高速鋼軋輥加工及應用
2020-3-5 來源: 安陽鋼鐵股份有限公司 作者: 靳長青 宋長林 宋杰
摘要: 針對高速鋼軋輥加工難度大,加工效率低等問題,從高速鋼軋輥特點、刀具材質、機床性能、加工工藝以及使用等方面進行闡述,明確了刀具選型、加工工藝、機床要求和軋輥使用等要素對高速鋼軋輥應用的影響。
關鍵詞: 高速鋼軋輥 刀具 加工工藝 機床 冷卻
0 前言
安陽鋼鐵股份有限公司第一軋鋼廠 260 機組軋鋼生產線,以生產 Ф12 mm ~Ф50 mm 螺紋鋼和礦用錨桿鋼筋為主,同時兼顧核電用鋼筋、高鐵用精軋螺紋等功能性鋼筋,軋機布置采用 6-4-7 工藝形式,1-10架平立交替,全連續無張力軋制。軋輥材質主要采用球墨無限冷硬鑄鐵、高鎳鉻無限冷硬復合鑄鐵。隨著高速鋼軋輥在線棒材軋機上的推廣應用,260 機組在精軋機列全部采用高速鋼材質軋輥,極大提高了軋機作業率、負差控制率和鋼材表面質量。但由于其本身高硬度、難以切削加工的特點,制約高速鋼軋輥的進一步拓展應用。筆者從高速鋼軋輥優勢、刀具材質選擇、加工工藝、機床性能和軋輥使用等方面進行簡要闡述,與大家探討。
1、 高速鋼軋輥
高碳高速鋼復合軋輥( 簡稱高速鋼軋輥) 是近年來發展最快且應用前景最廣的熱軋輥材料,它的成分是較為復雜的合金鋼,在熱處理工藝淬火后,即使在空氣中冷卻也能硬化。其工作層材料采用高碳鋼,軋輥的芯部材料采用球墨鑄鐵、石墨鋼或鍛鋼等,兩種不同的材料通過離心鑄造或者采用 CPC 工藝復合而成,基體組織一般為回火馬氏體+貝氏體+碳化物,碳化物以高度彌散形式分布在基體中,所以具有很高的耐磨性、強韌性,導致車削加工難度大。高速鋼軋輥與其他不同材質軋輥的力學性能對比見表 1。
表 1 高速鋼軋輥與其它軋輥材質力學性能比較

高速鋼軋輥特點是熱穩定性好、淬透性好,碳化物硬度高,容易形成氧化膜,具有良好的抗熱裂性和耐磨性能,對冷卻水的要求遠遠低于硬質合金的要求,它的單槽軋制量能達到鑄鐵軋輥的 4~5 倍。有利于軋材負公差控制,提高軋材表面質量。主要是應用在線棒材成品和成品前機架以及切分軋制預切、切分孔型為主而研發的新型材質軋輥,硬度可達HSD78 ~ 90,具有很高的耐磨性,同時具有良好的抗沖擊性能,抗熱疲勞性好。隨著高速鋼軋輥在線棒材軋鋼廠的普及,研發制造廠家隨之迅速蔓延,但是各廠家在高速鋼軋輥鑄造過程中添加的合金元素有所差異,為此在加工、使用方面,切削難易程度和在線使用效果并非完全一致,整體上主要包含有鎢、鉬、鉻、釩、鈮等碳化物形成元素。
2 、刀具材質選擇
刀具切削部分直接與軋輥接觸切削,承受著很大的切削壓力和沖擊,并在高溫、高壓下,與軋輥發生劇烈摩擦,工況條件十分惡劣。高速鋼軋輥的加工刀具通常選用金剛石和立方氮化硼( cubic boron nitride 簡稱 CBN) 這樣的超硬材料,其切削速度比普通硬質合金刀具提高 10~20 倍,且加工表面粗糙度的值很小。而 CBN 材質刀具較金剛石又具有更高的硬度、熱穩定性和化學惰性,以及良好的透紅外形和較寬的禁帶寬度等優異性能。
