航空復雜殼體零件深孔加工技術研究
2019-1-24 來源:- 作者:張曉東 韓策
摘要:深孔加工在航空制造業中具有廣泛需求,是加工難度最大的工序之一。復雜殼體零件是航空發動機的關鍵部件,其深孔加工質量直接影響航空發動機的服役性能和使用壽命。以航空復雜殼體零件為對象,針對航空復雜殼體零件深孔加工的工藝特點及難點,就目前現有深孔加工方法、深孔鉆削力學、深孔鉆削切屑形態與排屑方法、深孔加工在線監控及深孔加工設備等方面關鍵技術進行綜述,并探討了深孔加工未來的發展趨勢。
關鍵詞:深孔加工;鉆削;加工系統;復雜殼體
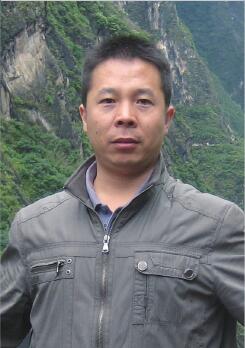
張曉東 博士研究生、高級工程師,主要從事數字化制造、數控加工技術以及智能加工技術研究
復雜殼體類零件是航空發動機系統中典型的結構件和關鍵件,是實現航空發動機燃油系統高、中、低壓油路導引的核心部件。航空復雜殼體零件的顯著特點是結構復雜、孔系眾多,其內部有多達幾百個縱橫交錯的各種深孔,孔徑小、深徑比大、直徑從 1mm 到幾十毫米不等、孔深與直徑之比高達 50 以上,而且帶有各種臺階孔、環形槽等結構。這些孔結構復雜、精度要求高、孔的圓度和直線度要求高、加工難度大,使深孔加工成為復雜殼體零件加工中難度最大的加工過程之一。復雜殼體零件的深孔孔系是燃油系統油路導引的通道,其加工尺寸誤差直接影響發動機燃油系統工作性能,其表面質量直接決定發動機燃油系統的服役壽命,對航空發動機的質量和服役性能有著舉足輕重的作用。隨著新一代飛機和航空發動機的發展,復雜殼體類零件孔系結構的設計更趨復雜、精度要求越來越高,對深孔加工技術提出了更高的要求。
然而,我國深孔加工領域的基礎較薄弱,目前航空企業中尚缺乏高性價比的深孔加工專用裝備,加之深孔加工技術的研究尚不成熟,導致目前我國航空企業中復雜殼體深孔加工普遍存在合格率低、生產效率低以及加工質量不穩定等問題。深孔加工技術成為航空發動機燃油控制系統研制生產的技術瓶頸,嚴重制約著我國航空制造業的發展,因此迫切需要對深孔加工技術展開深入研究。本文以航空復雜殼體零件為象,對深孔加工技術的工藝特點及難點、發展現狀、關鍵技術等進行闡述,并展望了未來深孔加工的發展趨勢。深孔加工工藝特點及難點在航空復雜殼體零件的深孔加工過程中,孔的超大深徑比帶來的鉆桿低剛度問題、排屑和散熱困難問題以及加工時的封閉或半封閉狀態等都使得深孔加工非常困難。航空復雜殼體零件深孔加工的難點主要體現在:
(1)工藝系統剛性差。殼體零件中孔的小直徑和超大深徑比直接決定了鉆削所用鉆桿細且長,使得鉆桿剛度不足,從而造成鉆削過程中鉆桿易產生偏斜、振動、扭曲,甚至折斷。為避免這一問題,生產中往往采用小進給量鉆削以避免大切削力帶來的鉆桿剛度問題,這嚴重制約了深孔的加工效率。然而即便如此,孔的加工質量仍很難保證。
(2)排屑困難。孔的小直徑和大深度決定了鉆削過程中切屑在孔內的排屑空間小且排屑路徑長,極易發生切屑堵塞,從而產生過大的扭矩,鉆頭隨之發生崩刃、折斷,造成
零件報廢。航空殼體零件多采用鋁合金材料,加工過程中易發生粘刀現象,使排屑問題更為嚴峻。此外,采用外排屑方式時切屑會刮傷孔的已加工表面,造成孔壁出現螺旋溝,嚴重影響孔表面質量。
