螺旋銑削在數控銑加工中的運用探究
2022-2-8 來源: 廣東省國防科技技師學院 作者:林柔瑄
摘要:在數控機床加工行業不斷發展的大環境下,數控機床的形式和種類也越來越多樣化,其中數控銑床就是常見的一種,在整個數控加工機床行業中發揮著不可替代的作用。在數控銑削加工實際生產操作中,加工的零件產品要求越來越高,對產品的外形邊變化也越來越復雜,為了達到越來越嚴苛的要求,我們要深入的研究生產加工技術以達到我們預期的效果,其中螺旋銑削對提高數控銑削的加工效果有很大的價值。因此,為了更好地實現數控銑削,有效提高加工效率,有必要科學合理地應用螺旋銑削。
關鍵詞:螺旋銑削;數控銑加工;運用探究
0、引言
經濟的發展,離不開工業的發展,近年來我國經濟發展迅速,數控加工技術的有力推動有著必不可少的因素。現如今各行各業只要涉及到機械加工的企業都離不開數控的身影,而數控機床的普及,也讓加工生產變得更加經濟和效率,讓加工產品的精度也在不斷地提高。數控機床的種類很多,一般按照工藝的形式可分為:數控車床、數控銑床、數控鏜床、數控磨床、數控鉆床、數控線切割機床等。在這我們就不一一贅述了。本文只針對數控銑床中的螺旋銑削進行深入度探討和研究。
1、數控銑削加工及螺旋銑削
數控銑床是一種可以進行產品外形加工的一種加工形式,他可以加工多種復雜樣式的產品,能夠完成別的數控機床不能完成的大部分工作。它通過電腦計算機編程與機床自身的操作系統一道,來完成的很多復雜的操作。
在加工過程中,首先要將準備加工零件的毛坯件進行在工作臺上的固定,然后選擇合適的銑刀,安裝就位后,通過程序預先設計好的編程程序,對零件進行加工。數控銑床一般加工產品上的曲線輪廓、直線、圓弧。孔、螺紋以及螺旋曲線,尤其是一些人工所不能加工的需要設備輔助加工的數學表達式給出的非圓曲線、列表曲線、空間曲面等。這些工件看似形狀簡單,實則尺寸繁瑣,難以測量和觀察,有些孔和平面要求的加工尺寸和精度而且還要求很高,這
些數控銑床都能很好的完成。
在數控銑削過程中,就不得不說螺旋銑削,它是數控銑削加工過程中一項重要的加工方式,螺旋銑削的加工軌跡就像彈簧,在加工過程中刀具按照編程設計的運動軌跡進行螺旋的進給,對加工工件進行逐步的切削,已達到預期的尺寸。對于螺旋銑削,刀具的選擇很重要,一般來說根據工件的加工銑削尺寸及螺旋半徑選擇大于刀具直徑的40%到 60%,當然也要看刀具的中心有多大的位置沒有切削刃,這對于刀具的切割壽命有很大影響,Z 軸也就是進刀尺寸的給定取正常切削的 20%左右,這也要看材料和實際加工確定,一般來說螺旋銑削加工在下刀的時候和走孔的時候用的情況比較多,不過加工鋼件的時候能不用就不用了,因為對刀磨損太快,嚴重影響刀具的壽命。
在數控銑削加工過程中,通過螺旋銑削的應用,從而提高了設備加工使用的優化,能夠跟好的滿足加工生產的要求,而且在刀具的使用上,發揮出跟大的價值。分析研究螺旋銑削的加工工藝技術,合理的運用螺旋洗對輪廓、孔、螺紋等進行參數調整,研究出一套適合的加工工藝。為數控技術發展,做更深層次的研究。
2、數控銑中螺旋銑削的的應用
2.1 螺旋銑削對工件外形輪廓銑削的作用
