電氣化設計在數控機床參數調試與日常維修中的應用
2020-12-21 來源:中國航發貴州黎陽航空發動機有限公司 作者:崔紅利,吳玉舫
摘要:使用基于微矩陣參數調試方式,缺少對實際機床精度參數考慮,導致參數調試結果并不精準。為了改善該情況,提出了電氣化設計在數控機床參數調試與日常維修中的應用。根據不同的控制要求設定CNC參數,確定主軸轉速和程序指令轉速之間零偏移和增益偏移誤差,通過調整該誤差,維護CNC。把數控CNC輸入的仿真量轉化為用于主軸電機上的的實際轉速,以使得主軸的實際輸出速度可以保持與數控仿真量相同,維護變頻器。觀察刀具庫和刀架的碰撞,確定角度偏差,調整位置編碼器方向停止位置和偏移方向停止位置,使其恢復到原來位置,維護主軸。通過修改No.1850(網格偏重)減速塊位置參數,維護機床。描述數控機床典型體及其相鄰低序幾何,確定坐標系中位置姿態,對于數控機床中參數調試誤差研究可以轉化為坐標系行為研究,由此修正參數調試誤差。由實驗結果可知,電氣化設計方法在靜態工作模式下,參數調試方式主軸工作電流與實際電流一致,實際位置跟蹤誤差為0A;在動態工作模式下,轉速與實際轉速一致,實際位置跟蹤誤差為0轉/分,為數控機床穩定運行奠定基礎。
關鍵詞:電氣化設計;數控機床;參數調試;日常維修
0、引言
人們對機械產品的需求日益增長,要求也日益提高。常規加工設備已不適應這種發展需要,因此,數控機床的出現勢在必行。以往使用基于微矩陣參數調試方式,需要計算每一參數的靈敏度,但由于未考慮各種參數,如備用電池出現故障,數控系統操作員誤操作,電網瞬間斷電,造成部分參數丟失或變化,影響機床正常工作,導致實際機床參數調試結果不準確,影響了數控機床的加工精度。如果用戶能夠充分了解參數意義,將為故障診斷帶來極大便利,通過機器電子控制系統實現對機床作業的模擬,為了使操作人員的工作效率變得更加高效,盡心了數字化技術的結合。
CNC機床是一種結合了電、氣、機于一體的一體化機器,其最為重要的組成部分是電控系統,一旦電力系統出現任何的問題,機床的工作都會受到影響,無法正常工作。因此在進行對數控機床的日常調試和維護時,機器電子控制系統模擬機床的工作過程,并結合數字技術來提高操作者的工作效率。電控系統是保證CNC機床自動化運行的核心部分,一旦出現故障,將影響CNC機床的正常工作。因此在數控機床參數調試和日常維護中,電氣化設計十分必要。
1 、基于電氣化設計數控機床參數調試與維護
數控機床參數調試主要包括主軸相關參數和信號調節結果,這對變頻器自身參數調試來說具有重要意義。通過調試,確保數控機床能按要求發出正確的模擬電壓信號,驅動主軸經過變頻調速后能正常工作。
1.1 CNC參數調試與維護
在整個參數調控過程中,CNC參數是按照所需進行設定的,同時需要在主軸轉速上顯示控制的結果,保證參數與主軸轉速輸出結果一一對應。以數控車床主軸電氣設計為例,進行了仿真分析,設置轉速命令輸出限值(模擬量)為10V,主軸檔位1~3對應的最高轉速分別是1500r/min,3000r/min,4500r/min,在數控機床上設定的主軸參數如表1所示。
