超大孔徑聚晶金剛石拉絲模具單向走絲電火花線切割加工工藝研究
2016-11-10 來源:北京迪蒙吉意超硬材料技術有限公司 作者:康凱敏,曹鳳國,桂小波
摘要:基于試驗研究,創新性地提出了采用單向走絲電火花線切割機床對超大孔徑聚晶金剛石拉絲模具的孔形進行粗加工。以金剛石粒度為25 μm 的直徑22 mm、厚度20 mm 的超大孔徑聚晶金剛石拉絲模具為例,進行單向走絲電火花線切割加工定徑區、壓縮區和安全角的工藝研究,得出了加工工藝曲線,確定了最優加工工藝參數,提高了粗加工效率,確保了良好的孔形精度。結果表明:選擇脈沖寬度4 μs、脈沖間隔40 μs、峰值電流15 A、走絲速度10 m/min 時,可獲得較滿意的加工效果。
關鍵詞:聚晶金剛石;超大孔徑拉絲模具;單向走絲電火花線切割加工;錐度加工
對傳統的鋼芯拉絲模具孔形,最早采用機械研磨的加工方法,即用機械傳動的方式帶動研磨工具(如磨針、磨錐、絲、繩等)作高速運動,利用研磨材料對模具孔形表面產生的磨削作用來加工孔形[1]。但對于聚晶金剛石(PCD)拉絲模具來說,模芯材料PCD 本身具有較高的硬度和抗壓強度,且熱導率極高、耐磨性較好,用傳統的機械加工方法加工孔形時,工時長、效率低、廢品率高,很難保證孔形尺寸和表面質量。目前,較多采用電火花、激光及超聲波等特種加工方法。電火花放電加工一般用于中、大孔徑拉絲模具孔形的粗加工;激光加工適于微孔和小孔拉絲模具的粗加工;超聲波加工主要用于拉絲模具的精加工[2]。
目前,國內模具制造廠家對于中、大孔徑PCD拉絲模具,主要用電火花成形加工來完成定徑區和各角度區域的粗加工, 用超聲波研磨進行精加工。這種加工方法不但效率很低, 且由于電極損耗嚴重,加工出的孔形精度也低,并隨著孔徑的增大,加工難度越來越大。隨著單向走絲電火花線切割技術在模具制作上的應用,采用單向走絲電火花線切割機床進行定徑區和角度區域的粗加工成為可能,該機床的優勢之一是能進行高精度的錐度加工。利用單向走絲電火花線切割+臥式超聲波加工的方式進行超大孔徑PCD 拉絲模具的加工,不僅粗加工效率提高了近3 倍,還提高了孔形精度。
本文以金剛石粒度為25 μm 的直徑22 mm、厚度20 mm 的超大孔徑PCD 拉絲模具為例, 進行單向走絲電火花線切割加工定徑區、壓縮區和安全角的工藝研究,確定最優加工工藝參數,并介紹了錐度加工方法及工藝技巧。
1. PCD 拉絲模具孔徑分類
PCD 拉絲模具孔形結構見圖1。按孔徑d 的大小可分為微孔(d≤0.1 mm)、小孔(0.1 mm<d≤1.0mm)、中孔(1.0 mm<d≤3.0 mm)、大孔(3.0 mm<d≤10.0 mm)和超大孔(d>10 mm)。孔徑大小不同,其加工方法也不盡相同。通常,對于PCD 拉絲模具的孔形加工方式,微孔、小孔采用激光+超聲波加工;中孔、大孔采用電火花成形+超聲波加工。
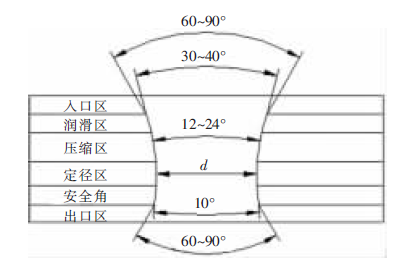
圖1 PCD 拉絲模具孔形結構圖
2. 超大孔徑PCD 拉絲模具線切割加工工藝
