發(fā)動(dòng)機(jī)動(dòng)、靜葉片激光電火花復(fù)合制孔加工工藝技術(shù)研究
2017-2-9 來(lái)源:中航工業(yè)西安航空發(fā)動(dòng)機(jī)(集團(tuán))有限公司 作者:陳陽(yáng),朱紅鋼,王增坤,王輝明,石銀喜
摘要:激光、電火花制孔這兩種加工方法有一個(gè)共同的、主要的應(yīng)用范圍,即可經(jīng)濟(jì)而高效地對(duì)復(fù)雜的身體形狀作精細(xì)加工,且可應(yīng)用于難加工材料,已成為航空工業(yè)一種不可取代的加工工藝新方法。由于這兩種加工方法有非凡的加工能力和互補(bǔ)優(yōu)勢(shì),當(dāng)今已穩(wěn)定地用在現(xiàn)代航空制造業(yè)中。
關(guān)鍵詞:激光制孔;電火花制孔;復(fù)合加工工藝;動(dòng)靜葉片
在航空發(fā)動(dòng)機(jī)中,各類(lèi)型的動(dòng)靜葉片在氣膜孔加工中,由于葉片鑄造型面不一致、加工工藝欠優(yōu)化、可達(dá)性差等問(wèn)題,存在氣膜孔位置、孔徑超差、連孔等諸多質(zhì)量問(wèn)題,造成激光、電火花都無(wú)法單工藝實(shí)現(xiàn)本工序加工。且各自工藝的短板,成為影響發(fā)動(dòng)機(jī)片動(dòng)靜葉片質(zhì)量的瓶頸及交付。通過(guò)優(yōu)化工藝及加工參數(shù), 同時(shí)采用激光、電火花復(fù)合加工的方式, 對(duì)加工工序進(jìn)行合理調(diào)配,對(duì)零件型面進(jìn)行探測(cè)研究,減少零件型面誤差對(duì)加工的影響。
1.激光、電火花打孔的優(yōu)缺點(diǎn)
1.1 激光打孔
激光打孔的缺點(diǎn):被加工孔的精度和表面粗糙度尚不夠理想。激光打孔的優(yōu)點(diǎn)有:
(1)激光不僅能對(duì)置于空氣中的工件打孔,而且也能對(duì)置于真空中或其他前提下的工件進(jìn)行打孔。
(2)因?yàn)榧庸み^(guò)程與工件不接觸,故加工出的工件清潔。因?yàn)榧庸r(shí)間短,故對(duì)被加工的材料氧化、變形、熱影響區(qū)域均較小,不需特殊保護(hù)。
(3)可加工各種材料的微孔。一般機(jī)械鉆頭只能鉆出直徑大于250 μm 的孔, 而激光則能加工出10 μm 以下的孔。就加工種類(lèi)來(lái)看,不僅可對(duì)金屬而且可對(duì)非金屬甚至橡膠等進(jìn)行鉆孔。從深徑比來(lái)看,用激光打出的孔,其深度與孔徑之比,可高達(dá)50以上,這是用其他加工方法難以達(dá)到的。如用一般方法在極硬的氧化鋁陶瓷上加工小孔所得到的深徑比為2,超聲波法只有4,而激光可達(dá)25。
1.2 電火花打孔的優(yōu)缺點(diǎn)
電火花打孔的優(yōu)點(diǎn)有:
(1)加工孔徑范圍一般在0.3~3 mm 之間,深徑比能達(dá)200∶1 以上。這是其相比于其他工藝非常重要的一個(gè)優(yōu)點(diǎn),即對(duì)小徑深孔的加工。由于高速電火花小孔加工技術(shù)使用水基工作液作為加工介質(zhì),因其電導(dǎo)率大,在極間電壓作用下會(huì)產(chǎn)生介電系數(shù)與水不同的氫氣,從而導(dǎo)致放電間隙增大,增加擊穿延時(shí),提高效率。另外,由于在加工過(guò)程中,脈沖間隔很小,使脈沖頻率大大增加,脈沖電源的有效利用率大大增加,進(jìn)一步提高了效率,獲得了高效的生產(chǎn)率。
