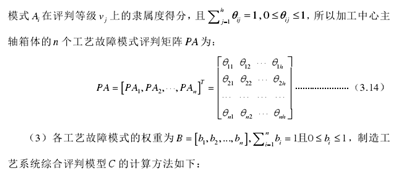
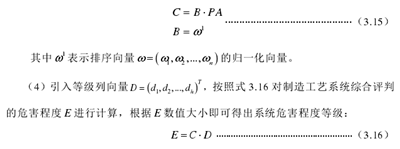
3.2.3 采用模糊評判的工藝 FMECA 分析流程
采用梯形模糊評判方法的加工中心主軸箱體制造工藝 FMECA 的分析流程可概括為圖 3.2 所示,其主要區別是將工藝 FMECA 原有的風險優先數( RPN )評分改為梯形模糊評判,相應的工藝 FMECA 表格也會進行修改,各流程的具體內容可參考本章的實例分析。

圖 3.2 采用模糊評判的加工中心主軸箱體制造工藝 FMECA 流程
3.3 實例分析
本文以某型號加工中心主軸箱體(如圖 3.3 所示)制造工藝為例,結合圖 3.2中的分析流程對其應用基于模糊評判的制造工藝 FMECA 方法,從而能夠在缺少生產過程統計數據的情況下,確定出薄弱工序并制定相應的改進措施,達到保障加工中心主軸箱體制造工藝可靠性的目的。為了便于理解和表達,本文以該型號加工中心主軸箱體的 2 道工序出現的 4 種故障原因引起的工藝故障模式為例進行分析。
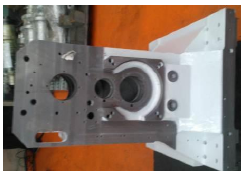
圖 3.3 某型號加工中心主軸箱體
3.3.1 系統定義
加工中心主軸箱體是承載主軸的關鍵零件,其制造精度對整機的加工精度有著重要影響;該型號主軸箱體毛坯為鑄件,體積較大并且加工精度要求高,加工過程中裝夾費時費力,而且運輸困難,具有較大的加工難度。 3.3.2 “工藝流程表”及“零部件-工藝關系矩陣”的繪制
繪制“工藝流程表”(見表 3.2)及“零部件-工藝關系矩陣”(見表 3.3)。
表 3.2主軸箱體工藝流程(部分)
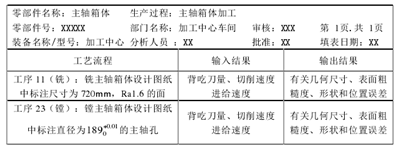
表3.3 零部件-工藝關系矩陣(部分)
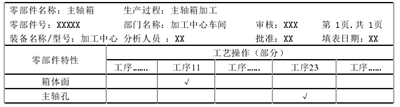
3.3.3 分析主軸箱體工藝故障模式、原因及影響
對加工中心主軸箱體各工序可能發生的工藝故障模式、相應的工藝故障原因及影響進行分析,并以故障原因為單位對工藝故障模式編號(見表 3.4)。
表 3.4 主軸箱體工藝故障模式、工藝故障原因及影響(部分)
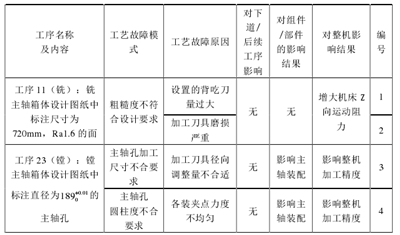
3.3.4 模糊對比評判計算
