軌道交通用大型鋁材構件數控龍門加工中心研制
2021-2-8 來源: 作者:
摘要:開發了一種適用于軌道交通車輛車廂用大型鋁材構件加工的高速、精密數控龍門五軸加工中心。由可行性試驗和有限元分析優化了 28m 超長分段床身結構以及由龍門框架、滑板工作臺、高速電主軸、多功能刀庫等組成的龍門加工中心整體結構,得出了電主軸輸出功率、扭矩、轉速適配表對控制系統進行二次開發,研發了夾緊位置的智能定位、自動夾緊、多點自動位置優化的智能夾具,提高了機床的高速移動速度和加工精度。
關鍵詞:軌道交通車輛 鋁型材構件 數控龍門加工中心
我國軌道交通制造業呈逐年高速增長的態勢,新一輪的高鐵、動車、地鐵的建設項目正在國內外積極展開。其中,為了保證高速行駛平穩性和可靠性等,高鐵、動車和地鐵等軌道交通車輛用的車廂廂板、底板、裙板以及邊梁等長大類零件不允許拼接,均采用整體式結構[1]。例如:如圖 1所示的車輛用車廂整體結構;如圖 2 所示的動車車廂廂板的大型薄壁型腔結構,其鋁合金構件的長度達 23.9m制造車輛車廂用零部件所需的關鍵加工設備均從國外進口,特別是目前我國引進的車輛車廂用超大型鋁材構件加工裝備的軟件升級、二次開發以及與其他 CAD/CAM 軟件的兼容性上都被設置了層層障礙,并且這些產品形成的技術標準也很難與我國現行的行業標準兼容。面對不斷發展的軌道交通用車廂等零部件的國際化需求,配套供應商的現有產能遠遠不能滿足市場的需求,嚴重制約了我國軌道交通車輛的快速發展。市場迫切需要開發一種能替代進口的軌道交通車輛車廂用大型鋁材構件的加工裝備,以滿足我國快速增長的軌道交通裝備制造的需求。為此,本文開發了一種適用于軌道交通車輛車廂用大型鋁材構件加工的高速、精密數控龍門五軸加工中心。
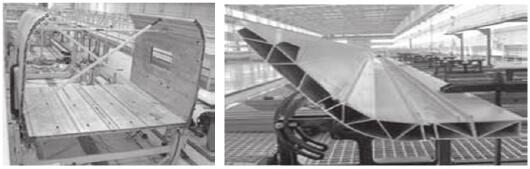
圖1 軌道交通車輛 用車廂整體結構 圖 2 大型薄壁型腔結構的鋁材構件斷面
1、數控龍門五軸加工中心總體結構
為滿足圖 1、圖 2 的大型鋁材構件的加工,開發的數控龍門五軸加工中心的結構如圖 3 所示。它主要由超長分段床身、龍門框架、移動滑板、高速電主軸、多功能刀庫、適用于薄壁型腔鋁材構件的自動夾緊、多點自動定位的智能夾具以及采用西門子控制器的數控系統等組成。作為加工中心的基礎平臺,床身左右兩側安裝有 X 向導軌和移動齒條。
X 向導軌上安裝龍門框架,龍門框架下方的齒輪齒條機構驅動其沿 X 向前后移動。Y 向導軌上安裝滑板工作臺,Y 軸絲杠驅動下可以沿 Y 向左右移動。滑板工作臺的Z向導軌滑塊和絲杠驅動電主軸滑板上下移動。電主軸具有可繞 Z 軸旋轉的 C 軸和可繞 Y 軸旋轉的 B 軸,共同完成雙擺運動。在龍門框架的左下方有旋轉式多功能刀庫。加工中心工作時,電主軸按設定速度完成刀具的旋轉主運動,由 X、Y、Z、B、C 這 5 個伺服軸共同驅動雙軸擺頭的移動和擺轉,實現五軸聯動,完成全行程范圍內空間任意角度和位置的加工。
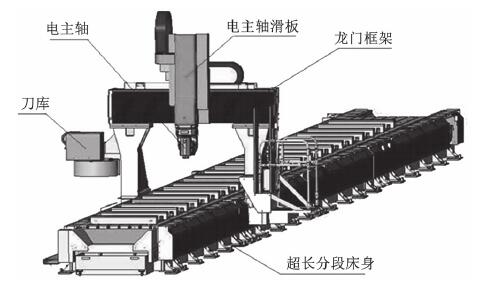
圖 3 大型鋁材構件數數控龍門加工中心結構示意
2、龍門五軸加工中心的關鍵零部件結構
2.1 28m 超長分段床身
