汽車輪轂潔凈加工生產線設計
2023-5-22 來源:青島理工大學 作者: 李長河 陳民凱
摘要:針對汽車輪轂生產線自動化程度低、工作環境差和加工精度要求高的現狀,設計了一條汽車輪轂潔凈加工生產線。該生產線對輪轂的機加工工藝進行規劃,采用間隙配合的方式設計料架,并通過拆分裝置和運輸裝置對輪轂進行運輸 ; 夾具運用心軸定位的原理,通過連桿機構帶動定位件實現自定位,使用曲柄滑塊機構實現夾緊,增強輪轂在機床上加工的定位精度和夾緊可靠性 ; 采用微量潤滑的潤滑方式實現機械加工過程中的環保節能 ; 通過 RobotStodio 對具有雙夾緊工位的上下料機械手進行軌跡規劃。該生產線通過智能管理系統合理規劃和優化輪轂生產線,為實際生產提供依據和借鑒。
關鍵詞 : 汽車輪轂 ; 生產線 ; 自動化 ; 設計新能源汽車 ; 電驅動橋 ; 齒輪 ; 軸承 ; 設計
1. 序言
綠色發展是國際大趨勢。當前環境和資源問題成為人類的共同挑戰,針對如何實現可持續性發展已達成共識,綠色制造無疑是工業升級轉型的必經之路。發展綠色制造技術,有利于緩解當前環境資源約束問題,有利于新經濟增長點快速培育,而且對加速經濟發展方式轉變、推動工業轉型升級、新舊動能轉化及提升制造業國際競爭力具有深遠歷史意義。
我國汽車行業不斷地發展,國內汽車的銷量數次刷新全球記錄,一直位于世界第一的銷量水平。但在我國汽車行業迅速發展的同時,汽車輪轂傳統生產線在加工過程中大量使用礦物油切削液,造成了資源浪費、環境污染和危害操作人員健康等問題。據調查,一家中小型汽車輪轂生產廠家每年消耗的潤滑液高達 65 萬 t,用于潤滑液采購、廢液處理等方面造價高達 300 余萬元,且存在工作環境出現臟、亂、差等問題。因此,在改造生產線實現自動化的同時,必須保證汽車輪轂的潔凈生產,使潔凈生產與自動化生產完美結合是未來生產的必由之路。
隨著國際社會對綠色制造的支持,綠色冷卻潤滑方式也得到了發展,干式加工在機械加工中的成功應用為綠色加工開啟了新的道路,但由于缺少切削液的直接潤滑,導致想要達到與澆注式潤滑相同的加工質量就必須保證刀具的韌性、硬度和耐磨性,這使得干式加工受到刀具限制,且加工過程中由于沒有介質參與,排屑和換熱性能不足,不可避免地造成工件表面出現燒傷情況。
隨著學者們的深入研究,提出了低溫冷卻技術。低溫冷卻技術是將低溫氣體介質噴射到切削區對切削區進行降溫,起到冷卻作用,達到加工要求。學者們進行大量試驗探究低溫冷卻技術在車削、銑削等多種加工形式中的冷卻效果。試驗表明,低溫冷卻潤滑得到的工件質量、刀具壽命和潤滑性能均優于干式切削,但與澆注式潤滑相比,成本相差無幾,且可能導致加工過程中氧氣含量降低引起工人窒息,與綠色發展、保證人體健康沖突,需進一步發展研究。繼干式切削之后,提出了介于澆注式切削與干式切削的微量潤滑技術,最小限度地使用切削液,保證加工質量。微量潤滑技術是在高壓氣體中加入微量潤滑油,借助高壓氣流,將微量潤滑油霧化后注入高速切削區,進行冷卻潤滑和切屑排出。微量潤滑油采用具有極好的生物降解性能的植物油作為基礎油,極大地改善了工作環境,降低了對環境的污染,保證了工件加工質量。將靜電場等多能場耦合到加工過程中會起到更好的潤滑效果。因此,將微量潤滑結合到生產線之中已成為必然選擇。