以風險優先數( RPN )為模糊評判原則,本文共邀請 5 位加工中心主軸箱體制造領域專家對所編號的工藝故障模式進行評判,根據工作年限、職稱、學歷等賦予各專家的權重如表 3.5 所示。根據互補判斷矩陣的性質,專家組只需要給出對角線以上的評判元素即可,具體評分如表 3.6 所示。
表 3.5 專家權重分配

表 3.6 專家組模糊對比評分
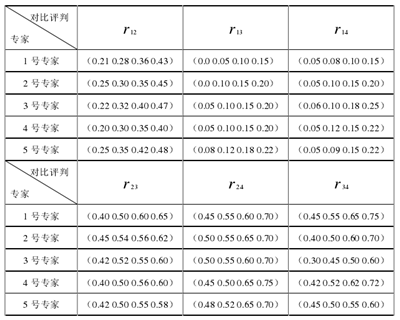
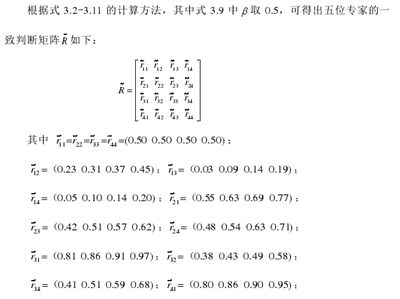
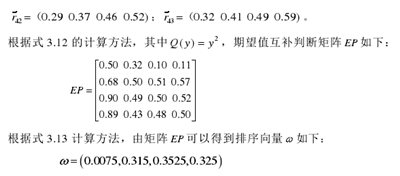
根據? 計算結果可以發現,編號為 3 的加工中心主軸箱體工藝故障模式即由加工刀具徑向調整量不合適引起的主軸孔加工尺寸不合要求,是表 3.4 中所編號的工藝故障模式中風險最大。 3.3.5 模糊綜合評判計算
對加工中心主軸箱體制造工藝系統實施模糊綜合評判,建立評判等級V??風險很高,風險較高,中等風險,輕度風險?,邀請上述 5 位專家對表 3.4 中全部工藝故障模式進行評判,評分如表 3.7 所。
表 3.7 專家組模糊綜合評分
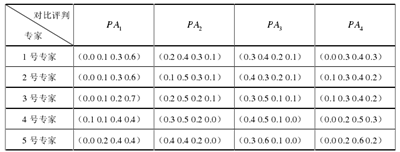
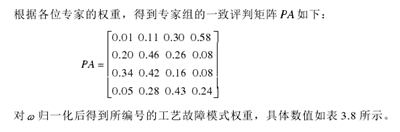
表 3.8 編號的各工藝故障模式權重分配

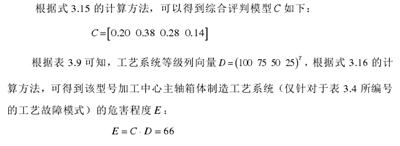
由表 3.9 可知,該型號加工中心主軸箱體制造工藝系統(僅針對表 3.4 所編號的工藝故障模式)風險較高,因此有必要針對薄弱工序采取改進措施,減少工藝故障的發生,比如對工序 23 建立關鍵工序質量控制點。
表 3.9 系統評判等級與改進措施

3.3.6 基于模糊評判的工藝 FMECA 表格
根據模糊評判的結果,針對不同工藝故障原因引起的加工中心主軸箱體制造工藝故障模式采取改進措施,直到發生的工藝故障模式風險程度降低到符合規定要求為止。例如針對工序 23 中的工藝故障模式“主軸孔加工尺寸不合要求”采取了“合理調整加工刀具徑向調整量,調整完之后進行檢查,對該工序建立關鍵質量控制點”的改進措施,對改進措施進行跟蹤后,專家組對其風險評價為“風險很小”,驗證了改進措施的有效性。將上述工作內容進行整理,制定采用模糊 評判方法的加工中心主軸箱體制造工藝 FMECA 表格(如表 3.10 所示,見下一 頁)。
表 3.10 采用模糊評判的加工中心主軸箱體工藝 FMECA 表(部分)