(2)加工速度一般能達(dá)20~60 mm/min,且加工深度對(duì)其影響相對(duì)不大,是電火花加工第一次在速度上能與機(jī)械加工相比擬。與常規(guī)電火花小孔加工技術(shù)相比, 由于水基工作液高速地流過(guò)工作間隙,將放電間隙中的蝕除物迅速排出間隙,并有良好的冷卻性能,因而整個(gè)過(guò)程速度快,消電離過(guò)程快,精度高。
(3)直接從斜面、曲面穿入,加工盲孔、深孔、斜孔及異形孔等。
(4)不受材料的硬度及韌性限制,除了能加工一般的導(dǎo)電材料以外,還能順利加工不銹鋼、淬火鋼、硬質(zhì)合金、欽合金、淬鋼等難加工材料。而普通加工方法手材料還有刀具的硬度和韌性限制較大。
(5)加工孔的尺寸一致性,一般能在0.03~0.05mm 之間,圓度在0.02~0.03 mm 之間,表面粗糙度Ra3.5 μm 左右,能滿(mǎn)足一定的垂直度要求。電火花打孔的缺點(diǎn)有:
(1)放電間隙狹窄。電火花放電加工中工具電極與工件間的絕緣工作介質(zhì)有一定的介電常數(shù),放電加工時(shí)有一定的擊穿間隙(放電間隙),因此放電加工后工件的尺寸與工具電極的尺寸并不完全一致。且放電間隙是隨電參數(shù)、電極材料、工作液等因素的變化而變化的,從而影響了加工精度。間隙越大,則復(fù)制精度越差,特別是對(duì)復(fù)雜形狀的加工表面。如電極為尖角時(shí),而由于放電間隙的等距離,工件則為圓角。因此,為了減少加工尺寸誤差,應(yīng)采用較弱小的加工規(guī)準(zhǔn),縮小放電間隙,另外還必須盡可能使加工過(guò)程穩(wěn)定。
(2)易出現(xiàn)加工錐度和圓角。由于工具電極下面部分加工時(shí)間長(zhǎng)、損耗大,因此電極變小,而入口處由于電蝕產(chǎn)物的存在,易發(fā)生因電蝕產(chǎn)物的介入而再次進(jìn)行的非正常放電(即“二次放電”),因而產(chǎn)生加工斜度。這就要求高壓水質(zhì)工作液必須有一定的速度,且持續(xù)工作。
(3)工具電極損耗嚴(yán)重。電火花加工是靠高溫熔化氣化金屬實(shí)現(xiàn)對(duì)工件的加工,工具電極必須是導(dǎo)電金屬用來(lái)傳導(dǎo)電能,所以在高溫和帶電粒子的撞擊作用下工具電極也存在損耗,特別是在電參數(shù)選擇不當(dāng)?shù)那闆r下,電極的損耗更加明顯。
2.實(shí)驗(yàn)過(guò)程及加工工藝方法
2.1 激光加工實(shí)例
某機(jī)的高壓渦輪導(dǎo)向葉片加工組合件需加工排氣邊1 排(8-φ0.7+0.1 0),進(jìn)氣邊3 排(25- φ0.4+0.1 0)共4 排33 個(gè)氣膜孔(圖1)。
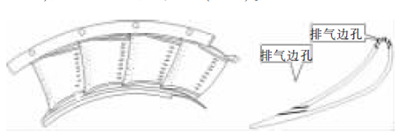
圖1 高壓渦輪導(dǎo)向葉片加工組合件氣膜孔分布示意圖
以前工藝方案為電火花加工,效率低。零件為鑄件,鑄件型面公差大,葉片型面一致性差,孔位置度難以保證。按照要求的葉片型面線輪廓度為0.2mm,由于逐漸的加工難度較大,只能保證葉片型面在0.4 mm 左右,嚴(yán)重影響了氣膜孔加工的位置度。通過(guò)對(duì)現(xiàn)有工藝分析,進(jìn)氣邊3 排孔中,兩排氣膜孔壁薄,孔出口距型腔內(nèi)壁較遠(yuǎn),可塞保護(hù)材料進(jìn)行有效保護(hù),故改為激光加工,因激光加工無(wú)法有效控制加工深度, 另一排距型腔內(nèi)壁很近,無(wú)法添加保護(hù)材料,存在擊傷內(nèi)壁的隱患,所以這排仍采用電火花加工。排氣邊孔為型腔內(nèi)角度斜孔,加工深度大,加工空間狹小,無(wú)法采用激光加工,故仍采用電火花加工。通過(guò)加工工藝的改進(jìn)(圖2),由以前的電火花加工優(yōu)化為激光-電火花復(fù)合加工,從而使加工效率得到很大提高。