在數控銑床中,輪廓銑削一直是一項主要的銑削目的,在以往傳統的平面加工過程中,機械加工的工作效率不是很高,而銑削加工大大改善了這個問題,但在銑削過程中,有一個重要的問題,那就是刀具在加工中,一般來說是旋轉的刀具相對于靜止的工件進行加工,當銑刀在切削過程中,如果刀具在高速旋轉狀態下,直接垂直切削工件時,在進刀的過程中,會對工件帶來一個直接的沖擊力,這樣的切削方式,會對工件產生一定的損傷,而且直進的加工方式對于刀具和機床的損傷也是不可忽視,長此以往,刀具的使用壽命會急劇降低,對機床的加工精度也會產生影響。為了減少這樣的情況的發生,螺旋銑削的出現也就得到了數控銑床的的大量應用。螺旋銑削的應用大大改善
了銑刀在銑削過程中所造成的干涉問題。優化了切削路徑,切削的過程刀具進刀形式是一種沿著工件輪廓螺旋進給的一種方式進刀,螺旋進刀時刀具以螺旋線的方式運動,以此來避開刀具中心無切削力的的問題,它靠銑刀的側刃逐漸向下切削從而實現向下進刀,這樣的進刀路徑,大大減少了刀具和工件的直接沖擊,也讓加工的效率和加工的精度得到了提高。
螺旋進刀的關鍵是選擇刀具的直徑,切削最大螺旋半徑、最小螺旋半徑、螺旋進到角度。刀具的種類很多,外形尺寸也很多,根據具體的加工零件、加工材料、加工尺寸、加工外形選擇合適的加工刀具,一般有面銑刀、立銑刀、模具銑刀等。最大螺旋半徑和最小螺旋半徑是一個相對的概念,根據銑削工件形狀尺寸,確定最大螺旋半徑是為了更快更效率的切削工件,螺旋半徑過大會影響切削時工件邊角的切削精度,可能會出現過切或者少切的情況。最小螺旋半徑是為了防止進刀時頂刀的,最小螺旋半徑不能小于刀具中心無切削力部分的半徑,防止切削受力過大。進刀角度的確定也是一個很重要的因素,進刀角度過大會產生過大的端刃切削力,角度過小側螺旋圈數又偏多,切削量偏少,切削時間過長,影響效率。所以切削角度的確定還需要根據實際情況,在不影響刀具使用壽命的情況下,經量增大切削角度,一般選擇 5-15 度之間。
2.2 螺旋銑削對工件螺紋加工的應用
說到螺紋加工,因為螺紋標準化的確定,所以在傳統的螺紋加工中大多數情況下都是用標準的刀具對工件進行相對的旋轉切削運動。以此來完成螺紋的加工生產,此種形式生產的螺紋形狀基本能夠達到使用要求,但是如果螺紋精度要求提高以后,這種傳統的螺紋生產加工方法對操作工的技術要求,以及對設備精度的要求都要有明顯的提高,這對于生產效益的影響還是提出了很高的要求。而且在螺紋加工中如果出現一些非標準的螺紋形式,這對傳統的車床就是一項很大的挑戰。而對于應用了數控銑床的螺旋銑削來說,這些問題都可以迎刃而解,螺紋銑削加工現對于傳統的螺紋加工,其加工的工件精度更改更高,加工的廢品率更低,而且加工效率也比傳統加工有著明顯優勢。
如圖 1 所示在螺紋結構形狀以及螺紋旋向方面也不受傳統的限制,有時可以利用一把螺紋銑削刀具完成多種形式的螺紋加工。在傳統的螺紋加工中,螺紋加工件必須有過渡段或者退刀槽的形式才能加工情況,在數控銑床中都可以很容易的減少此類工藝步序,直接加工螺紋,這樣的好處是減少了應力集中。而且螺紋銑刀加工的螺紋工件耐用度也有很大的提高,是一般絲錐板牙加工的螺紋的數十倍之多。數控螺紋銑削加工的優勢過于明顯,所以現如今對于很多要求較高的工件螺紋式生產中銑削工藝得到極大的應用。
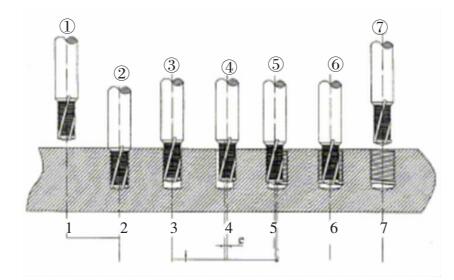
圖 1 螺紋加工
2.3 螺旋銑削對工件孔加工的應用