(3)切削散熱困難。一般孔的鉆削過程中,80%的切削熱被切屑帶走。而在深孔加工中鉆頭在相對封閉的狀態下工作,切削熱很難擴散,由于殼體零件中很多孔直徑很小,因此加工過程中的冷卻、潤滑也都很困難,這使得鉆頭和工件成為主要散熱體,熱量積聚效應非常明顯,使鉆頭溫度升高、磨損加劇,極大影響了鉆頭使用壽命。同時,當溫度過高時,加工孔也會受到熱效應影響而發生變形,影響孔的尺寸精度。
(4)難以觀察加工過程。由于殼體零件的孔隙結構復雜、深孔空間狹小,加工過程處于封閉或半封閉的狀態,無法直接觀察鉆頭的狀態和孔的加工情況。以上工藝特點及難點決定了深孔加工過程中的隨機故障很多。大量的試驗和研究表明,刀具磨損、破損和切屑堵塞是導致在深孔加工過程中較頻繁出現故障的主要原因。
在航空復雜殼體零件的加工中,孔加工通常是中間工序或最后工序,一旦在孔加工過程中發生鉆桿折斷或孔道刮傷、偏斜等故障,將直接導致零件報廢,造成巨大經濟損失。
深孔加工技術發展現狀
1 、深孔加工發展歷程
孔加工起源于美國人發明的扁鉆,以及后來改進形成的麻花鉆。這兩種鉆頭的結構相對簡單,切削液導入方便,便于制造出不同直徑和長度的鉆頭以適用于加工不同尺寸的孔。然而,當加工深孔時,扁鉆和麻花鉆的排屑和冷卻十分困難,同時由于鉆桿剛度隨之降低,也限制了加工效率。20 世紀初,為解決槍管加工問題,美、英等國軍事工業部門發明了槍鉆。槍鉆系統將高壓切削液通過鉆桿內部通道送到切削部分,進行冷卻和排屑,屬于外排屑的鉆削方式。此外,槍鉆鉆頭上安裝有導向塊,具有自導向功能。但由于采用外排屑方式,切屑與加工表面會發生刮擦,影響孔表面質量。同時,由于自身結構缺陷,導致槍鉆的成本較高而加工效率和精度較低。第二次世界大戰期間,為滿足槍炮高效生產的需求,德國的 Beisner 于 1942 年發明了一種內排屑深孔鉆,后經國際孔加工協會(Boring and Trepanning Association, BTA)的改進,形成了 BTA 鉆削方法。BTA 系統采用的鉆桿結構剛度較高,采用內排屑方式,孔表面質量較好。但是 BTA 系統具有切削液壓力高、密封困難的缺點。1963 年,瑞典Sandvik 公司利用液體的噴吸效應原理,發明了噴吸鉆法,利用切削液的噴、吸聯合作用,改善了排屑方法,降低了系統的壓力。20 世紀 70 年代,日本冶金股份公司發明了雙進油單管噴吸鉆系統(Double Feeder,DF),它將雙管系統改為單管,增加了一 個專門起吸效應的油壓頭,增大了鉆 桿 的 剛 度。20 世 紀 80 年 代,國內中北大學的王峻等發明了單管內排屑噴吸鉆(Single-Tube Inner Chip Removal Ejector Drill, SIED),SIED 技術完善了 DF 鉆的抽屑容器設計,使抽屑能力大大增強,同時對鉆頭結構進行了優化設計,構成了以單邊刃、單管內排屑噴吸鉆、自導向為特征的鉆削系統,這項技術成為當前先進的深孔加工技術。
2 、現有深孔加工系統及方法