由于傳統生產線存在自動化不足的問題,而自動化不足也限制了潤滑工況的改善,無法達到微量潤滑與生產要素同步的要求,因此需對生產線整體進行改進。隨著汽車銷量的增長,對輪轂的生產效率提出了進一步要求,增強生產線智能化也是行業發展的必然選擇。而汽車輪轂作為汽車的重要零部件,其精度、圓度和同軸度對汽車使用壽命、行車穩定性和駕駛員的安全有著重大影響。因此,生產線智能化的改造不僅需要提高生產效率,而且需要保證輪轂生產的質量。但我國輪轂生產廠家規模不一,輪轂機加工大部分依舊采用人工配合機床加工完成生產,大量使用人力,造成生產效率低、成本高、產品性能不穩定,極大制約了輪轂行業的發展。部分生產廠家試進行智能自動化生產線改造,但國內企業缺乏自己的核心技術,智能生產線成本較高,使得生產廠家無力更新設備。
面對輪轂生產的需要,我國開始著手組建汽車輪轂的自動化加工生產線。汽車輪轂加工的柔性自動化生產線需實現多規格、多尺寸和變批量的輪轂生產,滿足輪轂上下料、粗加工、半精加工、精加工及鉆孔等方面的加工自動化流水作業。由于輪轂加工的多樣性,眾多學者對輪轂加工過程進行了研究。傳統的輪轂加工需更換不同工裝設備來完成不同類型輪轂的加工,降低了生產效率,增加了成本,面對輪轂多規格、多尺寸的生產模式,對輪轂夾具進行改進是自動化柔性生產加工的大勢所趨,劉德偉對輪轂柔性夾具進行了設計與分析,通過旋轉機構帶動連桿實現不同半徑輪轂的夾緊,并對夾具進行夾緊力和定位誤差分析。梁盈富等對汽車輪轂生產線中智能制造系統總體框架進行了設計,將 MES 系統和 PLC 技術與機床機器人相結合。輪轂自動化柔性生產線從柔性加工的夾具,到加工過程中的檢測,再到整條生產線與物聯網結合,其智能化已經得到長足的發展。
綜上所述,生產線設計應解決以下問題 : ①輪轂的種類繁多,規格尺寸不同,往往需要不同的加工設備來完成生產。②加工單元采用島式布局,各單元之間加工連續性不足。③澆注式潤滑工況在加工過程中飛濺的潤滑液會污染環境,影響工人健康。④上下料采用人工,使得成本增加、效率下降。汽車市場對輪轂的需求量巨大,以上問題亟待解決。因此設計了汽車輪轂潔凈加工生產線,實現輪轂的上下料、機加工的自動化作業,并加裝微量潤滑裝置來解決污染問題。
2. 生產線整體方案設計
2.1 工藝優化設計
汽車輪轂加工的柔性自動化生產線需實現多規格、多尺寸和變批量的輪轂生產,滿足輪轂的上下料、粗加工、半精加工、精加工及鉆孔等方面加工的自動化流水作業。將輪轂機加工分為 5道工序,其規程設計見表 1,汽車輪轂加工需進行粗車、半精車和精車加工,將車削分為4道工序,鉆孔在加工中心上進行,作為一道工序。
表 1 輪轂加工工藝規程設計
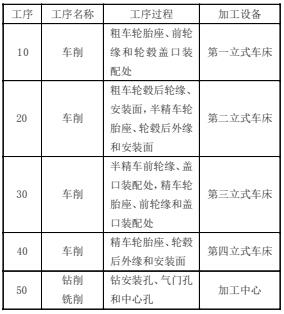
2.2 生產線整體布局
從工藝流程出發,對上下料裝置、機床夾具和生產工況進行整體設計,設計出的輪轂潔凈生產線如圖 1 所示。由 4 臺立式車床和 1 臺加工中心完成輪轂 5 道工序的加工,5 臺機床成兩排布局,通過 3 臺上下料機械手完成機床與輥道、輥道與輥道之間的物料傳輸。5 臺機床和 3 臺機械手組成一個加工單元,車間可布置多個加工單元,通過上料裝置進行統一上料。國內現有輪轂加工生產線多為人工搬運上料,既降低了生產效率,
又增加了生產成本,因此采用設計出的自動化上料裝置,實現生產線的自動上料。
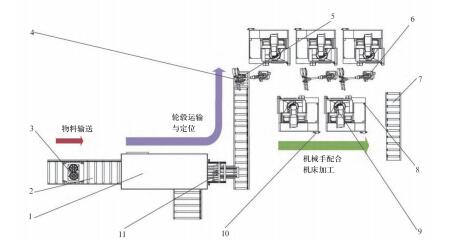
