汽車熱沖壓模具的數字化鑄造技術
2019-2-15 來源: 大連理工大學材料學院 作者:李 鑫 姚 山
摘 要:針對汽車熱沖壓模具這類具有復雜內腔結構的鑄件提出一種數字化鑄造技術路線。 利用鑄造模擬技術進行鑄造方案設計;利用 3D 打印技術完成砂型(芯)的制造;將得到的砂型(芯)各部分組合后進行澆注得到模具鑄坯;利用三維掃描技術對各個環節的產品進行精度檢測。 按照此工藝路線可以對鑄造的各個環節進行數字化的控制及調節,從而得到合格的模具鑄坯。
關鍵詞:熱沖壓模具;3D 打印;鑄造模擬
高強度鋼板代替傳統鋼板可以減少車身重量,并提高碰撞安全性,實現汽車輕量化。 與傳統鋼板不同,高強度鋼板的成形需要內部帶有隨形冷卻水道的熱沖壓模具,來保證零件的成形性要求以及良好的力學性能。
隨形冷卻水道的走向與模具型面的形狀基本一致, 且中心距離型面的距離都相同。內部隨形冷卻水道的成功成形,是熱沖壓模具制造的重點及難點。 目前熱沖壓模具制造工藝中,鉆孔工藝可以加工方向不變的直水道,但是很難滿足隨形要求;鑲 拼工藝對密封提出很高的要求;鑄 造工藝中預埋不銹鋼管可以得到隨形的冷卻水道,但是冷卻效果不佳,而 預埋陶瓷芯存在去除工藝繁瑣等缺點。3D 打印技術是近幾年非常熱門的技術,但是受制于打印材料的高成本,此項技術在工業生產上并沒有大面積應用。
使用 3D 打印技術打印出普通造型方法難以成形的砂型(芯),對于結構復雜的金屬零件, 特別是熱沖壓模具這種具有復雜內腔結構的金屬零件具有重要意義。
1 、技術路線
以某一款轎車熱沖壓模具為研究載體, 該熱沖壓模具的設計綜合考慮計算機 CAD 參數化建模、熱沖壓及淬火仿真分析、 水冷模具管道設計及優化等科學問題。圖 1 為一個典型車身模具鑲塊, 該模具具有復雜型面, 由于隨形冷卻水道要跟型面走向一致且要跟型面距離相等,所以冷卻水道的結構也比較復雜。
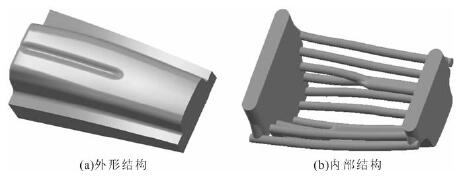
圖 1 鑄件的外形結構以及內部結構
傳統鑄造工藝中, 冷卻水道部分需要通過下芯的工藝實現,按照設計要求,每一根水道的形狀結構不盡相同, 所以每一根水道的成形都需要設計相對應的芯盒來實現,工藝比較繁瑣復雜。 由于砂芯比較細,單根砂芯很容易發生偏移而造成最后成形的水道與設計出現偏差。在汽車熱沖壓模具的數字化鑄造工藝路線中,首先對模具鑲塊進行鑄造方案設計, 此部分包括鑄件分析、澆冒口設計以及分型設計;將得到分型各部分進行切片處理得到打印數據,將打印數據傳輸到3D 打印設備中進行加工制作得到相應的砂型(芯);對砂型(芯)進行鑄造前處理,將各部分按照分型設計組合后進行澆注試驗;其中在各個加工制造過程中,使用三維掃描儀對各部分得到的產品,包括砂型(芯)以及最后得到的鑄坯進行掃描,然后進行精度評價。 圖 2 為整個工藝流程圖。
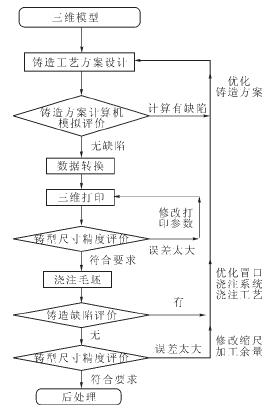
圖 2 數字化鑄造工藝路線
2 、鑄造方案設計優化
2.1 鑄件分析
由于后期鑄造表面質量并不能達到模具工作要求,模具型面需要后期機加工,而通過 3D 打印的砂型澆注得到的鑄坯精度很高, 僅需要一次精加工,加工余量不需要很大,取為 3 mm.