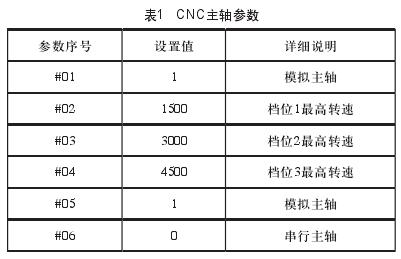
在采用模擬輸出主軸的情況下,由于溫度和元件特性的變化,實際主軸轉速和程序指令轉速之間可能存在較大誤差。當系統無編程工作時,CNC參數為輸出模擬量,此時電壓為0V。在完成表1中的參數設置后,可以通過參數#1~#6進行調整。以下是調整的方法和步驟:Step1:測量CNC輸出的模擬電壓,輸入M03S0指令,用萬用表測量逆變器兩端電壓值為-0.20V;Step2:輸入M03S4000指令,測得兩端電壓值為10V,記錄數據如表2所示。
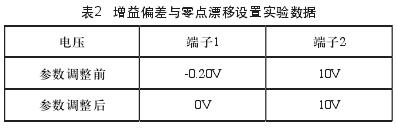
Step3:輸入數字#1~#6,使該數字生效,并驗證該數字輸出的模擬電壓;Step4:重復測試1的操作,分別測量速度為0和最高速度的模擬電壓,完成參數調整。
1.2 變頻器參數調試與維護
在調試變頻器參數時,主軸電機的所需要的實際轉速是通過對CNC輸入的模擬量進行轉換得到的,變頻器參數調整如表3所示。
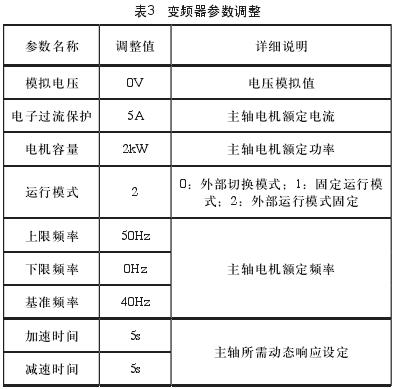
結合表3變頻器參數調整結果,需要設定系統運行速度與電流,保證主軸實際輸出結果與數控模擬結果一致。
1.3 主軸參數調試與維護
機器刀庫為滾筒刀庫,不需要機械手來換刀。一般工具更換過程如下:當機床收到工具更換指令后,主軸升至工具更換位置并停止時,“工具更換”程序就會從缸軸向前,并將空鼓的工具位置插入主軸工具箱。在把手凹槽處,用夾緊彈簧夾住滾筒,主軸工具自動夾緊釋放機構,松開切削刀,主軸上移,完成切削刀的提取過程;畫好切削刀,旋轉選擇工具[4]。對刀庫和刀架進行
了碰撞實驗,結果表明,位于刀架上的軸鍵槽和刀架的關鍵部分并不在一個位置,而且具有一定的角度偏差,從而引起碰撞。刀架上的鍵是和主軸的中心在一個水平線上。由此可以推論,刀架的鍵槽之所以沒有匹配刀架的關鍵位置,是因為主軸的停止位置不在其原本應在的正常位置上,主心軸尚未拆開。因此,對于主軸維護,需要調整主軸的定位位置,使其回到正常的位置。因為方向位置是通過對4031號和4077號兩個任何參數進行調整來恢復到之前原本的準確位置,也就是可以排除由于更換機床刀具引起的故障。
1.4 機床參數調整與維護
在CNC數控機床進行減速擋塊的調整時,偶爾會有回零的位置不一樣的情況。通過觀察發現,機床減速在進行參考點返回的時候,出現了一次結果為零的制動過程,但是這往往會導致制動的位置或前或后的出現一個螺距的位移,這也是機床位置編碼器發展上的一次改革創新,這可能是因為柵格信號產生的減速信號離開開關太近所造成的。因為傳送錯誤等原因,柵格信號正好漏掉了,必須等待下一個信號到達才能停止,這樣就會使停止位置或前或后出現一個絲杠螺距的移動。這樣,可通過修改No.1850(網格偏重)減速塊的位置或修改信號參數,使網格信號產生時間從減速信號關閉到啟動時間,從而避免了這一問題出現。