螺旋銑削在鉆孔來說,有著高效的加工能力,一般螺旋銑削鉆孔需要三軸同時運動,X 軸、Y 軸平面運動,Z 軸做垂直旋轉運動,刀具圍繞工件孔中心線做螺旋運動。這樣的好處是增大了銑削面積,切削更加快速,擴大了鉆孔尺寸,而且銑削出的孔表面光滑,加工精度高,減少了一般鉆孔后精鏜表面的工序,他的性能均超出麻花鉆、扁鉆、火焰切割、穿孔等技術。采用螺旋銑削,不論是在任何情況下,加工刀具與加工工件之前都只有很小的接觸面積,所以需要的切削力相對于其他鉆孔工藝也小得多,而且螺旋銑削增加了材料切屑的排出空間,減少了碎屑和刀具以及孔壁的摩擦。而且空的尺寸是由數控編程程序來確定加工的,所以孔的加工對于受刀具的選擇減少,從而降低了鉆頭的儲存要求。
鑒于數控銑刀的螺旋切削刃的幾何形狀的特點,銑刀可以切削出筆直的側壁和一個 90 度角度的底部,這相對傳統的鉆孔工具,是不能夠做到的。對于一些大型模具加工的廠家,在加工大型加工件時,機床之間的工件移動也是要消耗很多時間的,在一些大型工件造打孔后需要對孔進行精鏜,而這些工序可以在數控銑床上一次性完成。
不過在螺旋銑削孔加工中,冷卻方式也體現的至關重要,因為在銑削過程中,刀具在完成切削過程之前是沒有抬刀動作的,所以切削產生的鐵屑如果不能及時的叢孔中排出,就會對孔表面造成劃傷,而且切削和刀具的摩擦也會使刀具產生高溫,這會影響刀具的使用壽命,更有甚者會出現崩刀的可能。在孔加工過程中因為是冒孔狀態,故不能使用液冷,應該優先使用高壓氣體進行冷卻,這樣能夠讓鐵屑及時排除,而且也對刀具起到了冷卻的作用。以上闡述都體現出螺旋銑削孔加工在加工產品中的優勢,現如今,一些大型鍛造廠都采用了螺旋銑削來進行打孔加工,這極大提高了生產的工作效率,而且加工精度也得到了極大的提高。
3、螺旋銑削在數控銑加工中的優化發展
螺旋銑削的應用讓數控銑削變得越來越不可或缺,它能夠代替很多的傳統的加工工藝來更好地完成加工工件的生產。而為了讓螺旋銑削能夠更好地服務于實踐生活,我們還需要不斷地加強學習探索和改進。
3.1 選擇合適的切削方式
在很多銑削方式中,螺旋銑削能夠更好地完成加工生產,但是在社會不斷進步發展的過程中,會出現很多不同形狀各異的加工零件,這對于數控加工是一個挑戰,在日常加工中,我們要不斷摸索螺旋銑削中不同刀具選擇對不同材質的工件切削過程,還有各種不同工況下,如何合理選擇刀具,進給參數,程序的改進,已達到用最經濟的方式更好地完成工件的加工。
3.2 對數控加工螺旋銑削技術人員的要求
螺旋銑削加工在不斷應用和摸索過程中,對于數控機床的操作人員以及技術人員,都要學會善于總結,善于發現,善于嘗試。而且公司也要定期對員工進行同行業先進技術的專業的培訓,只有員工能夠充分掌握螺旋銑削的加工方法,讓數控機床能夠充分地得到利用,以促進公司乃至行業更好的發展。
4、結論
在目前的數控銑削過程中,螺旋銑削得到極大的發展,我們要充分利用好螺旋銑削這一加工方法。在未來的數控技術發展的道路中,我們要不斷探索,積極創新,努力提升自己的專業技術水平,為行業的發展和社會的進步做出貢獻。
投稿箱:
如果您有機床行業、企業相關新聞稿件發表,或進行資訊合作,歡迎聯系本網編輯部, 郵箱:skjcsc@vip.sina.com
如果您有機床行業、企業相關新聞稿件發表,或進行資訊合作,歡迎聯系本網編輯部, 郵箱:skjcsc@vip.sina.com