基于 PLC 的雙面鉆床控制系統設計
2019-1-31 來源:襄陽汽車職業技術學院 湖北文理學院 作者:李夢飛 秦 濤
摘 要:針對單面鉆床效率低下,工序復雜的問題,以雙面鉆組合機床為研究對象,采用三菱 FX1S- 20MR PLC 為主控制器,設計了一種 PLC 控制的雙面鉆床控制系統,包括系統的工作流程,I/ O 分配和軟件程序設計。軟件調試結果表明:基于 PLC 的雙面鉆床控制系統設計可靠,能夠有效地提高鉆孔效率。
關鍵詞:雙面鉆床;PLC;;SFC 圖;梯形圖
0 引言
組合機床是一種可實現多工序、多軸、多面的高效加工、自動化程度很高的加工設備。而在部分中小型企業生產加工過程中,由于資金缺乏、技術欠缺等原因,依舊采用故障頻繁出現、控制系統可靠性差、維修時間長的老式機床。為了能夠有效地提高組合機床鉆孔加工效率,減少電氣部分維修次數,滿足加工生產需求,實現雙面鉆組合機床的自動控制,本文設計了一種基于 PLC 控制的雙面鉆床控制系統。
1 、系統總體方案
雙面鉆床主要用于在工件相對的兩面鉆孔,機床由動力滑臺提供進給運動,刀具電動機固定在動力滑臺上。機床的控制過程是典型的順序控制,其控制系統模型如圖 1 所示,工作流程為:工件裝入后,按下啟動按鈕 X0,工件夾緊,兩側滑臺同時進入快速進給工步;工件兩面加工完成后,兩側動力滑臺退回原位,工件松開,觸發限位開關 X10,系統返回初始步,一次加工的工作循環結束。
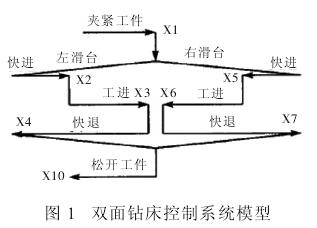
傳統的雙面鉆床采用繼電器-接觸器控制方式,需要的繼電器多且接線復雜,可靠性低且容易產生誤動作,故障率高。本文提出 PLC 控制方式實現鉆孔加工的周期性循環動作,滑臺的位置信息通過觸發行程開關獲得。為保證每個工序的同步性,采用并行序列程序,在各子序列的末尾增設了一個等待步,如果兩個子序列分別進入了等待步,表示兩側滑臺的快速退回均已結束,應轉換到下一狀態。
2 、軟件控制系統設計
2.1 I/O 點估算
通過對雙面鉆床總體控制方案分析可知,系統共有 9 個輸入點:啟動按鈕、夾緊開關、左側快進開關、左側工進開關、左側啟動開關、右側快進開關、右側工進開關、右側啟動開關以及松開開關;共有 8 個輸出點:夾緊閥觸發器、左側快進觸發器、左側工進觸發器、左側快退觸發器、右側快進觸發器、右側工進觸發器、右側快退觸發器以及松開閥觸發器。根據控制系統需要具備的功能分析和 I/O 點數目估算,本文選用三菱 PLC FX1S-20MR 型號,具有 16 個輸入點和 14 個輸出點,且外部接線留有 10% ~ 20%的余量,便于擴展,能滿足雙面鉆床的控制要求。
2.2 I/O 分配
根據雙面鉆床控制系統的功能及技術要求,可確定 PLC 控制系統的 I/O 分配表如表 1 所示,相應的外部接線圖如圖 2 所示。
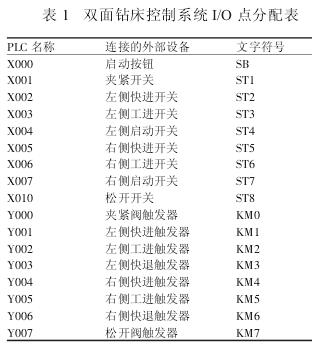
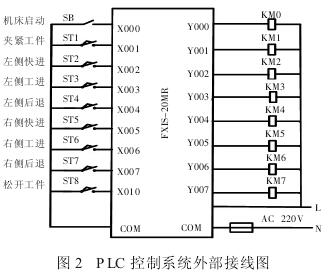
2.3 S FC 圖和梯形圖設計
基于三菱 GX developer 軟件進行雙面鉆床控制程序設計,其控制系統的 SFC 圖如圖 3(a)所示。具體的實施步驟:工件裝入機床后,按下啟動按鈕 x0,按下夾緊開關 X1,工件夾緊,M2 和 M6 變為活動步,兩側同時進入快速進給工步。待兩面加工均完成后,兩側動力滑臺退回原位,系統進入步 M10;工件松開,觸發限位開關 X10,系統返回初始步 M0,一次加工的工作循環結束。
為保證并行序列各子序列同時結束,在各子序列的末尾增設了一個等待步(即步 M5和 M9),如果兩個子序列分別進入了步 M5和 M9,表示兩側滑臺的快速退回均已結束,應轉換到步 M10.步 M5 和 M9 之后的轉換條件為“=1”,表示應無條件轉換,在梯形圖中,該轉換等效為一根短接線,或理解為不需要轉換條件。雙面鉆床控制程序梯形圖如圖 3(b)所示,通過對每步的輔助繼電器 M 置位,完成特定的功能指令。
按下啟動按鈕,系統發出初始化脈沖,置位 M0 后緊接著置位 M1,隨后完成功能指令 Y0,即實現工件的夾緊。組合機床動力滑臺夾緊運動觸發限位開關X1,分別置位輔助繼電器 M2、M6,同時復位 M1,實現機床動力滑臺的左側和右側工進。具體功能的實施過程與用狀態轉移圖編程所實現的功能一致。
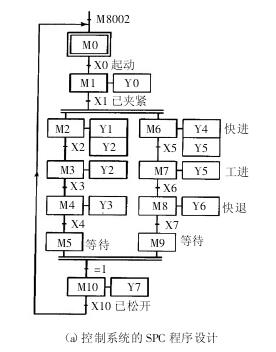
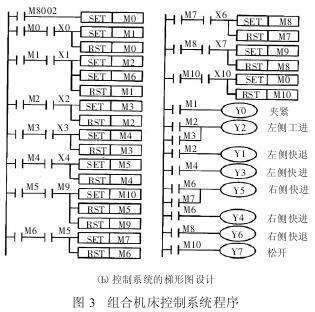
3 、結論
針對工廠現階段所使用的老式機床的配備情況以及在使用過程中可能出現的問題,本文設計了一種適用于雙面鉆孔組合機床的 PLC 控制系統。PLC控制程序修改方便,易于擴充且可靠性極高。在實現大批量生產,保證加工效率的同時節約了機床設備成本。軟件調試結果表明:本文設計的控制系統符合設計要求,可以用于雙面鉆床加工控制現場。
投稿箱:
如果您有機床行業、企業相關新聞稿件發表,或進行資訊合作,歡迎聯系本網編輯部, 郵箱:skjcsc@vip.sina.com
如果您有機床行業、企業相關新聞稿件發表,或進行資訊合作,歡迎聯系本網編輯部, 郵箱:skjcsc@vip.sina.com