除傳統鉆削外,目前常用的深孔加工系統有槍鉆系統、BTA 系統、噴吸鉆系統、DF 系統和 SIED 系統。現有深孔加工方法按排屑方式可分為外排屑和內排屑兩種,外排屑是指切削液由鉆桿內部進入,經鉆頭小孔噴射到切削區域,然后攜帶切屑從鉆桿外部與孔壁的間隙排出的方法,主要包括扁鉆、麻花鉆和槍鉆等;內排屑是指切削液從鉆桿與孔壁的間隙進入,靠切削液的壓力將切屑推入鉆頭小孔,經鉆桿的內部通道排出的方法,主要包括 BTA 鉆、噴吸鉆、DF 鉆和 SIED 鉆等。外排屑的缺點是切屑會與孔壁接觸產生劃痕而破壞孔表面質量,此外鉆桿剛度不足導致加工效率較低,加工精度難以保證;內排屑克服了這些缺點,但由于需要足夠的容屑空間,導致鉆桿的最小直徑受到限制。生產實踐中需要根據加工孔的尺寸和質量要求等實際情況合理選擇加工方法。
2.1 傳統鉆削
傳統深孔加工一般以使用麻花鉆為代表。在航空復雜殼體零件深孔加工中典型的工藝方法是采用長、短麻花鉆配合使用、鉆削過程多次退刀排屑、逐級延伸鉆孔的方法。傳統鉆削方法材料去除率大,便于在數控加工中心上與其他加工方法集成,加工效率高,而且具有加工操作簡單、不需要專用設備、成本低等優勢。因其鉆頭結構相對簡單,鉆桿可以制造得很細,目前對于直徑小于 6mm 的深孔,傳統鉆削仍是主要的加工方法。基于上述原因,傳統鉆削方法目前仍是我國航空企業復雜殼體零件深孔加工的最常用方法。但是,傳統深孔加工的主要問題在于鉆頭易折斷、排屑和冷卻問題難以解決,因此將造成返工返修,甚至整套殼體零件的報廢,導致生產周期延長、質量穩定性差等問題。目前,隨著航空復雜殼體批量生產質量和加工效率要求的逐步提高,傳統鉆削方法面臨越來越多的問題和挑戰。
2.2 槍鉆
槍鉆因最早用于槍管制造而得名。它采用單切削刃并具有自導向功能的 V 型中空鉆桿,屬于外排屑方式。其工作原理如圖 1 所示,切削液從入口經加壓泵進入鉆桿內部通道,流向鉆頭的切削部分進行冷卻潤滑,并將攜帶切屑通過鉆桿和孔壁間的 V 型槽,最后從出口排出。槍鉆相比于采用麻花鉆的傳統鉆削方式,改善了排屑和冷卻的方法,鉆頭具有自導向功能,能夠加工更深、更小的孔。但由于它仍屬于外排屑方式,切屑容易擦傷已加工孔壁,而且孔較深時切屑必須保持小而薄的形狀,才能保證被冷卻液沖出,加之槍鉆系統的排屑方法對油壓要求很高,要求使用專用機床,導致費用昂貴。此外,槍鉆具有難以彌補的結構性缺陷:一是其鉆桿是 V 形非對稱空心軸,剛性差,鉆孔過程中容易發生質心偏移,因此只能傳遞有限的扭矩,進給量受到限制,只適用于加工小直徑孔,加工效率低;二是其鉆頭與鉆桿不可分離,通用性差。目前,槍鉆系統主要用于加工直徑 φ<20mm 的深孔。
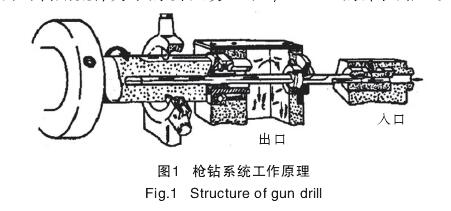
2.3 BTA系統
針對槍鉆系統存在的缺點,國際孔加工協會發明了一種內排屑深孔鉆,BTA 系統中鉆頭與鉆桿為中空圓柱體,提高了刀具剛性和快速拆裝問題。其工作原理如圖 2 所示,切削液經加壓從入口進入授油器后通過鉆桿與孔壁形成的密封環狀空間,流向切削部分進行冷卻潤滑,并將切屑壓入鉆頭上的出屑口,經鉆桿內腔從出口排出。相比于槍鉆,BTA 系統采用內排屑方式,切屑不與工件孔壁摩擦,加工質量較好,而且其鉆桿為圓管狀,剛性較好,加工效率較高。但 BTA 系統對切削液壓力要求高、密封困難,受鉆桿內排屑限制,排屑空間小,經常發生堵屑。為解決這一問題,通常需要在鉆頭上加工斷屑臺或采用錯齒結構,而結構的復雜化造成鉆頭制造難度大且價格高,使 BTA刀具實際上成為價格昂貴而并不耐用的壟斷性工具產品,這是 BTA 鉆在我國航空企業難以普及推廣的重要原因。目前,BTA 系統主要適用于直徑 φ>12mm 的深孔加工。
