絲杠磨損對數控機床進給系統摩擦特性的影響研究
2021-8-24 來源:東方電氣集團東方電機 華中科技大學 作者:陳文平 潘捷
摘要: 摩擦是影響數控機床進給系統傳動精度的主要因素之一。絲杠磨損會改變進給系統摩擦,降低其傳動精度,影響加工產品質量。本文針對絲杠磨損引起的摩擦特性變化,基于 Stribeck 摩擦模型對比分析了絲杠未磨損和磨損區域的摩擦曲線。結果表明: 絲杠磨損后中低速階段的摩擦呈現強烈非線性,與 Stribeck 模型描述不相符; 模型相對誤差高達 13. 0% ,遠高于未磨損區域的 3. 2% 。因此,摩擦特性的變化能反映絲杠磨損狀態變化。
關鍵詞: 數控機床; 滾珠絲杠; 磨損; 摩擦特性
1、引言
絲杠長時間使用時,受工件的切削負載沖擊和零部件間的摩擦等因素影響,滾道表面金屬疲勞脫落,滾珠與滾道間接觸發生改變,造成進給系統摩擦特性變化。摩擦的存在降低了工作臺運動的平穩性,使跟隨誤差偏大。
對于摩擦引起的運動精度問題,學者們多通過建立精確的摩擦模型來估算摩擦,并以此為基礎進行摩擦補償,以減小摩擦的影響。傅瑩等[1] 基于LuGre 摩擦模型,建立機器人轉動關節的摩擦模型,并通過實驗驗證了模型的正確性。Shubo Wang等[2]針對伺服系統的摩擦特性,建立非線性連續可微摩擦模型,并提出相應的自適應補償方法來提高系統的控制性能。Alexander Keck 等[3]針對線性驅動軸的摩擦,建立 ElastoPlastic 摩擦模型,并作為摩擦前饋補償的參考來提高系統運動性能。ZhangLibin 等[4]以 CFSM 模型來描述機器人關節的滯后效應,與 Stribeck 模型相比,提高了慢動作機器人關節扭矩的預測精度。Qing Pan 等[5]針對液壓系統的摩擦,結合滯后薄膜動力學 和 Bouc-Wen 模型對Stribeck 和 LuGre 模型進行修正,實驗結果表明,在流體潤滑狀態下,修正后的模型在描述摩擦力-速度環的滯后行為方面更精確。陳浩等[6]針對直線電機滑臺的摩擦特性,提出考慮加速度影響的 Stribeck 摩擦模型,并通過實驗驗證摩擦模型的準確性。上述研究多是針對特定系統,采用相應模型去描述系統的摩擦特性,但是絲杠磨損引起的摩擦變化尚未可知,摩擦模型能否適用還有待驗證。
為探究絲杠磨損對進給系統摩擦的影響,本文在絲杠特性測試平臺上設計相關實驗,通過絲杠磨損和未磨損區域實測摩擦力矩的對比分析,得到絲杠磨損對進給系統摩擦的影響規律。
2、經典摩擦模型
LuGre 模型是目前應用較為廣泛的摩擦力模型,該模型利用摩擦接觸面間彈性鬃毛形變的平均量來描述摩擦的動態行為[7]。如圖 1 所示,將兩接觸面看作是充滿彈性鬃毛的剛性表面,接觸面產生相對位移后,接觸面上鬃毛發生不同程度變形,此時接觸摩擦是鬃毛彈性變形產生回復力的合力。
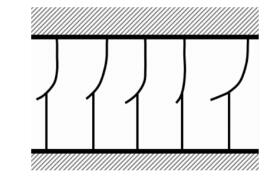
圖 1 LuGre 模型中的接觸鬃毛
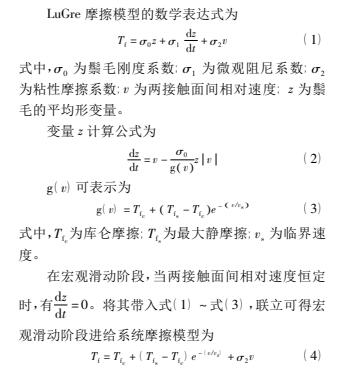
