交流伺服電機性能測試平臺設計與應用研究
2022-6-28 來源:武漢華中數控股份有限公司 作者:翟世欣 曾星
隨著中國智能制造 2025 戰略的提出以及電機工業的迅速發展,行業內對于交流伺服電機的性能指標提出了更多以及更高的要求,在電機廠商層面,除了對電機的磁路仿真設計、工藝路線進行研究以外,往往缺失的是對新產品樣機大批量的關鍵性能與理論仿真的驗證 ; 在配套主機廠層面,隨著電機選型品種繁多、應用層面廣、性能參數多、知識層面寬泛,且對應不同應用場合對性能的偏重點也不同,這些問題都對電機性能測試技術有了更高的要求。對此,需要形成全面的評價標準和準確的測試手段,因而,開發一套交流伺服電機性能測試平臺顯得尤為重要。
一、測試平臺總體架構
基于高精度高響應自主研發高響應高精度伺服電機作為負載,采用高性能自主驅動控制單元的轉矩、速度閉環控制策略,以及成熟穩定的電網回饋方案,既能實現零轉速下的持續扭矩輸出,又在節能環保方面獨樹一幟。具有其它測功機無法比擬的轉矩動態響應以及優異的轉矩轉速控制特性,提升了電機性能測試的高效節能及高可靠性。采用浮動式轉速轉矩傳感器,大幅增大轉速轉矩采樣準確性。該測試平臺實現了傳統靜態測功機無法進行的測控方案,如能量回饋、瞬態加載、反向拖動、轉速控制等。測試臺結構采用水平、垂直防震一體式臺架,被測電機 L 型板與測試臺面采用導軌安裝及導軌定位技術,保障了被測電機與傳感器間的同軸度。
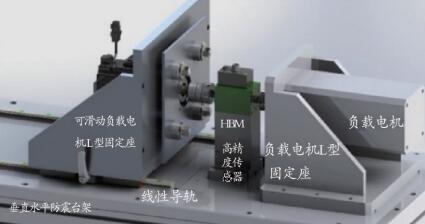
圖 1 測試平臺整體架構圖
二、系統工作原理
測試系統由上位機軟件給驅動單元發出轉矩指令或速度指令空載負載電機加載,并由高精度傳感器上傳實時轉矩轉速信號、功率分析儀檢實時輸入輸出電流、電壓、功率、效率并通過PCI 數據采集卡上傳至控制軟件,軟件通過負載電機編碼器及采集卡數據信息進行閉環控制,并由控制軟件繪制所需實驗曲線,進行實驗數據處負載電機通過回饋模塊實現能源高品質回收再利用。詳見圖 2 所示工作原理。
三、硬件設計
1. 負載電機選擇額定功率為 18.5Kw、額定轉速 1500rpm,最高轉速 10000rpm,額定電流為 43A 的異步電機 ;
2.選擇高精度200Nm數字轉矩轉速傳感器,轉速精度 ±0.5,轉矩精度 ±0.1,作為測量與控制系統的首要環節,傳感器必須具有快速、準確、可靠的性能。
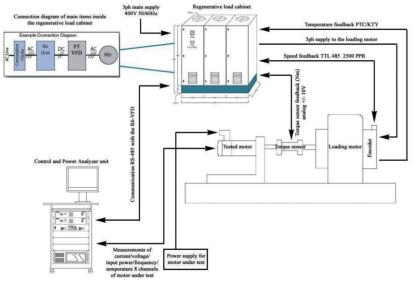
圖 2 系統工作原理圖
3. 聯軸器選用高精度彈性聯軸器,保障同軸度穩定性的同時,也能保障扭矩轉速的準確傳遞。
4. 能量回饋單元選用大容量能量回饋單元,全自動負載系統選用自主研發驅動單元實現高精度、高響應的扭矩及轉速輸出。
5.PID執行單元選用自主研發PLC控制系統,提供更穩定快速的執行各種測試條件。
6. 采用軍工級(6 通道)高精度多功能電力分析儀來進行電氣參數測試??赏瑫r測試驅動器前端和后端,保障實驗數據的準確性。
四、軟件功能
測試平臺的軟件開發與功能設計是十分重要的工作。根據測試需求,系統上位機控制軟件系統可以實現下列功能 :
1. 數據采集 : 能與下位機系統建立通訊,實現扭矩、轉速、功率、電流等數據互傳。
2. 命令發送 : 能將各種測試命令下發至下位機,實現與負載系統、PID 控制系統、功率分析儀主動控制權。
3. 實時數據繪制 : 將采集到的數據進行分析并繪制出曲線。
4. 參數設置 : 對負載控制系統剛性進行 PID調節。
5.狀態顯示:顯示當前測試扭矩、功率、轉速、電流、電機實時溫度等。