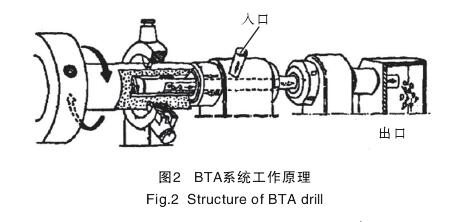
2.4 噴吸鉆系統
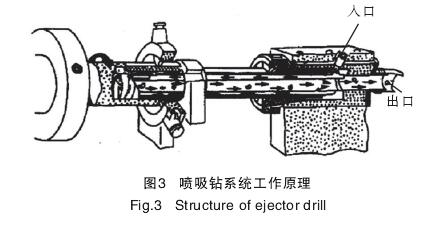
噴 吸 鉆 系 統(見 圖 3)是 瑞 典Sandvik 公司利用流體力學的噴吸效應原理發明的雙管內排屑深孔鉆削方法。進一步改善了排屑過程,降低了冷卻系統的壓力。其噴吸鉆系統采用雙層管刀桿,切削液經加壓后從入口進入,其中 2/3 的切削液進入內、外鉆桿間的環形空間,流向切削部分進行冷卻和潤滑,并將切屑推入鉆桿內腔;其余 1/3 的切削液,從內鉆桿上月牙狀噴嘴高速噴入內鉆桿,在內鉆桿內腔形成一個低壓區,對攜帶切屑的切削液產生抽吸作用,在噴、吸雙重作用下,促使切屑快速從出口排出。噴吸鉆系統的切削液壓力低且穩定,排屑順暢,降低了密封性要求。此外由于其采用雙層管刀桿,剛度較高,可以采用大進給量加工。然而噴吸鉆系統的鉆具結構復雜,制造難度大,成本高。對于孔深較大的孔負壓抽屑效果受限,加之其采用雙層管刀桿結構,容屑空間小,限制了排屑能力。目前,噴吸鉆系統主要適用于直徑 φ>18mm 的深孔加工。
2.5 DF系統
DF 系統(見圖 4)是日本冶金股份有限公司研制出的雙進油單管內排屑系統,其切削液分為前后兩支,分別從兩個入口進入。前一支 2/3的切削液經過鉆桿與己加工孔壁形成的環狀區域流向切削部分,并將切屑推入鉆頭上的出屑口進入鉆桿,流向抽屑器;后一支 1/3 的切削液直接進入抽屑器,經前、后噴嘴之間喇叭口狀的窄狹錐形間隙后獲得加速,產生負壓抽吸作用,達到加速排屑的目的。DF 系統前半部分起“推”作用的結構類似于 BTA 系統,后半部分起“吸”作用的結構類似于噴吸鉆系統,而由于 DF 系統采用了雙進油裝置,僅用一根鉆桿即完成推壓和抽吸的切屑方法,鉆桿直徑可以做得更小,相比于噴吸鉆能夠加工更小的孔,抽屑效果也優于噴吸鉆。但其抽屑器設計仍不夠完善,生產實踐中DF 系統僅可在有限范圍內能替代BTA 和雙管噴吸鉆。目前,DF 系統的最小加工直徑 φ 可達 6mm。
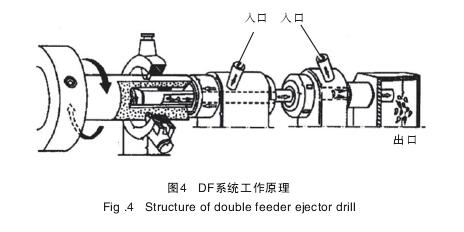
2.6 SIED系統
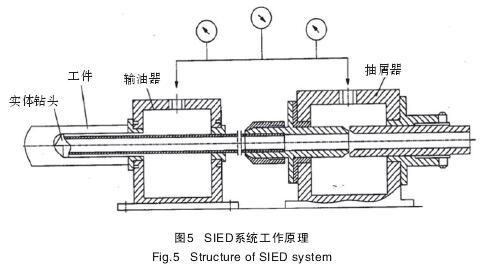
SIED 系統是一種由中北大學王峻 發明的單管內排屑噴吸鉆系統。該技術以 BTA、噴吸鉆、DF 系統 3 種內排屑鉆削技術為基礎,增加了分調式功率增補型抽屑裝置,可實現冷卻和排屑液流的獨立控制。其基本原理如圖 5 所示,切削液由液壓泵輸出后,分為兩個分支:前一支切削液流入輸油器,經鉆桿與孔壁之間的環狀空間流向切削部分,將切屑推入鉆頭上的出屑口;后一支切削液流入抽屑器,經錐形噴嘴副之間的間隙進入后噴嘴內腔,產生高速射流和負壓。SIED 系統對兩支液流各設獨立的調壓閥,可以分別調整至最佳冷卻、抽屑狀態。