該模型也是 Stribeck 模型。在速度較低時,摩擦力與速度呈非線性關系,摩擦力隨速度增大而先減小后增大; 在速度較高時,摩擦力與速度幾乎呈線性關系。Stribeck 模型曲線變化見圖 2。
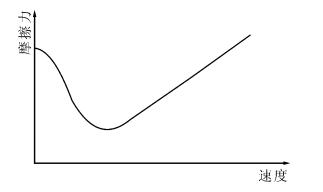
圖 2 Stribeck 模型曲線變化
3、絲杠特性測試平臺
在絲杠特性測試平臺上開展相關研究工作(見圖3) 。由圖可知,控制系統主要有 PMAC 運動控制卡和安川∑7 系列伺服驅動器,機械組成部分有安川∑7 系列伺服電機、梅花形聯軸器、軸承座、Rexroth 滾珠絲杠副、直線導軌和工作臺。測試平臺配有多種傳感器,見圖 3b 橢圓框。由圖可知: 在兩聯軸器間安裝有 Kistler 4501A100R 扭矩傳感器,用于測量絲杠的扭矩信號; 在直線導軌旁安裝有海德漢公司的 LS477 光柵尺,用于測量工作臺的位置; 絲杠螺母上貼有溫度傳感器,用于實時監測絲杠螺母的溫度。
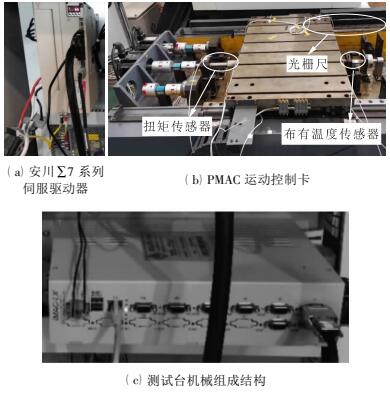
圖 3 絲杠特性測試平臺
測試平臺上安裝的絲杠在150~300mm 區域滾道表面磨損嚴重,并在長時間放置后該區域已經出現銹蝕(見圖4b) 。由圖 4 可知,絲杠未磨損區域的滾道表面光滑,而磨損區域的滾道表面存在許多金屬銹斑,且分布不均勻。
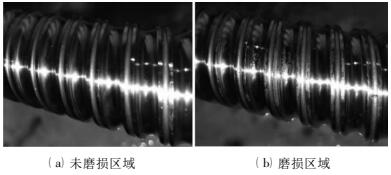
圖4 絲杠未磨損區域和磨損區域比較
4、絲杠磨損對摩擦的影響分析
測試平臺中,安裝在不同位置上的絲杠磨損程度不同,可用于對比分析絲杠磨損對摩擦的影響。為得到進給系統的摩擦曲線,在測試平臺上進行多組恒速空運行實驗。工作臺的運動速度為 60 ~20000mm /min,且速度間隔不等,共計進行 70 組實驗。為保證實驗過程進給系統各零部件間充分潤滑,在實驗前或泵油后令工作臺先往返運動多次。
為降低溫度變化對摩擦力矩測量的影響,實驗過程采用 Agilent 的 34972A 數據采集儀對螺母溫度進行實時監控,以保證實驗溫度波動范圍較小。處理數據時,絲杠兩端預留一定距離,以減小加減速和絲杠反向間隙對摩擦力矩的影響。取絲杠行程 50~ 450mm 的數據作為有效數據信號,并將其按位置區間劃分為若干段,分別統計速度和絲杠扭矩信號均值。取絲杠未磨損區域和絲杠磨損區域的實測摩擦力矩進行比較,結果見圖 5。
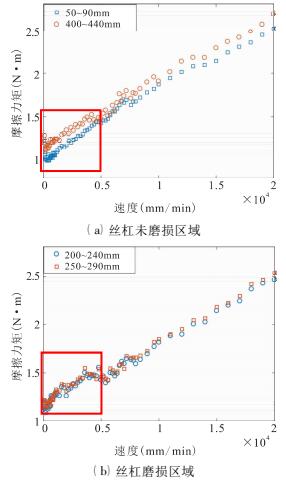
圖 5 絲杠未磨損區域和磨損區域的實測摩擦力矩比較
由圖 5 可以看出,絲杠磨損后進給系統的摩擦曲線出現明顯分段。在中低速階段,絲杠磨損區域的摩擦曲線較未磨損區域表現出強烈的非線性,這與 Stribeck 模型曲線不符; 在高速階段,兩者趨勢相同,摩擦力矩與速度幾乎呈線性關系,這與高速階段Stribeck 模型曲線相一致。由此可知,在中低速階段絲杠磨損對進給系統的摩擦有較大影響。
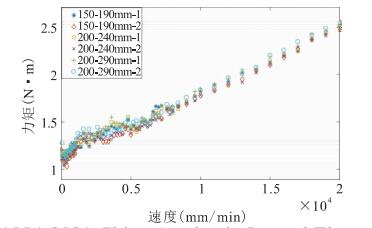
圖 6 絲杠磨損區域的實測摩擦力矩
