掛車車軸加工的全新工藝及機床的研究
2021-5-18 來源: 寧夏長興精密機械有限責任公司 作者:施文秀
摘要:汽車掛車軸專門化數控車床用于掛車軸的車削加工,掛車軸軸身部分為方形或圓形,車軸全長1.8~2.8 m。車軸需根據毛坯尺寸不同加工成長度不同的成品車軸。本文提出的掛車車軸加工全新藝為:在一臺機床上,一次上下料即可自動完成車軸兩端的全部車削加工。
關鍵詞:掛車車軸;加工工藝;基準轉換;多連桿測量
汽車掛車軸是汽車車輛的重要零部件,主要用于半掛載貨車的長途運輸。隨著公路網絡的建設及物流運輸的快速發展,該零部件市場有很大的需求。目前全國生產該產品的主要廠家有近百家,年產銷量180余萬件。大部分廠家制造該產品的工藝及設備都比較落后,車軸兩端的加工均采用分散工藝,一個車軸的軸端加工約需5~8序完成,存在生產效率低、制造精度低、人工成本高、生產流程長及難以實現自動化等問題。
通過對現行掛車軸加工工藝的分析研究,充分了解用戶不同車軸制造工藝、不同技術要求,本文提出的加工工藝采用高度集成的加工工藝,可實現一次裝夾,完成車軸兩端內孔、外圓以及端面的所有車削加工工序內容。為達到本加工工藝要求,機床通過總體方案設計、裝夾基準自動轉換、自動輸送料裝置、自動化控制技術等關鍵技術的研究,以及自動檢測裝置、高精度尾架、主軸托料裝置、送料裝置等關鍵部件的研發,最終設計形成了本文論述的掛車軸加工用的雙端面專門化數控車床。現就掛車軸的加工工藝和本文論述的雙端面專門化數控車床的大體結構進行介紹。
1、 車軸生產工藝分析及新型生產工藝推薦
為詳細了解車軸加工工藝,先介紹掛車車軸的結構及要求,汽車掛車軸有很多種,按形狀不同,分為實心方型車軸,空心方管車軸、空心圓管車軸,其中空心方管車軸按形狀和尺寸不同又分為美式車軸和德式車軸。其大體結構見圖1:掛車車軸結構示意圖。掛車軸要求除外圓內孔的通用車削加工要求外,要求后軸承位、油封位、過渡圓弧面以及底板位壁厚均勻且不得小于要求最小值,所以為保證壁厚均勻,在加工車軸前,應先對檢測軸肩進行軸向位置測量,以測量軸肩位置為加工工件的軸向基準,以最小加工余量完成車軸外圓、內孔和端面的加工。掛車車軸兩端車加工的形位公差、尺寸公差等精度要求均較高,本文不做過多贅述。
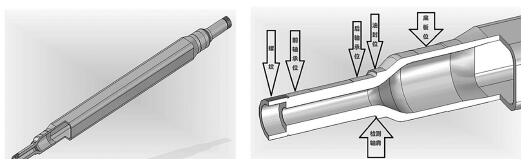
圖1 掛車車軸結構示意圖
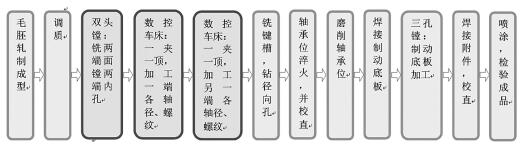
圖2
1.1 整體車軸傳統生產工藝
工序1:毛胚軋制成型。
工序2:毛胚調質。
工序3:雙頭鏜床/銑專機:加工兩端端面、內孔/中心孔。為保證加工零件壁厚均勻的要求,此序加工工藝基準為軸承位,軸向檢測油封位檢測軸肩。
工序4~5:采用單刀架通用數控車床:掉頭加工兩端軸徑各部位。此序加工工藝基準為前序加工的內孔及錐面,軸向檢測端面位置。少部分用戶用雙刀架數控車床:一端由主軸夾具內撐,另一端尾架頂緊,加工兩端軸徑各部位。采用此設備比單刀架數控車床效率高,但加工一些特定車軸,存在由于內孔較小,內撐夾具傳遞扭矩不夠,不能大扭矩車削等加工質量問題。
工序6:銑鍵槽、鉆徑向孔。
工序7:熱處理:軸徑淬火、校直;也有用戶軸徑不淬火。
