智能、柔性、復用,一套夾具覆蓋超 40 種航空零件
2021-7-13 來源:雄克公司 作者:-
航空工業慶安公司以雄克模塊化零點快換系統加速智能化生產轉型
航空制造業一直在面對產品質量、交貨期、生產管理等嚴苛挑戰,“十四五”發展規劃中,航空工業還作出了打造“數智航空”新業態的戰略部署。作為我國唯一集航空機載武器裝備、飛行器操縱控制系統(裝置)兩大專業優勢為一體的機載設備生產企業——航空工業慶安集團有限公司(以下簡稱慶安公司),在全面進行“提質增速”、“創新生產”任務達成的同時,果斷開啟了戰略變革:由傳統加工向自動化、數字化加工轉型。從頂層設計到具體工藝,慶安公司極其注重整體生產工藝優化的可持續性,技術團隊突破以數控機床投資優化為主導的傳統理念,進一步在提升機床利用率、自動上下料等方面動腦筋,以小博大。
南京航空航天大學機電學院李亮教授曾指出:“隨著智能制造理念的實踐深入,曾一度被忽視的工裝夾具,在工藝流程中的重要性突顯,以‘小工裝’撬動整個產線自動化升級的應用更是屢見不鮮。柔性、精密、標準、智能是現代工裝夾具的發展方向,模塊化工裝應用代表了發展所趨,有利于企業加速進行深度數字化、智能化生產。”慶安公司技術團隊深諳其理,從工件裝夾這一細節工序著手,基于業內最為領先的零點定位系統對廠內某一關鍵系列零件的夾持方案進行了全面更換與優化,實現了 43 種產品的全覆蓋夾持,并計劃將這一項目的成功思路拓展到更多零件的應用中。“雄克公司是零點定位系統的領先者,它的產品性能優勢明顯,更重要的是,能結合我們現有的生產需要來定制方案,它的設計能力,還可以為我們下一步持續優化打下基礎。”慶安技術團隊相關負責人
表示。
耗時費力、品質不穩定,傳統裝夾方式急需改善
在進行裝夾工藝優化前,慶安公司技術團隊先對多款同類型的殼體零件進行了細致分類,基于各種零件不同的工藝組成情況,最終確定了一款具備典型特性的測試零件。如圖 1 所示,該款殼體零件有著鏤空的圓柱體形狀,以及左右兩側對稱且帶有圓孔的耳片結構。在原有的工藝方案中,此零件的定位基準使用的是零件內孔齒頂圓及定位工藝孔。裝夾時,選用傳統“一面兩銷”的裝夾方式,當一次裝夾后,加工零件的上表面內腔及外輪廓;加工完成后,人工換裝以加工下表面內腔;而后再拆裝兩次,完成左、右耳片輪廓及孔的加工。至整個零件加工完成,需要兩套夾具主體(如圖 2),以及 4 次人工裝夾操作。
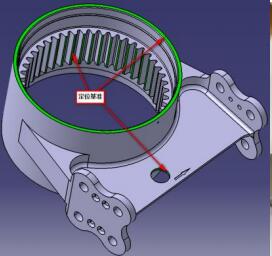
圖 1 殼體機構復雜
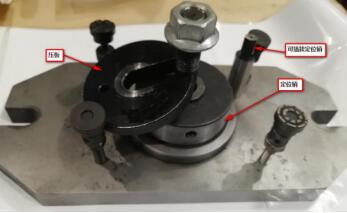
圖 2 夾具主體
“傳統裝夾的最大問題就是產品裝夾與產品換型的效率低下。以此零件為例,加工中人工裝夾的時間大概在 5 分鐘,4 次裝夾就是 20 分鐘。另外,在加工完成后需要更換另一型號零件時,由于現有夾具的齒頂圓定位芯軸與夾具本體為固定裝配,不能用于其他直徑的零件,因此需要進行包括拆卸清理、更換夾具、裝夾找正等長達 11 道工序的重新裝夾操作,所需時間更是超過 60 分鐘。”慶安公司技術團隊負責人表示,“人工裝夾時,機床必須處于停滯狀態,這也直接導致了生產效率的下降。”
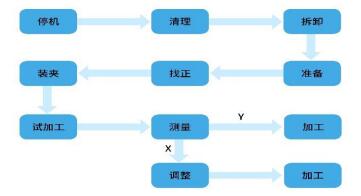