圖 6 為絲杠磨損區域的實測摩擦力矩。摩擦特性測試平臺進給系統的速度分割點選取可參考圖 6。可知,摩擦曲線的速度分割點在 5000mm /min 左右。因此,本文選取 5000mm /min 為速度分割點。
以 Stribeck 摩擦模型作為基礎,利用遺傳算法對中低速階段和高速階段的摩擦力矩和速度進行參數辨識,結果見圖 7 和圖 8。由圖 7 可知: 在中低速階段,絲杠未磨損區域的實測摩擦力矩隨速度提升先減小后增大,增長速率幾乎保持穩定,這與 Stribeck 模型描述相符,模型最大相對誤差為 3. 2% ; 絲杠磨損區域的實測摩擦力矩隨著速度提升先減小后逐漸增大,但是增長速率卻逐漸減小,摩擦曲線趨于平緩,這與 Stribeck 模型描述不符,此時模型最大相對誤差達 12. 9% 。由圖 8 可知,在高速階段,絲杠未磨損區域和磨損區域的實測摩擦力矩與速度幾乎呈線 性 關 系,最大模型相對誤差分別 3. 3% 和3. 5% ,因此 Stribeck 摩擦模型可以描述高速階段實測摩擦力矩的變化。
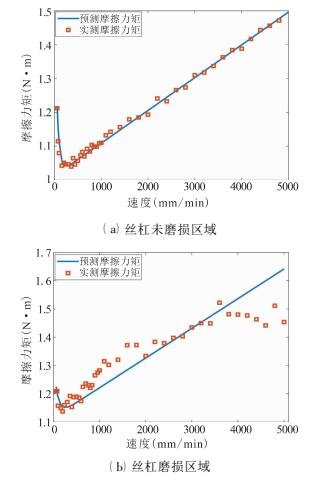
圖7 中低速階段摩擦力矩的預測值與實測值比較
對不同位置上的實測摩擦力矩和速度數據進行參數辨識,中低速階段的模型及最大相對誤差見表1。由表 1 可知,受絲杠磨損影響,中低速階段 Stribeck 摩擦模型無法描述磨損區域的摩擦變化,其最大相對誤差達 13.0% ,遠高于未磨損區域的最大相對誤差 3.2% 。

圖 8 高速階段摩擦力矩的預測值與實測值比較
表 1 中低速階段摩擦模型及其最大誤差
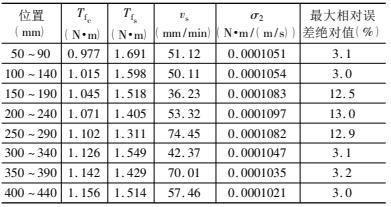
表 2 高速階段摩擦模型及其最大誤差
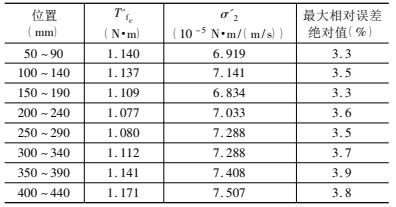
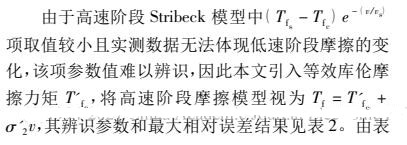
可知,絲杠磨損對摩擦的影響較小,經典摩擦模型可以描述摩擦力矩的變化趨勢,模型相對誤差在 4. 0%以下。在高速階段,由于潤滑油在絲杠轉速較高時會在接觸面間形成動壓油膜,絲杠磨損引起表面質量的改變對摩擦特性的影響明顯降低。
5、結語
本文針對絲杠磨損引起的摩擦變化,通過絲杠特性測試平臺的相關實驗數據,以 Striebck 摩擦模型為基礎,對比分析了絲杠磨損和未磨損區域的摩擦曲線,得到絲杠磨損主要在中低速階段對進給系統的摩擦影響較大,且摩擦表現為非線性,這時經典Stribeck 模型無法描述其摩擦力矩的變化,模型相對誤差達 13.00% ,遠高于未磨損區域的模型誤差3.2% 。后續可對絲杠磨損狀態下的摩擦特性進行建模,為摩擦補償提供參考來提高傳動精度。也可以結合大量實驗數據,利用摩擦特性的改變來表征絲杠的狀態改變。
投稿箱:
如果您有機床行業、企業相關新聞稿件發表,或進行資訊合作,歡迎聯系本網編輯部, 郵箱:skjcsc@vip.sina.com
如果您有機床行業、企業相關新聞稿件發表,或進行資訊合作,歡迎聯系本網編輯部, 郵箱:skjcsc@vip.sina.com
更多相關信息