電火花放電輔助化學加工間隙實驗研究
2016-11-22 來源:清華大學機械工程系制造工程研究所 作者:劉光 佟浩 何蘇欽 李勇
摘要:面向航空發動機渦輪葉片熱障涂層ZrO2陶瓷絕緣材料的加工,開展了不同加工間隙對加工穩定性及效率影響的實驗研究。采用CCD 圖像在線觀測微觀接觸的對準電極方法,實現了加工間隙測量給定精度可控±1 μm,進而在特定工藝參數下實驗研究了加工間隙的評價和優化,利用工件表面離子濺射鍍膜和Matlab 圖像處理技術實現蝕除量分析,得出了穩定加工時材料最大蝕除量的最佳加工間隙范圍,為電火花放電輔助化學加工工藝優化提供了依據。
關鍵詞:放電輔助化學加工;氧化鋯陶瓷;加工間隙
氧化鋯(ZrO2)陶瓷材料在生物醫療、航空航天、燃氣發電等領域具有廣泛的應用, 如陶瓷義齒、渦輪葉片熱障涂層等。但由于ZrO2陶瓷具有高硬、易脆等特性, 使其在傳統機械加工中難以精密成形,且由于熱應力、切削力等因素,易產生微裂紋,降低了材料使用壽命[1-2]。目前,氧化鋯絕緣陶瓷的非傳統加工方法主要有激光加工[3]、超聲加工[4]、磨料水力噴射[5]等。然而,激光加工會使材料表面產生熱影響、應力集中等而出現微裂紋;超聲加工存在工具磨損嚴重、加工效率低、易產生微裂紋損傷等不足;磨料水力噴射加工用噴嘴需經常更換,且加工精度較低[6-7]。
近年來,有學者采用電火花放電輔助化學加工(apark assisted chemical engraving,SACE)的方法對玻璃、石英等多種絕緣材料進行加工[8-10]。SACE 的材料蝕除原理是在電解液中利用電解原理,在工具電極(陰極)上形成氫氣泡,工具電極端部被氣泡包裹,使工具電極與電解液分離,在絕緣氣泡內瞬間火花放電引導下的電解液內進行蝕除加工,從而實現絕緣材料的加工。該方法無宏觀接觸力、電極損耗小,且電解液內腐蝕加工原理有望實現材料的無損傷加工。國內外研究已驗證了ZrO2陶瓷SACE 加工的可行性,劉永紅等研究了不同電解液對ZrO2陶瓷加工效率的影響[11];張有等在鈦合金基體的氧化鋯陶瓷涂層材料上加工出了直徑1.4 mm 的通孔[12];Doloi 等進行了氧化鋯陶瓷等絕緣材料的SACE 加工工藝研究,分析了電壓、電解液濃度及電極間距等因素對材料去除率的影響[13]。
若要實現SACE 的連續加工, 就需控制工具電極的加工進給,其主要方式有恒力進給和恒速進給兩種。恒力進給是通過控制工具電極與工件的接觸力,實現工具電極的不斷進給;但由于工具電極底部存在液膜,其實質是通過控制接觸力來實現微米級的加工間隙;而恒速進給速度過快,會發生電極與工件碰撞,過慢則嚴重影響加工效率。不論哪種控制方式,目前其合理或最佳加工間隙尚未被闡述清楚,且本研究的前期實驗發現,加工間隙對ZrO2陶瓷SACE 加工穩定性和效率具有較大影響。因此,本研究面向航空發動機ZrO2陶瓷熱障涂層材料加工,通過開展熱障涂層SACE 工藝實驗,探索加工間隙對加工結果的影響,進而通過研究加工間隙的測量方法及合理加工間隙的評價方法,得出在特定參數下的SACE 最優加工間隙。
1.加工間隙對SACE 的影響實驗