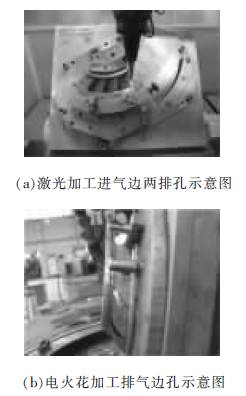
圖2 激光-電火花復(fù)合加工示意圖
存在問(wèn)題:
(1)零件型面對(duì)加工的影響。零件為鑄件,型面公差大且一致性差,加工中需根據(jù)零件型面調(diào)整孔位,加工效率低。型面公差大還影響到加工深度,4排孔的出口都在狹小的型腔內(nèi),空間小(圖3),加工中存在擊傷內(nèi)腔的隱患。加工時(shí)無(wú)法設(shè)定一個(gè)固定的加工深度, 只能根據(jù)加工情況手動(dòng)調(diào)整加工深度,以保證孔徑,避免擊傷零件。
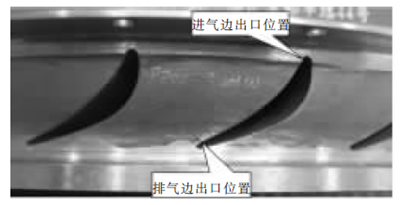
圖3 零件型腔示意圖
為降低零件型面對(duì)孔位置度的影響,加工時(shí)需根據(jù)零件型面情況對(duì)孔位進(jìn)行調(diào)整。孔位調(diào)整步驟為:標(biāo)準(zhǔn)樣件確定加工孔位→編制加工程序→加工試件→測(cè)算試件和標(biāo)準(zhǔn)件型面差異對(duì)孔位的影響量→調(diào)整孔位→修改加工程序→加工正式零件。
(2)排氣邊孔加工效率低。排氣邊孔為型腔內(nèi)的斜孔,加工中選用細(xì)長(zhǎng)桿導(dǎo)向器,避免與夾具發(fā)生干涉。所用電極為400 mm 長(zhǎng)的銅管電極,因選用細(xì)長(zhǎng)桿導(dǎo)向器,使電極的有效使用部分變小,加工效率低。孔的入口位于型腔斜面上,加工可靠性差,加工時(shí)電極沿型面滑動(dòng),孔位確定困難。加工時(shí)選用合理的加工參數(shù),改善加工時(shí)的沖液狀況,以提高加工穩(wěn)定性和加工效率。
2.2 電火花加工實(shí)例
使用ZT-017 型電火花小孔機(jī)床加工, 電極材料為黃銅,直徑分別為0.25、0.35 mm,長(zhǎng)300 mm,加工前找正夾具外圓跳動(dòng)在0.01 mm 以?xún)?nèi)。用去離子水作為工作介質(zhì),電導(dǎo)率為0.1×103 μs/cm。
2.2.1 加工過(guò)程與步驟
(1)裝夾電極,校正電極基準(zhǔn)面與工作臺(tái)的位置精度,保證裝夾可靠。
(2)以榫齒和側(cè)平面為定位基準(zhǔn)面裝夾工件,加工時(shí)將工件以定位面為基準(zhǔn),裝夾后校正與電極的相對(duì)位置。機(jī)床可建立及變更坐標(biāo)系統(tǒng)原點(diǎn),利用高靈敏度和快速響應(yīng)速度的置零功能,能實(shí)現(xiàn)電極對(duì)工件的定位、找正。校正電極與工件的相對(duì)位置后將工件固定,移動(dòng)主軸頭,使電極下端面與工件上平面保持合適的距離。
(3)打開(kāi)工作液泵,將壓力調(diào)到8 MPa,工作液由循環(huán)系統(tǒng)進(jìn)入密封夾頭,再通過(guò)電極中部毛細(xì)管孔進(jìn)入加工區(qū),啟動(dòng)脈沖電源與控制系統(tǒng),調(diào)出編制好的加工程序,準(zhǔn)備進(jìn)行加工。