實驗采用AQ360 單向走絲電火花線切割機床,電極絲為直徑0.2 mm 的黃銅絲, 加工介質為去離子水,加工方式為浸沒式加工。利用單向走絲線切割機床切割拉絲模具時,需事先加工穿絲孔。實驗用機床數據庫雖然提供了加工PCD 的參考加工參數,但實際切割中,該參數不適合超大孔徑PCD 拉絲模具的切割。超大孔徑PCD拉絲模具的特點是孔徑大、工件厚度大、材料粒度大,其切割工藝要求為:表面粗糙度均勻,孔形精度高,切割時間長,且切割過程不允許斷絲,這些要求增加了線切割的加工難度。若在切割過程中發生斷絲,在斷絲部位會出現凹槽或凸棱,將給后續的超聲研磨加工增加相當大的工作量, 既浪費磨料,時間和成本均增加,還影響模具精度。因此,有必要對超大孔徑PCD 拉絲模具的線切割工藝進行研究,對脈沖寬度、脈沖間隔、峰值電流、伺服參考電壓等電參數和其他非電參數進行分析及適當的調整,選擇最佳的工藝參數,以提高切割速度和加工質量。
2.1 電參數對切割速度及表面質量的影響
2.1.1 脈沖寬度
脈沖寬度是單個脈沖能量的決定因素之一。脈沖寬度過小,脈沖能量不夠,幾乎無法加工PCD 材料。當脈沖寬度增加時,單個脈沖放電能量增加,切割速度也隨之增加。圖2 是超大孔徑PCD 拉絲模具的切割速度隨脈沖寬度變化的曲線。當脈沖寬度增大到一定值時,切割速度將不再與脈沖寬度呈正比增長關系,甚至還會隨著脈沖寬度的增加而下降[3]。這主要是由于PCD 材料的導熱率高,放電脈沖能量通過工件散發而損失,反而削弱了蝕除作用。電蝕產物的拋出作用不會隨著脈沖寬度的增加而顯著提高,使短路幾率增大,加工變得不穩定,切割速度減小,甚至造成斷絲。另外,由于單脈沖能量的增大會使電極絲振動加強, 從而增大表面粗糙度值,降低表面質量。
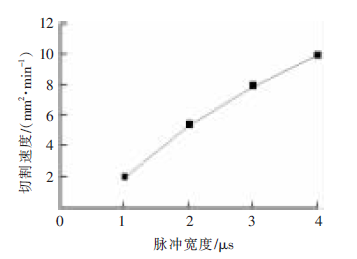
圖2 切割速度隨脈沖寬度變化的曲線
脈沖寬度過大,單個脈沖能量過大,金剛石顆粒被沖擊或局部碎化脫落,或整體脫落,在加工表面將留下較大的凹陷,因此加工表面粗糙度值大[4]。金剛石粒度越大,留下的凹陷就越大,表面越粗糙,將給后續的研磨精加工增加難度。此外,還有可能使正常的脈沖放電狀態轉變為瞬間電弧放電狀態,燒壞工件(圖3a),或造成斷絲現象時常發生。正常切割時的表面見圖3b。超大孔徑PCD 拉絲模具厚度大、排屑條件差,因此,線切割加工時一般不采用增加脈沖寬度的方法來提高切割速度,而普遍采用窄脈沖寬度、高峰值電流。
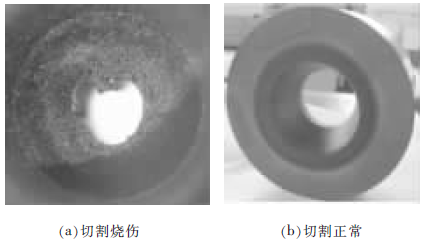
圖3 切割燒傷與切割正常表面狀況
2.1.2 脈沖間隔
脈沖間隔對超大孔徑PCD 拉絲模具切割速度的影響較大,對表面粗糙度的影響較小。圖4 是切割速度隨脈沖間隔變化的曲線。脈沖間隔增大,脈沖空載百分率提高,加工穩定性提高,極間不易產生拉弧現象,但切割速度降低明顯。脈沖間隔減小,會使脈沖放電頻率增加,平均加工電流增大,切割速度提高;但脈沖間隔過小,會使放電間隙中的電蝕產物來不及排出,加工狀態變得不穩定,影響切割速度的提高, 甚至會產生電弧放電燒斷電極絲,使加工無法繼續進行。因此,在工作液恢復極間絕緣性的條件下,可適當減小脈沖間隔,使單位時間內的放電次數增多,從而提高切割速度。