當鉆孔長徑比過大時,可適當加大后油路的壓力,以保證不因油壓降過大而降低抽屑功效。SIED 系統的分調式功率增補型噴吸鉆抽屑裝置提高了系統對于不同尺寸深孔排屑的適用性。Sl ED 機床具有全面的兼容性,適用于包括內排屑深孔鉆、深孔擴鉆、套料鉆、深孔鉸刀、深孔鏜頭、電鍍金剛石深孔刀具在內的各種內排屑深孔刀具。Sl ED 系統是一種正在逐漸推廣的系統,也是目前較先進的系統。目前,Sl ED 系統可將最小鉆孔直徑縮小 φ5mm 以下。深孔加工關鍵技術近年,針對深孔加工中存在的問題,國內外專家學者進行了大量的研究,主要涉及深孔加工的鉆削力學、切屑形態及排屑方法、在線監控、加工系統及設備等方面。
1 、 鉆削力學研究
鉆削靜力學是研究鉆削過程力學特性的基礎,過去幾十年間得到了專家學者的廣泛關注。Altintas以標準麻花鉆為研究對象,推導了鉆頭切削刃微元的幾何角度關系并利用直角切削到斜角切削的變換建立了麻花鉆的鉆削力和扭矩模型。白萬民等以鉆槍為研究對象,對深孔鉆削過程進行了受力分析,建立了槍鉆的鉆削力模型,并提出了試驗和模型相結合的求解方法。李琦等以內排屑深孔鉆為研究對象,通過試驗方法建立了鉆削力的經驗公式,試驗表明各段切削刃對切屑變形的影響趨勢基本相同。除鉆削靜力學的
研究外,鉆削動力學也是近年來深孔加工領域的研究熱點之一。朱林等通過鉆削試驗,根據鉆削過程模型和試驗數據分析了影響鉆削穩定性的因素,在此基礎上改進了深孔鉆的結構設計,提高了鉆削的穩定性。常豆豆以 BTA 系統為研究對象,分析了鉆削過程中由于速度和位移反饋引起的切削顫振現象,建立了 BTA 鉆橫向、軸向、扭轉方向的動力學模型及動態鉆削力模型。Perng等根據 Hamilton 原理,考慮切削液和軸向壓力的影響,分別推導了基于 Timoshenko 和 Eule-Bemoulli 梁模型的深孔鉆桿運動方程,用旋轉鉆桿和非旋轉鉆桿兩種不同方式添加隨機激勵,研究了鉆桿的動態特性。
Ahmadi 等研究了鉆桿不同方向的穩定性,建立了通用的鉆削過程穩定性模型,并采用磨損刀具的鉆削試驗驗證了模型的準確性。許多研究表明,深孔鉆削過程中,鉆桿系統存在明顯的非線性特征,針對這一問題,Kovacic建立了深孔鉆削鉆桿系統的非線性動力學模型,并采用不同的刀具前角、剪切角以及進給量對鉆削顫振機理進行了較全面的理論分析。因鉆頭的幾何特點、鉆削加工的封閉性以及鉆削過程切屑和熱效應影響,鉆削相對于銑削、車削等切削過程更為復雜。目前針對鉆削力學的研究中,大多以試驗和數值模擬作為研究手段,得到的模型和結論主要依靠經驗,缺乏對鉆削機理的透徹理解,相關理論尚不完善。但這些研究對于了解鉆削過程,改進鉆削系統、鉆削刀具、鉆削工藝,以及優化鉆削參數具有指導意義。
2 、切屑形態及排屑方法研究
