高精度橋式五軸加工中心橫梁仿形工藝技術
2023-5-4 來源: 通用技術集團沈陽機床有限責任公司 作者:尚 紅 趙普金
摘要 : 現代航空航天等行業對零件精度和質量要求較高,需要加工機床具備高精度、高可靠性和精度保持性。國產設備在高精度和可靠性方面與國外先進技術水平還有一定差距,在航空航天等領域國產設備占有率低,在關鍵核心技術上還有許多 “卡脖子” 問題急需解決。高精度橋式五軸加工中心主要用于飛機部件骨架表面銑削、鉆削加工與裝配制孔。其加工能力強,尺寸規格大,定位精度高,兼容高效切削,機床具有五軸聯動功能。對機床的關鍵部件大型橫梁導軌直線度仿形加工、裝配、測量技術研究,是此類機床精度保持性的核心制造技術之一。本文通過對橫梁加工、裝配及檢測精度的制造工藝技術的實踐與總結,詳述大型橫梁的仿形加工及裝配工藝過程。
一、依據有限元分析繪出橫梁導軌受力變形曲線
高精度橋式五軸加工中心因橫梁兩端由橋梁、滑座雙支撐橫跨工作臺的結構特點,中間懸掛滑板、滑枕和五軸頭等部件,導致橫梁導軌除受自身重力外,還需承載較大的重力及傾覆力矩,實際裝配掛梁后由于重力及傾覆力矩作用橫梁產生塌腰現象。
1.Ansys靜力分析
以裝配體的形式建立橫梁三維模型,通過有限元對橫梁靜、動態性能進行分析,依據橫梁振動相對變形的振型和幅值,以及機床的工作環境和機床設計的結構力學理論,提出橫梁結構及加工的改進建議,從而對橫梁進行仿形加工。
建立橫梁裝配體三維模型,以 X 方向為垂直于橫梁向內、Y 方向為平行于橫梁向左、Z 方向為垂直于橫梁向上為正。依據有限元分析,設計大型橫梁 1# 上導軌大面、2# 上導軌立面、3#下導軌大面、4# 下導軌立面仿形曲線圖(見圖 1)。
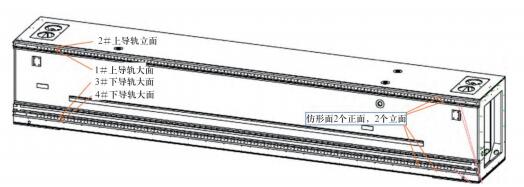
圖 1 橫梁導軌面示意圖
2.橫梁導軌仿形曲線
裝配狀態下橫梁僅受重力作用,由于受自身重力及懸掛滑板、滑枕等部件的重力導致變形,橫梁上下兩條直線導軌面中間部位變形最大,最大位置為橫梁中間上端部分 , 變形趨勢主要為橫梁中間部分下沉和繞 Y 方向扭轉。橫梁受重力和切削力共同作用,受 X/Y/Z 方向切削力情況下的整體和分方向靜力變形,最大位置均為橫梁中間上端,其中受 X 方向切削力變形明顯,主要是因為中部上端受切削力后扭轉增大 ; 受 Y 方向切削力變形不大 ; 受 Z 方向切削力變形中部上端變化明顯。橫梁的最大變形量發生在滑板移動到橫梁中間,滑枕移到下極限位置時。加工工藝根據其變形曲線仿形加工,減少滑板、滑枕在橫梁上移動時產生的直線度誤差。橫梁導軌受力變形量仿形曲線圖(見圖 2)。
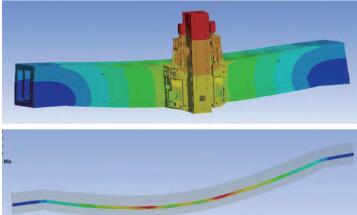
圖 2 橫梁導軌仿形曲線圖
二、橫梁仿形加工
從橫梁材料硬度、熱處理、加工、裝配及檢測精度入手,通過橫梁加工及裝配過程直線度等精度檢測數據分析,找出橫梁導軌面加工曲線及工藝方法滿足裝配精度要求。
1. 材料及熱處理
高精度橋式五軸加工中心大型橫梁材料為焊接低合金結構鋼 16Mn,零件輪廓尺寸長 × 寬 ×高為 10460×1815×1580mm,凈重 25.5 噸,標準材料 16Mn 鋼材厚度大于 50~100mm 方,抗拉強度 Rm 為 470~620N/mm2。根據硬度抗拉強度對照表德國標準 DIN50150 查得布氏硬度為143~185HBW。