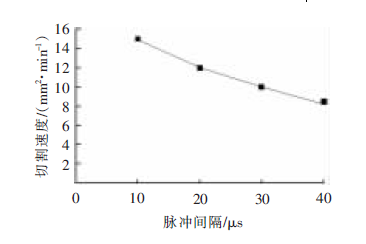
圖4 切割速度隨脈沖間隔變化的曲線
實際加工時,應根據超大孔徑PCD 拉絲模具的厚度選取合理的脈沖間隔。脈沖寬度不能過小,否則壓力沖液很難充分進入工件中間部位,不利于電蝕產物的排出,易斷絲。因此,應選擇較大的脈沖間隔加工,以保持加工的穩定性。
2.1.3 峰值電流
對于PCD 材料, 尤其是超大孔徑PCD 拉絲模具的切割,應采用大脈沖能量、大峰值電流,否則能量太小,無法切割。與脈沖寬度的影響相似,隨著峰值電流的增加,單個脈沖能量增大,切割速度提高,而表面粗糙度值卻變大;同時,加工間隙大,也使加工精度降低。切割速度隨峰值電流變化的曲線見圖5。提高脈沖峰值電流可按比例提高單個脈沖的放電能量,單向走絲線切割加工在其他參數保持不變的情況下,提高單個脈沖能量就意味著提高切割加工的速度。但如同脈沖寬度和脈沖間隔的影響一樣,峰值電流的提高也應在一定的范圍內。若峰值電流過大,在沖液狀況沒有改善的情況下,切縫內排屑不暢,切割速度會減慢,并可能引起斷絲。
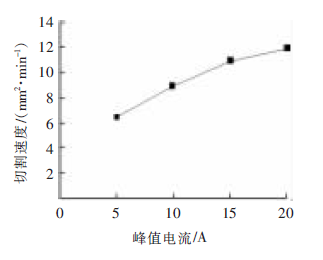
圖5 切割速度隨峰值電流變化的曲線
2.1.4 伺服參考電壓
伺服參考電壓是預先設定的用以控制電極絲前進和后退的標準電壓。當平均加工電壓高于該值時,電極絲前進;低于該值時,電極絲后退。切割PCD 時需杜絕發生斷絲,因此切割超大孔徑PCD 拉絲模具時,適當增加伺服參考電壓的設定值,可增大電極絲和工件間的間隙,有利于排屑,使加工穩定,不易造成斷絲。
2.1.5 伺服進給速度
切割PCD 材料時的伺服進給速度與切割普通材料不同,不允許伺服進給速度超過加工速度(即過進給)。因為當伺服進給速度超過加工速度后,對于普通材料會出現頻繁的短路現象,同時增大了斷絲的可能性; 而對于PCD 材料是直接將電極絲劃斷,影響了加工速度。因此,切割超大孔徑PCD 拉絲模具時,伺服進給速度應略低于加工速度(即欠進給),以避免斷絲。
2.1.6 開路電壓
在正常情況下,提高開路電壓會使切割速度顯著提高,這是因為電壓的提高必然使脈沖峰值電流和加工平均電流都提高,單個脈沖能量加大,對提高切割速度有利,但表面粗糙度值卻變大;同時,加工間隙大,也使加工精度降低。切割加工超大孔徑PCD 拉絲模具時,開路電壓一般在100 V 左右。
2.2 非電參數對切割速度及表面質量的影響
2.2.1 走絲速度
走絲速度對切割速度有一定的影響。提高走絲速度,電蝕產物的排出速度也會加快,這將減少產生二次放電的幾率,提高加工穩定性,從而提高切割速度。但走絲速度過快,將使電極絲振動加大,表面粗糙度變差,降低表面加工質量,也會造成電極絲的浪費;走絲速度過慢,會使電極絲上某一點可能產生多次放電,易造成斷絲。因此,結合超大孔徑PCD 拉絲模具定徑區、壓縮區和安全角的不同切割厚度,適當地調節走絲速度在9~10 m/min 為宜。
