誤操作導致自動換刀系統故障典型案例分析
2024-7-22 來源: 中航西安飛機工業集團股份有限公司設備廠 作者:蔚騰,陳國良,盧西寧
摘要:針對數控加工中心由于操作不當引起的自動換刀機構典型故障,分析故障產生的原因和排除方法,提出預防該類型故障的有效措施。
關鍵詞:數控加工中心;自動換刀;刀具管理;刀長
0 引言
作為工業母機,數控機床的應用越來越廣泛,實際維修中經常遇到由于操作不當引發的設備故障。特別是對于具備自動換刀功能的機床,由于操作不當造成刀具參數錯誤引發的設故障,輕則造成工件超差,更有造成設備損壞的巨大風險。
1、換刀子程序重名引起機床換刀動作異常
1.1 故障現象
一臺操作系統為 Sinumerik 84OD SL 的加工中心在進行自動刀具交換時動作異常,輸入換刀指令 TXX 后,機床 Z 軸未像正常情況抬高至 Z 軸預設的換刀點,而是向工作臺方向快速進給,并且主軸開始高速旋轉,緊急按下急停按鈕終止 Z 軸的繼續進給才避免了銑傷工件、損傷主軸的重大設備事故。
1.2 故障分析與排除
維修人員利用發生故障的程序對故障現象進行復原再現。
為了保證設備和人員安全,在輸入換刀指令調用換刀子程序進行換刀之前,激活機床的單段進給“Signal Block”模式,并將進給倍率旋至 10%擋位。在進行測試時發現,在進行換刀動作時,Z 軸沿負方向進給并且伴隨主軸高速旋轉。繼續測試發現 Z 軸降低一定高度后不再繼續進給,但主軸依然高速旋轉,按下“CycleStart”按鍵繼續單歩運行,發現機床 3 個坐標均開始發生位移。
多次按下“Cycle Start”按鍵繼續進行測試觀察,發現機床工作臺運動軌跡近似于正在加工的工件,經分析判斷此時機床在進行自動加工,運行程序為將要加工的下一道工件程序。
詢問操作人員機床發生故障之前的操作行為,得知加工的工件為批量產品,工作臺面上同時陣列布局 8 個工件,其加工程序相同,只是起到點有差別。通過改變工件原點來進行自動加工,為了便于調用加工子程序,加工時不斷更改程序名為 L1、L2 至L6,發生故障時剛好加工至第 5 個工件,在執行換刀指令時發生了上述故障,西門子系統默認換刀子程序名為 L6,機床廠家會編譯一個換刀子程序便于使用,該程序通常存儲在“Manufacture”文件夾下,標準 L6 子程序一般包含 3 部分,如圖 1 所示:
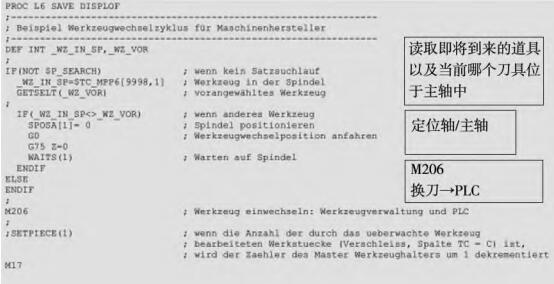
圖 1 L6 換刀子程序示例
西門子系統可通過調用 M6 指令、調用 L6 子程序和直接調用目標刀具名 T=“xx”三種方式實現自動刀具交換。在本例中,加工子程序執行到 M6 代碼時,激活機床自動換刀功能。故障原因是由于操作人員新命名的 L6 子程序和西門子數控系統的換刀子程序 L6 重名,因此在執行第 5 個子程序 L5 時,當執行換
刀指令時,數控系統直接調用了操作人員新命名的存儲于用戶加工程序“workpiece”目錄下的 L6 加工子程序,導致機床換刀動作異常。重新命名加工子程序后再執行換刀指令,機床順利完成目標刀具的更換,故障排除。
1.3 故障反思