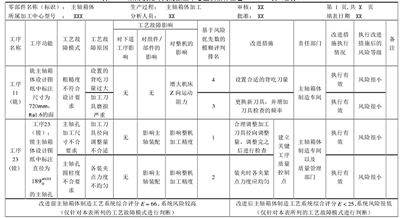
3.4 本章小結
本章介紹了加工中心主軸箱體制造工藝 FMECA 實施流程,以風險優先數為判原則對以故障原因為單位的工藝故障模式應用梯形模糊數評判方法,通過對其風險程度的兩兩比較并對專家組評分進行計算,從而得出各工藝故障模式的風險程度排序,對加工中心主軸箱體整個制造工藝系統進行綜合評判,確定出系統風險等級,為是否實施改進措施提供依據。本章以某型號加工中心主軸箱體的制造工藝為例,對其應用了基于模糊評判的制造工藝 FMECA 方法,得出各工藝故障模式風險排序以及整個制造工藝系統的風險評判等級,制定了針對各個工藝故障模式的改進措施,并對改進措施的有效性進行了驗證,從而降低了整個工藝系統的風險等級,達到了保障加工中心主軸箱體制造工藝可靠性的目的,也驗證了基于模糊評判的加工中心主軸箱體制造工藝 FMECA 方法的可行性。
第 4 章加工中心主軸箱體制造過程控制圖分析及軟件編制
工藝 FMECA 方法能夠針對發生的工藝故障采取相應改進措施,實現對加工中心主軸箱體制造工藝可靠性進行保障的目的,具有直接有效的特點,但工藝FMECA 方法并不能在工藝故障發生之前及時發現生產過程中存在異常因素,所以無法對工藝故障的發生起到預防作用,因此本章將研究以預防工藝故障發生為目的的控制圖分析方法,從而彌補工藝 FMECA 方法所存在的不足。 控制圖分析方法又被稱作統計過程控制(SPC),可以在工序質量特性值符合規定要求的情況下判斷出加工中心主軸箱體制造過程是否存在異常因素。若不存在異常因素,可以通過控制圖對加工中心主軸箱體制造過程進行監控,從而保障加工中心主軸箱體制造過程處于穩定狀態;若存在異常因素,通過對異常因素的排查能夠預防或者減少工藝故障的發生,使生產過程處于穩定狀態,從而提高加工中心主軸箱體制造工藝穩定性。判斷工序質量特性值分布異常的條件較多,為了能夠降低操作人員工作強度,并能快速準確的判別加工過程是否處于穩定狀態,本章采用 MATLAB 的 GUI(圖形用戶界面)編制了加工中心主軸箱體制造過程控制圖分析軟件。
4.1 加工中心主軸箱體制造過程控制圖分析
4.1.1 控制圖分析原理