本試驗目的是得到一套汽車熱沖壓模具的數字化鑄造工藝路線, 主要為驗證基于此路線的模具及其冷卻水道的最后成形, 用鑄造高溫性能與模具鋼相似的 35 鋼代替驗證其成形性 ,鑄造縮尺為2.5%。
2.2 澆道與冒口的設計及優化
由于模具的復雜型面一側為將來沖壓的工作面,所以這個工作面需要有比較好的鑄造性能,在鑄造方案設計時,將這個面置于底側。 采用底注式澆注方案,澆口設計在鑄件的最底端。
由于隨形冷卻水道的直徑大約在 10~12 mm,對應的砂芯直徑也很細,鋼液澆注時, 需要保證鋼液在上升充型的時候要平穩,故采用 開放式澆 注系統,減少鋼液對砂芯的沖擊。
澆道橫截面的面積比取∑F直∶∑F 橫∶∑F 內=1∶1.2∶1.5,直澆道為阻流面,根據以下公式計算阻流面面積以及澆注時間:
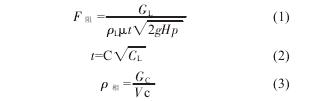
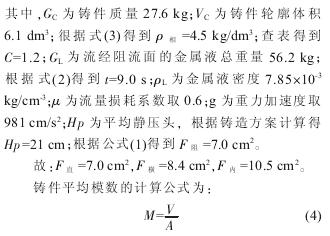
式中 ,V 為鑄件體積 3 540.05 cm3,A為傳熱表面積 1781.22cm2,根據式(4)可得,鑄件模數 M=1.98cm。根據鑄件模數,通過查,選取冒口為標準圓柱形冒口,其中直徑高度均為 120 mm。
依據計算得到的澆注系統以及冒口尺寸,鑄造方案設計如圖 3。 將設計的鑄造方案 CAD 數據轉化為有限元網格數據文件后,用 procast 鑄造模擬軟件對鑄造方案進行計算
,對澆注系統以及冒口的設計進行校核。
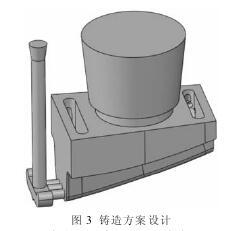
計算結果最后凝固位置位于冒口內,證明了冒口設置的合理性, 但是由于各部分砂型采用 3D 打印的方案制作,所以冒口的設計并不需要完全按照標準形狀設計,而可以參照模具的結構進行單獨設計。 由于此模具呈長條狀,且一側質量大于另一側,所以設計冒口形狀為腰圓形,且腰圓形兩側圓弧并不相等,圓弧半徑較大的一側對應于模具鑄件質量比較大的一側。
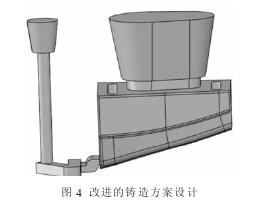
圖 4 中所示,改進的鑄造方案中冒口為腰圓形冒口。由于隨形水道的直徑比較小,對應的水道芯的直徑也會比較小,為了降低澆注時鋼液對砂芯的沖擊,所以要考慮降低鋼液進入鑄型時的速度。 除了采用全開放的澆注系統外,在內澆道與橫澆道上做一定的緩流設計,而由于采用 3D 打印制作的工藝,并不會因為澆道設計的復雜而增加制造難度。 圖 4所示,改進的鑄造方案設計中內澆道與橫澆上有緩流設計。

圖 5 最后凝固位置
