精密離心機主軸回轉誤差測量仿真技術研究
2017-1-10 來源:中國工程物理研究院總體工程研究所 作者:張 榮,牛寶良,凌明祥,王 玨,周繼昆
摘要:精密離心機主軸回轉誤差直接影響精密離心機動態半徑的測量、離心加速度輸出精度以及精密離心機主軸運行安全性,必須精確測量主軸回轉誤差參數;介紹一種應用3 個電容測微儀測試并分離主軸回轉誤差與圓度誤差的方法,利用MATLAB 對三只電容測微儀安裝角度誤差、主軸全周采樣點數、測試系統本底噪聲對主軸回轉誤差測試結果影響進行仿真分析,得出采樣點數N、測微儀安裝角度誤差δα、δβ 以及測試系統本底噪聲對回轉誤差分離的影響,基于仿真結果確定了1 0 -6 量級精密離心機主軸回轉誤差測量的幾個工程參數。該方法已應用于某高精度精密離心機主軸回轉誤差精密測試中,實測表明,轉速在300 rpm 內精密離心機純回轉誤差測量結果為0.2 5 μm,滿足1 0 -6 量級高精度精密離心機的研制指標需求。
關鍵詞:精密離心機;回轉誤差;圓度誤差;三點法;電容測微儀
0.引言
精密離心機空氣主軸徑向回轉誤差是影響高精度精密離心機性能的重要因素,主要表現在:1 ) 在利用外基準測量精密離心機動態半徑時,主軸徑向回轉誤差將混入動態半徑測量值中,回轉誤差量級較大時,其對動態半徑的影響不可忽略,必須對動態半徑進行補償,否則經離心加速度補償模型[1 ]輸出的加速度信號精度無法得到保證;2 ) 主軸徑向回轉誤差直接關系到主軸運行安全,對于空氣靜浮主軸,氣膜厚度通常僅幾微米,為保證離心機在各G 值下安全運行,必須對主軸的回轉運動誤差進行監視,設定主軸回轉運動誤差限,當主軸回轉運動誤差接近超限值時,離心機必須停機。因此,為滿足高精度精密離心機研制技術指標,對其主軸的回轉運動參數必須進行精確測量。針對某1 0 -6 量級精密離心機研制,精密離心機主軸回轉誤差的精度指標為≤0.5 μm,為完成該參數的高精度測試,筆者提出采用電容測微儀和三點法進行測試,并設計精密測試系統完成了1 0 -6 量級精密離心機主軸回轉誤差的測試,實測主軸純回轉誤差為0.2 5 μm。