控制圖分析方法[77]是美國 W. A. Shewhart(休哈特)以預防工藝故障發生為原則首創的控制過程工具,也被稱為統計過程控制(Statistical Process Control, 簡稱 SPC)。W. A. Shewhart 認為產品的質量特性值在生產過程中存在著波動,引起波動的原因有兩種:一種是生產過程中固有的偶然因素所造成的偶然波動,另一種是非生產過程中固有的異常因素(也稱系統因素)所造成的異常波動。偶然因素一直存在于生產過程中并且無法避免,但是對產品質量影響較?。欢惓R蛩厥菚r斷時續的存在于生產過程中并且對產品質量影響較大,但可以避免。因此在生產過程中應利用控制圖分析方法準確判斷出系統因素所造成的波動是否存在,如果存在異常波動應盡快尋找并排除引起異常波動的系統因素,從而能夠預防或者減少工藝故障的發生,保證生產過程的穩定。
文27
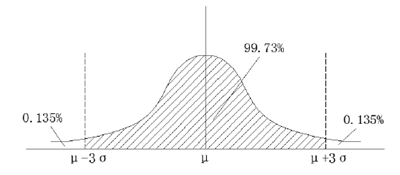
圖 4.1 正態分布曲線
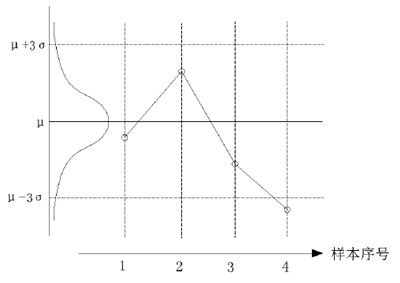
圖 4.2 工序樣本質量特性值描點圖
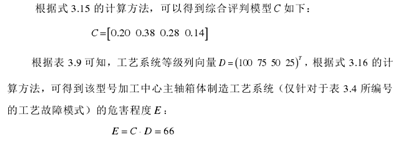
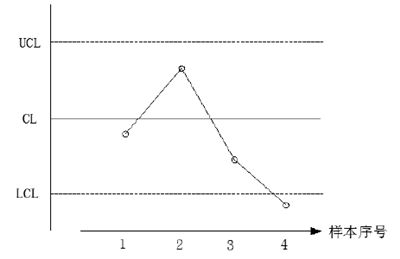
圖4.3 控制圖形式
控制圖可以分為分析用控制圖和控制用控制圖,分析用控制圖是用于判別生產過程中是否存在異常情況以及工序能力指數是否符合要求,控制用控制圖是以當前穩定的生產狀態衡量后續生產的工件質量特性值是否穩定。控制圖又可以分為計量值控制圖、計點值控制圖以及計件值控制圖。計量值中應用較多的是均值
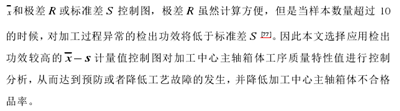
4.1.2 加工中心主軸箱體制造工序控制圖分析流程
目前控制圖分析方法已經形成相應的國家標準以及國際標準[78-80],根據標準的要求,加工中心主軸箱體制造工序控制圖分析流程如下: (1)準備工作:確定所要分析加工中心主軸箱體制造工序的質量特性值 X,根據生產情況按一定的時間間隔采集樣本,并根據時間順序進行分組和排序,樣本容量 n 為 4 ~ 5個,并保證樣本容量相同,樣本個數 K 為 20 ~ 30 個,記錄采集到的樣本數據。
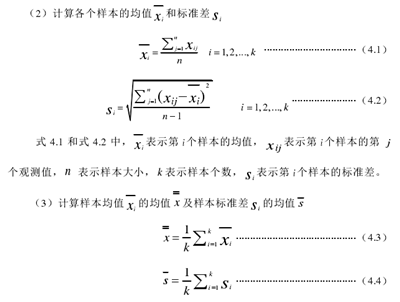
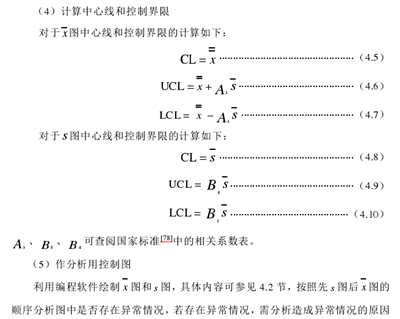
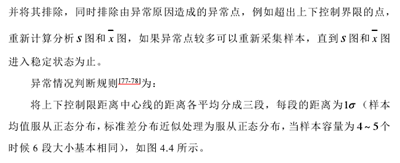
1)有 1 個點落在區域 A 之外;
2) 連續 3 個點有 2 個點落在 A 區;
3) 連續 6 個及以上的點出現遞增或者遞減趨勢;
4)連續 9 個及以上的點出現在中心線同一側;