大型零件材料為焊接件的由于焊接引起焊件不均勻的溫度分布,焊縫金屬的熱脹冷縮等因造成焊接殘余應力,零件在機加工之后其內部易殘存應力,所有這些內應力都必須消除。消除殘余應力最通用的方法是去應力退火,即將零件放在熱處理爐內加熱到一定溫度 (Ac1 以下 ) 和保溫一定時間,利用材料在高溫下屈服極限的降低,使內應力高的地方產生塑性流動,彈性變形逐漸減少,塑性變形逐漸增加而使應力降低。焊接件去應力退火加熱溫度為 500~550℃,保溫時間為 2~4h,爐冷至 300℃以下出爐空冷,消除加工應力退火加熱溫度為 400~550℃,保溫時間為 2~4h,爐冷或空冷。橫梁去應力退火對零件精度保持有重要作用,零件質量穩定性較好,因此大型橫梁應二次以上去應力熱處理即毛坯焊接
后及粗加工后去應力退火。
依據標準并結合實際應用繪出熱處理溫度 -時間工藝曲線圖(見圖 3)。熱處理工藝規程 :大型焊接橫梁裝爐底部墊平,入爐溫度不大于300℃,加熱升溫速度不大于 100℃ /h,加熱至500~550℃保持溫度 4h,后隨爐冷卻至 300℃以下,出爐空冷。
2. 橫梁加工工藝
大型橫梁加工工藝流程 : 毛坯( 焊接16Mn)- 毛坯去應力退火 - 劃 - 粗銑 - 時效處理(二次去應力退火)- 半精銑(放置 48h)-精銑(仿形加工)- 搖鉆 - 鉗序(清理)- 油漆。大型橫梁在加工前應劃線,照顧支撐面及直線導軌面壁厚均勻,回字內腔壁厚均勻且成矩形。粗銑選用大型龍門銑床,用可調墊鐵,以導軌面為粗加工基準,銑背面做為導軌面粗銑加工基準面,粗銑序橫梁直線導軌向上,銑出導軌形狀,去除機械加工余量,提前發現毛坯缺陷等。橫梁粗加工后要進行二次時效,去除殘余應力退火。半精銑選擇大型數控龍門鏜銑床,為避免大型橫梁吊裝、翻轉產生變形,大型橫梁應在此序以裝配狀態加工,以導軌面為裝置面,精銑橫梁支撐面做裝置面,除直線導軌、光柵尺、齒條基準面
留量外,其余防護、管路及電氣元件等結合面、螺紋孔均加工完成,保證零件相關尺寸精度。
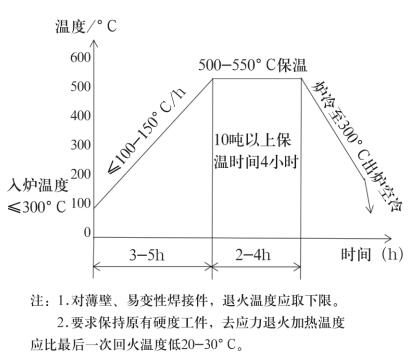
圖 3 溫度 - 時間工藝曲線圖
關鍵工序精銑序,選擇精密龍門五面加工中心,先以導軌面為裝置面,精銑橫梁支撐面做裝置面,保證支撐面平面度不大于 0.05mm。再以裝配狀態支撐面為裝置面,將四塊墊鐵按橫梁支撐面內側基面位置固定于方箱座上,自銑墊鐵鈔平,橫梁放置于四塊鈔平墊鐵上,按導軌大面找正 0.02mm,檢測各墊鐵與橫梁支撐基面間是否有縫隙,將 4 個 0.1mm 等厚銅皮放于墊鐵上,橫梁落下后,抽動銅皮不動,可以進行加工(見圖 4)。用直角頭精銑齒條安裝正、側面,檢測正面和側面直線度,通過數據曲線分析機床實際精度。按設計仿形曲線圖及機床實際精度綜合修正值編程,按程序再次加工齒條安裝正、側面驗證曲線,加工后檢測。檢測直線度與導軌設計仿形曲線一致后,仿形加工上下導軌大面、立面,同時精銑齒條面、光柵尺面等安裝基面,精銑時壓板松開不夾緊。
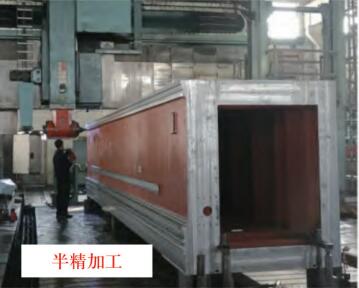
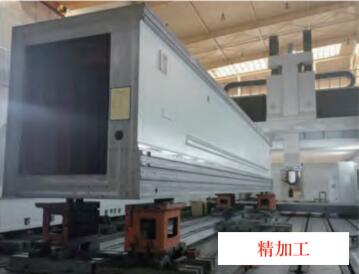
圖 4 橫梁加工示意圖
