基于五軸聯動加工技術的葉輪加工方法分析
2021-5-24 來源:桂林航天工業學院 廣西桂林 作者:鐘國成
摘要: 葉輪是動力機械中不可缺少的重要部件,已經被廣泛應用于汽車制造、航空航天等多個領域。由于葉輪本身的結構復雜性較強,應用傳統加工技術困難性大,性價比不高。五軸聯動加工技術可有效避免刀具干涉,提升表面質量,增強加工精度,性價比高,目前已經逐漸取代傳統加工技術。本文主要討論了基于五軸聯動加工技術的葉輪加工思路與具體加工方法,以供參考。
關鍵詞: 五軸聯動加工技術; 葉輪加工; 方法
所謂五軸聯動加工技術,簡單來說就是一種在 CNC 控制下五個坐標軸協調運動加工零件的加工技術,它以計算機網絡技術作為主要的技術支撐。隨著加工技術的持續發展,虛擬仿真技術逐漸被應用于五軸聯動加工中,給后者加工質量與精度的提升產生了重大的積極影響。基于五軸聯動加工技術加工葉輪,為避免刀具干涉、碰撞,先在仿真環境中構建葉輪模型,經多次試驗后確定切削參數,并對其進行驗證,再將參數錄入五軸聯動數控機床,葉輪一次成型。
這不僅能提升葉輪加工質量與精度,也能減少加工葉輪的必要時間,同時做到資源的有效節約。那么,基于五軸聯動加工技術的葉輪加工具體方法是什么樣的呢? 以下就是筆者對此的分析與論述。
一、基于五軸聯動加工技術的葉輪加工思路
( 一) 工藝流程葉輪加工主要是加工葉片與流道,由于葉片通常為扭曲狀,而流道則很狹窄,所以加工中常有干涉、過切、碰刀現象。為了實現對這些現象的有效規避,并保證加工精度,選擇分階段濟鋼。第一階段,葉片、流道粗加工,主要采用五軸曲線加工法,對于流道,先進行結構分割后再加工; 第二階段,葉片精加工與清根處理,主要采用五軸側銑方式; 第三階段,流道精加工,主要采用五軸限制面加工法。
( 二) 五軸加工刀具路徑規劃
( 1) 粗加工刀具。
第一階段粗加工從流道深度延伸的方向進行分層加工,合理連接每層的刀具路徑,使之構成整體加工路徑。由于流道普遍為梯形,入口窄出口寬,所以選擇倒“Y”型路徑,這不僅可縮小切削路徑長度,也能有效提升加工效率。在此過程中,先根據刀具軌跡點確定開槽刀位,再以刀具直徑
、開槽刀位至偏置面弧長等確定擴槽走刀行數,基于此確定行距,從而構建刀軸矢量圖。
( 2) 精加工刀具。
對于選擇五軸側銑方式的葉片曲面,確定以葉片上下曲線為導向線,從而保證切削刃與被加工曲面相切。由于流道面對加工精度及表面順滑度有極高要求,所以通過等參數線法進行刀具路徑的規劃。先沿一定方向將流道曲面離散成點,再根據流道走向連接這些點,構成刀具路徑。以同等方法生成的等參數刀具路徑,就是刀軸矢量控制線。
( 三) 刀具選擇
刀具的選擇應充分考慮加工目的、加工工藝要求、毛坯材料、允許切削面、刀具特性等多方面的因素。粗加工的主要目的在于切削可能多的材料,為達到這一目的,就要選擇直徑較大的刀具,而流道的加工需要刀具直徑小于兩葉片間最小距離。那么,粗加工選擇球頭銑刀,精加工選擇球頭刀,兩種刀皆為硬質合金涂層。
二、基于五軸聯動加工技術的葉輪加工方法
( 一) 數控編程規劃( 附工程圖)選擇支持復雜五軸加工、具有軌跡批處理功能、攜帶后置處理模塊的軟件進行數控編程,如 CAXA 制造工程師、北京精雕軟件等。
附工程圖:
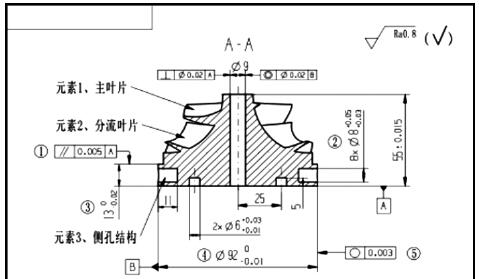
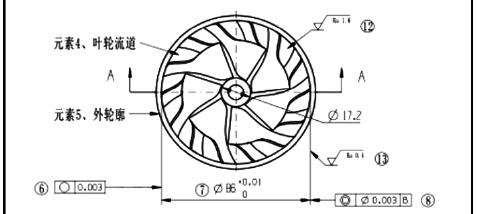
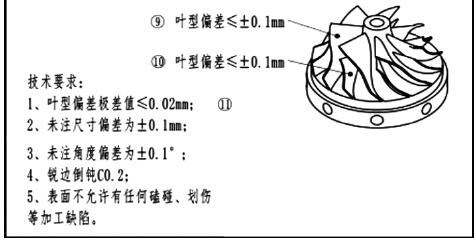
葉片流道粗加工階段,根據倒“Y”型刀具路徑,以葉片上緣高度為建構分成面的基準,對流道面進行等距劃分,從而形成流道代替面。基于此,確定最大層深,先定位加工輔助面母線,再通過旋轉面方面建構加工輔助面。在明確開槽到位的情況下,以刀具精度、開槽刀位至偏執面出氣口弧長確定走刀行數,并設定相應的速度參數。為了防止撞刀、干涉等現象的發生,以工件大小及其原點位置確定相應的高度參數。葉片精加工階段,CAXA 環境中側銑導線是以刀位點為定位點的,那么刀具就極大可能出現刀尖過切,因而要手動設置相應的偏置參數。建構好等距面后,將其與葉片曲面交線確定為葉根線加工導線。
