基于流固耦合的多級缸缸體性能分析
2016-8-22 來源:山東科技大學機械電子工程學院 作者:隋秀華 劉翠 蘇旭 何靜
以ZZ15000/24/47 型液壓支架立柱缸體為研究對象,利用三維數字化建模軟件對缸體進行建模,應用有限元分析軟件,基于單向流固耦合原理對缸體結構進行流固耦合分析,對純油液壓力作用下缸體結構進行靜力學分析,然后將缸體結構在上述2 種分析中得到的位移云圖和應力云圖進行分析比較。
電感1 000 mH。圖4、圖5 是最終輸出的相電壓和線電壓波形,相電壓輸出為3 個電平,線電壓輸出為5 個電平。相電流波形如圖6 所示。
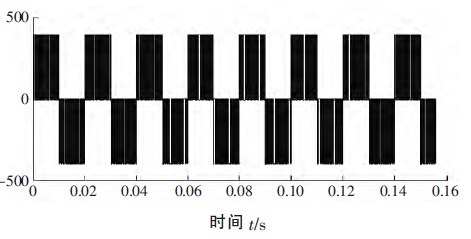
圖4 逆變器輸出的相電壓波形
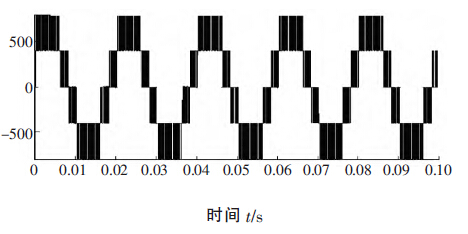
圖5 逆變器輸出的線電壓波形
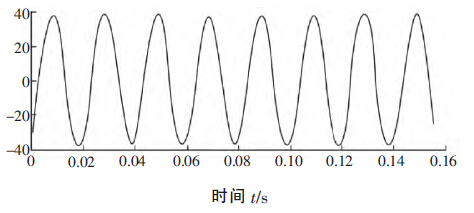
圖6 相電流波形
若帶的負載為電機時,輸出的線電壓波形如圖7 所示。
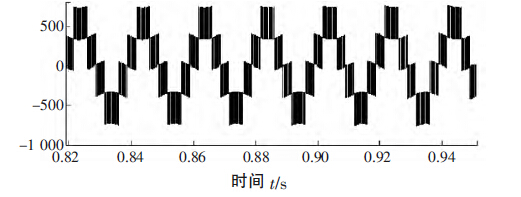
圖7 帶電機時的相電壓波形
4 結語在傳統的煤礦變頻器SVPWM 算法的基礎上采用了一種基于60°坐標系SVPWM 的新算法, 該方法極大地簡化了扇區判斷和矢量作用時間的計算過程,具有很強的實用性,并通過MATLAB 建模仿真實現了該算法, 在仿真中采用了電機負載和靜態阻感負載2 種負載,結果表明了該方法的正確性。
液壓支架是機械化采煤的重要設備,通常用于支撐煤壁和保護采煤過程順利進行,而立柱是液壓支架重要的部件,其穩定性直接影響著支架的可靠性。立柱的強度校核是液壓支架設計的關鍵環節,本文采用有限元分析軟件,基于單向流固耦合對液壓支架伸縮式雙作用立柱全部伸出時的缸體進行流固耦合分析,獲得流場真實的壓力載荷,將此載荷施加到缸體內表面上進行結構分析;同時對缸體在油液壓力作用下進行了結構靜力學分析。最后對比2種分析下缸體的應力分布和變形分布。
1 缸體流固耦合數值模擬
(1)流固耦合問題的數值求解方法流固耦合是流體力學與固體力學交叉生成的一門學科。近年來得到了廣泛的應用。從控制方程解法角度,流固耦合分為直接求解的強耦合和分區迭代的弱耦合。從本質上講,強耦合即為流固耦合問題的求解應該根據統一的耦合方程,在一個時間步內對流體域和固體域中所有的未知量同時求解。忽略固體變形對流場的影響,選用弱耦合方法中的單向流固耦合方法對缸體結構進行力學性能分析。
(2)幾何模型的建立