5) 連續 5 點中有 4 點落在中心線一側的 C 區之外;
6) 連續 8 點落在中心線兩側并且未落在 C 區內;
7) 連續 14 個點中相鄰點交替上下;
8) 連續 15 點落在中心線兩側的 C 區內;
9)點子呈現周期性變化。
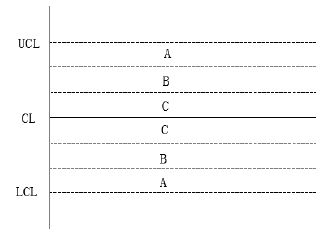
圖 4.4 控制圖區域劃分
(6)判斷該加工中心主軸箱體制造工序質量特性值及控制圖修正后的工序能力指數是否符合規定要求,對其它要求的判斷可根據實際生產情況進行。如果有生產要求不符合規定的情況,應對相關生產因素進行調整,最終將分析用控制圖的控制界限延長從而轉為控制用控制圖。
(7)作控制用控制圖對加工中心主軸箱體生產過程進行控制,按流程(1) 中確定的采集樣本方法采集后續生產的樣本數據,并在控制用控制圖中描點, 判斷是否存在異常。
(8)一段時間后應根據實際質量水平對控制用控制圖的中心線和控制界限進行修正。
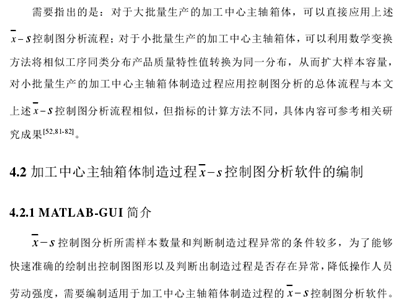
該軟件應具備數據錄入、數據計算、圖形繪制以及制造過程異常判斷等功能,同時能夠記錄加工中心主軸箱體制造過程發生的工藝故障模式、工藝故障原因及影響等,為技術人員提供統計數據,當記錄的數據足夠豐富時可以直接應用于工藝FMECA 分析中而不需要采取模糊評判等數學方法,從而簡化分析過程。 目前編程語言種類豐富如 Java、C、C++、Visual Basic、MATLAB 等,且具備各自獨特的優點,因此根據不同的編程要求及應用領域選擇合適的語言可以提高編程效率并獲得運行穩定的程序。MATLAB 是一種廣泛用于數據分析、數值計算、數據可視化、建模仿真、算法開發等多個方面的高級計算語言和交互環境,并且提供了大量現成的函數,具有計算效率高、編程效率高、操作方便等優點[83]。因此本文采用 MATLAB-GUI(圖形用戶界面)編制加工中心主軸箱體制造過程x ?s 控制圖分析軟件。 MATLAB-GUI 指的是 MATLAB 圖形用戶界面(Graphical User Interfaces,GUI)設計。本文以 MATLAB7.10 版本為例介紹 GUI 設計窗口,如圖 4.5 所示。GUI 設計窗口的上方為菜單欄,包括“File”、“Edit”等6個菜單項;菜單欄下方為工具欄,用于打開布局編輯器、打開菜單編輯器等;網格區的左側為控件工具箱,包括按鈕、可編輯文本框等控件對象;網格區為設計區,用于布置菜單和控件對象。
