葉片泵轉子葉片槽的分度銑床夾具設計
2017-7-7 來源:北京工商大學材料與機械工程學院 作者:劉玉德,侯亞茹,吳 剛,張 浩,王 碩
摘要:設計用于臥式銑床加工的葉片泵轉子葉片槽的分度銑床夾具,銑刀每次加工一個槽,通過分度裝置使工件轉動一定角度到達加工位置,依次完成其它槽的加工。
關鍵字:葉片泵;分度;銑床;夾具
0.引言
夾具最早出現在 18 世紀后期, 隨著科學技術的不斷進步,夾具已從一種輔助工具發展成為門類齊全的工藝裝備。 夾具可快速、方便地將工件安裝到指定位置,大幅提高了產品精度,使工藝更加便捷
,使用相當廣泛。 按用途分,可將夾具分為焊接夾具、機床夾具、裝配夾具、檢驗夾具等。
1.零件圖分析
被加工的零件如圖 1 所示, 零件的毛坯為 40Cr,金屬模鑄造,技術要求與尺寸精度都不高,生產批量為 2 000 件,其加工工序為:車外圓,保證 Φ50mm 外圓→車端面,保證 24mm 的長度→中心鉆孔、擴孔、鉸孔至尺寸要求→銑槽。 其中,銑槽的過程需要用到分度裝置,銑刀每加工一個槽,通過分度裝置使工件轉動一定角度到達加工位置,以便完成其它槽的加工。
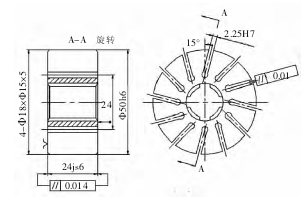
圖 1 工件零件圖
2.夾具設計
保證工件加工質量是機床夾具設計的基本要求,也是夾具設計的首要任務。 為此,必須正確地設計與選擇定位方法、定位件及夾緊裝置。 在設計之前,要認真了解工件的作用、特點、材料、生產規模及技術要求, 詳細分析加工工藝過程及本工序的加工要求,如加工余量、加工精度、加工表面、定位基準以及前后工序的聯系等。 本文夾具的設計主要分成以下幾個方面:定位方案、夾緊方案、分度裝置、夾具體和連接元件的設計。
2.1 定位方案
工件定位是指在工件加工之前,將工件放在相對于機床、刀具一個比較準確的加工位置。 工件的定位,實質上是對空間自由度的限制,根據工件自由度被約束的情況,工件定位方式有完全定位、不完全定位、欠定位、過定位 4 種。本設計因加工的需要,在銑槽的過程中零件不能發生任何移動,6 個自由度都要進行約束,故選用完全定位。 定位方法為花鍵孔和主軸端面定位,圖 2 為定位主軸設計圖。
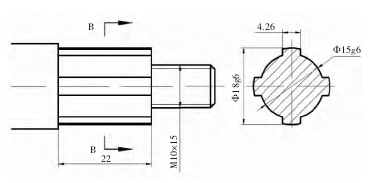
圖2 定位主軸圖
空間 6 個自由度的限制,雖然解決了工件在加工過程中“定與不定”等問題,但每個工件在加工過程中所占據的位置并不一致,這就涉及到“準與不準”的問題。 工件在夾具中所占據的位置不準確,加工的工件尺寸必然不一致,就會形成誤差,稱之為定位誤差,用ΔD 表示。 生產中為了保證加工精度,一般要求定位誤差不超過工件加工公差 T 的 1/5~1/3。 定位誤差包括基準位移誤差和基準不重合誤差,當無基準位移誤差時,ΔY=0;當定位基準與工序基準重合時,ΔB=0;若兩項誤差均沒有, 則 ΔD=0。 分析和計算定位誤差的目的,是為了驗證定位方案能否保證定位要求,以便對不同方案進行比較,從而選出最合理的方案。從零件設計要求可知, 工件和軸的配合尺寸為φ18H7/g6, 查閱國標軸、 孔的基本偏差表有:ΔB=0;ΔY=ES-ei=0.021-(-0.017)=0.038mm;ΔD=0.038mm。按照 GB/T 1804—2000 《未注公差的線性和角度尺寸公差》要求,指明工件加工公差等級為中等 m,則T =0.1 -(-0.1) =0.2mm。 而 ΔD =0.038mm ≤(1/5 ~1/3)T =0.04~0.067mm,定位方案合格。
2.2 夾緊方案的設計
