FANUC伺服優化功能在模具加工中的應用
2021-3-30 來源:蕪湖職業技術學院 機械工程學院 作者:葛阿萍
摘要:為了改善模具加工中零件加工表面存在振紋、過切等表面質量不佳的問題。文中通過FANUC SERVO GUIDE 軟件測試機床的伺服系統性能,針對測試結果,對機床伺服系統三環參數、背隙加速等伺服參數進行逐步調試和優化,并將優化結果應用于某模具樣件加工試驗,試驗結果表明,優化后的伺服系統響應性能和機床的加工性能都有所提高。
關鍵詞:伺服優化;伺服系統;SERVO GUIDE;加工質量
數控機床是模具產品的生產載體,其伺服系統性能的好壞直接影響著模具產品的加工質量。一般在機床剛出廠時,廠家會給定一組能夠保證正常加工的參數值,但并不能發揮機床最佳的加工性能[1]。另一種情況是隨著數控機床使用時間的增加,機床的機械性能發生了變化。此時與之相關的伺服參數也要隨之做出調整,否則會引起機床機電不匹配,造成機床運行不穩,產生振動,使得零件加工表面存在振紋、過切等表面質量不佳的問題[2]。因此為了保證模具產品的加工精度和表面質量,對數控機床伺服系統進行優化顯得尤為必要。
文中通過FANUC SERVO GUIDE 軟件測試機床的伺服系統性能,針對測試結果,對機床伺服系統三環參數、背隙加速等參數進行逐步調試和優化,以獲得良好的伺服動態性能和機械剛性,使數控機床處于穩定的工作狀態,充分發揮最優加工性能,從而提升模具產品加工品質和精度。
1 、伺服優化原理和內容
1.1 伺服優化原理
數控機床伺服系統優化的目的,是為了更好地優化機械特性和電氣特性之間的配合,以獲得更高的伺服系統響應和機械剛性,從而獲得更好的加工性能[2]。FANUC 伺服系統控制采用三環控制的方式,如圖 1 所示[2-3]。
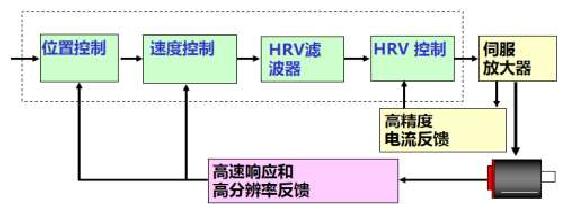
圖1 伺服控制原理圖
FANUC系統將伺服三環控制集成在NC的軸卡上,通過接收NC所發出的指令,經軸卡的三環處理后輸出至放大器,驅動電機運行。最內環是電流控制,中間環是速度控制,最外環為位置控制。三環中,電流環是整個伺服系統控制的根本環節,作用是提高系統的快速性,限制最大電流,使系統有足夠大的加速轉矩。速度環是伺服控制的中間環節,作用是提高系統抗負載擾動能力,抑制速度波動。位置環是最外環,其作用是保證系統的靜態精度和動態跟隨性能[4]。三環中,電流環響應速度最快,其次是速度環,最后是位置環。若要提高位置環回路增益須先提高速度環回路增益,否則容易導致機床振蕩,運行不穩。因此,伺服優化應遵循“由內而外”的原則,秉承先電流環、后速度環,最后位置環的先后順序進行優化。
伺服優化的實質是根據機床的頻率響應曲線、圓弧測試圖進行分析,合理調整伺服三環參數,盡可能使各軸精確的跟隨移動指令和抑制干擾扭矩,即在一定的機械狀態下確保伺服系統不會出現振蕩,保證三環控制回路能夠在高響應、高剛性下“和諧”工作[5-6]。
