全鋁風冷發動機缸套一缸體的制備技術及其傳熱性能研究
2018-2-5 來源:重慶工程職業技術學院機械工程學院 、教務 作者:林雪冬 何彼
摘要:采用離心鑄造工藝制備了自生初SifM92Si顆粒增強A1.Si.Mg復合材料汽缸套,并與鋁合金缸體進行壓鑄成形,形成了全鋁合金缸套.缸體。應用熱電偶埋設法,在自制的五點測溫傳熱實驗裝置上分別檢測并對比分析了風冷發動機鋁合金缸套.鋁合金缸體與鑄鐵缸套.鋁合金缸體的傳熱性能。研究表明:相比鑄鐵缸套一缸體,鋁合金缸套-缸體具有更佳的傳熱性能;通過實驗測溫.數據曲線擬合法,推算獲得了全鋁合金發動機工作時汽缸的內表面溫度為231℃,比鑄鐵缸套內表面溫度低11℃。
關鍵詞:AI.Si—Mgg套;鋁合金缸套一缸體;傳熱性能;熱電偶
為了達到減重降排增效的目的,近年來,汽車行業已逐步采用輕合金(如鋁合金)材料來制備汽車零部件,如發動機缸體、活塞均已采用鋁合金材料【l-2]。將鑄鐵缸套鑲鑄在鋁合金缸體中使用是目前我國絕大部分摩托車發動機、通用機械發動機和小排量汽車發動機等采用的方式。利用該種方式制備的氣缸,其缸套的內表面耐磨性能優越;然而,由于鑄鐵缸套與鋁合金缸體材質上的不同,使得這種氣缸存在諸多問題,如熱傳導性能一般,鑄鐵缸套與鋁合金缸體壓鑄成形冶金結合效果欠佳等,使氣缸在使用過程中易出現變形、漏氣。鑒于此,國內外紛紛開展鋁合金缸套的制備技術研究[3-”],成形全鋁發動機缸套一缸體,以解決此類I司題。
作者在前期的研究工作中采用離心鑄造工藝制備了自生初晶Si/M92Si顆粒增強Al—Si—Mg合金鑄件,獲得了硬質顆粒增強鑄件內壁的鋁合金缸套,具有較好的摩擦學性能和綜合力學性能【協閽,為實現成形全鋁發動機缸套.缸體奠定了較好的基礎。本研究就全鋁發動機缸套.缸體的制備技術進行了詳細報道,并在這一研究基礎上,應用熱電偶埋設法,在自制的五點測溫傳熱實驗裝置上,分別對風冷鋁合金缸套一鋁合金缸體與鑄鐵缸套一鋁合金缸體的傳熱性能進行檢測并對比分析。通過實驗測溫.數據曲線擬合法推算全鋁合金發動機工作時汽缸的內表面溫度,驗證鋁合金缸套缸體在傳熱方面的優越性,為實現全鋁發動機缸套缸體的推廣應用提供實驗數據。
1 、實驗方法
1.1 缸套尺寸與模具設計尺寸
如圖1a所示,149cc發動機缸套內徑為62 mm,外徑75 IIllll,高度110.5 mm;在考慮了毛坯車削加工余量后,設計本實驗離心模具內徑為76 mm,高度130 mnl,如圖1b所示。
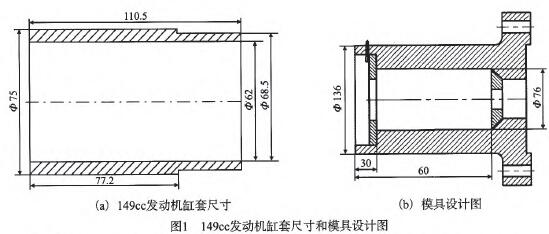
1.2 材料準備與鑄件制備
實驗以工業純Al、純si、純Mg及A1—18Si一1.2Mg合金為原料,在井式電阻爐中加熱熔煉配制A1.22Si一7Mg合金漿料,采用P—Cu變質劑進行變質處理。澆注工藝為:澆注溫度720~760℃,模具溫度150~200℃,離心轉速R=4 200 r/min。離心鑄造獲得高度129 mm,外圓直徑76 mill,厚度10~1 1 mm的筒狀零件,如圖2所示。
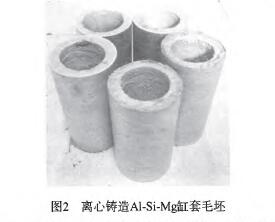
1.3 鋁合金缸套一缸體壓鑄