圖 4 是本立項提出的 28m 超長分段床身的結構。為便于床身加工,它分成 4 段節。為了保證床身的強度、剛度和抗扭轉能力,研發的主要內容包括:分段床身的加工方法、連接方式及對接精度;如何降低對接裝配的難度,減少對接時間;由試驗和有限元分析,優化床身的強度、剛度和抗扭轉能力,在滿足剛性、抗扭鉆要求的前提下進行超長床身的輕量化設計。
(1)在實驗的基礎上,采用有限元(ANSYS)軟件分析 28m 床身的強度、剛度和穩定性,檢查和鑒定床身結構的合理性。
(2)研發一種分段床身對接方法。在床身的內側和外側分別固定一套連接裝置,以分段床身的主導軌一側安裝面為定位基準、副導軌為自由浮動的床身定位方法,并通過激光干涉儀、光學準直儀等實時確認多段床身的平行度和重合度。對接后的床身平行度和重合度分別達到了±0.02mm,滿足床身導軌的使用要求,表明本文提出的床身對接方法裝配精度高且簡單可行。
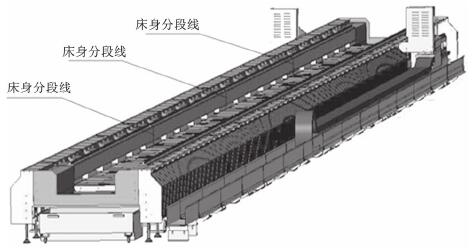
圖 4 28m 超長分段對接床身結構圖
2.2 龍門框架及其附屬的滑板工作臺、電主軸等整體結構
除圖 4 的加工中心分段床身之外,圖 5 的龍門加工中心整體結構主要由龍門框架、電主軸滑板工作臺、高速電主軸以及多功能刀庫等組成。該加工中心整體位于如圖 4 所示的床身導軌之上。由于動車車廂廂板等大型加工件長度大,龍門加工中心工作狀態時的固有振動特性等是評價其工作平穩性和提高加工精度的重要指標。因此,對龍門加工中心整體結構進行結構設計和模態分析獲得其模態特性,是龍門加工中心整體結構優化設計必要的技術手段。圖 6 是建立的龍門加工中心整體結構的有限元模型。有限元網格設定為綁定接觸,在接觸面或接觸邊之間不存在切向的相對滑動或法向的相對分離,以使得接觸面上網格節點錯開,減少網格數量。選定龍門加工中心的雙立柱、橫梁和電主軸等零部件的材料為結構鋼,彈性模量為200GPa,密度為 7850kg/m3,泊松比為 0.3。計算時,考慮到龍門框架及其附屬的滑板工作臺、電主軸等整體結構自重產生的預應力,采用帶預應力的模態分析方法,即先對整個加工中心進行預應力分析,再以該預應力分析結果作為模態分析的初始和邊界條件進行了模態分析,得到了龍門加工中心整體結構的前六階模態頻率及振動特性等,圖7 和圖 8 分別是第 5 階和第 6 階模態振型[2]。將上述分析結果與電主軸電機頻率比較,可知電主軸電機的頻率和模態分析中的第 6 階模態頻率比較接近。因此,為避免高速主軸電機與龍門加工中心整體結構產生共振,有必要對龍門框架、滑板工作臺等進行相應的結構改進。改進后的整體結構提高了機床移動速度和響應速度,保證了高速切削穩定性。
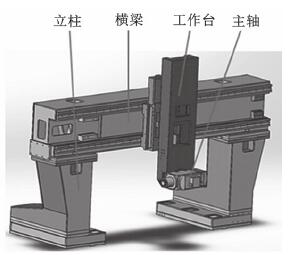
圖 5 龍門加工中心整體結構

圖 6 龍門加工中心有限元模型
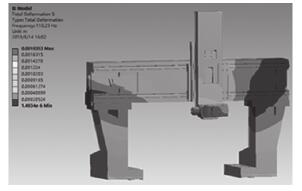
圖 7 第 5 階振型(電主軸振動)
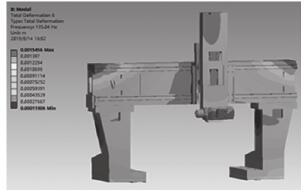
圖 8 第 6 階振型(電主軸振動、雙立柱扭擺)
2.3 高速電主軸運轉參數