1精密離心機主軸回轉誤差測試方法研究
目前,對于1 0 -5 及以下量級精密離心機研制, 由于量級低,主軸回轉誤差的量值大小對精密離心機輸出加速度精度影響不明顯,而主軸運行安全性監測是主要的,常采用在主軸截面上安裝兩只[2 3 ]正交的電容傳感器測量主軸轉動一周測微儀輸出最大值與最小值,這種測量無法測試出純主軸回轉誤差運動極值。對于1 0 -6 及以上量級的精密離心機研制,必須考慮主軸安全性以及主軸運動誤差對動態半徑的貢獻,采用雙測微儀法測試無法滿足測試要求,必須采用新的測試手段。
1.1主軸回轉誤差測試的難點
主軸回轉誤差測試難點在于通常主軸圓度誤差和回轉誤差同時混雜于測試結果中, 并且圓度誤差往往比回轉誤差大得多,測試純回轉誤差較難,解決方法有兩種:一種是借助于安裝在主軸上的標準球, 采用電容非接觸式或電感接觸式測試標準球的徑向跳動量, 此時忽略標準球圓度誤差, 采用正交雙測微儀合成李薩如[4 ]圖獲得主軸回轉誤差, 但該法僅適用便于安裝標準球的場合, 同時標準球的安裝還存在偏心誤差,必須在測量結果中進行一次諧波分離去偏心誤差; 對不便安裝標準球的測試, 如本項目中的精密離心機主軸, 采用在主軸外沿安裝測微儀測試, 測試結果包括了主軸回轉差和圓度誤差兩類信號,必須通過測試方法從結果中分離出圓度誤差信號,得到真實的回轉誤差信號, 故信號分離算法是關鍵。目前基本的圓度誤差分離方法有反向法[5 ]、多點法[6 ]、多步法[7 ]等, 多點法分兩點法、三點法、四點法等。