大型橫梁精加工設備采用沈陽機床自制的龍門橋式五軸加工中心 GMC50200u, 用A/C 五軸頭(刀柄 HSK-A63)直角定位精銑仿形曲線,設備精度具備 X/Y/Z 定位精度0.02/0.015/0.01mm,重復定位精度0.008mm。加工刀具 : 大面精銑用方肩面銑刀 Φ63(Z=5),立面精銑整體硬質合金立銑刀 Φ20(Z=3),液壓夾緊刀柄,切削參數均為轉速 S=1000r/min, 進給 F=285mm/min。
三、橫梁裝配
高精度橋式五軸加工中心與橫梁相關的幾何精度有:G3 項Y軸軸線運動的直線度 : ① 在YZ 垂直平面內 ; ② 在XY水平平面內允差值 :0.014/1000mm;0.035/7000mm。G4項Y軸移動的角度偏差 : ① 在 YZ垂直平面內 ( 俯 仰 ); ② 在 XZ 垂直平面內(傾斜); ③在 XY 水平面內(偏擺)允差值:0.015/1000mm;0.04/7000mm。
1. 橫梁裝配工藝
橫梁裝配工藝流程 : 橫梁精加工后入裝配 -單件直線度檢測 - 線軌裝配 -- 安裝線軌后直線度檢測 - 齒條裝配 - 光柵尺裝配 -Y 軸驅動裝配 -安裝液壓管路 - 電氣接線 - 安裝行程開關確定 Y軸行程 -Y 軸總裝直線度檢測(加修或刮研調整)-角度偏差檢測(加修或刮研調整)- 防護安裝。通常,龍門式數控機床為保證裝配后的 Y 軸運動的直線度,工藝方法根據設計變形曲線圖進行仿形加工,但因設備精度、環境溫度、材料硬度等諸多因素影響,實際銑削仿形曲線往往會隨之發生變化。橫梁精加工后轉部裝,為減少環境溫度偏差造成的直線度誤差,橫梁進部裝在安裝直線導軌前、后應復檢導軌正、側向直線度,對于直線導軌橫梁部裝檢測有兩種姿態即平放或立放檢測。平放即直線導軌大面向上,用自準直儀檢測
直線度,根據直線度計算軟件得出上下導軌正、側向曲線值,應用于小型批量型龍門式數控鏜銑床橫梁。大型橫梁采用立放即裝配狀態,用激光校準儀檢測導軌直線度,檢測數值與設計曲線值對比,不合格轉加工車間加修,合格轉總裝掛箱檢測。
總裝掛箱后實測 Y 軸移動直線度,滑枕處于最下端,用激光校準儀通過專用支板具與滑枕結合置于滑枕上,200mm 步長采數,分別得出 YZ垂直平面內正向直線度,XY 水平平面內側向直線度。用電子水平儀置于與滑枕連接支架具上,500mm 步長采數,移動滑板 Y 軸由負向正,得ZX 垂直面內角偏和 YZ 垂直面內角偏。用自準直儀移動滑板 Y 軸由負向正,得在 XY 水平面內角偏。通過總裝掛箱后實測 Y 軸運動直線度及角度偏差,分析直線度及角度偏差是否滿足幾何精度允差值,如與要求不符合裝配分析直線度及角偏數值及曲線圖形,計算實際曲線修正值并編制程序加修,或裝配采取刮研方法,達到整機幾何精度的驗收要求。
2. 橫梁裝配刮研
橫梁在總裝精度檢測后為減少其加修過程中的變形,裝配采取刮研方法進行精度調整。高精度橋式五軸加工中心大型橫梁直線導軌呈對稱式設計,依據仿形曲線并結合實際,裝配仿形曲線導軌直線度檢測精度在 YZ 垂直面內下導軌大面直線度為 0.01~0.02mm,導軌中部凹,上導軌大面直線度為 0.025~0.03mm,導軌中部凹。在 XY 水平面內上、下導軌立面直線度為0.1~0.13mm,導軌中部上凹下凸,上下導軌平行度 0.02mm。仿形加工后,部裝安裝直線導軌,用電子水平儀檢測導軌直線度,對比理論曲線 : │實測值 - 理論值│≤ 50μm,導軌直線度基本符合設計曲線允差范圍。