整機全三維仿真技術加速航空發動機研發
2023-7-18 來源:航空動力 作者:張衡 曾軍 張劍
導語
整機全三維仿真技術作為加快航空發動機研發的數字引擎,可在虛擬數字空間實現發動機整機全三維性能高精度快速預測,解決發動機整機匹配問題,縮短研發周期、降低研制風險和成本,實現從傳統設計到預測設計的模式轉變,加速航空發動機研發進程。
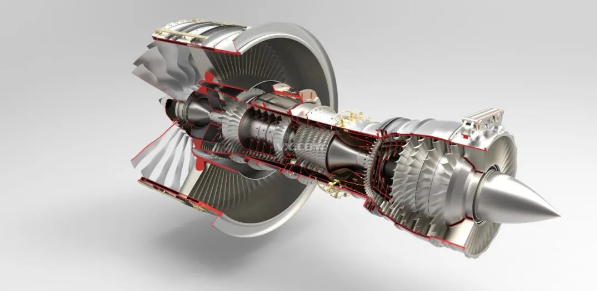
傳統航空發動機的研制采用的是“設計、試驗驗證、修改設計、再試驗”反復迭代的串行研制模式,特別是整機性能更是需要通過大量的試驗進行驗證,這將導致驗證周期長、試驗成本和風險高,無法滿足當前航空發動機快速研制的需求[1-2]。目前,整機性能評估方法主要停留在一維階段,各個部件之間的參數傳遞精度、維度都比較低,極大地影響了發動機整機性能參數的準確評估[3]。隨著計算流體力學(CFD)技術和信息技術的快速發展,發動機整機全三維仿真已經成為可能,該技術可預測發動機穩態條件下的整機性能、預估部件之間匹配工作狀態、指導部件之間一體化設計、為部件設計提供技術依據。同時,整機仿真工作有助于促進航空發動機整機研發從一維向三維設計發展,極大地提高航空發動機總體設計精度和水平,進一步完善航空發動機設計體系。
研究方案
為快速形成整機全三維仿真能力,加快推進整機仿真技術在發動機工程研制中的轉化運用,急需做到提高仿真精度和加快仿真進度。為此,創新團隊按照航空發動機正向研發的思路,提出了航空發動機整機CFD仿真方法研究方案,如圖1所示。一方面,為提高整機仿真精度,通過開展整機復雜模型建模方法、網格生成技術、高精度求解算法等方法研究,形成一套適合工程使用的整機仿真方法與工具;另一方面,為加快仿真進度、縮短整機仿真周期,開發了一套標準化的整機仿真平臺,優化仿真流程、集成核心算法、固化仿真經驗,最終建立整機全三維仿真設計體系,以支持航空發動機快速研制。
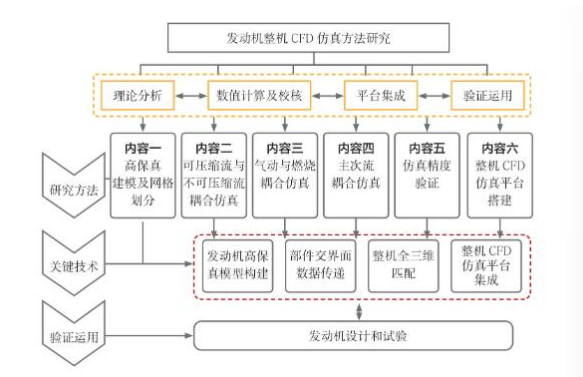
圖1 項目研究方案
關鍵技術
整機全三維仿真關鍵技術主要包括高保真模型構建技術、部件交界面數據傳遞技術、整機全三維匹配技術、整機CFD仿真平臺集成技術。為攻克上述關鍵技術,開展了以下6個方面的研究工作。
高保真幾何建模及網格劃分
針對發動機整機模型保真度問題,開展了整機高保真幾何模型快速獲取方法研究。為提高模型精度,全方位梳理了發動機各部件真實技術狀態,例如,風扇、壓氣機可調導向葉片根尖間隙,渦輪葉片軸向、徑向間隙,可調噴管喉部面積等,以提高發動機模型保真度。掌握了整機各部件高保真物理模型快速處理方法,葉輪機部件直接采用定制葉型輸出文件,通過程序轉化輸出標準化的格式。燃燒室、加力燃燒室、噴管等采用計算機輔助設計(CAD)軟件生成三維實體,并對細節結構進行適當簡化,通過該方法解決了整機復雜模型高保真幾何建模關鍵技術,完成了整機復雜模型界面劃分及內流域模型構建。