1.2 伺服優化的內容
對于數控機床伺服優化主要包括兩個方面[7]:
(1)提高伺服電機增益,抑制機床振動通過頻率響應測試抑制機床共振點,提高機床增益,以匹配機床的機械剛性、提高電機的響應速度。
(2)循圓象限凸起抑制,調整加工精度通過觀察機床圓弧象限測試進行調整,抑制伺服軸換向時的凸起,消除加工時的象限痕。
2 、伺服優化案例分析
2.1 加工故障現象
某加工中心使用 FANUC 0i-MF 系統加工模具產品試件,使用AICC功能,進給量為2000mm/min, 經加工后,零件加工表面有明顯的振紋,存在過切,如圖2所示。
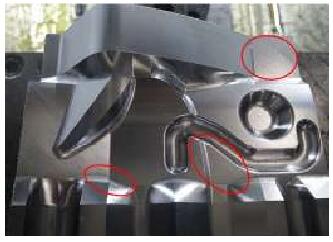
圖2 優化前試件
2.2 伺服優化方案
(1)首先利用 SERVO GUIDE 軟件測試機床 3 軸靜態頻率響應曲線,觀察機床的機械性能。靜態頻率響應測試是 SER?VO GUIDE 調試中非常重要的一環,它波形的好壞反映了機床很重要的機械特性,它調整的好壞直接影響了后續圓弧部分的調整,以及機床運行的平穩和加工效果的好壞,在整個調試中具有非常重的分量。頻率響應測試通過頻率響應測量各軸的共振點,并用濾波器參數來抑制共振[5]。在滿足波形要求,保證共振點被抑制的情況下,提高速度環路增益。以 X 軸測試為例,優化前頻率響應圖如圖3所示。
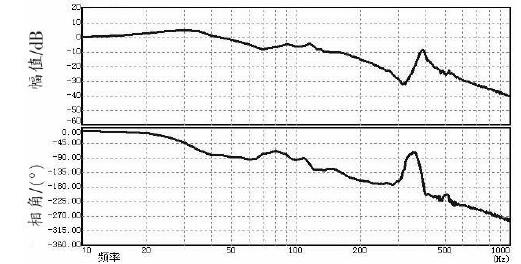
圖3 X軸優化前頻率響應波形
調試中主要以幅頻特性曲線作為考察伺服特性的主要依據[5]。由圖3 可知,幅頻曲線在低頻 50HZ—200HZ 范圍內幅值低于 0d B,表示系統響應滯后。先檢查電流環參數,發現“HRV+
控制有效”未選中,如圖4所示。此功能是在HRV3基礎上進行控制的,即HRV3+功能,可以實現電流環更高速響應和較高的速度增益設定。選中“HRV+控制有效”選項,再次測試頻響曲線,如圖5所示。

圖4 電流環參數

圖5 X軸優化中頻率響應波形
在使用了HRV+控制有效后,低頻部分幅值基本接近0d B,系統響應滯后明顯改善。但高頻部分在 380h Z 左右仍存在明顯的共振點。調試中逐步加入濾波器來抑制高頻振蕩。在使用 HRV 濾波器后機床高頻共振被抑制,振蕩現象明顯減弱。機床消除振動的原則是在抑制掉高頻振蕩點后,確保機床平穩運行的狀態下盡可能提高機床伺服系統速度增益[4]。經反復調試,最終將速度環增益由原來的 150 調整到最終的 180。優化前后的速度環參數設置如圖6所示。
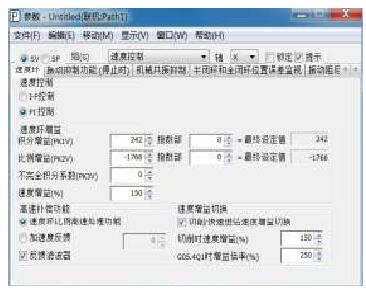
(a)速度增益優化前
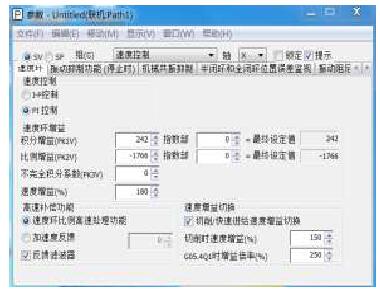
(b)速度增益優化后
圖6 速度環關鍵參數
最終優化后X軸頻響特性曲線如圖7所示。此時曲線的最高點低于5d B,高頻衰減區域的幅值低于-20d B。經優化后的機床機械特性已明顯提高,既充分發揮了伺服的剛性余量,又保證了伺服軸的穩定運行。