腰圓形冒口形狀的設計, 可以起到標準圓形冒口相應的補縮作用, 圖 5 所示為兩種冒口設計中計算的最后凝固位置, 以看到最后凝固位置都位于冒口中。由于腰圓形冒口與模具形狀相對應,可以減少冒口質量從而提高工藝出品率。通過比較計算結果中鋼液流經內澆道時的速度, 可以發現在內澆道橫澆道上做緩流設計可以減少鋼液進入鑄件的速度。
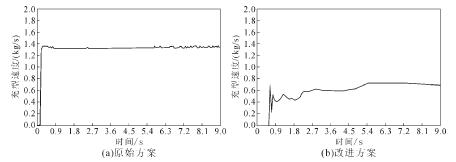
圖 6 鋼水流經內澆道的速度
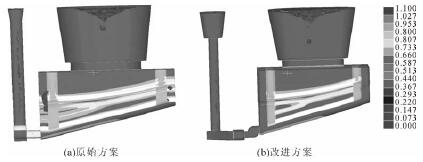
圖 7 縮松縮孔示意圖
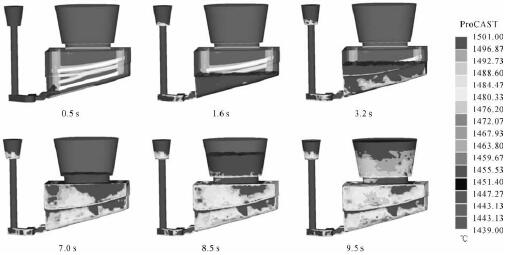
圖 8 充型示意圖
圖 6 所示為不同設計的澆道計算得到的鋼液流經內澆道的速度。比較兩種設計計算得到縮松縮, 可以發現改進后的方案鑄件內部縮孔縮松明顯少于初始方案設計。 圖 7 所示為縮松縮孔計算結果。選定改進后的鑄造方案為實驗澆注方案, 圖 8所示為不同時間下的充型圖, 充型期間比較平穩。3 3D 打印鑄型在完成鑄造方案的設計以及校核優化后, 需要對鑄件的陰模進行分型設計。由于各個部分采用 3D打印工藝進行制作, 所以分型時并不需要像傳統砂型鑄造分型需要考慮的拔模問題。 考慮到最后各個砂型的組合以及 3D 打印設備制作效率, 將鑄件陰模分成四個部分:下型部分,砂芯部分,冒口部分,澆注系統部分。 圖 9 為鑄件陰模的分型設計。
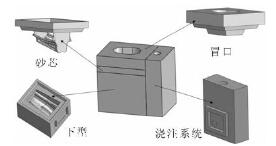
圖 9 鑄件陰模的分型設計
采用 SLS 法(選擇性激光燒結法)加工打印各個部分。 由于砂芯部分中隨形冷卻水道芯比較細,打印砂芯不能使用一般的覆膜砂,因此采用強度指標比較高的寶珠砂,可以保證打印成功率以及打印得到砂芯強度。 其他部分采用一般砂型所需要的普通覆膜砂。 打印過程中,調整打印設備中激光的掃描功率,以及打印設備腔體內環境溫度,特別對于砂芯部分,由于結構比較復雜,在加工時需要對打印參數精確控制。
各部分的加工參數見表 1。將 3D 打印的預成型產品放入烘箱中烘烤以使其強度滿足澆注要求。 為了防止在烘烤時發生變形,將砂型周圍埋上細小的玻璃珠。 表 2 為烘烤參數。
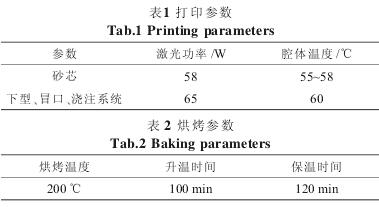
圖 10 所示為 3D 打印設備打印制作以及烘烤完成的砂芯以及砂型。打印制作的砂型的尺寸精度直接影響最后得到的鑄件尺寸精度。 使用三維掃描儀對打印得到的各部分砂型進行掃描測量, 將測量所得的點云數據與三維 CAD 數據進行精度比對, 確定砂型的制作誤差。 圖 11 為砂芯的精度比對結果,可以看出砂芯的整體制作誤差在 1.5 mm 以內,根據誤差分布圖以及誤差云圖顯示結果, 隨形水道部分對應的砂芯制作誤差在0.75 mm 以內 , 且大部分誤差在0 . 30 mm 以內。 由于砂芯部分對應鑄件的隨形水道部分, 而最后隨形水道位于鑄件內部無法測量其尺寸精度, 所以此時測量的砂芯精度可以為最后鑄件內部的隨形水道尺寸精度提供參考。