排屑過程是深孔加工與一般孔加工相比最顯著的不同之處。在深孔加工中,由于排屑空間狹小,排屑過程變得困難且重要,直接影響加工的順利進行,決定了孔加工的質量。因此,切屑形態以及排屑方法一直是深孔加工領域的難點與研究熱點。趙如意等通過試驗研究了 3 種不同刀片在 BTA 鉆過程中,在不同切削參數下的切屑形態和切屑容屑系數對排屑的影響。試驗表明,切屑容屑系數越小排屑越好,而且 C 形切屑的切屑容屑系數最小,對排屑最有利。汪志明對負壓抽屑裝置進行了研究,改善了深孔加工系統的排屑條件。馬龍等通過 SIED 深孔鉆削試驗研究了不同主軸轉速和進給下切屑的形態和容屑系數對排屑效果的影響。針對深孔加工中斷屑和排屑的問題,隈部淳一郎在 20 世紀50 年代提出了振動鉆削理論,即在鉆削過程中在某一個或幾個特定方向對鉆桿或工件施加某種有規律的振動激勵,鉆頭在振動中切削,使切削用量按某種規律變化,以控制切屑的大小和形狀,達到避免發生切屑堵塞的目標。在國內,薛萬夫等在1982 年開發出振動鉆削設備,并對深孔振動鉆削中切削刃的相鄰運動軌跡進行了理論分析,得出了保證斷屑的加工條件。西安石油大學朱林,西安交通大學高本河等以及成都工具所的樊鐵鑌也在深孔加工的低頻振動鉆削開展了大量研究。目前,振動鉆削已成為深孔加工的一個重要分支。排屑問題是深孔加工中最關鍵的問題之一,針對這一問題,近年來專家學者們從鉆削刀具結構、抽屑裝置、鉆削參數以及鉆削方法等方面進行了研究,發明了大量的新刀具、新裝置和新工藝,排屑問題得到一定改善。未來,切屑形態和排屑過程的定量化以及各種排屑結構、裝置和方法的融合有待進一步研究。
3 、在線監控研究
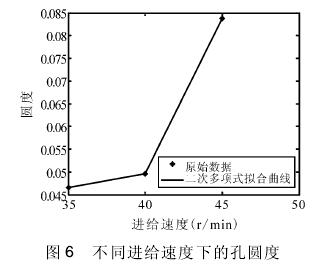
由于大深徑比以及加工時的封閉或半封閉狀態,無法直接觀察到深孔加工過程中刀具的狀態變化。因此,通過各種手段對深孔加工過程進行在線監測與控制成為深孔加工的另一個重要研究方向。在線監控的研究主要以切削力、機床功率、聲發射、振動加速度等信號作為測量參量,在線監控鉆頭磨損及失效、振動、切屑堵塞、軸線偏移等現象,研究問題包括深孔加工在線監測的信號處理、信號特征提取和加工狀態識別與反饋控制。常見的深孔加工在線監測方案如圖 6 所示。Kavaratzis 等將深孔鉆削過程分為 4 個階段,以鉆削力和扭矩為監測信號,采用多層級的控制方法,針對鉆削過程的不同階段采用不同的控制策略。在國內,哈爾濱工業大學、北京理工大學、西安理工大學、上海交通大學等院校和一些科研機構都對此進行了深入研究。其中,哈爾濱工業大學的王清明等提出利用多個特征參數綜合監測鉆削過程,通過大量試驗,觀察刀具在破損、折斷等異常情況下,各個特征參數的變化規律,并設定閾值,對鉆削加工過程進行監測。北京理工大學的王忠民等利用模糊模式識別技術處理經過離散二階小波變換分解的切削過程聲發射信號樣本,實現對刀具磨損狀態的在線識別。西安理工大學的李鵬陽等以鉆削軸向力和扭矩為監測信號,通過對信號進行幅域和頻域分析,提取了特征信號隨鉆頭磨損量的變化規律。上海交通大學的孫程成等分析了槍鉆擴散磨損和粘結磨損的形成機理,并以鉆削力、扭矩和聲發射為監測信號對鉆頭狀態進行監測,采用聲發射信號對刀具磨損狀態進行了表征。現有文獻及相關報道中,在在線監測方面針對信號處理、特征提取和狀態識別3 個領域均有大量研究,以上研究為在線監控系統及設備的研發提供了理論依據,但多數為針對各領域相關算法及策略的獨立研究,缺乏對完整在線監控閉環系統的整體研究。此外,針對深孔加工中易出現的故障,文獻中對刀具狀態的研究較多,而針對鉆削過程的其他現象諸如切屑堵塞、鉆桿振動以及孔擴大、偏斜等與孔加工質量相關的問題仍需要進一步研究。