2.2.2 電極絲張力
電極絲張力在加工過程中應保持恒定, 它與PCD 厚度密切相關,PCD 越厚, 所需電極絲張力應越大。如果張力較小,電極絲的跨距較大,除了其振幅大以外,還會在加工過程中受放電爆炸力的作用而彎曲變形或抖動,造成腰鼓形狀,且會降低模具的切割精度和表面粗糙度等級。電極絲的張力越大,加工時絲的振動幅度越小,加工變得穩定,尺寸精度高,表面質量好。但電極絲張力過大,在加工過程中易造成斷絲,使加工無法繼續。因此,在切割超大孔徑PCD 拉絲模具的壓縮區和安全角時,絲張力應比切割定徑區適當增加10~20,確保角度的精度。
2.2.3 噴流壓力
噴流的壓力及流量直接影響線切割的加工速度和模具表面質量。為了將加工過程中產生的電蝕產物迅速排出,采用強噴流,且PCD 厚度越大,所需的噴流壓力越大, 以便帶走更多的熱量及蝕除物,避免二次放電的發生,且不易斷絲,切割速度提高。但噴流壓力過高,造成電極絲抖動,反而降低了切割速度,同時造成加工精度及表面質量的降低。與電極絲張力調節一樣, 在切割壓縮區和安全角時,噴流壓力應比切割定徑區適當增加5~10 Hz (變頻器頻率),以確保角度的精度。
此外,實驗用機床數據庫中的加工條件給出了另外2 個有益參數,可通過調整其數值對脈沖的持續加工和加工穩定性進行控制。
(1)高壓遮斷
在通常的控制電路中增加遮斷電路和高壓電路,以對放電中單個脈沖的持續加工進行良好的控制。H 值越大,電壓越高;R 和P 值越大,電阻值越小,能量越大。
(2)MAO
調整加工穩定性的參數,通過M 值對加工狀態進行判斷。若加工狀態不穩定,脈沖間隔將根據設定的A 值倍率伸展, 脈沖寬度將被設定的O 值取代,從而提高加工穩定性。M 值越大,進行加工穩定性判斷的頻次越多,影響切割速度;A 值越大,伸展倍率越大,加工越穩定,但切割速度會降低;O 值越小,加工越穩定。通過以上一系列的實驗,摸索出了加工超大孔
徑PCD 拉絲模具的工藝參數(表1)。
表1 加工超大孔徑PCD 拉絲模具工藝參數
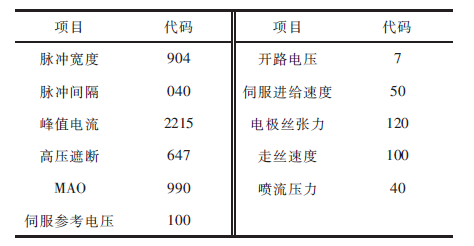
注:表中參數值均以實驗用機床加工條件代碼表示。
2.3 錐度加工的原理及技巧
通過單向走絲線切割機床的錐度切割功能可精確加工壓縮區和安全角,這為高效率、高質量加工超大孔徑PCD 拉絲模具部分區域的角度提供了精度保障。
2.3.1 錐度加工原理
數控單向走絲線切割機床的上、下導絲器兩點形成一條直線,下導絲器中心軸線不動,上導絲器通過步進電機驅動U、V 軸的移動,使電極絲與垂直線偏移角度, 并與X、Y 軸按軌跡運動實現錐度加工。圖6 是錐度加工示意圖,U、V 軸移動距離越大,產生的錐度就越大,實驗用放電加工機的U、V 軸最大移動距離為80 mm。在進行角度區域加工時,應注意U、V 軸的行程是否會超出機床的限定范圍。
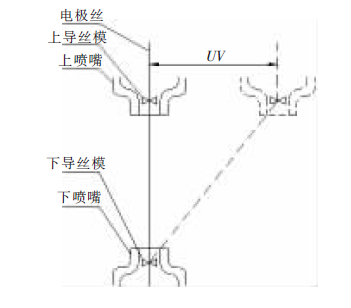
圖6 U、V 運動示意圖
2.3.2 錐度加工程序及加工設定