總裝掛箱并安裝五軸頭后Y 軸移動用激光校準儀檢測導軌直線度及用電子水平儀檢測角偏,裝配記錄檢測數值并分析。為減少橫梁反修周轉變形,裝配采用刮研橫梁上下導軌大面及立面方法,使用電動或手動刮刀,通過刮研導軌大面和立面,提高 Y 軸移動的直線度及角偏精度。刮研方法,刮研前根據總裝檢測數值及圖形,先確定刮研位置及范圍、刮研量、刮研次數。按 200mm 一段劃線做好標記,導軌面刮研應邊刮研邊檢測,每次刮研嚴格控制刮研量,不許刮過量,每刮一次需用專用研具檢驗接觸率 ,當刮研直線導軌兩端時,假導軌面也需要刮研,保證假導軌與導軌對接處平整,不能出現臺階。刮研完成后,安裝直線導軌檢驗幾何精度,若不合,再一次進行刮研,直至合格為止。
四、橫梁直線度檢測方法
導軌直線度現有四種檢測方法 : 平尺拉表法、自準直儀(平行光管)、水平儀、激光校準儀。平尺拉表法因為受平尺長度影響,只能檢測橫梁局部的直線度,所以不采用。一般情況下,橫梁直線度檢測用自準直儀,通過專用橋板長200mm 置于直線導軌大面及立面上,檢測平數隨導軌長度增加而增多,記錄數據后通過輸入計算機直線度計算程序軟件,生成圖形曲線。框式水平儀一般用于調整橫梁水平,因檢測直線度效率低及讀數誤差大,現已很少使用。大型橫梁直線度檢測,為提高檢測精度及檢測效率購置高精度的電子水平儀、激光校準儀、直線度鏡組,并根據檢測方法設計專用的滑塊連接板、平行檢具、等高塊等。電子水平儀因無讀數誤差、數據可傳輸、可通過軟件計算生成曲線圖,操作簡單等優
點,為工藝方法廣泛推廣使用。
五、結束語
通過對大型橫梁仿形加工及裝配的實踐,提出橫梁設計及工藝優化的建議。
(1)橫梁結構直線導軌應采用上下導軌側基準在下導軌形狀平移式分布,不應如床身直線導軌形狀對稱式分布(見圖 5)。優點在于 : ①側基準在下可作為直線導軌的支撐面,通過預變形仿形加工凸形補償導軌因重力塌腰 ; ②平移式側基準面因中凸式仿形加工,立銑刀為切出式切削,切削力小,切削精度及效率高,相反如果對稱式分布其中一條側基準為切入式吃刀,切削力變大,切削精度受影響 ; ③平移式側基準對于大型橫梁立式裝配有利。大型橫梁為避免吊裝、翻轉的變形,部裝采用裝配狀態安裝直線導軌、齒條、光柵尺,直線導軌側壓塊安裝方便且側頂力均勻。相反如果對稱式分布其中一條側基準在上,導軌仿形為凹形,側壓塊在鎖緊固定時,需要較大的力,導致直線導軌側基準因受力不均而變形,影響裝配精度。④平移式側基準對于裝配刮研有力。因側基準為平行中凸,裝配刮研只刮高點,操作相對容易且準確快捷。而對稱式分布兩條側基準仿形為上凹下凸式,凹面刮研量大且困難。
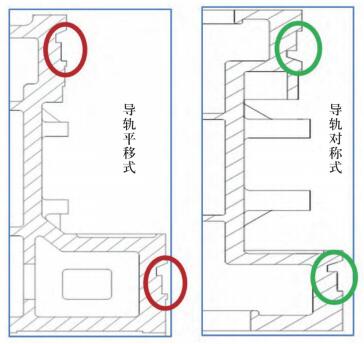
圖 5 橫梁直線導軌分布
(2)大型橫梁超重超大,因結構優化橫梁外觀差別較大。鑄件橫梁上下導軌階梯平移式布局、焊接橫梁背板整板煨彎式設計、大型焊接橫梁回字腔整板筋加強型設計等,大型橫梁因吊裝翻轉困難且容易變形,建議橫梁半精加工、精加工按裝配狀態自然裝夾,保持加工及裝配基準統一。
投稿箱:
如果您有機床行業、企業相關新聞稿件發表,或進行資訊合作,歡迎聯系本網編輯部, 郵箱:skjcsc@vip.sina.com
如果您有機床行業、企業相關新聞稿件發表,或進行資訊合作,歡迎聯系本網編輯部, 郵箱:skjcsc@vip.sina.com
更多相關信息