圖 3 傳統裝夾方式下產品換型流程圖
過度依賴人工裝夾,所帶來的另一大問題就是加工精度的不穩定。由于操作人員技能水平的差異,在產品換型裝夾、找正夾具精度上會產生偏差,造成定位基準不一致,由此而帶來的加工質量不穩定的情況時常出現。大量的人工干預也無法滿足慶安公司未來計劃使用機器人進行上下料的自動化需求。除此之外,還有傳統夾具通用性差所引起的夾具庫存大、成本浪費,以及可插拔定位銷易對夾具本體和銷子造成磨損,降低夾具定位精度等多種問題困擾。
全新方案設計:零點快換系統+芯軸+快換拉釘
以上提到的這些困擾還僅限于測試的一個零件,而慶安公司這一類殼體零件的種類就超過了 40 種,如何優化裝夾方案,縮短加工準備時間,提升生產效率與產品品質呢?技術團隊在多方思考與對比下選擇了零點快換系統。
零點快換系統是當前工裝夾具標準化趨勢下的一項創新技術,是機床工作臺與工件(或夾具)的一個標準接口,在數秒內,即可通過一個或多個定位銷將工件、夾持裝置、托盤與機床端的夾持系統快速緊固連接,精確地夾緊在設備中,從而提升不同工藝的轉化和設備連接的通用性,將整個制造資源的匹配最大化。
“我們非常看重雄克公司的設計能力,當我們提出改進需求后,雄克的技術力量第一時間便來到車間現場,共同進行具體裝夾方案的分析討論以及加工測試。我們不僅僅看重這一個零件的優化,而是希望能借鑒他們的專業設計能力和全球化的應用經驗,在實現該類零件提質、增速需求的同時,將模塊化工裝的思路進一步拓展至整體。” 慶安公司技術團隊負責人說道。
“我們在航空零件夾持方案的優化設計上有著豐富的經驗,慶安公司的需求比較典型,但也有其特殊性,基于零件的結構特征、加工工藝,并綜合考量生產效率、成本節約、空間布局以及慶安公司想要適應未來加工品質提升與加工需求拓展等多方因素,我們為其提供了定制化的解決方案——‘零點定位系統+芯軸+快換拉釘’夾持方案。” 項目負責人,雄克公司高級技術經理麻曉杰表示。這一夾持方案(如圖 4),在不改變原有工藝方案及定位基準的情況下,通過由基礎底座、零點定位器、液壓芯軸、零點快換拉釘和變徑套組成的工裝系統,實現一次裝夾加工 3個表面,再通過零點快換的方式,快速切換到工件反面與側面的加工工位,大大簡化了原有的裝夾流程,提升了裝夾效率與精度。
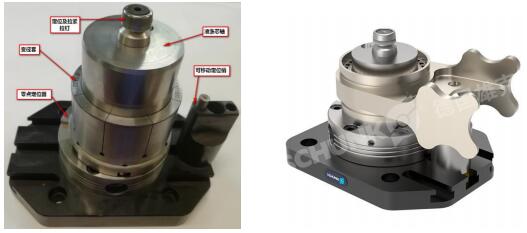
圖 4 “零點定位系統+芯軸+快換拉釘”夾持方案
零件在機床外通過液壓芯軸鎖緊后,利用零點快換方式安裝于 4 軸加工中心的工作臺上,而后只需將角向限位安裝到位,即可開始加工產品的正面輪廓。一面加工完成后,再通過簡單的 4 軸正、負向旋轉 90°,實現兩側耳片輪廓的切削加工。
產品反面特征的加工則更為便捷,也是此新方案的一大亮點。雄克技術人員根據零件的結構特征,在液壓芯軸的的正反兩側均制作了快換接口,當正面輪廓加工完成后,只需將芯軸調換 180°,即可立即對工件反面進行夾持加工,這樣創新性的設計思路不僅最大程度提升了裝夾效率,也將夾具的柔性無限拓展。當外輪廓與正反面特征均加工完成后,將夾具側置安裝在 4 軸加工中心的法蘭上,通過 4 軸的旋轉,可最后完成產品兩側耳片上斜孔的加工。在產品換型的裝夾中,對于不同齒頂圓直徑的零件也無需再更換整個夾具主體,只需在一套夾具基礎底座上增加零點快換系統和可移動定位銷,同時通過更換芯軸和芯軸的變徑套以及端面定位裝置,調整定位銷位置或更換不同規格定位銷即可實現不同零件的快速更換與夾緊。