使用三坐標測量儀、粗糙度測量儀以及扭矩儀等檢測設備,測定主軸轉速、扭矩、進給量之間的配合關系,并通過可行性試驗和仿真分析確認高速電主軸運轉參數的適配性,得出了表 1 所示的高速電主軸輸出功率、扭矩、轉速適配表,優化了不同轉速下的電主軸輸出關系。表 1 中,S1為額定輸出,S6為 60% 超載輸出。
2.4 自動夾緊、多點自動位置優化的智能夾具
圖 9 是研發的適用于薄壁型腔的大型鋁材構件的自動夾緊、多點自動位置優化的智能夾具。為防止軌道交通用大型鋁材構件由于長度過長造成彎曲變形,有必要采用多組可移動夾具對工件進行支撐。按照工藝要求擺放各組夾具工作效率低,且易造成切削刀具和工作臺夾具干涉。為此,針對不同規格的大型鋁材構件,在實驗驗證的基礎上,采用 Adams 進行仿真分析,在非加工區域確定最優夾緊點的位置。借助 Simulink 的框圖設計環境,對控制系統進行二次開發,由專用軟件給出準確夾具位置,由數控系統的X 軸驅動夾緊撥快,拖動每組夾具移動到預定位置,實現根據圖紙工藝自動撥動夾具并優化夾具位置的功能。
表 1 高速電主軸輸出功率、扭矩、轉速適配表

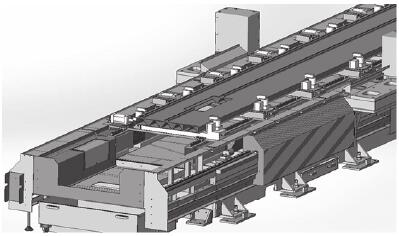
圖 9 機床智能夾具結構圖
2.5 控制系統的軟件二次開發
原有的加工程序是由經驗豐富的工藝員依據待加工件圖紙手工編制而成。為提高數控加工中心的自動化程度,本文在西門子控制系統基礎上二次開發了一種能根據工件圖紙自動生成加工程序的軟件。針對大型鋁型材構件以銑削、鉆削為主要加工工藝,加工圖元以孔槽、立筋去除為主要技術特征,并且在鋁型材多個面都有加工要求的特點,開發了針對大型鋁型材構件的任意角度均能實現以上工藝功能的 CAM 軟件。將常用的圖元及圖元組模塊化,需要時直接調用,采用填表式參數對話框,對所有切削工藝參數及位置切削參數均采用彈出式圖表菜單形式,可直接填寫參數,直觀易懂,保障了機床較高的工作效率和加工精度。同時,通過軟件功能的擴展,提高了機床的操控便利性和人際交互界面的友好程度。
3、結語
本文研發了一種適用于軌道交通車輛車廂用大型鋁材構件加工的高速、精密數控龍門五軸加工中心。由可行性試驗和有限元分析優化了 28m 超長分段床身結構、由龍門框架、滑板工作臺、高速電主軸、多功能刀庫等組成的門加工中心整體結構,得出了電主軸輸出功率、扭矩、轉速適配表對控制系統進行二次開發。通過軟件功能的擴展,實現了夾緊位置的智能定位、自動夾緊,提高了機床的高速移動速度、加工精度以及人機交互界面的友好程度。完成的產品主要技術指標如下:分段床身總長度 28m;大型鋁材構件加工長度≥ 26m;最大加工寬度為 1100mm;電主軸最高轉速為 18000r/m;最大輸出扭矩為 20.9/6000N·m;最大切削速度為 5m/min;最大快移速度為 55/30/20m/min。
來源:
周倩劉 新海 亓愛林 閆法義 鄭明剛 許伯彥
濟南天辰鋁機股份有限公司 山東建筑大學 機電工程學院
投稿箱:
如果您有機床行業、企業相關新聞稿件發表,或進行資訊合作,歡迎聯系本網編輯部, 郵箱:skjcsc@vip.sina.com
如果您有機床行業、企業相關新聞稿件發表,或進行資訊合作,歡迎聯系本網編輯部, 郵箱:skjcsc@vip.sina.com
更多相關信息