實驗系統見圖1,主要包括主軸機構(定位精度為±0.5 μm)、脈沖電源、金屬鎢工具電極、大尺寸石墨輔助電極(電極浸入電解液的表面積至少為工具電極的100 倍以上[14])。實驗采用正極性加工方式,即工具電極為陰極,輔助電極為陽極。實驗主要參數見表1。
主軸采用恒速進給方式,對ZrO2陶瓷工件進行逐層掃描恒速進給加工實驗,SACE 掃描路徑見圖2。為了減少側壁放電的概率并提供氣膜形成的氛圍,工具電極浸入電解液液面約2 mm。實驗過程監測及結果見圖3。實驗發現電極與工件之間的間隙大小對加工穩定性、效率具有顯著
表1 SACE 實驗工藝參數
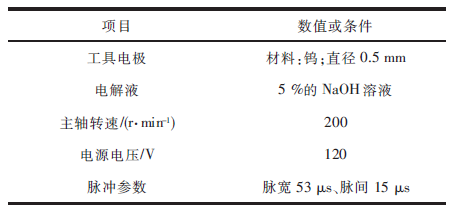
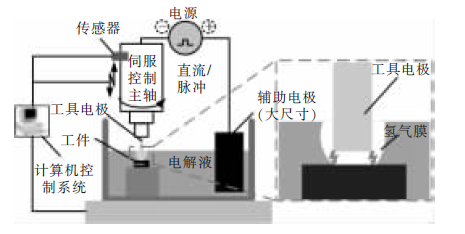
圖1 SACE 實驗系統示意圖
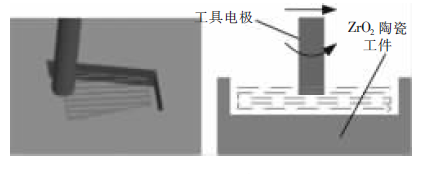
圖2 SACE 掃描路徑規劃
影響。當工具電極與工件表面的間隙過大時,火花放電的瞬間作用在工件表面的爆炸力弱,不足以達到蝕除材料的目的(圖3a);當工具電極與工件表面的間隙過小甚至互相接觸時,對氣膜形態產生了影響,且易產生拉弧現象,這種因電弧放電產生的高溫高熱將使工具電極與工件表面均出現不同程度的燒傷破壞(圖3b)。因此,確定SACE 最佳加工間隙對ZrO2陶瓷穩定加工具有重要意義。
2.加工間隙測量方法
為研究SACE 最佳加工間隙, 首先要實現微米級加工間隙的測量和給定。本研究前期借鑒電接觸測量原理,考慮到ZrO2陶瓷作為絕緣工件,故采用在工件表面放置標準厚度金屬片作為輔助,以滿足電接觸回路形成的條件,從而通過工具電極電接觸輔助金屬片來獲知工具電極與工件之間的相對位置,擬測量并給定加工間隙。
然而,應用中發現該方法的間隙測量精度無法達到要求,其誤差分析見圖4。分析可知,間隙測量誤差主要來源于標準片變形Δ1和工件表面微觀不平度Δ2。由于本研究采用等離子噴涂法制備ZrO2陶
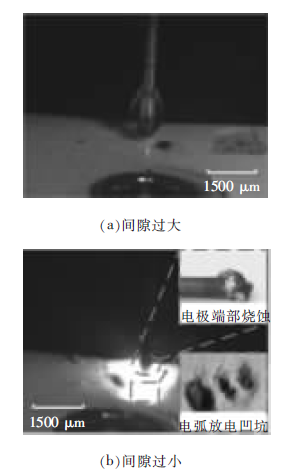
圖3 不同間隙的SACE 放電現象對比
瓷熱障涂層工件,該方法的工藝特點是工件材料表面會呈現微觀不平形貌。實驗中,當采用厚0.2 mm的輔助標準片時,位置誤差甚至達到100~200 μm,已超出預設加工間隙所需的測量精度。因此,為了精確測定加工間隙,實驗采用分辨率為500 萬像素的工業數字攝像機,并利用主軸裝置的高運動分辨率(0.5 μm),通過在線觀測工具電極與工件微觀瞬間接觸狀態,確定工具電極與工件的相對位置。
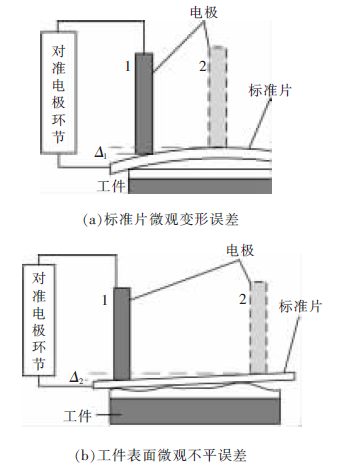
圖4 輔助金屬片對準電極方法的誤差示意圖
如圖5 所示,電極先接近工件表面,并以每步0.5 μm 的進給量逐次進給, 當接觸瞬間CCD 圖像觀測到接觸狀態微觀變化,即認為電極與工件接觸(圖5b);然后,電極回退,直至微觀接觸變化恢復(圖5a),可保證h1和h2在±1 μm 之間,即實現可控的測量精度達±1 μm。這樣,就能精確確定工具電極與工件表面的接觸點位置,再控制電極的回退量即可給定加工間隙。由于工件表面微觀不平,故每個位置的實驗將重復上述步驟。
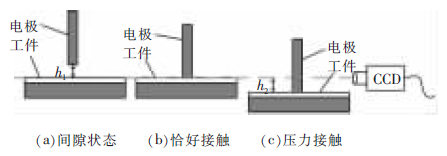