柔性、復用的模塊化工裝帶來極致高效
通過雄克模塊化零點快換裝夾方案,工件在加工中人工裝夾的操作時間從原來的 5 分鐘縮短至 1 分鐘,在產品換型時的裝夾中,由于無需更換夾具底座并重新找正,裝夾效率顯著提高,時間從 60 分鐘大幅縮短至 10 分鐘。
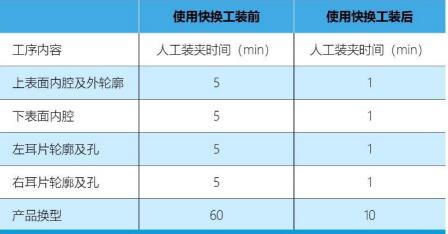
圖 5 時間對比表
同時,基于零點定位系統和液壓芯軸的配合,不同零件的換型裝夾操作可在機床外進行。在實際生產過程中,可實現一套在機內加工,一套在機外裝夾工件,如發現工件需要返工時,也可以將芯軸和工件二次裝入機床,直接加工。無需停機等待的優勢更進一步提升了機床利用率、提高了加工效率。另外,用一套夾具覆蓋 43 種同類型產品,替換原有的 28 套夾具的強大通用性,大大減少了夾具庫存,降低了成本投入,也為日后批量生產奠定了基礎。
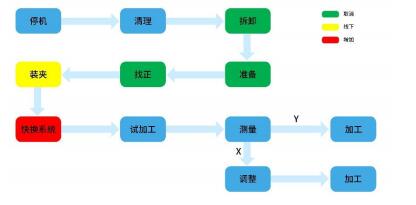
圖 6 優化后產品換型的流程
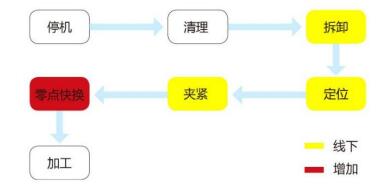
圖 7 批生產加工流程
保障加工品質,是采用雄克零點快換系統的另一大優勢。與傳統依賴人工手動裝夾、找正相比,液壓芯軸的定位精度小于 0.003mm、零點定位系統的重復精度在 0.002mm 以內,雙重精度的保障使得產品在實現快速換型的同時,工件的良率以及穩定性、經濟性都得到了大幅提升。
“慶安公司是航空機載設備的領先企業,工藝技能扎實,對于品質的要求十分嚴格,此次能夠攜手完成這一裝夾工藝優化項目,我們備感榮幸。以夾持技術的創新設計最大程度地挖掘現有設備所蘊含的生產潛能,是雄克始終致力所為的目標,此次用戶獲得滿意生產效果便是對我們的最大認可。慶安公司在方案設計之初便已要求我們要為下一步自動化升級打基礎,這樣的頂層創新能力,這樣腳踏實地的技術團隊令人佩服。”麻曉杰對此項目不無感嘆。的確,對于慶安公司而言,采用模塊化工裝技術還有一層更為深遠的意義——賦能自動化轉型升級。無論是自動化生產還是數字化技術,其所作用的對象始終是要制造的工件,整個工藝流程設置的核心也是工件在不同設備的流轉,而這一流轉過程就離不開工裝夾具的支撐。傳統的工裝夾具僅適用于人工上下料,不能滿足機器人自動化的要求,慶安公司技術團隊清晰地認識到了工裝夾具技術優化對于生產邁入智能化階段的重要性,果斷采用了前沿的智能化模塊工裝,并已將其輻射至工廠的更多應用領域。新一輪工業革命浪潮已經來襲,市場需求瞬息萬變,面對機遇和挑戰,慶安公司將持續致力智能制造、數字化生產轉型,為建設新時代航空強國貢獻力量。
投稿箱:
如果您有機床行業、企業相關新聞稿件發表,或進行資訊合作,歡迎聯系本網編輯部, 郵箱:skjcsc@vip.sina.com
如果您有機床行業、企業相關新聞稿件發表,或進行資訊合作,歡迎聯系本網編輯部, 郵箱:skjcsc@vip.sina.com
更多相關信息