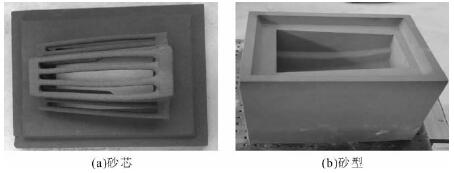
圖 10 砂芯與砂型
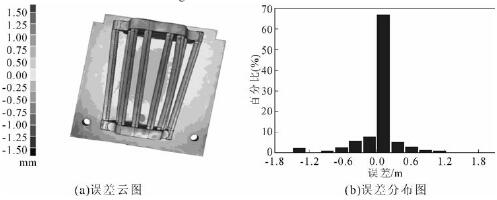
圖 11 砂芯精度檢測結果
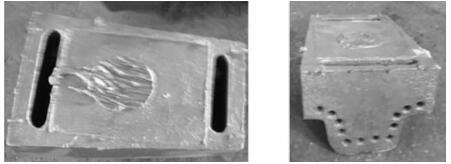
圖12 模具鑄坯
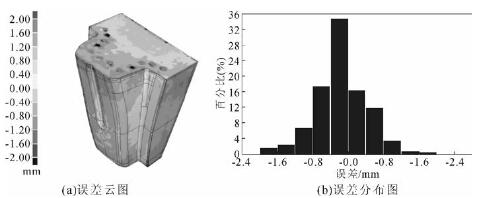
圖 13 鑄坯精度檢測結果
4 、澆注及澆注結果
將各部分砂型按照圖 9 的分型設計進行組合,組合完成后進行澆注,按照之前模擬計算得到的 1 560 ℃的澆注溫度進行澆注。 圖 12 為澆注得到的模具鑄坯, 使用三維掃描儀對鑄坯進行掃描后再進行精度評價。 圖 13 所示為鑄坯精度評價,根據結果發現鑄坯的整體尺寸誤差大部分集中在 2 mm 以內,工作型面的制作誤差在 1.2 mm 以內,根據誤差分布圖分析,大部分誤差在 0.8 mm 以內。將模具進行剖分操作, 一方面檢驗其內部水道的成形情況, 另一方面檢測模具內部是否有縮松縮孔等鑄造缺陷。
圖 14 為鑄坯剖分結果,根據剖分結果可以看出,內部冷卻水道完全成形,并沒有水道堵塞的情況出現, 且模具內部不存在鑄造缺陷。
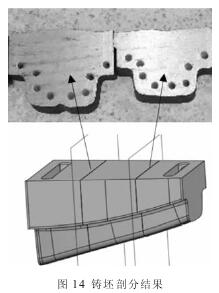
由于得到的鑄坯尺寸已經接近所需要的模具尺寸, 所以鑄坯進行相關熱處理及一次表面精加工即可得到最后的熱沖壓模具。
5 、結論
汽車熱沖壓模具由于內部存在隨形冷卻水道 , 生產制作難度很大 。 本文結合3D打印技術 、傳統砂型鑄造技術以及鑄造模擬技術 、三 維掃描技術 , 提出汽車熱沖壓模具 的數字化鑄造技術 。 利用鑄造模擬技術設計優化出最合適的鑄造方案 ,通過3D打印技術打印出高精度的砂型 ,將砂型組合后進行澆注得到高精度的鑄坯 ,在整個過程中 , 通過三維掃描技術對各個環節的產品進行精度評價 。 整個技術路線中 ,每個環節都可以通過數字化控制與調節以保證熱沖壓模具的成型質量 。
此種工藝路線對于汽車熱沖壓模具這類內部復雜結構的鑄件成形具有示范意義。
投稿箱:
如果您有機床行業、企業相關新聞稿件發表,或進行資訊合作,歡迎聯系本網編輯部, 郵箱:skjcsc@vip.sina.com
如果您有機床行業、企業相關新聞稿件發表,或進行資訊合作,歡迎聯系本網編輯部, 郵箱:skjcsc@vip.sina.com
更多相關信息