基于對加工精度及撞刀、干涉現象的充分考慮,設置刀具運轉中的拓展余量參數及切削速度參數。流道精加工階段,確定限制面與加工面,根據精度要求設置切削參數。根據單個刀具軌跡生成全部葉輪刀具軌跡,確定仿真效果。
( 二) 后置處理
在生成刀具軌跡的過程中,CAXA 軟件自動形成相應的文件,這些文件需要通過后置處理才能被虛擬數控機床讀取。后置處理中,結合虛擬數控機床特性與功能,確定最適宜的后置處理器,該工具可直接進行從文件向機床可讀取代碼的轉換。后置處理器的開發,遵循“數控系統選擇———機床類型選擇( 運動學設置與機床組件配置) ———機床參數設置( 運動軸行程等) ———其他控制程序設置( 起止刀具進退等) ———子程序調用( 鉆孔、循環控制等) ———宏程序編制”,同時確保刀位點數值和機床運動的一致性。
( 三) 設計仿真加工流程
選擇可仿真五軸聯動加工過程、有真實三維實體展示效果與 CAD/CAM 接口、能實現與其他工程軟件的嵌套運行、可驗證與優化 NC 程序的數控加工方針軟件進行仿真加工,如 VER-ICUT 等。基于 VERICUT 的葉輪仿真加工流程如下: 設置仿真機床 環 境———設 置 控 制 程 序———添 加 刀 具、毛 坯、加 工 程序———基礎參數設置———仿真———比較檢查結果———合格后進入數控現場加工( 不合格修改加工程序) 。
仿真機床環境設置中,先構建五個軸間的邏輯關系,以此作為參照設置結構樹,再根據結構樹導入不同部件的幾何模型,從而完成機床環境設置。至于幾何模型的建立,可選擇應用 UG、CAD 等軟件建模后將文件導入 VERICUT,也可選擇直接在 VERICUT 建模。處于對仿真機床模仿真實機床運作的考慮,還應設置對刀點、碰撞檢查等機床參數。
控制程序設置中,需要對控制程序進行二次開發,這主要是為了保證加工代碼與機床實際需求相符。對于換刀及五軸開關功能的實現,以 WFL M65 機床為例,這一機床的“換刀”是以“TLPREP1”與“TLCH1”代碼實現的,前者用于刀具準備,后者用于更換刀具以及調節刀軸角度,那么在仿真加工中需要加入這兩種代碼。
另外,五軸加工時,由于兩個旋轉軸共同運作,為防止刀具中心偏移,通常該機床要打開“RTCP”功能。那么在仿真加工中就要加入相應的指令代碼。
( 四) 加工
( 1) 加工程序。
先確定加工坐標系,并結合葉輪加工要求以及刀具相關數據定義刀具,再根據葉輪結構特性確定具體加工流程,基于此,選擇切削參數進行模擬加工,經多次實驗排除干涉、撞刀等問題,在 NC 程序驗證后確定實物切削參數,最后在實體的五軸聯動數控機床的計算機上錄入切削參數,并將毛坯、NC程序載入機床,通過實物加工獲得葉輪零件。
( 2) 結果檢測。
仿真加工完成后,對加工效果圖進行分析檢測,看有無過切、欠切、殘留量較多的情況,基于此,優化加工工藝,從而滿足葉輪加工要求。
( 3) NC 程序優化。
仿真完成后,通過 VERICUT 相應模塊進行 NC 程序的優化與驗證。優化過程中,設置刀具參數、工件材料、機床類型等,并對比前后程序變化。
三、結語
綜上所述,基于五軸聯動技術的葉輪加工,將虛擬仿真技術融入其中,先通過仿真獲得經驗證后的 NC 程序及最優切削參數,再將其錄入實體機床進行實物加工,可有效避免實際加工中的干涉、撞刀問題,并提升加工精度與質量。值得注意的是,仿真所獲得的葉輪模型是在理想的環境下獲得的,實際加工還得考慮機床的維護管理問題,保證機床在最接近理想環境的情況下運行。
投稿箱:
如果您有機床行業、企業相關新聞稿件發表,或進行資訊合作,歡迎聯系本網編輯部, 郵箱:skjcsc@vip.sina.com
如果您有機床行業、企業相關新聞稿件發表,或進行資訊合作,歡迎聯系本網編輯部, 郵箱:skjcsc@vip.sina.com
更多相關信息