隨后,開展了整機幾何模型網格快速劃分方法研究。針對常規的壓氣機流道及渦輪流道網格劃分可以采用模板化的全六面體網格劃分工具生成,但針對部分非常復雜的幾何模型,如發動機外涵道、燃燒室、加力燃燒室及噴管的網格劃分需要采用非結構化網格生成工具進行劃分。通過深入研究復雜結構網格的分網策略,將幾何結構關鍵參數對分網結果的影響規律進行提煉和總結,最后生成自動化分網腳本文件,實現上億級網格的自動化快速劃分。通過該方法完成了整機各部件復雜模型網格劃分,并串裝完成整機網格模型,如圖2所示。
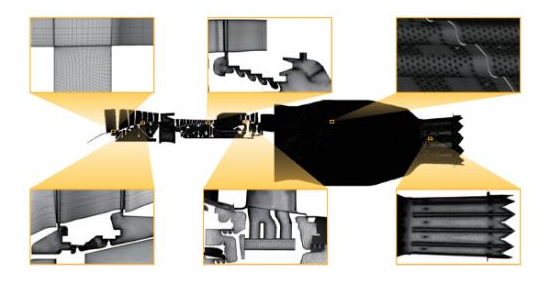
圖2 發動機整機及局部網格示例
可壓縮流與不可壓縮流高精度耦合仿真
為解決可壓縮流與不可壓縮流耦合仿真問題,針對發動機風扇、壓氣機、渦輪等高速可壓縮流與燃燒室及部件盤腔等低速不可壓流相互耦合仿真方法進行了研究。重點開展了燃燒室與渦輪部件耦合求解方法研究。從發動機燃燒室與渦輪耦合仿真結果,可以看到主燃燒室核心區速度很低,屬于不可壓縮流動,渦輪導向器區域為高速的可壓縮流,通過多方位對湍流模型參數選取及交界面數據傳遞參數的設定,最終實現了主燃燒室與渦輪高精度耦合仿真(見圖3),獲取了不可壓縮流與可壓縮流參數的高精度耦合數據傳遞方法。
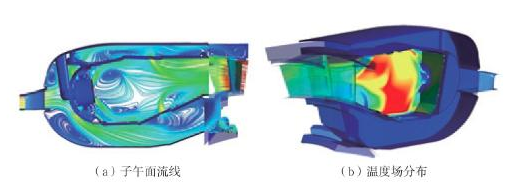
圖3 發動機燃燒室與渦輪耦合仿真
高精度氣動與燃燒耦合仿真
由于燃燒室或加力燃燒室內部存在燃油的霧化、蒸發、摻混、快速化學反應等多相流流動特點,而壓氣機、渦輪內部高速流動存在高流動曲率、激波尾跡邊界層相互作用、封嚴流與主流相互摻混現象。因此,燃燒室流動模擬和葉輪機部件內流存在非常明顯的差異,需要對氣動與燃燒耦合仿真模型進行針對性研究,從而確保較高的仿真精度。重點需要突破復雜反應流和葉輪機械高速內流高精度仿真模擬技術,并結合當前模擬仿真結果和試驗結果,對模型參數進行考核驗證和精度評判。為此,針對整機全加力狀態全三維仿真存在的燃燒模型精度低的問題,對加力燃燒模型進行了改進,攻克了加力出口溫度過高問題,并形成了一套具有完全自主知識產權的新化學反應模型,評估精度提升40%以上。圖4為一型發動機全加力狀態下整機全三維仿真結果,通過與試驗數據對比表明,加力燃燒室出口溫度評估精度得到大幅提高,并準確獲取了發動機最大狀態下的性能參數。
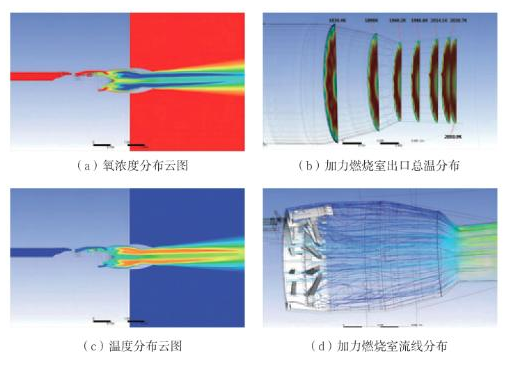
圖4 發動機全加力狀態高精度氣動與燃燒耦合仿真
發動機主流與空氣系統次流耦合仿真
為了認識發動機主流路、容腔流路和盤腔流路相互干擾作用下的內部流動特征,精準評估發動機軸向力、空氣系統流路詳細分配,進一步提高發動機整機全三維仿真精度,需開展考慮主次流影響的發動機整機全三維仿真研究[4]。考慮到整機主次流全三維模型復雜、網格量大、計算時間長等問題,為減小技術風險,采用由簡到繁、由易到難的研究方法。首先開展了考慮主次流影響的風扇、壓氣機、渦輪等單部件仿真技術研究,獲取單部件主次流耦合流動規律及仿真方法,隨后將各部件網格模型進行組裝并通過賦值初場方式進行計算求解,獲得了發動機整機全三維主次流耦合仿真結果。通過與試驗結果對比,考慮了主次流耦合的整機全三維仿真結果精度更高,同時還可以精準獲取發動機轉子軸向力與整機空氣系統流量分配,軸向力評估精度高達5%,空氣流量分配精度為2%,這為發動機設計和試驗提供了良好的數據支撐作用。