149CC發動機缸套將使用在風冷發動機上,一般采用高壓壓鑄,以形成薄而密集的散熱片。壓鑄采用3 000 kN高壓鑄造機,壓鑄鋁合金材料為ZLl 13Y。高壓壓鑄時,只需對缸套進行簡單預熱或不預熱。壓鑄時,使用壓鑄模具的芯棒對缸套進行定位。
1.4 缸套一鋁合金缸體組合體的傳熱性能測試一
圖2離心鑄造Al—Si—Mg缸套毛坯Fig.2 The AI-Si—Mg liner castings fabricated by centrifugal casting1.3鋁合金缸套一缸體壓鑄149CC發動機缸套將使用在風冷發動機上,一般采用高壓壓鑄,以形成薄而密集的散熱片。壓鑄采用3 000 kN高壓鑄造機,壓鑄鋁合金材料為ZLl 13Y。高壓壓鑄時,只需對缸套進行簡單預熱或不預熱。壓鑄時,使用壓鑄模具的芯棒對缸套進行定位。本實驗設計了一種傳熱實驗裝置,對比檢測了鋁缸套.鋁缸體組合體與鑄鐵缸套.鋁缸體組合體的傳熱性能,如圖3所示。整套裝置由熱源、上下圓形隔熱鐵塊、缸套.缸體、熱電偶一測溫儀組成。
其中,圖3a所示為熱源,由陶瓷棒與纏繞其上的電阻絲組成,電阻絲與外部交流電源接通,對缸套.缸體進行加熱,電阻絲功率為1.5 kW,陶瓷棒直徑略小于缸套內徑。上下圓形鐵塊用于隔絕熱量散失,同時也對整套實驗裝置起到固定支撐作用。沿缸體徑向方向,在其中部位置由外向內鉆有不同深度的測溫盲孔,直徑為1.6 Ilq/lq,用于埋設端頭經打磨后的鎧裝NiCr-NiSi熱電偶(K型,多1.6 mnl,精度:±1℃),測試缸體徑向方向上不同位置的溫度,如圖3b所示。實驗時,熱源被套在缸孔內部,熱電偶插在測溫孑L內并以高溫絕緣密封膠密封,熱電偶另一端聯接由重慶川儀十八廠生產的數字溫度顯示儀(型號:XMZ.H8—01一000A,精度:±1℃),讀取同一時刻缸體不同位置的溫度。
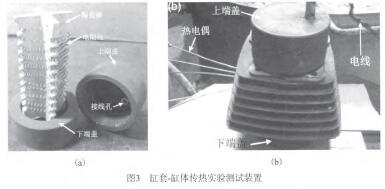
2、結果與討論
2.1 鋁合金缸套加工
本實驗中,鋁合金缸套鑄件中的微觀組織主要有灰色顆粒狀初晶Si相、黑色顆粒狀初晶M92Si相、共晶si、共晶MgESil)2及基體僅相。其中,在鑄件內層的初晶顆粒增強區域,初晶Si、M92Si顆粒的體積分數可達30%t舊。
對經過熱處理后的鑄件進行一系列機械加工,為鋁合金缸套.鋁合金缸體的壓鑄做準備。鑄件的機加工主要包括鑄件外表面粗車、內表面粗車/半精車、外表面螺旋槽車削、端部車削以及倒角等。根據前期研究成果【151,在經過了工藝優化后,鑄件的端部車削量控制在6 mm以內。本實驗中,首先應對鑄件的兩端進行車削,去除端部夾渣,保證剩余部分鑄件的質量。在后續的壓鑄過程中,為了使零件的外表面與缸體在高壓或低壓作用下實現良好的冶金結合,缸套應具有粗糙的外表面,因此,在對鑄件外表面進行車削時,應保持較大的進刀量,并適當降低機床的主軸轉速,盡可能使零件的外表面形成大量的毛刺。并且,為了進一步增強鋁合金缸套.缸體的冶金結合能力,本實驗在缸套零件的外表面車削有一系列的螺旋槽,如圖4所示,設計槽深1~2 mm,槽距3~5 mm。
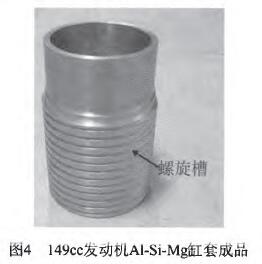
2.2 缸套一缸體壓鑄成形