工序8:磨兩端外圓軸承位,也有客戶軸徑不淬火,而選用毫克能的。
工序9:焊接制動底板等附件。
工序10:加工制動底板端面孔,或者外側端面(碟剎車軸)。
工序11:焊接叉架、校直。
工序12:噴涂、檢驗,然后轉車軸總成裝配。
按照此傳統工藝進行車削加工,從工序3~工序5,工序3序完成車加工工序,掛車軸零件外形不規則,長度1.8m~2.8m,單件重約150Kg,采用傳統工藝多次上下料,增加制造過程的輔助時間,生產效率低,人工上下料不易操作,工人勞動
強度大。并且存在發生特定車軸內孔小,撐內孔尾架頂緊工件時,夾緊力不足,發生加工效率低下或夾持不牢造成廢品等質量問題的可能性。
1.2 整體車軸全新生產工藝
為改善和解決上述傳統生產工藝所存在的問題,提出本文論述的全新生產工藝及車加工設備。
新工藝將傳統生產工藝中工序3~工序5結合在一臺機床上進行加工,其余傳統加工工藝不做大幅變動。因工序3加工工藝基準為后軸承位,工序4~工序5加工工藝基準為工序3加工的內孔及錐面。如將工序3~工序5結合在一臺機床上完
成,加工過程中,機床需具備工藝基準轉換的能力。為此結合中間驅動雙端面數控車床的結構,提出開發本文論述的掛車軸加工用雙端面專門化數控車床。
2 、 掛車軸加工用雙端面專門化數控車床方案及結構
通過對掛車車軸加工工藝的分析,以及上述全新工藝的解析,結合用戶全自動上下料要求和雙端面數控車床的結構特點,應用模塊化設計思路,完成了掛車軸加工用雙端面專門化數控車床的總體方案設計:機床采用45°斜床身布局,剛性好,排屑方便。機床采用雙通道控制系統,左右刀架安裝在上導軌,可同時或分別與主軸聯動,完成零件兩端的同時或順序加工。由一臺機床完成軸端的全部加工,主、副主軸箱夾具夾持軸端軸承位,雙端同時加工端面、內孔和錐面,然后夾持基準自動轉換,轉為由左右尾架頂持工件兩端錐面,主軸箱浮動夾具夾持軸體并傳遞扭矩,加工軸端外圓各部位。按照工藝要求,機床總體布局方案見圖3。
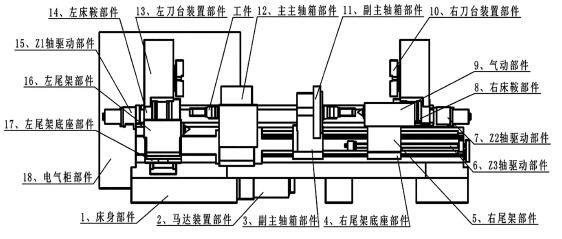
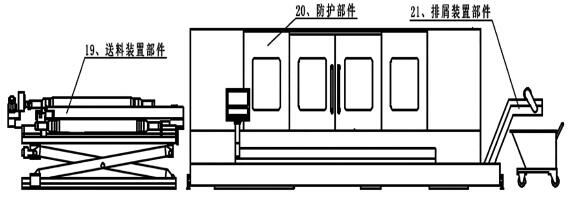
圖3 機床總體布局方案
附圖中所示序號代表的名稱:
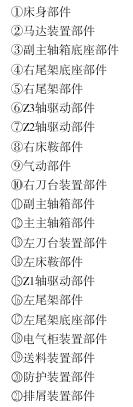
機床為了加工工件的高精度和高效率,配置了自動上下料裝置,上下料裝置通過懸伸臂將工件送入機床,至主主軸箱左端,為配合上下料,機床主軸箱內孔設有滾動托料裝置,輸送料道的懸臂上帶有動力裝置。上料時,工件向前移動,右端刀架對工件進行粗定位,當工件進入加工位置后,主軸箱夾持工件,懸臂收回;由左右兩套軸向檢測裝置,檢測并反饋工件測量軸肩的位置,對機床程序進行自動修正,從而實現零件的精確軸向定位,完成工件第一工步的加工。第一工步加工完成后,左尾架升起,主主軸箱卡爪松開,副主軸箱拖動工件至左尾架頂尖定位,副主軸箱卡爪松開并繼續向左移動,至右尾架頂緊范圍,右尾架與左尾架共同頂緊工件,實現工件定心,主主軸箱右端卡爪浮動夾持工件,帶動工件旋轉,完成工件第二工步的加工。第二工步加工完成后,主軸卡爪松開,兩尾架松開,左尾架下降,輸送料道的懸臂伸入機床,將工件拖出機床。機床完成單次加工循環。