2 、參數調試誤差修正
在參數調試方面,除了用戶感覺到的是否達到精度要求外,還需通過模擬處理、誤差分析了解使用數控機床調試電氣設計參數,以及數控機床主軸加工方向,對于參數均優和參數不優兩種情況,需對數控機床主軸加工方向展開分析,如圖1所示。
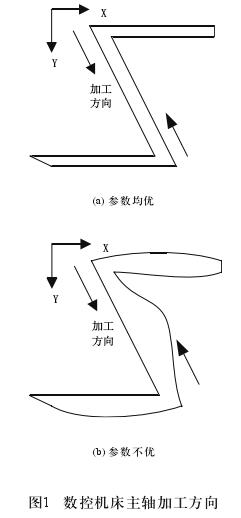
深入研究分析由Z字中選取“\”的筆畫,通過加工方向圖可發現,X/Y在軸速度為正的時候接收到了同步信號,然而實際模式則是出現在X軸方向的反應比較慢, 而出現在Y軸方向的反應卻是正常的,這也就使得開始點與結束點都變成了拋物線形狀的斜線。由此可知,確定出口標志的斜線段起點X軸的實際產生的位移值一直比出口標志的斜線段低主要原因,所以需要通過增加X軸的度。
參調主軸參數誤差分析時的主要工作是進行確認圓周半徑和角度誤差的精度是否在所需的范圍內,如果半徑誤差超過了所要求的精度范圍時,則需要增加X/Y軸伺服系統的剛度;如果角誤差超過精度要求范圍的時候,則需要對主刀的升刀延遲時間和刀降的推進時間進行增加,該過程是通過插補控制器完成的,進而使伺服系統位置跟蹤精準度得到一定的提升。設數控機床典型體Bk
及其相鄰低序Bj,如圖2所示
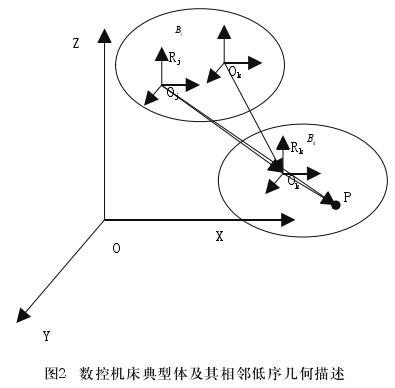
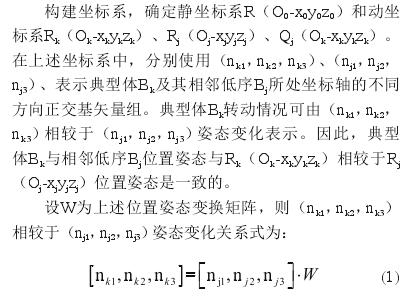
描述了位置姿態變換關系,即為相鄰體變換矩陣,對于數控機床中參數調試誤差研究可以轉化為坐標系行為研究。
在四個象限內分析軸心運動的輪廓誤差,如果存在于同一個象限上同一起點的半徑誤差和半徑誤差完全一致,而且半徑誤差在兩個不同的象限內,那么X/Y軸的PID參數值保持不變,主軸運動輪廓如圖3所示。
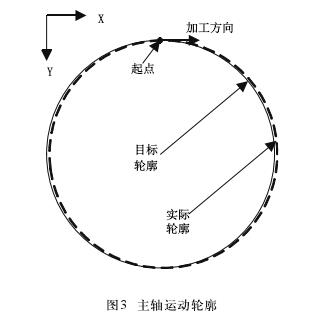
從圖3可以得知,當半徑誤差同時滿足在第二象限而且在第一象限的起始點相同時,如果兩象限和半徑誤差大于精度要求,X/Y軸的位置跟蹤性能應該進行一定的改善;如果第一象限和半徑誤差高于精度要求,那么X/Y軸的位置跟蹤性能需要進行一定程度上的完善;也可以根據圓口曲線是內、外的圓口曲線還是外的圓口曲線,判斷軸伺服系統的軟化特性,結合圖3中的輪廓輪廓可以看出,X軸的動態性能不良會出現一些偏差,但通過對上述內容進行修正,可以完成參數修正。
3 、實驗
針對電氣化設計在數控機床參數調試與日常維修中的應用合理性,展開分析。
3.1 模擬主軸系統組成
數控系統模擬主軸控制系統電氣化原理圖如圖4 所示。
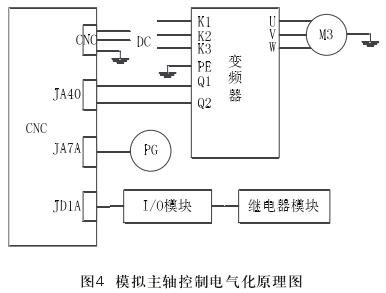