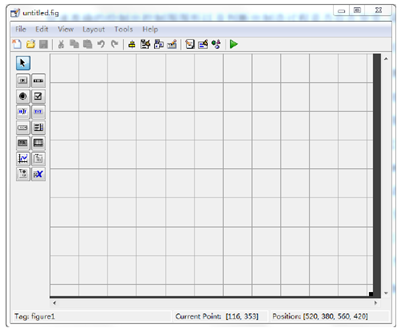
圖 4.5 MATLAB 7.10 版本的 GUI 設計窗口
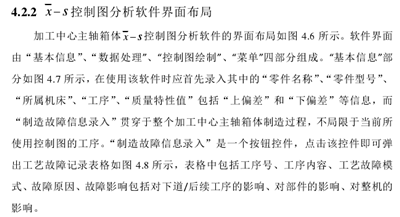
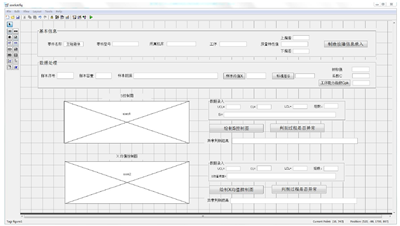
圖 4.6 加工中心主軸箱體 x?s控制圖分析軟件的界面布局
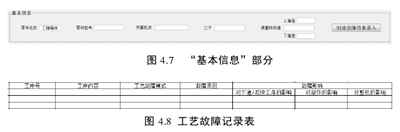
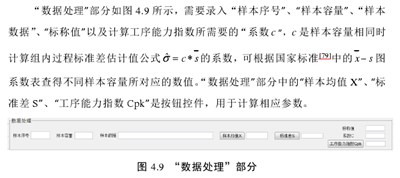
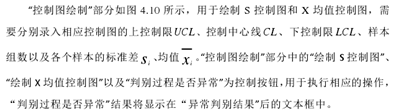
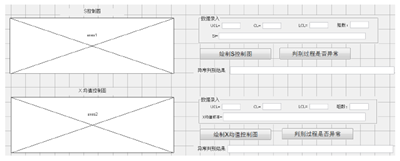
圖 4.10 “控制圖”繪制部分
“菜單”部分如圖 4.11 所示,包括“保存”、“退出”、“軟件說明”三個功能,“保存”功能是將整個軟件界面以圖片形式進行保存,“軟件說明”是點擊之后彈出 word 文檔如圖 4.12 所示,用于說明或者解釋軟件的一些信息,對于4.1.2 節中異常判斷原則中的點子呈現周期性變化,需要通過對控制圖形狀觀察可得。
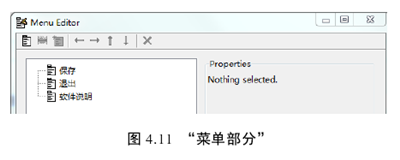
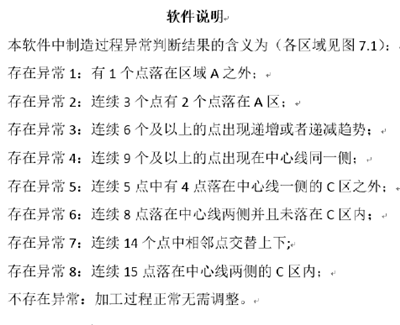
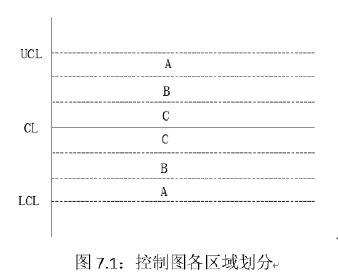
圖 4.12 軟件說明
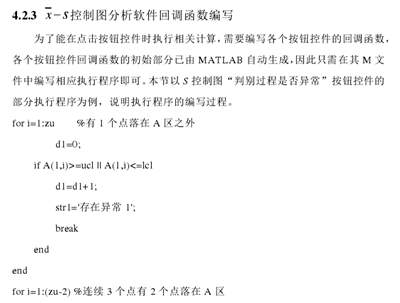
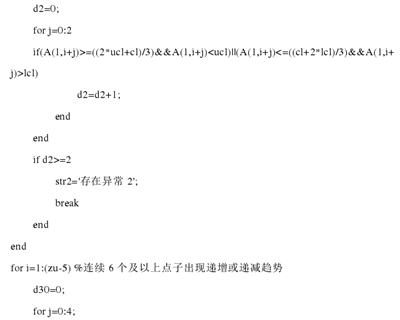
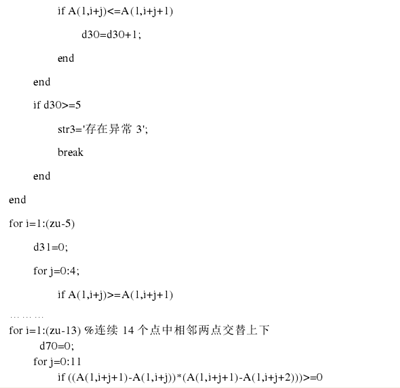
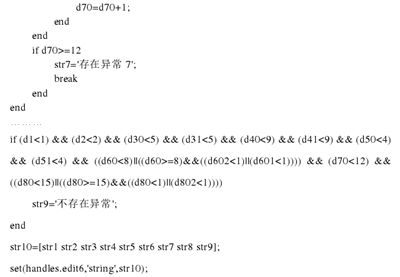
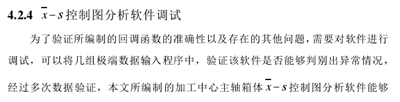
滿足所要求的功能,并且參數計算及異常結果的判斷均準確無誤,由于下一節將進行實例分析,因此本節對軟件調試驗證的具體過程不進行詳細描述。 4.3 實例分析
4.3.1 數據采集與處理
根據 4.1.2 節中的要求,采集了某型號加工中心主軸箱體制造工序 23 的樣本,樣本數量為 25 組,樣本容量為 4,并對樣本數據進行了計算處理,具體數據如表 4.1 所示。
表 4.1 數據記錄表