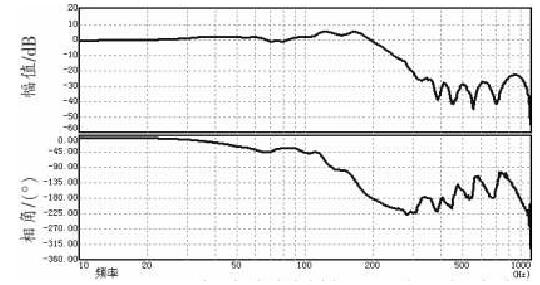
圖7 X軸優化后頻率響應波形
(2)在合理優化了三軸伺服環增益,確保三軸在高剛性下穩定運行后。將 CMR(柔性齒輪比)擴大 10 倍(系統檢測精度提升)。因為在機械性能較好的前提下,擴大CMR倍數能夠改
善電流特性曲線,使得機床運行更加平穩,降低電流波動,對加工表面的光潔度一定的改善作用。
(3)經上述調試后,機床高頻振動被抑制,伺服響應性能有所提高。再次加工,奔馳件試件表面振紋已明顯改善,但加工試件上仍存在過切現象,需通過圓度測試進一步檢測。以 XY
插補圓弧為例,如圖8所示。橫軸為X軸,縱軸為Y軸。
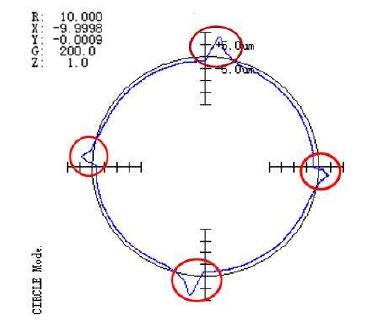
圖8 XZ軸圓弧調整前圖形
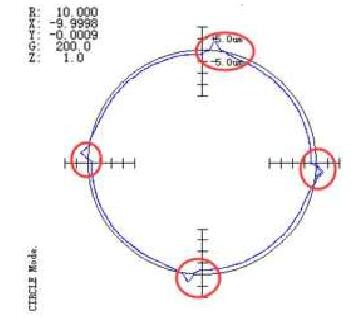
圖9 XZ軸圓弧調整后圖形
根據XY軸圓度測試圖分析,四個象限均有凸起,Y軸兩象限凸起接近 10um。這可能是造成工件加工爬坡過切的原因。在機床系統中,當反沖摩擦的影響較大時,在電機反轉時,就會產生延遲,造成圓弧切削時的象限凸起。以Y軸為例,嘗試對Y的象限凸起進行補償,試著將背隙加速補償參數調大,觀察Y 軸象限凸起有所改善,經反復調試,將 Y 軸背隙加速補償量(NO. 2048)由原來的 200 增加到 600,背隙加速有效時間(NO.2071)由原來的0增加到10。X軸背隙加速補償量由原來的0增加到300,背隙加速有效時間由原來的0加到6。經優化后的XY軸圓弧圖形如圖9所示。四個象限凸起均被抑制在5um以內,明顯改善。
2.3 加工測試
完成上述步驟調試后,使用AICC功能,再次加工。由于高頻振動得到抑制,象限凸起現象改善,使得機床運行平穩。最終加工效果刀路整齊,表面光滑無振紋,過切現象有所改善。加工后試件如圖10所示。
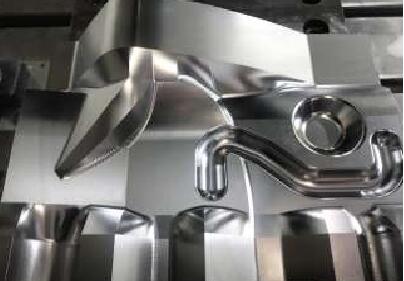
圖10 優化后試件
3 、結語
經試驗研究結果表明,通過 FANUC 伺服優化可有效解決模具加工中零件表面振紋和過切現象,改善模具產品表面加工品質和加工精度,提高數控機床的加工性能。在實際伺服優化過程中,由于各廠家機床本身機械的不同,裝配的差異,其伺服參數調整會有些差異,即便是同一臺機床不同時期因磨損使用程度的不同,其伺服優化也并不完全相同,但整個伺服優化的方法和流程大體一致。伺服優化是一項煩瑣的工作,需反復調試,摸索總結,方能確定好的優化結果。
投稿箱:
如果您有機床行業、企業相關新聞稿件發表,或進行資訊合作,歡迎聯系本網編輯部, 郵箱:skjcsc@vip.sina.com
如果您有機床行業、企業相關新聞稿件發表,或進行資訊合作,歡迎聯系本網編輯部, 郵箱:skjcsc@vip.sina.com
更多相關信息