本切割實驗屬于固定錐度加工,上、下表面具有相同的表面形狀———圓形,編程較簡單。 錐度加工需根據生成的程序進行相關的設定,涉及錐度加工的設定參數主要包括主程序面(編程平面,也是精度尺寸在工件上的位置) 到工作臺面的距離TP、從程序面(工件上另一個有尺寸要求的面)到工作臺面的距離TN 及角度的方向。這3 個參數需正確設定,否則會影響拉絲模具的尺寸、角度所在的位置和角度精度。
2.3.3 噴嘴的干涉檢查
在進行角度切割時,需事先通過加工預演來確定噴嘴與電極絲是否發生干涉。如發生干涉,會造成與實際要求的加工角度不符,可更換規格大的噴嘴或將噴嘴取下。但取下噴嘴會使噴流起不到相應的作用,排屑不通暢會造成斷絲。
2.3.4 錐度加工技巧
在切割壓縮區和安全角時,均帶有不同大小的錐度,由于高壓沖液不能有效地沖入切縫,電蝕產物不能有效排出,易造成斷絲。且帶有錐度區域的切割速度與無錐度區域的切割速度相比要低得多,錐度越大,切割速度越低。適當減小脈沖寬度,降低脈沖能量,可避免發生斷絲。此外,應盡可能保證上、下噴嘴貼近工件表面,改善噴液狀態,并檢查上、下噴嘴,確保其完好無損。錐度加工前,需使用找正器找正電極絲的垂直度(0.01 mm),如果電極絲垂直度誤差較大,將導致超大孔徑PCD 拉絲模具的角度區域在各個方向的錐度不一致,降低角度的精度[5-6]。
3. 結論
(1)隨著脈沖寬度的增加,切割速度呈非線性增加,一般選擇脈沖寬度3~4 μs 區間時,可獲得良好的表面質量及合理的加工速度。脈沖間隔對切割速度影響較大,為確保加工的穩定性,應選取較大的脈沖間隔,一般35~40 μs 為宜。隨著峰值電流的增加,切割速度增加,但表面粗糙度變差,也應在一定范圍內合理選取, 避免電流太大而燒傷工件、太小則無法切割PCD 材料,因此選15 A 左右為宜。適當增加伺服參考電壓,以增加電極和工件之間的放電間隙,使加工穩定。伺服進給速度不能超過加工速度,否則易造成斷絲,欠進給狀態較合適。其他非電參數的選取均以加工穩定、防止斷絲為主要前提條件,因為切割超大孔徑PCD 拉絲模具時不允許斷絲,斷絲處留下的凹槽和凸棱會給后續的研磨加工增加相當大的工作量,浪費時間和成本。
(2)采用單向走絲電火花線切割進行超大孔徑PCD 拉絲模具的定徑區、壓縮區和安全角的粗加工,達到了預期要求,實現了更好的工藝效果,提高粗加工效率近3 倍。一次裝夾,各個區域尺寸的同軸度得到了保證。尺寸余量更小,減少了原工序復雜的整形工序,降低了廢品率。切割后的內芯可制作小孔徑拉絲模具的原始坯料, 比EDM 套料尺寸直徑大1~2 mm,提高一個組距。
(3)以粒度為25 μm 的超大孔徑PCD 拉絲模具為例, 進行單向走絲電火花線切割加工工藝研究,對于不同粒度的PCD 性能有一定的差別,在切割時,工藝參數選擇也應區別對待。
投稿箱:
如果您有機床行業、企業相關新聞稿件發表,或進行資訊合作,歡迎聯系本網編輯部, 郵箱:skjcsc@vip.sina.com
如果您有機床行業、企業相關新聞稿件發表,或進行資訊合作,歡迎聯系本網編輯部, 郵箱:skjcsc@vip.sina.com