圖 1 汽車輪轂潔凈生產線
1—拆分裝置 2—第一輥道 3—料架 4—輪轂定位裝置 5—輪轂 6—上下料機器人 7—出料輥道 8—機床 9—夾具 10—微量潤滑裝置 11—輪轂搬運機械手
3. 產線主要部分設計
3.1 夾具柔性設計
隨著汽車行業的發展,輪轂呈現出多樣化的特征,而現有夾具柔性化程度不足,加工不同規格的輪轂需更換夾具,嚴重制約了輪轂的自動化生產。為解決該問題,學者對現有輪轂夾具進行了柔性設計與分析,但與生產線的聯系不夠密切。
為適應自動化生產線的需求,設計了一款自動化輪轂夾具,其結構如圖 2 所示。為解決重復定位精度問題,設置有自定位裝置提高定位精度 ; 為滿足輪轂多尺寸柔性加工,夾緊爪收緊方式通過曲柄滑塊機構實現,活動平臺可進行軸向調節。
自定位裝置包括 3 個定位塊、連桿、連接架和上下兩部分組成的軌道架。夾緊部分包括固定平臺、活動平臺和由連桿機構連接的夾緊爪。
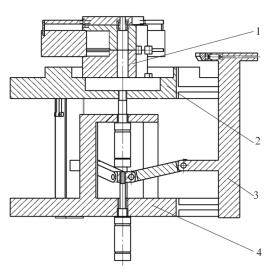
圖 2 夾具結構
1—自定位裝置 2—活動平臺 3—夾緊爪 4—固定平臺
自定位裝置實現夾緊前的定位,為夾緊提高更好的定位精度,有利于減小重復定位誤差。以輪轂底平面為主要定位基準面,活動平臺限制輪轂 X、Y 軸轉動和 Z 軸移動,在氣缸的驅動下,通過連桿機構帶動 3 個定位塊同時向外運動,限制輪轂的 X、Y 軸轉動,實現對輪轂的自定位 ;固定平臺與機床相連接,夾緊爪的移動由第一氣缸控制,第一氣缸通過曲柄滑塊機構將垂直的驅動力轉換成水平的徑向力,夾緊爪在徑向力的作用下沿固定平臺徑向移動,對輪轂進行徑向夾緊 ;第二氣缸帶動活動平臺在 Z 軸移動,配合夾緊爪對輪轂進行軸向夾緊。
在加工時,夾緊力既要保證不破壞工件,又要保證加工的正常進行。最小夾緊力為保證加工過程中汽車輪轂不因切削力發生位移偏轉的夾緊力。氣缸需對夾緊爪提供一個最小夾緊力保證加工的正常運行。加工時,夾緊爪與輪轂發生位置偏移,對輪轂產生的摩擦力,摩擦力與力偶相對,從而達到靜力平衡,靜力平衡條件為

式中,M為主切削力作用在輪轂上產生的力偶(N ·m);f2 為摩擦力(kN);d 為摩擦力作用點到輪轂內孔中心的距離(mm)。
夾緊時的摩擦力是由單個夾緊力產生,刀具與輪轂接觸產生的主切削力作用在輪轂上,形成力偶
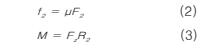
式中,μ 為定位爪下表面與輪轂凸緣表面間的摩擦系數 ;F2 為單個拉臂給的夾緊力(kN);Fz 為主切削力(kN);R2 為輪轂半徑(mm)。
設定機床加工鋁合金輪轂時的參數 : 轉速2500r/min,切削深度 4mm,工件直徑 580mm,進給量 0.5mm/r,切削長度為 400mm。計算切削速度
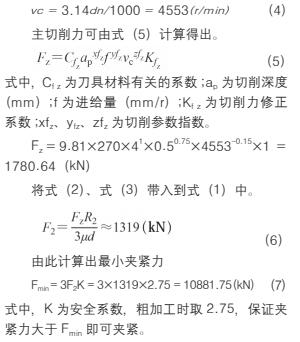
3.2 微量潤滑裝置
在《中國制造 2025》中提出了推動制造業朝智能、綠色、高端等創新驅動方向發展。綠色加工是國際大趨勢,在這種國際大趨勢的推動下,輪轂生產線從澆注式轉變為微量潤滑式的加工工況成為必然。傳統的澆注式潤滑使用大量的礦物油切削液,污染環境、危害工人的健康且切削液的使用和處理費用昂貴,而微量潤滑使用的切削液為植物油基切削液,具有良好的降解能力。微量潤滑從澆注式的 60L/h 降至 30~00mL/h,不僅減少了浪費,而且加工效果有所上升。