缸套壓鑄時,需要定位在壓鑄模具的芯棒上,既要保證壓鑄過程中缸套內孔不“跑水”,又要保證鑄件壓鑄成形后能夠順利取出,因此,鑄件的內表面在加工時具有一定的精度要求。不同缸套產品的壓鑄內孔尺寸的精度要求不一樣。工廠中,鑄鐵缸套.缸體的壓鑄設備同樣適用于鋁合金缸套.缸體的壓鑄,只是在工藝方面有所變化。缸套在壓鑄前可進行簡單預熱處理以保證在壓鑄時缸體缸套之間的冶金結合度。由于鋁合金的熔點比鑄鐵低,其預熱溫度相對較低,一般以不超過300℃為宜。在預熱時,由于材質的不同,鋁合金缸套與鑄鐵缸套的膨脹量顯然不同。A1.Si.Mg合金的線膨脹系數為20.48x106/"C(20~300℃),而鑄鐵的線膨脹系數一般為(8.5~l 1.6)xlO-6/℃(20~300℃),二者相差較大,鋁缸套受熱更易膨脹。因此,在車削鋁合金缸套內孔時,其尺寸偏差范圍一般取公差下偏差,使得鋁合金缸套的內孑L尺寸在總體上相比于鑄鐵偏小。如圖5所示為鋁合金缸套壓鑄成形件,圖6所示為兩種缸套壓鑄成形件經機械加工后的成品,圖7是將鋁合金缸套一缸體成形件沿缸套軸向方向由中間位置剖開后打磨、拋光后的形貌圖。由圖7中可以看到,經壓鑄后,鋁合金缸套與鋁合金缸體間的結合效果良好,這為全鋁合金缸套一缸體呈現優越的傳熱性能奠定了基礎。
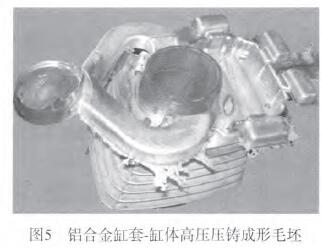
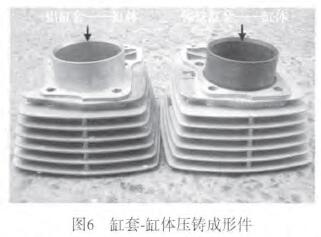
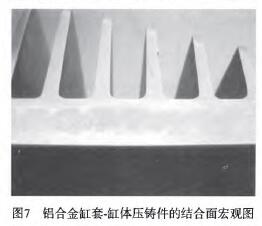
2.3 缸套一缸體組合體的傳熱性能
與鑄鐵缸套相比,鋁合金缸套尤其在傳熱性能方面具有明顯的優勢:鋁合金缸套材料的熱導率為A鋁=70w/(m·K),鑄鐵缸套的導熱系數為A鐵=55 W/(m·K),壓鑄鋁合金的熱導率為A=177 W/(m·K)t181,即:鋁缸套與壓鑄鋁合金缸體的熱導率基本相等,是鑄鐵缸套熱導率的3倍。較高的熱導率有利于缸體的整體散熱,特別是風冷系列發動機,將極大地改善熱機的工況。關于模擬鑄鐵缸套一缸體工況并測算缸體內壁溫度的研究已有不少,然而,對于鑲鑄有鋁合金缸套的全鋁發動機汽缸體在這方面的報道尚未見到。為了獲得風冷發動機鋁合金缸套的傳熱性能指標,在實驗室進行了風冷發動機的工況模擬實驗,并與鑄鐵缸套進行了對比。按1.4節所述方法,分別對鋁合金缸套.鋁合金缸體,鑄鐵缸套.鋁合金缸體組合體進行了發動機工況模擬、并分別測量缸體不同位置的溫度,從而對比兩種缸套的傳熱性能。實驗時,通過套在缸體缸孔內部的電阻絲加熱來模擬發動機工作產生的熱量,通過缸體正前方的電風扇轉動來模擬空氣對流對缸體的散熱作用。鑄鐵缸套一缸體發動機在正常工作一段時間后,其外表面溫度將達到相對平衡狀態。此時,缸體外表面上部(缸體大端面)溫度達180--一200℃,缸體外表面下部(缸體小端面)溫度達140 150℃(企業數據)。根據這一平衡溫度區間,本實驗制定了模擬發動機燃燒室工況的熱源加熱工藝,即1.5 kW電阻絲每加熱14 s,斷開電源5 S,依次反復進行,使埋設于鑄鐵缸套發動機缸體外表面的熱電偶A的溫度處于平衡溫度區間內,兩種缸套發動機均采用相同的加熱頻率進行測試。經測量,在缸套.缸體中部,組合體的最大壁厚約12 nllYl。依此,熱電偶偶頭埋設在距離缸體外表面不同的深度,如圖8所示,埋設點A、B、C、D、E分別距缸體外表面的距離為2.0 rain、3.5 mm、5.0 rtlln、6.5 mrfl、8.0 nllTl。測試時,在不同時刻,同時記下所有點的溫度讀數。