4 、深孔鉆削設備的研發
在深孔加工中,由切屑堵塞和鉆頭磨損失效造成的鉆桿折斷是最常見的故障。近年來隨著傳感技術的發展,越來越多的在線監測設備已經應用于深孔加工領域。目前,在深孔鉆削力測量技術方面處于國際領先地位的德國 Dortmund 大學的科研工作者 Raabe 等發明了帶有測力元件的測量鉆頭,可以直接測量切削分量。日本町田鐵工生產的全自動鉆床 Micro-hole 配備了扭矩傳感器和鉆頭磨損監控系統,鉆削過程中當鉆頭所受扭矩超過預設值時,系統控制鉆頭退刀并重新開始鉆削,實現了鉆削過程多次退刀排屑方法的自動化。近幾年國內越來越多的專家學者已開始投入研發深孔加工的新設備、新裝置。中北大學的關世璽等結合力傳感器、加速度傳感器以及電磁離合器自主研發了電磁式過載保護裝置,可以實時監控加工的全過程,對深孔加工刀具系統和被加工零件起到保護作用。蘇州大學的張勇等利用 PLC 和交流變頻調速技術把普通車床改造成具有電氣控制系統的深孔加工機床,降低了加工成本,提高了深孔加工的效率和精度。德州德隆機床公司自主研發了可在塑料模具上進行多孔系加工的ZK2103 型三坐標數控深孔鉆床,其鉆孔直徑范圍為
φ4~φ30mm,最大加工深度 1200mm,在國內處于領先水平。目前,國產深孔加工設備相對德國、美國等制造業發達的國家仍較落后。在我國航空企業中,大多數仍采用傳統鉆削方法,對專用深孔加工設備的使用較少,少數企業通過對普通機床的改造以滿足深孔加工的需求。目前,高性價比的專用深孔加工設備的研發仍是我國航空企業亟待解決的問題。
深孔加工技術發展趨勢
1 、智能加工
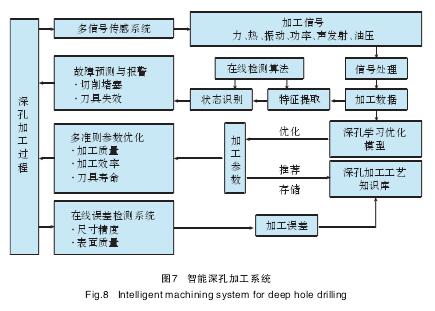
目前,我國航空企業在復雜殼體零件深孔加工中,對于鉆削參數的設定往往是憑經驗。為避免加工中出現鉆頭折斷和切屑堵塞等問題,設定的鉆削參數通常很保守,這樣就造成了加工效率低下,加工質量難以保證。近年來,隨著計算機輔助制造技術、傳感技術以及機器學習等領域的發展,加工設備及加工系統具有對加工狀態的自主感知,對加工工藝知識的學習、進化、積累,以及對加工過程的實時反饋、決策等智能化功能已成為可能。智能加工已成為未來深孔加工發展的必然趨勢,發展具有自主感知、學習、進化、決策功能的智能深孔加工系統將成為深孔加工的重要研究方向。智能深孔加工系統的結構如圖 7 所示。智能深孔加工系統包括多信號傳感系統、在線誤差檢測系統等感知模塊,通過時監測得到深孔加工過程力、熱、振動、功率、聲發射、油壓等信號,利用在線監測算法將處理后的加工數據做特征提取及加工狀態識別,用于切屑堵塞、刀具失效等故障預測與報警;同時,利用智能學習優化模型并結合工藝知識庫,以加工數據和在線誤差檢測系統獲取的孔尺寸精度和表面質量信息作為輸入,實現加工質量、加工效率和刀具壽命等多準則加工參數優化,實時反饋到深孔加工過程,完成深孔加工學習進化的閉環系統。目前在機械加工領域中,智能刀柄、智能刀具的等智能元器件,以及智能加工系統的研發已成為研究的熱點與趨勢。已有一些公司開發了商業化的加工過程智能監控系統,比如ARTIS 在線監控系統,該系統利用傳感及在線監測技術,不僅可監測加工過程機床狀態、刀具狀態、異常及故障,而且可通過其內部算法對加工周期進行優化,根據在每一個加工周期中工藝知識的學習與積累,優化下一個加工周期的加工參數,使加工系統具有自主學習、進化的能力。未來,隨著相關學科與技術的不斷發展,智能深孔加工系統將亦趨成熟。