( 1) 高硬度。立方氮化硼( CBN) 僅次于金剛石,具有很高的硬度及耐磨性,是當前軋鋼企業高速鋼軋輥加工刀具材質首選。目前 CBN 刀具合成類型有聚晶片( 由 CBN 與結合劑合成) 和復合片( 由CBN 與結合劑合成復合在硬質合金片上) 兩種。在高速鋼軋輥加工上常采用金屬陶瓷結合劑和超細晶粒 CBN 材 質 刀 具,常 用 牌 號 有 MBN3 500 和MBN5 000。實踐也證明,這兩種牌號的 CBN 材質刀具是加工高速鋼軋輥的最佳選擇。
( 2) 足夠的強度和韌性。刀具切削部分材質在切削過程中承受很大切削力和沖擊力。所以其必須具備足夠的強度和韌性。聚晶金剛石( PCD) 有天然和人造兩種類型,工業上多使用人造金剛石作為刀具材料。但是人造金剛石脆性大,抗沖擊能力差,對機床的精度、平穩性要求高,同時金剛石刀具耐熱性差,與鐵元素有較強的親和力,因此金剛石刀具主要用于有色金屬及其合金材料加工,不適用加工鐵系金屬,故一般不用于軋輥加工。而 CBN 刀具熱穩定性較金剛石高一倍,具有優良的化學穩定性,抗彎強度和斷裂韌性介于硬質合金和陶瓷刀具之間,適合加工鋼鐵材料。
( 3) 高耐磨性和耐熱性。一般來說,刀具材質硬度越高,耐磨性越好。耐磨性與耐熱性密切相關,高溫下硬度越高,表示耐熱性越好。CBN 材質刀具能夠在高溫下保持較高的硬度,即紅硬性好。同時在高溫下抗塑性變形能力強,故此耐磨性也高。
( 4) 良好的導熱性。導熱性好的刀具材質其耐熱沖擊和抗熱龜裂的性能也好。CBN 復合刀片熱穩定性能在 1 000 ℃ 左右保持較好的紅硬性,所以其受切削熱量影響不大。
( 5) 良好的工藝性和經濟性。CBN 刀具是利用人工方法在高溫高壓條件下用 CBN 微粉和少量的結合劑合成的 CBN 材質刀具,適合制造成各種形狀,不同角度的刀片,是數控機床加工的理想刀具。硬質合金、人造金剛石與 CBN 材質力學性能對比見表 2。
表 2 普通硬質合金、人造金剛石與 CBN 材質力學性能

3 、高速鋼軋輥加工
高速鋼軋輥輥身工作層是在馬氏體基體中彌散分布高硬度的細微碳化物,在切削加工過程中,對刀具刃口產生劇烈高頻沖擊,同時輥身加工中溫度對硬度影響很小,加速刀具磨損,從而使得高速鋼軋輥加工難度大,切削效率低。因此,高速鋼軋輥的加工應采用高轉速、低切削用量,勤換刀的方法,來克服加工過程的困難。
3.1 軋輥孔型的加工