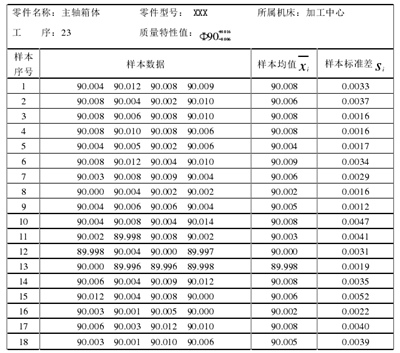
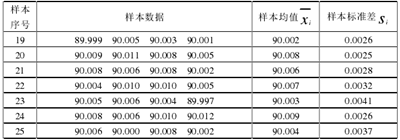
4.3.2 控制圖參數計算
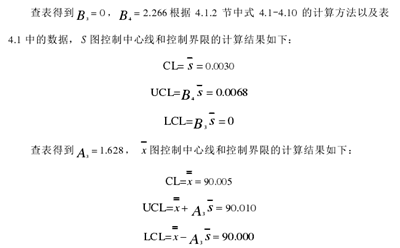
4.3.3 作分析用控制圖及控制用控制圖

件的判別結果可以發現第 12 個樣本和第 13 個樣本均值超出控制界限,因此需要查找造成點子出界的異常原因,通過調查發現是工人師傅未能按規定要求及時調整加工刀具的調刀量,因此需要讓操作工人嚴格遵守生產規定進行操作。 將異常點即樣本 12 和樣本 13 的均值和標準差排除,對剩余的 23 個樣本重新繪制控制圖,并按照式 4.1-4.10 計算新的控制界限,如圖 4.14 所示,可以發現 S
圖和 x 圖均無異常,且樣本數據均符合生產要求,工序能力指數 Cpk為 1.02,表明工序能力尚可,因此可以將去除異常點后的控制圖作為控制用控制圖,對后續生產進行控制,并經過一定時間后對控制界限進行調整。
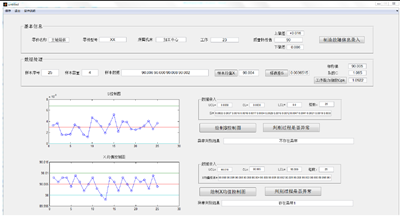
圖 4.13 繪制的分析用控制圖
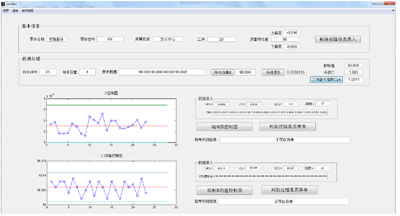
圖 4.14 去除異常點后的控制圖
4.4 本章小結
本章介紹了控制圖分析方法的原理以及加工中心主軸箱體制造過程控制圖分析步驟,利用 MATLAB-GUI(圖形用戶界面)編制了加工中心主軸箱體制造過程 x ?s 控制圖分析軟件,該軟件具備數據錄入、數據計算處理、繪制控制圖、判斷制造過程是否異常、記錄工藝故障數據等功能,通過實例分析表明所編制軟件能夠準確快速計算樣本數據、繪制分析用 S 圖和 x 圖、判斷出加工中心主軸箱體制造過程是否存在異常,通過對異常因素和異常樣本數據的排除可以生成相應的控制用控制圖,用于監測后續加工中心主軸箱體制造過程的波動情況。因此本章所研究的控制圖分析方法能夠保障加工中心主軸箱體制造過程的穩定,預防制造工藝故障的發生,從而達到保障加工中心主軸箱體制造工藝可靠性的目的。
投稿箱:
如果您有機床行業、企業相關新聞稿件發表,或進行資訊合作,歡迎聯系本網編輯部, 郵箱:skjcsc@vip.sina.com
如果您有機床行業、企業相關新聞稿件發表,或進行資訊合作,歡迎聯系本網編輯部, 郵箱:skjcsc@vip.sina.com
更多本專題新聞
專題點擊前十
| 更多