圖5 CCD 圖像觀測對準電極方法示意圖
3.加工間隙優化實驗
給定不同的加工間隙并保持一段時間, 進行ZrO2陶瓷的SACE 加工實驗,通過評價材料去除率和加工過程的放電穩定性,可得出最佳加工間隙范圍。由于白色ZrO2陶瓷工件表面不便觀測材料去除效果, 故對工件表面采用離子濺射金靶的方式鍍膜,使工件表面與基體材料呈現色差,加工后工件表層材料剝離,可與未加工部分形成明顯對比。因納米級厚度鍍膜瞬間即可剝離,故忽略其對實驗效果的影響。
實驗沿用表1 所示的加工參數,通過設定不同加工間隙δ 進行分組實驗,每次實驗保持加工時間5 min。實驗結果見圖6,觀測發現:當加工間隙δ 為150 μm 時,加工痕跡微小;隨著δ 逐漸減小,加工痕跡越來越明顯;當δ 進一步減小時,加工進入穩定階段,加工痕跡增大;當δ 小于某一間隙值時,開始出現明顯的電弧放電現象, 工件表面出現過熱燒蝕,使SACE 不能穩定進行。
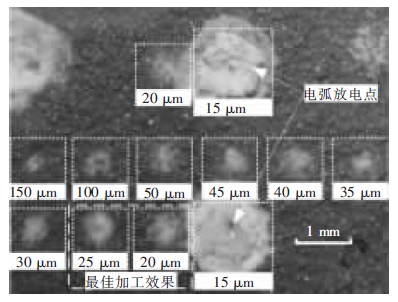
圖6 不同加工間隙δ 對應SACE 加工結果
根據加工過程和實驗結果可認為,在正常穩定放電情況下,材料去除量最大時的加工間隙為最佳加工間隙。因為實驗去除的工件材料為不規則形狀,為便于對比評價材料蝕除量大小,通過圖形處理方法對比加工位置的蝕除面積大小。本研究采用Matlab 軟件對各組實驗結果進行圖像分析處理,對比反顯圖像灰度值0~2 范圍內的像素(圖7),得出不同間隙時材料去除面積的對比情況(圖8),即像值越高,材料去除面積越大。從圖8 可看出,加工間隙δ 為20~25 μm 時,工件材料蝕除量最大,即為該加工條件下的SACE 最佳加工間隙。利用該方法,可評價并得到給定工藝條件下的最佳加工間隙。
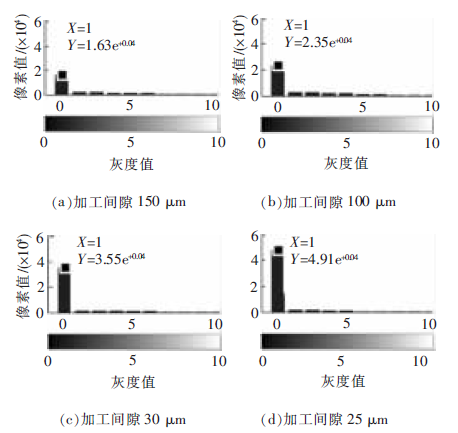
圖7 不同加工間隙的實驗結果灰度圖
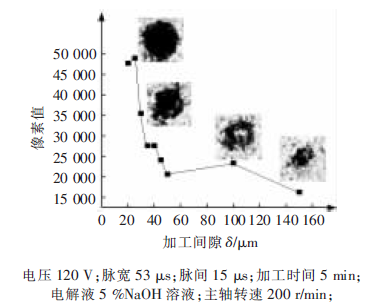
圖8 各組SACE 加工點像素值對比
4.結論
為優化ZrO2陶瓷的放電輔助化學加工(SACE)工藝,探索了加工間隙對工藝過程的影響,開展了加工間隙測量評價及最佳間隙實驗研究,得到如下結論:
(1)當加工間隙過大時,雖然可在電極端部氣泡內放電,但作用于工件上的放電能量過小,難以去除工件材料;加工間隙過小時,易產生電弧放電現象,損傷工具電極和工件。
(2)輔助標準片的電接觸對準電極方法會產生較大的間隙測量誤差(達到100~200 μm),因此采用分辨率為500 萬像素的數字攝像機在線觀測工具電極與工件微觀瞬間接觸變形的對準電極方法,實現了加工間隙在線測量,且給定大小的精度可控達±1 μm。
(3)借助Matlab 圖像分析方法評價加工去除面積, 在本實驗條件下優化得到了正常放電情況下(避免電弧放電) 蝕除面積最大時的最佳加工間隙為20~25 μm。
投稿箱:
如果您有機床行業、企業相關新聞稿件發表,或進行資訊合作,歡迎聯系本網編輯部, 郵箱:skjcsc@vip.sina.com
如果您有機床行業、企業相關新聞稿件發表,或進行資訊合作,歡迎聯系本網編輯部, 郵箱:skjcsc@vip.sina.com
更多相關信息