(4)加工時(shí)根據(jù)加工穩(wěn)定狀態(tài)調(diào)節(jié)進(jìn)給速度、沖液壓力等。通過(guò)參數(shù)顯示屏隨時(shí)觀察孔的加工深度、電極損耗及加工時(shí)間等。加工過(guò)程中應(yīng)抽查孔的尺寸和加工表面情況,以保證零件的加工品質(zhì)。
2.2.2 試驗(yàn)結(jié)果
試驗(yàn)加工參數(shù)見(jiàn)表1,試驗(yàn)現(xiàn)場(chǎng)見(jiàn)圖4。利用電火花工藝進(jìn)行高壓渦輪葉片氣膜孔加工,產(chǎn)品品質(zhì)明顯改善,效率與葉片加工合格率大幅提高,零件合格率提高到80.7 %,加工成本顯著降低。加工品質(zhì)與效率的提高使發(fā)動(dòng)機(jī)的按時(shí)交付得到了保證。
表1 氣膜孔電加工參數(shù)
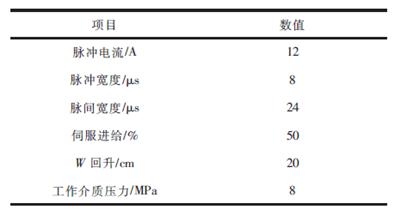
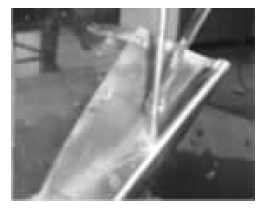
圖4 工作葉片加工現(xiàn)場(chǎng)
2.2.3 加工工藝難點(diǎn)分析與對(duì)策
在試驗(yàn)過(guò)程中發(fā)現(xiàn),采用小孔機(jī)加工氣膜孔的難點(diǎn)主要表現(xiàn)在加工深度控制、加工設(shè)備穩(wěn)定性與精度的提高、加工中硬件故障的判斷與排除等。在分析原因的基礎(chǔ)上, 結(jié)合實(shí)際情況來(lái)制定解決措施,取得了良好效果。
2.2.4 加工深度的控制
由于目前使用的電火花加工設(shè)備使用半閉環(huán)系統(tǒng),加工深度信號(hào)沒(méi)有反饋,所以無(wú)法準(zhǔn)確控制加工深度。高壓渦輪葉片, 內(nèi)腔距離僅為0.198~0.215 mm。如何保證既把孔打通又不打傷或打穿葉片內(nèi)腔對(duì)面基體的難度非常大。現(xiàn)采取以下措施來(lái)解決問(wèn)題。
(1)軟阻斷。計(jì)算出所有孔各截面穿頭深度,根據(jù)電極長(zhǎng)度消耗值,按尺寸公差偏上差計(jì)算加工深度,并將深度值固化在程序中,控制電極加工深度。
(2)硬阻斷。將一個(gè)長(zhǎng)80 mm、寬1.85 mm、厚0.8 mm 的銅條插入葉片腔體, 用來(lái)阻擋電極損耗,防止打傷或打穿葉片。
(3)補(bǔ)加工工藝方案。當(dāng)遇到葉片壁厚不均勻、電極品質(zhì)不好、機(jī)床故障等特殊情況,造成孔沒(méi)有打通時(shí),分別編制了直徑0.3、0.5 mm 孔的補(bǔ)加工程序,對(duì)通孔位進(jìn)行補(bǔ)加工。
2.4.5 加工設(shè)備穩(wěn)定性與精度的提高
試驗(yàn)發(fā)現(xiàn),電火花設(shè)備的B 軸、旋轉(zhuǎn)頭、泵、電器等設(shè)備易出現(xiàn)故障。B 軸剛性差, 易出現(xiàn)位置偏移,造成第6~9 排孔的位置度極易不合格;旋轉(zhuǎn)頭不轉(zhuǎn)、碳刷接觸不好及導(dǎo)向器同心度不好等;高壓泵正常使用壓力為6 MPa 以下,而加工需8 MPa 的高壓,這就使高壓泵超常運(yùn)行,再加上設(shè)備全天不間斷運(yùn)行,使高壓泵的許多部件疲勞運(yùn)行,其故障必然頻繁發(fā)生,主要損傷的部件有過(guò)濾器、節(jié)流墊、節(jié)流閥、滾珠、電動(dòng)機(jī)等。另外,由于疲勞運(yùn)行,工作液里含有電蝕物及部分金屬微粒,再加上某些泵的品質(zhì)問(wèn)題,使低壓泵也常有故障發(fā)生,嚴(yán)重影響電火花機(jī)床的效率。實(shí)踐證明,通過(guò)下述措施可有效解決故障問(wèn)題。