6. 測試項目 : 能夠為測試者提供多種不同的測試項目及自動測試方案。
五、軟件程序結構
基于以上功能,選擇測試程序在 WINDOS系統下使用 Visual Studio 采樣用面向使用者編程方法進行開發,軟件結構如圖所示 :
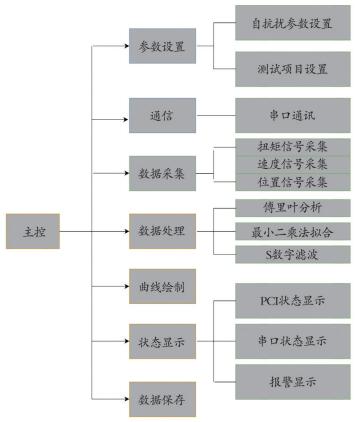
圖 3 平臺軟件程序結構圖
測試臺程序運行過程如下 : 主程序啟動,初始化 PCI 設置、PLC 設置,初始化串口 1、串口2 以及實驗中所需的設置 ; 選擇測試種類 ; 設置好所需數據和測試項目后開始進入測試階段。由上位機發送指令給負載電機進行數據采集及曲線繪制。期間可人工停止測試或等待自動測試停止。
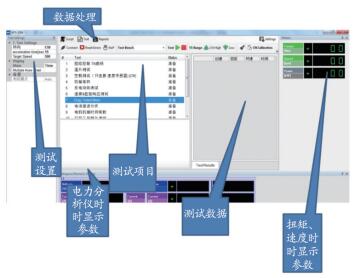
圖 4 測試實驗平臺界面圖
對所需數據進行分析,測試結束后選擇保存,將本次數據保存。
六、測試項目
1. 手動 / 自動加載,測試負載特性,包括 :扭矩 / 轉速 / 電流 / 電壓 / 功率 / 效率,通過該測試可準確判定被測電機工作區間分布范圍以及電機承受負載的情況,有效的了解電機性能指標。
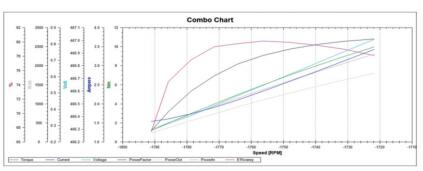
圖 5 負載特性測試曲線
2. 驅動器的電流不同負載下的諧波分析測試,測量伺服驅動器輸入輸出三相電運行情況,能夠定量分析伺服系統整體存在的諧波含量、有功使用、無功損耗、功率因數、電壓變動、閃變干擾、三相不平衡等指標,能夠準確反映整個伺服電機系統的 “健康” 狀況。
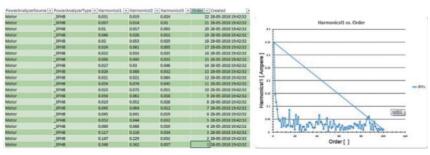
圖 6 諧波分析測試曲線
3. 轉矩波動測試,由于電機直接用于負載,在運轉的過程中,其自身由于齒槽力矩,電磁效應和加工裝配工藝等生產的轉矩波動將直接傳遞到負載上,從而對整個伺服電機系統的平穩及控制精度產生影響。尤其在低轉速低負載狀態下,力矩波動占電機輸出力矩比例較大,直接影響電
機控制精度,該測試可在電機出廠前對電機工藝進行精準控制。

圖 7 轉矩波動測試曲線圖
4. 反電動勢測試,電機反電勢設計好壞對于電機性能有著直觀的影響,低反電勢電機驅動器輸出電流波形毛刺較大,高反電勢電機通過自身電感來抑制磁勢變化斜率,通過降低諧波達到降低鐵耗,過高的反電勢也會由于弱磁角度變化引起電機高速過載能力較弱。通過該測試可直觀對比不同電機反電勢的差異化。
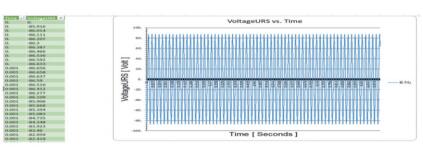
圖 8 反電勢測試曲線圖
5. 交變工況測試,通過自動化編程加載方式模擬電機在不同工作區不同時間交替使用狀態,也同時模擬電機在自身不同工作區交替工作時電機繞組溫升以及控制精度的穩定性,通過該測試提升電機出廠前的可靠性。
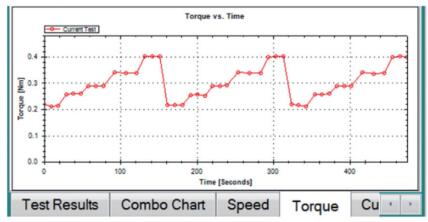
圖 9 交變工況測試曲線
七、結論
本文設計并實現了一個用于測試伺服電機性能的自動化測試平臺,該系統將計算機、采集卡、傳感器等硬件與數據采集、分析以及圖形用戶界面的應用軟件有效的結合,能充分發揮計算機的軟件控制能力。利用此平臺對特定的伺服系統進行了各種功能測試,測試結果證明,該平臺能夠按照測試系統設計功能要求,成功及準確的實現伺服電機的測試工作。
投稿箱:
如果您有機床行業、企業相關新聞稿件發表,或進行資訊合作,歡迎聯系本網編輯部, 郵箱:skjcsc@vip.sina.com
如果您有機床行業、企業相關新聞稿件發表,或進行資訊合作,歡迎聯系本網編輯部, 郵箱:skjcsc@vip.sina.com
更多相關信息