表1 [8 ]是幾類誤差分離方法精度統計, 通常各方法應用在不同的測試場合,但對于回轉誤差的總體分離精度均可控制在1 0 %以內,這為本項目中空氣主軸的回轉誤差的測試奠定了基礎。從技術實現難易程度、成本等綜合考慮選擇在項目中應用三點法測試主軸回轉誤差。
表1 回轉誤差與圓度誤差分離方法及誤差表

1.2 三點法主軸回轉誤差分離測試原理
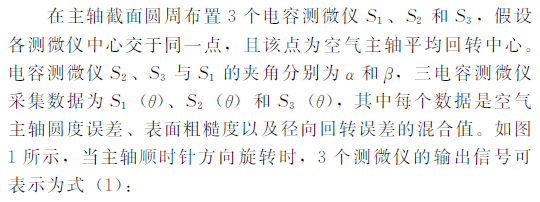
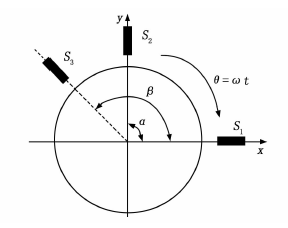
圖1 三點法主軸回轉誤差分離測試示意圖
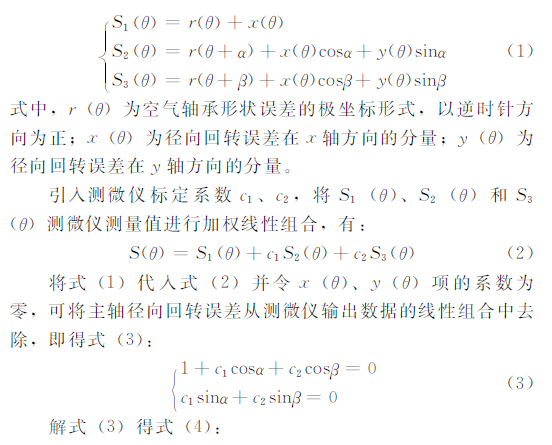
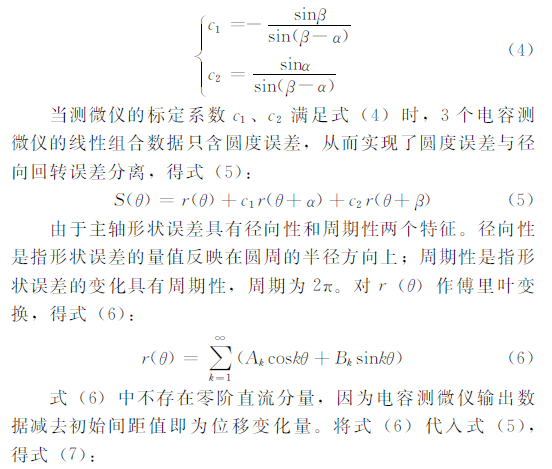
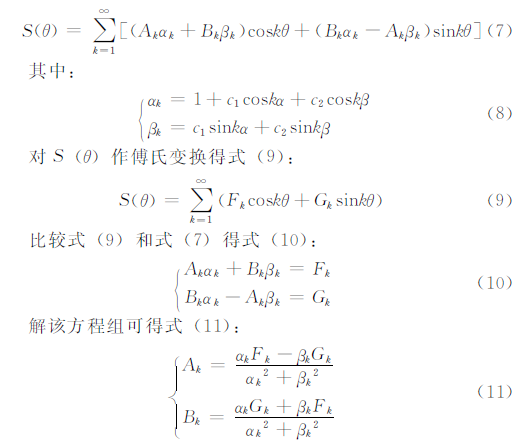
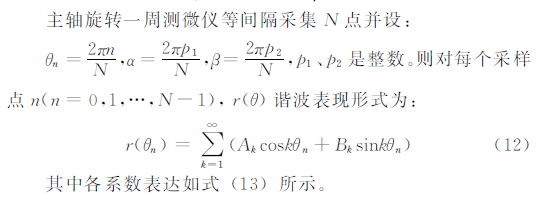
由式(1 3)可知,采樣點數N 、測微儀安裝角度誤差以及諧波分析階次均會給分離精度帶來影響,故須根據諧波分析階次與分離精度要求確定三測微儀安裝角度; 根據ISO 標準,當被測零件圓度誤差的諧波次數大于22 ~45 階后,可將其歸結為零件表面粗糙度和波度[9 ],本項目參考ISO 標準, 設定主軸圓度誤差諧波上限為45 階,45 階以上的諧波成分將作為表面粗糙度與波紋度處理。圓度誤差分離完成后,則回轉誤差也即得到分離。
2.主軸回轉誤差分離測試影響因素的仿真分析
精密離心機主軸回轉誤差測試實際設計時,需確定主軸全周采樣點數N 、三測微儀安裝角度誤差以及測試系統本底噪聲對回轉誤差分離結果的影響程度, 為此在MATLAB 下
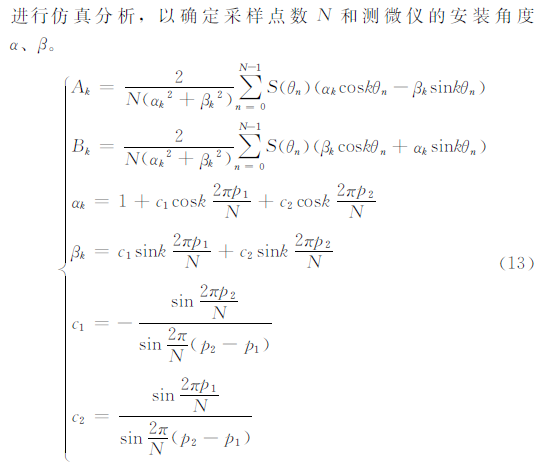
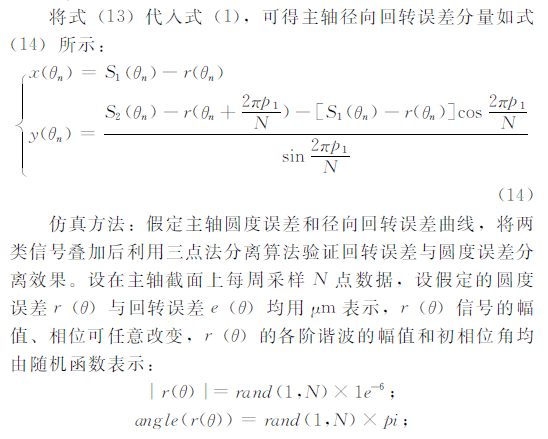
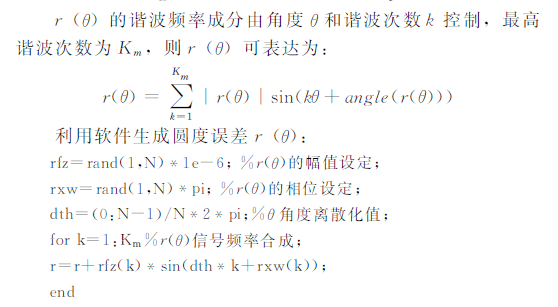