對生產線進行微量潤滑裝置的改造成為必然選擇,微量潤滑裝置結構如圖 3 所示,其懸掛式安裝在機床上,為輪轂加工提供微量潤滑工況。用微量潤滑裝置代替原有的澆注式潤滑裝置,并根據機床加工的主軸轉速對微量潤滑裝置的注油量進行調整,這樣既增強了潤滑效果,又降低了成本和污染。
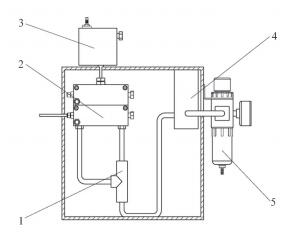
圖 3 微量潤滑裝置結構
1—油氣混合裝置 2—油泵 3—油箱 4—氣泵 5—氣體過濾器
3.3 上下料機器人軌跡規劃與效率
上下料機器人負責各個加工機床之間及機床與輥道之間的物料傳輸,對生產線的加工效率有很大的影響。機器人結構如圖 4 所示,包括現有機械臂和機械手,機械手具有兩個抓取輪轂的位置,通過機械臂轉動配合完成具有連續性的上下料,從而節約時間,提高加工效率。
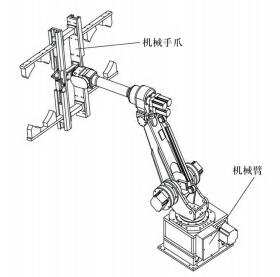
圖 4 上下料機器人結構
輪轂機械手搬運軌跡復雜,為避免機床與上下料機械手發生碰撞,對機械手進行軌跡規劃尤為重要。以第一立式機床和第二立式機床之間的物料搬運為例,上下料機器人需示教的點為 9個——1 個 pHome 點、1 個過渡點、3 個避障點、1 個定位裝置抓取點、1 個機床抓取點和 2 個機床放置點。機械臂通過偏移指令完成 3 個避障點之間的搬運,具體如圖 5 所示。上下料流程在階段 1~ 階段 6 之間循環,其中 pHome 點、過渡點和避障點之間采用關節插補運動,以空載最大運行速度 v 空載 max 和滿載最大運行速度 v 滿載 max 運行 ; 避障點和抓取點、放置點之間采用直線插補運動,以空載最小運行速度 v 空載 min 和滿載最小運行速度 v 滿載 min 運行。
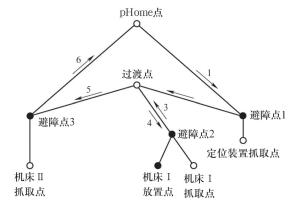
圖 5 機器人手部 TCP 軌跡規劃
通過 Robotstodio 進行仿真,行動軌跡表明上下料機器人可以達到預期運行效果,以機器人代替人工搬運,提高了工作效率。通過 TCP 軌跡跟蹤,可判斷是否產生碰撞和干涉,節省實際調試時間避免意外。軟件運行后,輪轂在輥道和各個機床之間平均搬運時間為 27s,而在傳統車間中,輪轂和機床間的上下料通過人工完成,平均搬運時間約為 33s,上下料效率提高了

4. 結束語
根據我國對輪轂生產的重大需求,針對自動化輪轂生產線組建的迫切要求,設計了汽車輪轂潔凈加工生產線。通過對輪轂生產的加工工藝進行規劃,對輪轂生產線進行整體設計,將各個生產單元通過上料裝置實現并聯 ; 對輪轂夾具進行設計,實現對輪轂的自定位和柔性夾緊,并提高了重復定位精度,為輪轂加工提供保障 ; 對加工機床進行改進,安裝微量潤滑裝置,可根據機床不同的轉速,對機床進行不同的供液,既可保證加工的精度與質量,又能減少資源浪費。設計方案通過虛擬仿真,對系統運行軌跡做出規劃,模擬輪轂自動化生產過程,提高工作效率,為實際生產提供理論依據,實現輪轂潔凈自動化加工。
投稿箱:
如果您有機床行業、企業相關新聞稿件發表,或進行資訊合作,歡迎聯系本網編輯部, 郵箱:skjcsc@vip.sina.com
如果您有機床行業、企業相關新聞稿件發表,或進行資訊合作,歡迎聯系本網編輯部, 郵箱:skjcsc@vip.sina.com