2 、特種加工
深孔機械加工由于需要刀具,屬于接觸加工,這就導致無法避免一些固有問題:例如刀具材料的硬度必須大于工件材料、切削力導致的變形和振動、工件殘余應力等。當面臨未來航空復雜殼體零件的復雜孔系結構、微小孔以及新材料時,傳統機械加工難以達到要求。特種加工技術是借助電能、熱能、化學能、聲能、光能等多種能量或將幾種能量進行復合以實現材料切除的加工方法。自943 年前蘇聯科學家拉扎林柯發明電火花加工方法后,利用機械方法以外的非傳統加工方式得到了大量的研究,形成了特種加工這一新的發展領域,可以實現超硬、超軟、超精、超光和超微等加工。目前,對于微小孔的加工,特種加工是主要的加工方法。一些學者已經開展了針對深孔的特種加工方法的研究,主要有:電火花加工、電化學加工、超聲加工、激光加工、電子束加工、離子束加工、液體噴射加工等。未來,隨著深孔加工的要求越來越高,機械加工方法將難以滿足,深孔的特種加工方法將成為學術界的關注點之一。
3、綠色加工
近年來,隨著環境保護的迫切度越來越高,對制造業綠色化提出了更高的要求。傳統深孔加工由于需要冷卻和排屑,會產生大量的切削液,造成環境污染和資源浪費。為節省資源和減少污染物排放,綠色加工成為未來深孔加工發展的必然趨勢。目前新型綠色加工技術主要有:綠色切削液、微量潤滑、壓縮空氣冷卻和干式加工。干式加工即在加工過程中不使用切削液,這從根本上避免了切削液的處理以及排放造成的污染,同時也降低了加工成本。但目前的深孔加工技術水平尚難以處理干式加工中產生的大量切削熱,因此暫時無法推廣應用。相對來講,使用微量切削液可較大程度減少污染,同時技術難度大大小于干式切削,目前在學術界受到更多的關注。此外,已有學者研究具有生態性能的冷卻劑,這既降低了散熱的技術難度,又可實現綠色加工,并且其對人體健康無影響,也是一種有潛力的發展方向。未來,深孔加工的綠色化將成為工業界不可忽視的研究內容。
結論
深孔加工技術是一項多學科交叉的綜合應用技術,目前在理論和應用方面都還不夠成熟。由于深孔加工的困難,迫切需要對其理論和技術進行更加深入的研究。本文結合航空復雜殼體零件的深孔加工,介紹了深孔加工的概念,分析深孔加工的工藝特點及難點,闡述深孔加工發展的歷程和目前的發展現狀。通過對文獻資料的調研,給出深孔加工的關鍵技術,并結合目前機械工業的發展現狀展望了深孔加工未來的發展趨勢。隨著數字化技術、傳感技術、信息技術等的快速發展和不斷融合,深孔加工技術將會朝著智能化、多樣化、環境友好的方向不斷發展,在我國航空制造業中發揮更大的作用。
來源:西北工業大學現代設計與集成制造技術教育部重點實驗室 西安航空動力控制科技有限公司
投稿箱:
如果您有機床行業、企業相關新聞稿件發表,或進行資訊合作,歡迎聯系本網編輯部, 郵箱:skjcsc@vip.sina.com
如果您有機床行業、企業相關新聞稿件發表,或進行資訊合作,歡迎聯系本網編輯部, 郵箱:skjcsc@vip.sina.com