選取ZZ15000/24/47 型液壓支架立柱為研究對象。采用三維建模軟件Pro/E 對立柱進行建模,如圖1 所示。本文主要分析缸體,因此需要對缸體結構進行簡化,去除受力不大的附件、倒角等結構。為能正確反映缸體的實際工作情況,需要保留中缸體和缸底。簡化后立柱缸體的三維模型如圖2 所示。
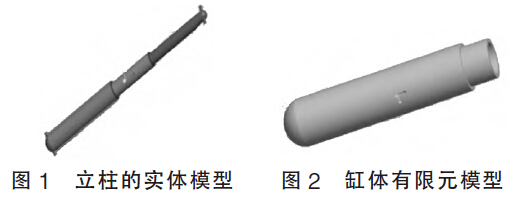
(3)缸體流固耦合分析
①缸體流場模型流場計算選用的是有限元分析軟件中的流體模塊fluent,分析時將缸體的進口
設為泵站壓力(p=32 MPa),中缸體底端底閥處作為缸體流場的出口,將該出口設為壓力出口,出口壓力為中缸體內部壓力,固壁邊界采用無滑移邊界條件,近壁區域采用標準壁面函數處理。將分析中流動介質設為水,采用SIMPLEC 算法及基于壓力基穩態求解器,選用標準的k-ε 雙方程湍流模型,標準k-ε 模型
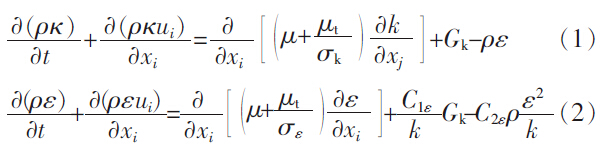
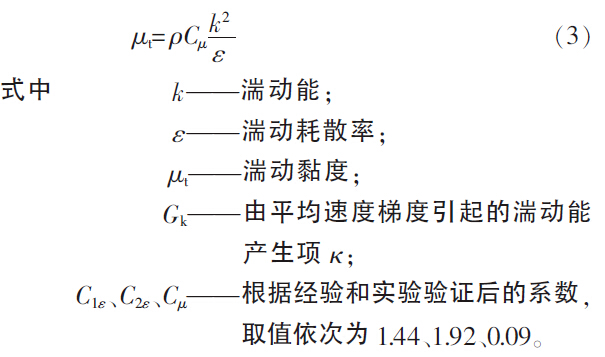
②缸體內流道靜壓分布油缸ZX 對稱面上的油壓分布圖如圖3 所示。由于立柱油缸的動力是由泵站提供的,油缸的進口與泵站相連,所以油缸進口處油壓為33 MPa。中缸體底端底閥處為缸體流場的出口,油壓最大為62.4 MPa,并且缸體內部的流場壓力分布均勻;
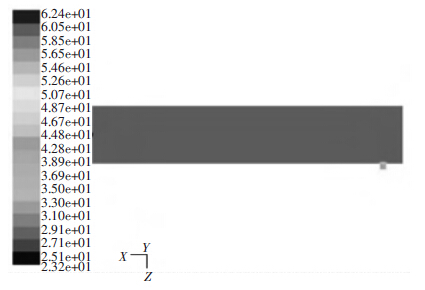
圖3 油缸ZX 對稱面上的靜壓分布圖(MPa)
③缸體有限元模型基于ANSYS Workbench平臺對立柱缸體進行流固耦合分析。利用ANSYS12.0軟件的無縫連接功能,將缸體的三維視圖傳遞到靜態結構分析中,油缸的材料采用27SiMn,材料屬性如表1 所示。利用ANSYS Workbench 網格劃分功能,進行缸體的網格劃分。

缸體有限元模型的約束條件:缸體的缸底采用固定約束;中缸體內部的油液對中缸體的下表面有壓力作用,所以在保留的中缸體的下表面施加壓力載荷;
④計算結果分析圖4 和圖5 分別為流固耦合作用下的位移變形及應力云圖。由圖4 可以看出,在流固耦合作用下,位于中缸體底端底閥處的位移變形最大,最大值為1.723 mm,且位于缸體結構體上越靠近缸體底端位移變形越小。由圖5 可知,油液經缸體進口進入到缸體內時油壓均勻作用到內表面,致使缸體的內表面壓力變化比較均勻,應力值為160.19 MPa,缸體頂端應力值為639.82 MPa,中缸體底端底閥處應力值最大,應力值為1 439.2 MPa。
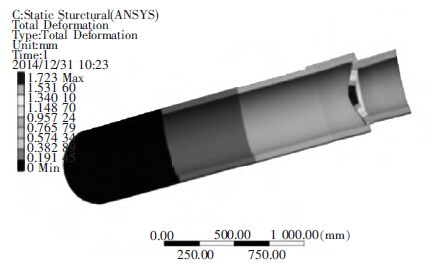
圖4 流固耦合作用下缸體的位移變形云圖
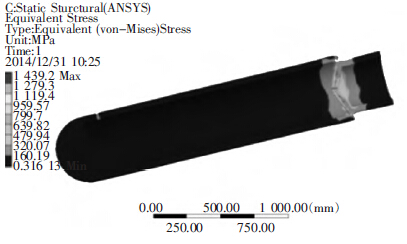