(1)重新編制一個(gè)新程序,對(duì)6~9 排孔單獨(dú)加工,以保證其空間位置不受機(jī)床缺陷的影響。
(2)新旋轉(zhuǎn)頭采用陶瓷軸承,防止了銹蝕和電蝕,一般壽命提高3~6 倍。
(3)通向電極的電流直接連接碳刷,減少電流流經(jīng)的中間環(huán)節(jié),降低了故障率,也提高了系統(tǒng)加工的穩(wěn)定性。
(4)優(yōu)選高、低壓泵,通過(guò)多品牌、多型號(hào)泵的運(yùn)轉(zhuǎn)試驗(yàn),選擇壽命長(zhǎng)、參數(shù)和性能穩(wěn)定的泵進(jìn)行加工。
(5)對(duì)主要損傷部件增加了庫(kù)存量,使設(shè)備可進(jìn)行長(zhǎng)時(shí)間、不停機(jī)加工,提高緊迫生產(chǎn)任務(wù)的應(yīng)變能力。
(6)定期對(duì)高、低壓泵進(jìn)行檢查,如發(fā)現(xiàn)異常情況立即更換, 并對(duì)更換下來(lái)的高壓泵進(jìn)行檢查、維護(hù)、修理。
(7)對(duì)計(jì)算機(jī)系統(tǒng)軟件進(jìn)行修改和升級(jí),對(duì)原時(shí)間當(dāng)量由原來(lái)的30 s 改為10 s,有效降低了超差品的概率和機(jī)床故障率。
3.成效及結(jié)論
激光打孔不論材料的種類(lèi)和硬度都可進(jìn)行,故應(yīng)用范圍較廣,但因精度較差,重復(fù)精度也較低,所以用量、規(guī)模都不是很大。但對(duì)一些特殊零件,采用激光打孔卻取得了很大的效益。渦輪葉片氣膜孔的加工采用激光旋切,盡管在孔壁局部范圍尚存在重熔層,最大厚度<0.05 mm,個(gè)別孔存在微裂紋,但不進(jìn)入基體。另外,激光打孔對(duì)高硬度、非導(dǎo)體材料的微小孔、孔數(shù)量很大的零件進(jìn)行加工也很有優(yōu)勢(shì)。電火花打孔最突出的特點(diǎn)是其重熔層厚度僅為激光打孔重熔層厚度的一半, 可控制在0.02 mm以?xún)?nèi),能滿(mǎn)足所有發(fā)動(dòng)機(jī)動(dòng)、靜葉片的冶金質(zhì)量要求。對(duì)于某些位于葉身型面的氣膜冷卻孔,可使用高速電火花打孔機(jī)床, 重熔層厚度一般在0.04 mm以?xún)?nèi)。
激光打孔工藝不需工作電極,在數(shù)控工作臺(tái)上安裝零件不需制作復(fù)雜的工裝,氣膜冷卻孔的尺寸可任意調(diào)節(jié),最適宜作為新機(jī)研制時(shí)打孔的工藝方法。電火花打孔成本低,加工質(zhì)量比激光加工重熔層薄。在加工氣膜孔的過(guò)程中,將電火花及激光工藝共同融入其中,合理地調(diào)整加工工序,會(huì)大大地提高零件的加工質(zhì)量及效率,同時(shí)也會(huì)降低其加工成本。通過(guò)采用電火花加工、激光加工兩種工藝方法,對(duì)零件工序進(jìn)行合理調(diào)配,并對(duì)工藝方法和加工參數(shù)進(jìn)行優(yōu)化。