在夾緊過程中,工件應能保持在既定位置,即在夾緊力作用下工件不應離開定位支承;夾緊力的大小要適當、可靠。 既要使工件在加工過程中不產生移動和振動,又不使工件產生不允許的變形和損傷,夾緊裝置的自動化程度和復雜程度應與工件的產量和批量相適應。夾緊裝置主要由動力裝置、中間遞力機構、夾緊元件組成。 常用的夾緊裝置有楔塊、螺旋、偏心輪等,楔塊夾緊可改變夾緊力方向,但使用效率低,多用于機動夾緊裝置中;螺旋夾緊結構簡單、自鎖性好、夾緊可靠、緊行程不受限制,遠比楔塊夾緊力大,其通用性大,但效率低,多用于手動夾緊裝置中;偏心夾緊機構產生的夾緊力較小,自鎖性能不好,一般用于切削力不大且無振動的場合,對夾緊尺寸要求嚴格。 可見各夾緊裝置都有各自的優缺點,應結合設計要求選擇合理的夾緊裝置。 綜合以上特點,本設計選用螺旋夾緊裝置。花鍵主軸上的螺桿、開口墊圈和夾緊螺母為主要的夾緊元件。 當旋緊夾緊螺母時,通過開口墊圈將工件夾緊在花鍵主軸上。 查閱資料,旋緊螺母時使用扳手的六角螺母:當螺紋直徑=10mm,螺距=1.5mm,手柄長度=120mm,作用力=45N 時,夾緊力=3550N。為了保證裝夾的穩固和加工時的剛性,需要在夾具后部設置支承機構,將安裝工件的螺桿頂住,如圖 3所示。 支撐機構中除頂尖外,還有尾架、端蓋、螺桿、鎖緊旋鈕、手輪、手柄等。 通過手輪、手柄使螺桿旋轉,推動頂尖向左移動, 從而將花鍵主軸上的螺桿部分頂住,再擰緊鎖緊旋鈕,防止頂尖松動。 尾架和端蓋在這個機構中起支撐作用。
2.3 分度裝置的設計
分度裝置是能夠實現角向或直線均分的裝置。 工件被夾緊,完成一個工位的加工后,夾具不松開,工件通過移動一段距離或者轉動一個角度,達到下個加工工位,從而完成整個工件的加工。 由零件的設計要求可知,槽的分度精度要求并不高,因此采用圓柱銷定位分度結構,該結構簡單、易制造。 操縱機構選用手拉式,如圖 4 所示。 通過轉動手柄,根據手柄轉動的圈數來確定加工的工件旋轉角度。 旋轉一定角度后,將定位銷通過手柄上的孔插入到分度盤上的槽中,實現分度的鎖緊。
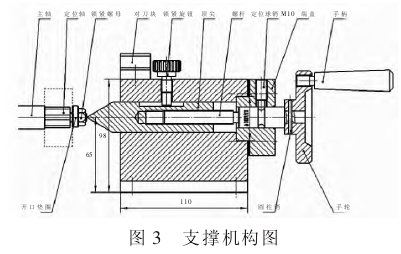
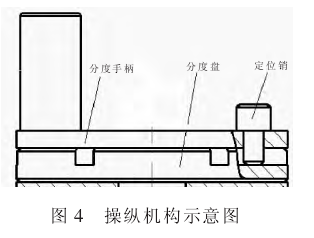
分度的傳動機構是通過蝸輪蝸桿傳動來實現的,其特點是傳動平穩、嚙合沖擊小,能獲得較大的傳動比,且結構緊湊。 蝸桿是齒數 z1=1 的單頭蝸桿,蝸輪的齒數 z2=30,即蝸桿轉動一圈,蝸輪轉動 1/30 圈。 應工件加工要求,每加工一個槽工件轉動 30°,即蝸輪轉動1/12 圈。 由此可計算出蝸桿所需轉動的圈數為 2.5 圈,即轉動分度手柄時,每次轉動兩圈半即可。 蝸輪蝸桿傳動機構及分度盤如圖 5、圖 6 所示。
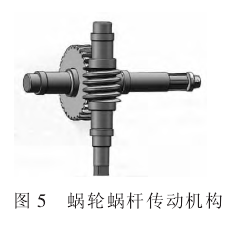
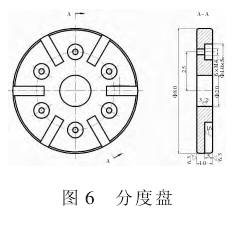
(1)定位鍵。 銑床夾具以定位鍵和機床工作臺 T型槽配合,每個夾具一般設置兩個定位鍵,起夾具在機床上的定向作用,并用埋頭螺釘把定位鍵固定在夾具體的鍵槽中。 材料選用 45 鋼。(2)帶 U 型槽的耳座。 在銑床夾具縱向兩端底邊上,設計帶 U 型槽的耳座,機床上有對應的螺孔,螺栓穿過 T 型槽與機床上的螺孔,將夾具體緊固在工作臺上。 材料選用 HT300。
2.5 夾具體的設計
夾具體一般是夾具上最大最復雜的基礎元件,其形狀和尺寸主要取決于組成該夾具的各種元件、機構和裝置。 同時,在進行夾具設計時,還應考慮到因夾緊力、切削力而產生的沖擊和振動,保證夾的強度和剛度需求。 另外,在銑槽的過程中,會有一些碎屑掉到夾具體里面, 時間長了會損害傳動機構或其它零件,為保證夾具正常工作,應考慮到排屑的方便性,且夾具應該便于裝卸。本夾具體采用鑄造結構, 鑄造的生產周期長,且因鑄造時的內應力緣故,易引起變形,從而影響夾具體精度的持久性。 為此,鑄造夾具體必須進行時效處理,而與焊接結構相比,鑄造可以鑄出形狀復雜的結構, 故本夾具體采用鑄造結構比較合適。 材料選用HT200,壁厚 4mm。3 結語本文分析了被加工工件的特點、作用、材料、生產規模及技術要求,并通過相關計算設計了一套專用的帶分度裝置的銑床夾具。實際上,在生產中,零件的狀是千差萬別的,沒有任何一種夾具能適用于所有的零件,合理、靈活的設計并使用夾具能夠降低生產成本,提高工作效率,降低廢品率。
投稿箱:
如果您有機床行業、企業相關新聞稿件發表,或進行資訊合作,歡迎聯系本網編輯部, 郵箱:skjcsc@vip.sina.com
如果您有機床行業、企業相關新聞稿件發表,或進行資訊合作,歡迎聯系本網編輯部, 郵箱:skjcsc@vip.sina.com