3、新型工藝的優點和特點
(1)工序集中,減少了工件裝夾次數,減少了輔助加工時間,采用兩端同時加工工藝,生產效率顯著提高。
(2)一次上料,兩端同時加工,提高了車軸的加工精度和同軸度。
(3)縮短生產工藝流程,減少生產現場零件周轉,提高場地作業面積使用效率,有利于提高生產的組織管理。
(4)由于采用了高效加工設備,本機床在研發之初就已經考慮了配備上下料裝置及儲料裝置,這樣很容易就可以實現全自動化生產,以降低人工制造成本。
(5)工件在中間位置夾緊,裝夾可靠,傳遞機床切削時所需的扭矩足夠,尤其是對端面內孔較小的車軸,或者實體車軸而言,相比端面驅動方式,可以進行大余量車削,機床剛性強、加工精度高。
(6)機床可帶自動檢測裝置,尤其是對空心車軸,可以確保加工后的車軸壁厚均勻。
(7)如果車軸兩端的鍵槽和徑向孔需要加工,則本機床也可配置動力刀架,將后序的鍵槽和徑向孔一起加工完成。
4、攻克的掛車軸加工用雙端面專門化數控車床技術難題
(1)開發了滿足各種掛車軸全新加工工藝的需求,可實現轉換基準、軸肩測量、自動上下料等功能的中間驅動車床的機床布局方案。
(2)研制成功了高性能主軸箱。雙端面數控車床的核心關鍵技術在于中間驅動、夾持零件實現雙端車削的主軸箱,主軸箱的性能、水平決定了整機的性能、水平。其結構是將主軸系統、夾具、夾緊油缸、配油系統、驅動裝置一體化設計。滿足掛車車軸加工工藝要求。
(3)多連桿擺臂測量裝置,可實現車軸加工時毛坯的軸肩測量,由于測量點位于主軸箱孔內部,測量裝置需從卡爪中間較小空間內進入測量,檢測裝置采用多連桿機構從而完美解決這一難題。
(4)機床左端上下料輔機,輔機可將工件從機床左側將工件滾動送入主軸箱,等加工完成后,可將工件從機床內拖出,輔機可根據用戶需求,進一步擴展與自動線連接,實現自動線全自動生產。
(5)為配合上下料動作,主軸箱內孔設計了專門的滾動托料架,以降低車軸在上下料過程中的摩擦阻力。方便上下料。
(6)機床左側尾架設計了高精度上下移動的結構,滿足上下料動作的同時,實現了大切削力時尾架所需的較高剛性。
(7)機床設計有三套大行程徑向油缸卡盤,分別可實現自定心夾持工件和浮動夾持工件的功能,從最大限度上滿足掛車軸全新加工工藝的需求,其最大卡爪行程單邊可達65mm。
5、掛車車軸加工全新工藝實現的意義
汽車掛車軸在長途公路運輸中占據著重要的地位。提高其加工質量和加工效率其意義不言而喻;整體式車軸在車軸行業已經普遍應用,但是由于國內大部分掛車軸生產企業所用設備普遍落后,效率低,質量差。隨著公路交通運輸車輛市場需求的穩步增長及車軸制造行業面臨設備急需更新換代的現狀,采用高集成化、高復合化、高效率、高自動化、智能化是現代制造技術的發展方向,也是車軸制造行業眾多用戶的迫切需求。
新工藝的實施將為該行業提供效率高、精度高、自動化程度高、制造成本低的先進制造設備,對促進公路運輸的發展及國家經濟建設具有重要意義。
投稿箱:
如果您有機床行業、企業相關新聞稿件發表,或進行資訊合作,歡迎聯系本網編輯部, 郵箱:skjcsc@vip.sina.com
如果您有機床行業、企業相關新聞稿件發表,或進行資訊合作,歡迎聯系本網編輯部, 郵箱:skjcsc@vip.sina.com