高速鋼軋輥孔型新輥加工由于粗加工量大,刀具磨損快、壽命短,所以一般先使用略小于孔型基圓直徑的刀片在輥身上切出軋槽形狀。然后采用CBN 刀具按照數控加工程序循環加工。切削用量根據加工孔型的不同部位,采用不同的參數。一般切削 深 度 選 擇 為 0. 3 mm ~ 0. 4 mm,切 削 速 度60 m / min ~ 80 m / min,進給量在加工程序編制中根據需要設置,輥環部位為 0.8 mm/r 左右,孔型槽口圓弧部位 0.3 mm/r ~0.5 mm/r,孔型槽底( 基圓大圓弧) 為 0.3 mm/r ~ 0.4 mm/r,進行精加工。軋輥軋槽不同部位示意圖如圖 1 所示。
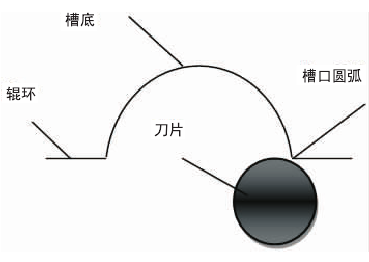
圖 1 軋輥軋槽的不同部位
3.2 孔型加工常見問題
3.2.1 孔型不符合樣板或尺寸精度
( 1) 槽底有縫隙。可適當降低孔型精加工的進給量,或在數控加工程序中減小刀具補償。
( 2) 槽型不對稱,一側縫隙大。需更換新刀片,若問題仍然存在,就考慮在程序中增加絲杠補償值。
( 3) 軋槽深度不夠。若排除刀具磨損,就降低槽底圓弧加工的進給量或適當增加刀具補償值。
3.2.2 刀具損壞形式
( 1) 崩刃。在切削刃上產生的幾個小缺口或崩掉一小塊是常見的一種損壞形式。如微崩刃的刀具在允許的磨損限度內還能繼續切削,超差則需要更換,并適當降低切削用量。
( 2) 碎斷。一般為刀具磨損后材料疲勞未及時更換或沖擊載荷過大造成的,需要減小進給量。
( 3) 剝落。刀片在前刀面上產生貝殼狀的剝落。是由于切削速度與進給量選擇不匹配導致的,適當提高切削速度、減小進給量。
3.3 橫肋銑削加工( 以 XK500C 多功能數控螺紋銑床為例)
在高速鋼軋輥的加工橫肋時,建議選用飛刀銑床( 如 XK9350 或 XK500 系列) ,在飛刀工位銑橫肋,在擺頭工位加工商標字符。裝夾刀桿后調整刀頭位置,采用專用孔型對中樣板進行對正調整( 如圖 2 所示) ,將刀桿上的刀頭、樣板與孔型調整到一條直線上,確認刀頭對準基圓孔型正中后,取下對中樣板,將刀退出。啟動加工程序,采用手動( 手搖脈沖器) 緩慢進刀,直到刀頭接觸到槽底并產生銑削劃痕,通過劃痕檢查確認對刀的準確性,如果刀頭仍然不對中,同樣采用手輪進行微調。
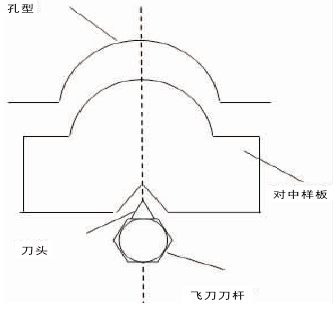
圖2 孔型加工刀頭對中示意圖
銑刀頭材質采用 H06 或 6EF 牌號,根據高速鋼軋輥材質軟硬程度,一般銑削加工進給量選擇0.03 mm / r ~ 0.05 mm / r,勤檢查刀頭磨損情況,及時提前更換,避免刀具磨損加工阻力增大,損壞刀具,增加加工成本。
商標字符加工時,先將機床加工方式調整到擺頭方式,對刀方式同銑橫肋相同,采用 Ф8 mm ~Ф10 mm棒刀,一次加工夠標準深度,字體大小及間距在加工程序中設定或修改。
4、 軋輥裝夾方式及機床要求