由圖4可以得出,CNC數控系統的JA40接口輸出電壓為0~15V的模擬電壓,E700變頻器上的兩個Q1、Q2子端接收模擬電壓信號,該模擬信號是通過JA40接口輸出的,由JD1A接口輸出的轉向信號則由子端接收,JA7A接入由主軸編碼器反饋得到的信號。
3.2 數控機床性能調試
對于數控機床性能調試,分別從靜態工作模式和動態工作模式兩個方面展開。
3.2.1 靜態工作模式
當數控機床在靜態工作模式下,主軸工作電流和位置跟蹤誤差如圖5所示。
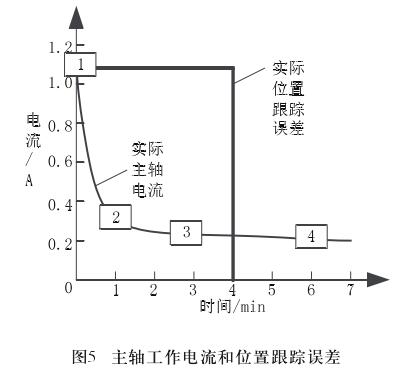
由圖5可知,4個特征點下主軸工作電流分別為1.1A、0.3A、0.25A、0.2A,針對這4個特征點的位置跟蹤誤差電流分別為0A、0.8 A、0.85 A、0.2A。基于該內容,分別使用基于微矩陣參數調試方式和電氣化設計參數調試方式對該工作模式下的實際主軸工作電流和位置跟蹤誤差展開分析,結果如表4所示。
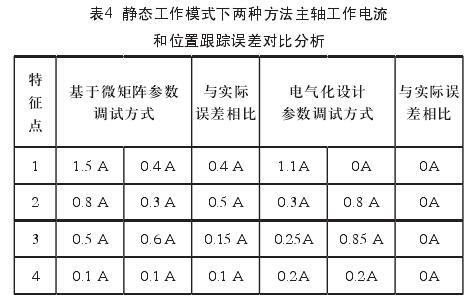
由表4可知,使用基于微矩陣參數調試方式主軸工作電流與實際電流相差較大,其中實際位置跟蹤誤差最大為0.5A,而使用電氣化設計參數調試方式主軸工作電流與實際電流一致,實際位置跟蹤誤差為0A,由此說明,當數控機床在靜態工作模式下,電氣化設計參數調試方式合理。
3.2.2 動態工作模式
當數控機床在靜態工作模式下,實際轉速和位置跟蹤誤差如圖6所示。
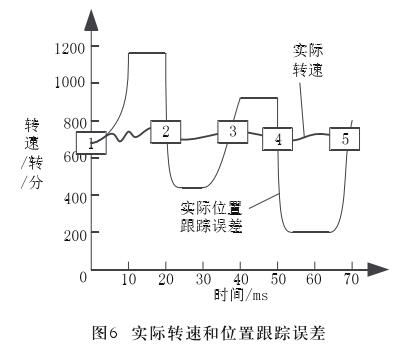
由圖6可知,5個特征點下實際轉速分別為700轉/分、750轉/分、740轉/分、680轉/分、680轉/分,針對這5個特征點的位置跟蹤誤差轉速均為0轉/分。基于該內容,分別使用基于微矩陣參數調試方式和電氣化設計參數調試方式對該工作模式下的實際轉速和位置跟蹤誤差展開分析,結果如表5所示。
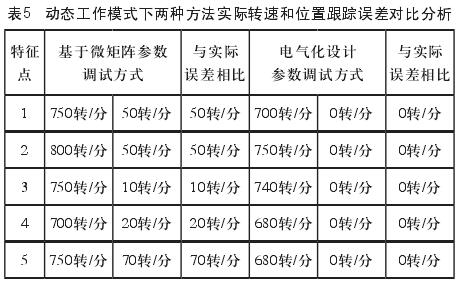
由表5可知,使用基于微矩陣參數調試方式轉速與實際轉速存在一定偏差,其中實際位置跟蹤誤差最大為70轉/分,而使用電氣化設計參數調試方式轉速與實際轉速一致,實際位置跟蹤誤差為
0轉/分,由此說明,當數控機床在動態工作模式下,電氣化設計參數調試方式合理。
4 、結語
主軸控制系統的調試是數控機床調試的重點,若輸入的指令和主軸的實際轉速不符,且在進行零件加的時候誤差較大,就需要對主軸進行調試。因為電氣化設計在進行參數調試的時候主要側重于對主軸主軸控制系統的硬件組成進行模擬和調試,缺乏分析了解數控機床軟件的功能部分,所以今后可以在調試過程中總結和積累更加豐富的經驗,進而完善和提高在調試和維修方面的技能。
投稿箱:
如果您有機床行業、企業相關新聞稿件發表,或進行資訊合作,歡迎聯系本網編輯部, 郵箱:skjcsc@vip.sina.com
如果您有機床行業、企業相關新聞稿件發表,或進行資訊合作,歡迎聯系本網編輯部, 郵箱:skjcsc@vip.sina.com
更多相關信息