隨著先進(jìn)制造技術(shù)的發(fā)展,新的氣膜孔加工工藝不斷被開(kāi)發(fā)出來(lái),對(duì)帶有陶瓷涂層葉片的氣膜孔加工,公司內(nèi)部現(xiàn)正在使用的加工工藝是先加工冷卻氣膜孔,再涂覆陶瓷,最后用微型鉆頭在相應(yīng)的孔位處去除陶瓷涂層,其工序復(fù)雜、效率低、質(zhì)量不易控制。現(xiàn)在使用激光電火花復(fù)合加工技術(shù),可在相應(yīng)的打孔位置上精確地用激光去除陶瓷涂層,再使用高速電火花精確打孔, 縮短了零件的加工周期,確保了加工質(zhì)量。同時(shí),為公司各類(lèi)型動(dòng)、靜葉片零件的加工摸索出可行的工藝方案, 此方法也可在其他機(jī)種的零件中應(yīng)用, 拓寬了該方法的用途。因此,激光、電火花復(fù)合加工工藝的研發(fā),對(duì)航空發(fā)動(dòng)機(jī)的制造有著深遠(yuǎn)意義。
投稿箱:
如果您有機(jī)床行業(yè)、企業(yè)相關(guān)新聞稿件發(fā)表,或進(jìn)行資訊合作,歡迎聯(lián)系本網(wǎng)編輯部, 郵箱:skjcsc@vip.sina.com
如果您有機(jī)床行業(yè)、企業(yè)相關(guān)新聞稿件發(fā)表,或進(jìn)行資訊合作,歡迎聯(lián)系本網(wǎng)編輯部, 郵箱:skjcsc@vip.sina.com
更多相關(guān)信息
業(yè)界視點(diǎn)
| 更多
行業(yè)數(shù)據(jù)
| 更多
- 2025年1月 新能源汽車(chē)銷(xiāo)量情況
- 2024年12月 新能源汽車(chē)產(chǎn)量數(shù)據(jù)
- 2024年12月 基本型乘用車(chē)(轎車(chē))產(chǎn)量數(shù)據(jù)
- 2024年12月 軸承出口情況
- 2024年12月 分地區(qū)金屬切削機(jī)床產(chǎn)量數(shù)據(jù)
- 2024年12月 金屬切削機(jī)床產(chǎn)量數(shù)據(jù)
- 2024年11月 金屬切削機(jī)床產(chǎn)量數(shù)據(jù)
- 2024年11月 分地區(qū)金屬切削機(jī)床產(chǎn)量數(shù)據(jù)
- 2024年11月 軸承出口情況
- 2024年11月 基本型乘用車(chē)(轎車(chē))產(chǎn)量數(shù)據(jù)
- 2024年11月 新能源汽車(chē)產(chǎn)量數(shù)據(jù)
- 2024年11月 新能源汽車(chē)銷(xiāo)量情況
- 2024年10月 新能源汽車(chē)產(chǎn)量數(shù)據(jù)
博文選萃
| 更多
- 機(jī)械加工過(guò)程圖示
- 判斷一臺(tái)加工中心精度的幾種辦法
- 中走絲線切割機(jī)床的發(fā)展趨勢(shì)
- 國(guó)產(chǎn)數(shù)控系統(tǒng)和數(shù)控機(jī)床何去何從?
- 中國(guó)的技術(shù)工人都去哪里了?
- 機(jī)械老板做了十多年,為何還是小作坊?
- 機(jī)械行業(yè)最新自殺性營(yíng)銷(xiāo),害人害己!不倒閉才
- 制造業(yè)大逃亡
- 智能時(shí)代,少談點(diǎn)智造,多談點(diǎn)制造
- 現(xiàn)實(shí)面前,國(guó)人沉默。制造業(yè)的騰飛,要從機(jī)床
- 一文搞懂?dāng)?shù)控車(chē)床加工刀具補(bǔ)償功能
- 車(chē)床鉆孔攻螺紋加工方法及工裝設(shè)計(jì)
- 傳統(tǒng)鉆削與螺旋銑孔加工工藝的區(qū)別