西門子數控系統 L6 子程序為自動換刀專用名稱(西門子系統NC 參數 MD10716 定義,默認值“L6”),通常存儲于 Manufacture 循環目錄下,在系統執行換刀指令時進行調用。而在這一案例中,操作人員在“工件”目錄下建立了一個同名的 L6 加工子程序,導致在進行換刀動作時發生錯誤調用。針對這一間題,對操作人員進行了培訓。同時需要注意的是,西門子系統還有一些用戶變量和系統變量都有特殊定義,需要操作人員了解,防止由于重復命名引起設備故障。
2、換刀交換時終止程序致主軸刀具刀長丟失
2.1 故障現象
一臺操作系統為 Sinumerik 84OD SL 的加工中心在加工工件時發生故障,主軸刀具撞上加工工件造成刀具斷裂、正在加工的產品報廢的嚴重后果。
2.2 故障分析與排除
通過現場模擬對故障現象進行復原再現,發現在加工時刀具路徑與發生故障時一致。經詢問操作人員,該程序為定型程序確認無誤,且在發生報警之前采用該程序進行了一次粗加工,在開始進行精加工運行 2 min 左右就發生了事故。對該設備故障進行分析,發現機床當前主軸刀具刀長(在 Z 軸方向的長度)值為“0”,檢查機床設定有效零偏后確認刀長設定值同樣為“0”。由于機床主軸刀具有效刀長和實際刀具長度數值相差250.95 mm,因此在加工時 Z 軸向下多進給了 250.95 mm,導致發生設備事故。
經檢查確認當前主軸刀具刀號正確無誤,但是加工界面下的刀長“0”和刀具管理界面下的該刀具定義的刀長“250.95”不一致。根據操作人員描述,在發生故障前剛進行過一次粗加工,完成后進行了一次刀具測量動作,然后采用同一刀具進行精加工,因此無法確定何時刀具長度丟失。
通過試驗,執行換刀命令來更換其他刀具進行測試,刀號和刀長都正確,重新換回發生故障的刀具后刀具刀長變為“250.95”,一切正常。其后繼續進行了 4 h 機床空運行對機床換刀動作進行反復測試,模擬可能引起故障的條件,但都未能再現上述故障。
查看機床報警記錄,確認機床發生故障前 24 h 內無報警發生,該機床連接有 MES 系統用來監控機床運行狀態。打開MES系統運行記錄發現機床運行狀態基本和操作人員描述一致。在發生報警之前 4 h 機床進行過 2 次短暫的 MDA 運行,其后機床待機 30 min(此時操作人員在進行工件裝夾)。采用發生故障時的程序進行了 2 h 左右的加工,再停機 3 min 又有一條只執行了3 s 的程序(程序名:_MA_JOG_STEP1_MPF)調用記錄(這與操作人員描述有偏差),引起了維修人員的注意。再結合其后維修測試時的記錄,可確認每執行一次刀具交換都會產生一條調用該程序的記錄,但是不同的是,其后測試時程序的執行時間在15~45 s 內,這是由于刀具交換時目標刀具在刀庫位置不同引起。但是在發生故障前的這一換刀動作紀錄僅為3 s,明顯存在異常。通過查找資料,在執行換刀指令時,系統會根據程序的執行情況對主軸刀具長度進行實時賦值,主要參數見表 1。
表 1 自動刀具交換時主軸刀長參數
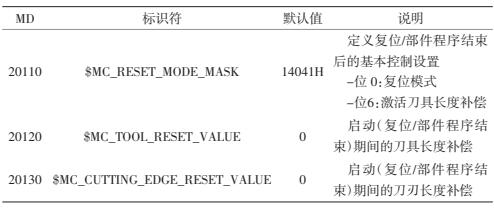