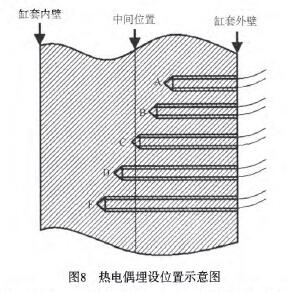
在同樣的加熱條件下分別測試兩種缸套一缸體上不同位置的溫度,記錄并繪制如圖9所示的溫度一時間曲線圖。可以看到,隨著加熱時間的延長,兩缸套一缸體不同位置的溫度均呈現逐漸上升的趨勢。并且,經過長達1 415 s的吸熱、傳熱的循環過程后,缸套.缸體的溫度處于一種相對平衡狀態。從圖9a可以看到,處于平衡狀態的鑄鐵缸套一缸體的E點(最深測溫位置)的最后溫度達223℃,而同樣位置的鋁合金缸套.缸體的最后溫度為206℃,如圖9b所示,其溫差達到17℃。而在距離缸體外表面最近的測試點A點,其溫差更是達到了20℃。顯然,在同等工況下,鋁合金缸套.缸體具有更低的溫度,其傳熱性能更佳。
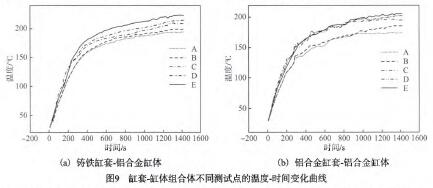
圖10所示是兩缸套.缸體溫度達到平衡態后,不同為:測試點的溫度值。可以看到,無論是鑄鐵缸套一缸體,還是鋁合金缸套二缸體,其不同位置的溫度值近似呈現線性變化規律。
分別對兩缸套一缸體溫度變化曲線進行擬合,則得鑄鐵缸套.缸體不同位置的溫度變化曲線方程為:Y=4.866 7戈+1 83.47 (1)鋁合金缸套一缸體不同位置的溫度變化曲線方程Y=5.4x+1 66 (2)根據這一擬合曲線方程,可以近似預測發動機在正常工作后,缸套.缸體溫度達平衡態后,缸套內壁的平均溫度。據式(1),則得鑄鐵缸套內表面的平衡溫
度為242℃;據式(2),則得鋁合金缸套內表面的平衡溫度為231℃。可見,鋁合金缸套的內表面溫度更低,這有益于減輕汽缸內部的燃燒積炭現象。并且,這也是首次在實驗的基礎上,預測獲得的全鋁合金發動機工作時汽缸的內表面溫度,對于進一步研究全鋁
發動機的工況具有參考價值。
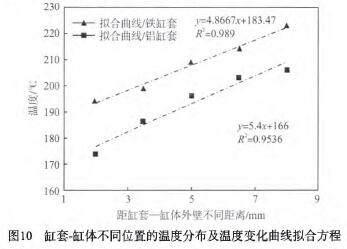
3、結論
(1)通過離心鑄造法成功制備了自生初晶Si/M92Si顆粒增強A1.Si.Mg復合材料汽缸套,并經高壓壓鑄機與鋁合金缸體進行了壓鑄成形,得到全鋁風冷發動機缸體。且鋁合金缸套與鋁合金缸體間的結合效果良好,為全鋁合金缸套.缸體呈現優越的傳熱性能奠定了基礎。
(2)應用熱電偶埋設法,在自制的五點測溫傳熱實驗裝置上分別檢測并對比分析了風冷鋁合金缸套一鋁合金缸體與鑄鐵缸套.鋁合金缸體的傳熱性能。研究表明:相比鑄鐵缸套.缸體,鋁合金缸套.缸體具有更佳的傳熱性能
(3)通過實驗測溫一數據曲線擬合法獲得了全鋁合金發動機工作時汽缸的內表面溫度為231℃,比鑄鐵缸套內表面溫度低11℃。對于進一步研究全鋁發動機的工況具有參考價值。
投稿箱:
如果您有機床行業、企業相關新聞稿件發表,或進行資訊合作,歡迎聯系本網編輯部, 郵箱:skjcsc@vip.sina.com
如果您有機床行業、企業相關新聞稿件發表,或進行資訊合作,歡迎聯系本網編輯部, 郵箱:skjcsc@vip.sina.com
更多相關信息