圖5 流固耦合作用下缸體的應力云圖
2 油液壓力作用下缸體的結構靜力學分析
(1)缸體的有限元模型
將上述分析中結構體模型導入到結構靜力分析模塊中,對缸體的缸底施加固定約束,把油缸看
作是受壓容器,所以分析時在缸體的內部、中缸體的底端均施加壓力載荷。缸體加載壓力
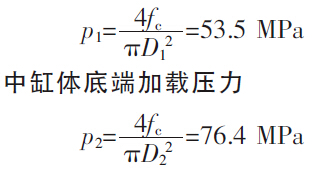
圖6 和圖7 為分析后的位移變形云圖和應力云圖。由圖6 可以看出,中缸體底端底閥處位移變
形最大,最大值為0.781 1 mm,且缸體上越靠近底端位移變形值越小。由圖7 可知,缸體進出口處的
應力值最大,最大值為623.71 MPa。且缸體頂端的應力值為278.56 MPa,缸體內表面應力值為347.59
MPa。
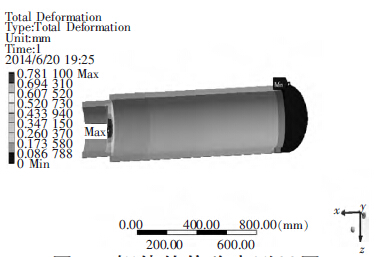
圖6 缸體的位移變形云圖
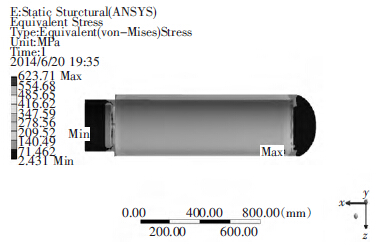
圖7 缸體的應力云圖
3 分析結果比較
對比分析上述2 種工況可以得到,缸體在純油液壓力作用下的位移變形與在流固耦合作用下的位移變形變化趨勢一致,但同一位置處的變形值相差較大。在流固耦合作用下中缸體底端底閥處最大應力為1 439.2 MPa,遠大于油液壓力作用下的最大應力值623.71 MPa,這是因為從活柱傳遞來的力使中缸體內的壓力增大,并且底閥處的截面積突然減小,油液經缸體進入到中缸體內時,油液的阻力變大, 致使底閥處的應力值最大。立柱的材料為27SiMn,其屈服極限為σs=835 MPa,中缸體底端底閥處的應力值大于材料的屈服極限,此處為危險位置。并且流固耦合作用下缸體頂端的應力值大于油液壓力作用下此處的應力值。通過分析可得應用流固耦合對立柱進行分析更加符合實際情況。
4 結語
(1)缸體在流固耦合作用下的應力分布比較均勻,最大應力出現在中缸體底端底閥處,超過了油缸材料的屈服極限,此處為立柱的危險位置,越靠近缸體底端位移變形越小;
(2)缸體在純油液壓力作用下的位移變形與流固耦合作用下的位移變形變化趨勢一致,但相同位置處的變形值相差較大。缸體的應力分布比較均勻,中缸體底端底閥處應力沒有超過材料的屈服極限,是安全的;
(3)立柱作為液壓支架重要的部件,不僅要考慮油液壓力對缸體的作用,還要考慮油液的流固耦合作用對立柱缸體帶來的影響。
投稿箱:
如果您有機床行業、企業相關新聞稿件發表,或進行資訊合作,歡迎聯系本網編輯部, 郵箱:skjcsc@vip.sina.com
如果您有機床行業、企業相關新聞稿件發表,或進行資訊合作,歡迎聯系本網編輯部, 郵箱:skjcsc@vip.sina.com
更多相關信息