模擬該條記錄作如下測試:在執行換刀命令后 3 s 時按下“Reset”按鍵終止換刀程序,機床未發生任何報警,MES 系統會產生一條該程序時長 3 s 的調用記錄。由于程序未執行完畢,系統在程序復位時根據參數 20120 設定的默認值“0”將主軸刀長設置為“0”,而不是正常程序執行完畢后激活刀具長度補償的“250.95”,這是造成故障發生的原因。
2.3 解決方法
針對這一問題,對操作人員進行了培訓,并完善了安全操作規程,以杜絕由于人員誤操作導致的事故。
3、忽視刀庫異常報警導致刀具錯誤調用
3.1 故障現象
一臺操作系統為 Sinumerik 828D SL 的加工中心在加工時發生故障,主軸刀具刀長異常造成刀具斷裂、加工工件報廢的嚴重后果。經過檢查發現當前主軸刀具刀號正確,但是實際刀長和刀具管理界面刀具列表的設定值存在偏差,操作人員再次檢查確認當前主軸刀具并不是目標刀具。
3.2 故障分析與排除
查看機床報警記錄,發現機床在發生故障前有過一次報警記錄,提示刀庫刀具計數開關信號異常。詢問操作人員得知該報警提示發生時為黒色對話框,機床可以正常進給,因此操作人員在進行故障復位后繼續進行后續加工。發生故障的原因是操作人員未對機床報警進行正確處理從而引起刀具管理功能數據紊亂。
西門子系統 OPERATOR 人機界面的刀具管理功能對機床刀庫和刀具信息進行實時管理,如圖 2 所示。
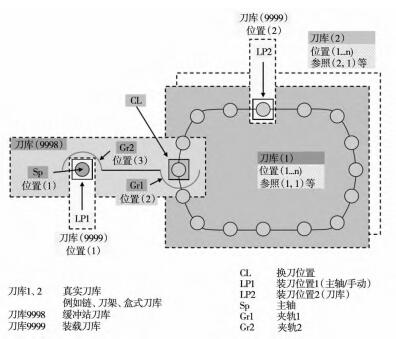
圖 2 刀具管理定義的刀庫示意圖
該機床為 24 把刀的鏈式刀庫,預選刀動作通過異步電機和刀庫零位檢測開關、刀具計數開關控制。每轉過一個刀位,計數開關觸發一次并實時更改刀具管理系統的刀具信息參數。當機床提示刀庫計數開關信號異常時,系統無法準確計算出實際刀庫轉過的刀位數,而操作人員未及時停機并告知維修人員檢修。在進行下次刀具交換之前機床可以正常運行,當再次執行換刀動作時,由于刀庫計數開關信號異常導致機床在刀具尋址時發生偏差,所選擇刀具并不是目標刀具,但是數控系統并不能對此錯誤做出判斷,導致機床換刀動作可以正常進行,但是實際刀具是錯誤的刀具,刀長發生改變引起工件的損傷。
經檢查,刀具計數開關存在松動現象,重新緊固該開關并執行機床刀庫回零動作,建立正確刀具列表,再次執行換刀動作刀具自動交換動作正常。
3.3 解決方法
該故障的發生是由于操作人員在機床發生報警時忽視機床報警信息而草率進行了復位確認,因此對操作人員進行培訓并完善安全操作規程。通過修改 PLC 程序,提高該報警響應級別,在發生該報警時切斷機床進給,杜絕由于誤操作引發事故。
4、結語
隨著數控技術的不斷發展,數控系統的開放性越來越高,給機床廠家和操作人員提供了更多的權限和空間,這對機床操作人員技能水平提出了更高的要求。誤操作會導致機床報警甚至發生設備損傷事故,因此對于操作人員培訓和管理亟待加強,同時需要通過技術手段來規避誤操作造成的隱患。
投稿箱:
如果您有機床行業、企業相關新聞稿件發表,或進行資訊合作,歡迎聯系本網編輯部, 郵箱:skjcsc@vip.sina.com
如果您有機床行業、企業相關新聞稿件發表,或進行資訊合作,歡迎聯系本網編輯部, 郵箱:skjcsc@vip.sina.com
更多相關信息