臺達AI視覺檢測解決方案高效掌握瑕疵零件大幅提升產品良率
2020-2-21 來源:中達電通 作者:-
工業 4.0 在全球制造業掀起智能化浪潮,通過智能制造系統,制造流程將可大幅優化,進而提升產線效能、降低成本支出,在智能制造系統中,人工智能扮演了重要角色,尤其是深度學習(Deep Learning)演算法更開始被應用到產線系統中的視覺檢測,快速而精準的判別產品瑕疵。
機器視覺檢測有效取代人眼,全靠“深度學習”
深度學習屬于機器學習的領域,其演算方式是通過不斷重復判別物件獲得龐大數據,再經過大量的運算讓精準度不斷接近完美,臺達指出,目前深度學習已經被大量應用于各種領域,制造業的視覺檢測則是其中重點應用。
產品檢測是制造業質量管理的一環,過去皆由現場作業員親力親為,然而人眼有其極限,檢測速度與正確率會隨著作業時間拉長降低,再加上產線速度越來越快、產品體積逐漸輕薄短小,后期機器視覺開始取代人眼,成為產線檢測主流。
在產線中,視覺檢測有四大主要功能,包括量測、辨識、定位、檢查等,而檢測是所有功能中最困難的部分,由于現場人員對瑕疵的認知不同,因此即便是已然自動化的機器視覺,仍會存在因系統設定或現場質管人員不同,導致出貨產品質量無法一致性的問題,要解決此一問題,臺達指出深度學習將會是最佳方式。
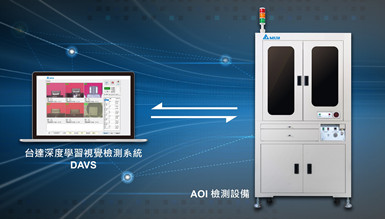
純 AOI 系統將快速消失,結合 AI 成轉型關鍵
將深度學習導入至產線檢測,對制造業與系統供應商兩端來說,都可提升工作效率。在使用者端,視覺檢測系統可以省下大量人眼檢核的成本,機器視覺軟硬件架構的準確率與判斷速度,已遠遠超過人眼,而且設定完成后,即可長時間不間斷且以一致標準的工作,將可為制造業者省下大量的人力成本。
過往的機器視覺系統,每一次上線都必須不斷調整設定,在智能制造概念中,產線必須可快速回應訂單,彈性調整生產內容,現行機器視覺檢測的繁復設定將難以滿足彈性化生產需求,深度學習架構只要事先通過訓練,即可快速上線使用,且還能自主學習,系統可以自動找出最佳的 OK/NG 參數,不必再由人員調整,在此狀態下,各設備的瑕疵檢測標準將可一致性,不會因品牌、使用時間的不同產生差別。
至于系統整合商,運用人工智能也將強化市場競爭力。人工智能在視覺檢測市場正加速普及,純 AOI 系統在制造業的競爭力將會快速消失,不過臺達也指出,現在市場對人工智能的導入也有迷思,多數廠商認為將 AOI 全面替換為人工智能,將可立即降低漏檢與誤判機率,然而這種一步到位的想法在實際狀況中并不可行,反而會讓漏檢和誤檢率大幅增加,建議應該保留現行 AOI 功能并結合人工智能,才能迭加兩者的優勢。
產品漏檢率趨近于零,誤判率極低
臺達針對視覺檢測所推出的 DAVS 即是以人工智能為核心的運送系統,此系統可以結合既有的 AOI 系統,讓既有設備可延長使用年限,以此保障制造業者過去的投資,而人工智能與 AOI 整合的模式,也提升了產品的檢出率。
以SMT用電感(用于手機/小型化PCB)為例,除非是嚴重裂紋,否則傳統的 AOI 系統常無法判斷影像中的線條是原有紋路或裂痕,且AOI對其中度裂紋的檢出率小于 50%,輕微裂紋檢出率更是在 5% 以下,加裝 DAVS 之后,檢出率大幅提升,不但漏檢率為零,誤判率更低于 0.3%。
臺達指出,工業 4.0 強調產線彈性化與快速自主學習,DAVS 通過人工智能與 AOI 的結合,以深度學習解決了現在 AOI 系統難以檢測的產品瑕疵,同時讓漏檢率趨近于零,達到超高檢出率需求,藉此提升出貨產品質量。
此外 DAVS 容易安裝的特色,可讓檢控設備建置在產線中的每一個重要環節,一旦制造過程中出現錯誤,系統就可立即提醒改善,避免將錯誤累積到最后檢測端,造成更大的成本浪費,也由于 DAVS 可大幅減少人力與管理成本,其投資可在 0.8~1.5 年之間回收。臺達以自身打造AOI設備的扎實經驗,建議制造業者可依自身需求,于AOI設備加裝建置便利的人工智能視覺檢測系統,向智能制造更邁近一步。
投稿箱:
如果您有機床行業、企業相關新聞稿件發表,或進行資訊合作,歡迎聯系本網編輯部, 郵箱:skjcsc@vip.sina.com
如果您有機床行業、企業相關新聞稿件發表,或進行資訊合作,歡迎聯系本網編輯部, 郵箱:skjcsc@vip.sina.com
更多相關信息