整機仿真精度驗證
為驗證整機仿真精度,提高整機仿真方法的工程適用性,開展了基于發動機系統的試驗數據整理及分析工作,實現了對整機全三維仿真方法的校核與精度的驗證,發展一套高精度的整機性能預測方法。圖5為一型小涵道比發動機整機CFD仿真結果與試驗測量結果對比,其中pt為總壓、Tt為總溫、W 為流量、π 為部件膨脹比、F 為發動機推力,SFC為耗油率[5],經過試驗數據驗證表明整機性能預測模型具有較高的評估精度,發動機進口流量偏差為1%以內,推力偏差為2%左右。圖6與圖7分別給出了壓氣機與渦輪出口參數沿徑向分布與試驗對比曲線,通過對比分析發現三維仿真獲取的徑向參數分布精度為3%左右,充分表明發動機整機全三維仿真技術已達到了一個較高的水平,可以直接應用于航空發動機的設計和試驗。
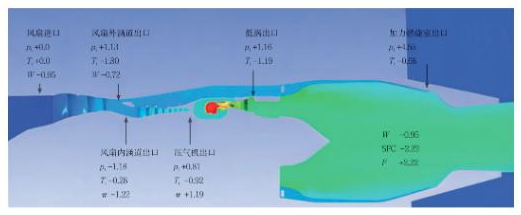
圖5 小涵道比發動機整機仿真結果與試驗測量結果對比
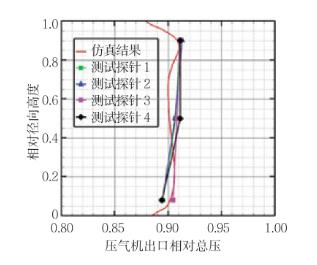
圖6 壓氣機出口總壓徑向分布
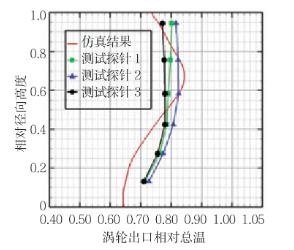
圖7 低壓渦輪出口總溫徑向分布
整機CFD數字化仿真及管理平臺
為提高整機仿真效率,實現參數自動化、標準化輸入輸出,搭建了整機CFD數字化仿真及管理平臺,實現對各部件模型、網格、邊界條件集中統一管理,確保獲取的模型與網格能實時隨發動機真實技術狀態更新而自動更新。搭建完成的整機全三維仿真平臺集成了整機仿真自動化的前后處理模塊,可實現對計算模型的邊界條件快速加載與整機性能參數的快速獲取,讓仿真耗時從原有的16周降低到只有4周,大幅提升了仿真效率。
結束語
航空發動機整機全三維仿真技術實現了整機性能參數的快速高精度預測,借助整機仿真,加速了發動機的研制步伐,縮短了研制周期,降低試驗風險,確保了“設計一次到位,試驗一次成功”。目前,該方法已通過多個型號發動機項目的成功實踐,指導了發動機設計、試驗及排故工作,充分驗證了創新項目對加快航空發動研制的重要意義。同時,創新團隊還總結了項目成果,全方位梳理了整機仿真流程,搭建了一套完善的數字化仿真平臺,總結出了一系列設計標準、指南和規范,為豐富與完善研發體系建設提供了有力支撐。
投稿箱:
如果您有機床行業、企業相關新聞稿件發表,或進行資訊合作,歡迎聯系本網編輯部, 郵箱:skjcsc@vip.sina.com
如果您有機床行業、企業相關新聞稿件發表,或進行資訊合作,歡迎聯系本網編輯部, 郵箱:skjcsc@vip.sina.com
更多相關信息