高速鋼軋輥裝夾采用四爪重型卡盤或過渡套筒,加上尾座回轉套筒式大頂尖,利用兩頂一夾的裝夾方式。目前棒線在用軋機多采用軋輥圓頭端大螺栓固定,所以軋輥圓頭中心孔內部往往是一個M48 mm或更大的螺絲孔,這就需要尾座頂尖定制為傘狀回轉結構,增加裝夾剛性。傳動端為了便于萬向節套筒裝卸方便,加工倒角大,標準卡爪卡不到傳動端平面上,這就需要使用過度套筒,套筒內孔要大于輥頭尺寸,圓周上安裝4 ~ 6條螺栓,用于橢圓度微調。數控軋輥加工要求機床剛性好,安裝牢固,減少周圍設備對機床的震動影響。軋輥裝夾牢固后,機床刀臺對刀具的固定同樣需要足夠的剛性,在滿足孔型最小圓弧的前提下,盡量使用大尺寸刀桿。當刀桿伸出較長時,需要安裝輔助刀頂,支撐刀具彈性變形。
在飛刀銑床上進行橫肋加工時,支承銅塊間隙不宜過大,以確保飛刀刀桿剛性。加工過程中及時調整支承銅塊磨損后與刀桿的間隙,防止刀桿折斷。
5 、高速鋼軋輥使用
高速鋼軋輥在使用過程中,輥身冷卻要求使用干凈、低溫水,既要保證水壓,又要確保水量。從而避免過熱導致輥身產生熱裂紋,以及熱裂紋的擴展造成輥身剝落,同時減少輥身溫度過高,造成的輥身組織發生相變。理想的冷卻系統是對軋槽呈環狀分布多個噴嘴,如圖 3 所示。保證向軋槽噴射出持續、充足的水流。一般水溫不超 40 ℃,水壓控制在 0.4 MPa ~0.6 MPa,單槽水量不低于 300 L/min ~500 L/min,保證有 70%~ 80%的水量在出口側,水流要對準軋槽,避免散射。另外高速鋼軋輥的熱裂敏感度較高,在軋輥與紅鋼接觸前,需提前打開冷卻水,對軋槽進行冷卻。
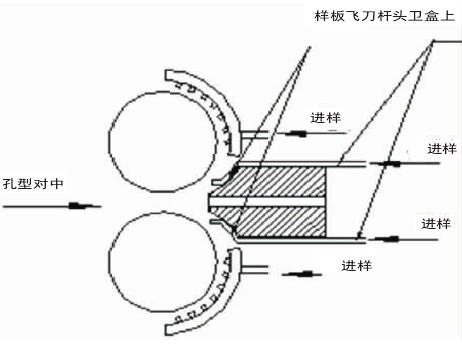
圖 3 冷卻水管
當發生卡鋼或堆鋼時,應繼續給水冷卻,使軋材及軋槽溫度冷卻下來后再停水,并將堆積在軋槽內的軋件移開。事故處理后再次生產時,如果軋槽溫度高于 60 ℃,建議更換槽孔,而且要隔 2 個槽。
6 、結束語
高速鋼軋輥的高硬耐磨性能,同等軋制條件下,與冷硬鑄鐵軋輥和高鎳鉻復合鑄鐵軋輥相比,磨損量更小,單槽軋制量成倍增加,且能夠大大改善鋼材表面質量,有效控制負差尺寸精度,在線棒材機組的優越性日益凸顯。但是高速鋼軋輥的加工刀具材質是制約其發展的一大瓶頸,隨著 CBN 刀具材質的持續升級,通過合理的加工工藝,在機床剛性滿足加工條件下,加工難度會逐漸降低,加工效率將得到進一步提升,同時高速鋼軋輥的冷卻方式也將隨之改進。為此,高速鋼軋輥的推廣應用前景廣闊,必將帶動高速鋼軋輥優勢發揮到極致,推動軋鋼生產裝備的再次飛躍。
投稿箱:
如果您有機床行業、企業相關新聞稿件發表,或進行資訊合作,歡迎聯系本網編輯部, 郵箱:skjcsc@vip.sina.com
如果您有機床行業、企業相關新聞稿件發表,或進行資訊合作,歡迎聯系本網編輯部, 郵箱:skjcsc@vip.sina.com
更多相關信息