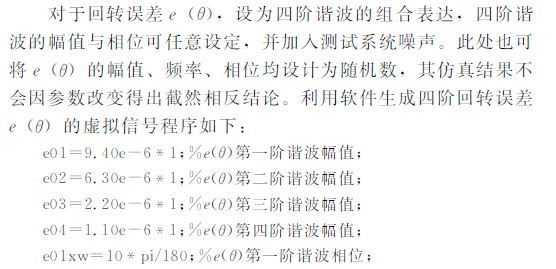
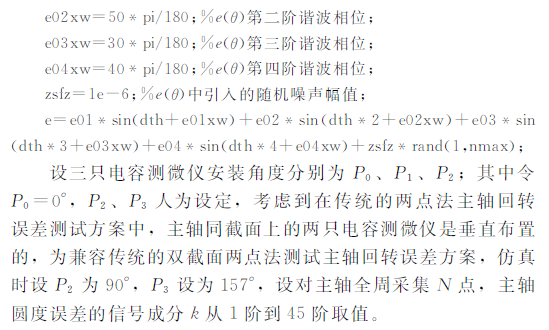
2.1采樣點數N 對回轉誤差測試影響仿真
分別設定N =1 28,N =5 1 2 進行仿真,回轉誤差與圓度誤差的分離結果如圖2 ~圖5 所示。
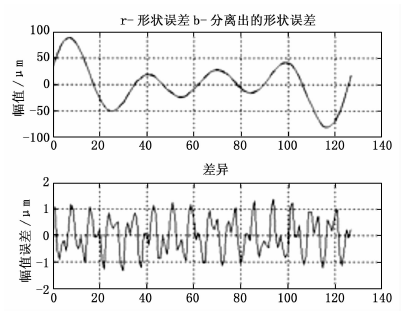
圖2 N =1 2 8 時圓度誤差設定與分離結果
從仿真結果看,N 值越大,回轉誤差與圓度誤差的分離精度越高,適當選擇N 值可使圓度誤差分離信號的誤差達1 0 -1 3 量級。本項目中N 取1 600 點。
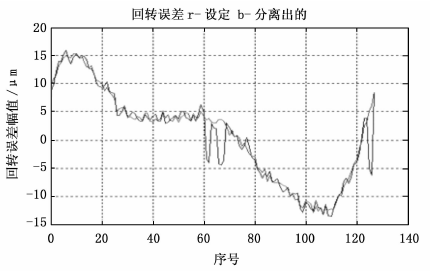
圖3 N =1 2 8 時回轉誤差設定與分離結果
2.2 測微儀安裝角度對回轉誤差測試影響仿真
設三只測微儀理論安裝角度分別為0°,α=90°,β=1 5 7°。工程設計時因測微儀裝配誤差使各安裝角度存在誤差,以第一只測微儀安裝位置為參考,第二只與第三只測微儀相對于第一只測微儀的安裝夾角存在偏差δα、δβ, 仿真δα、δβ 對回轉誤差分離結果的影響。考慮到離心機最高轉速為300 rpm 的工程實際,設測微儀安裝偏差角δα、δβ 控制在±1°范圍內,在輸入信號和采樣點數N =1 024 不變時,開展如表2 仿真分析,給出代表性的仿真結果如圖6 ~圖9 所示。
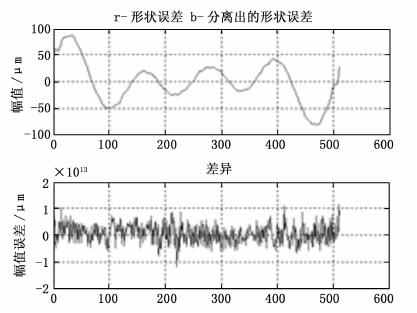
圖4 N =5 1 2 時圓度誤差設定與分離結果
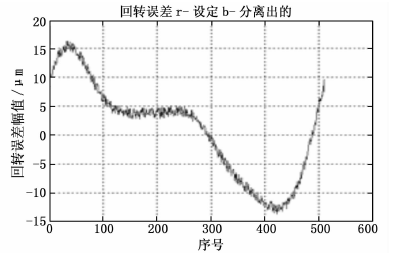
圖5 N =5 1 2 時回轉誤差設定與分離結果
表2 仿真測試測微儀安裝角度偏差δα、δβ 表 c°
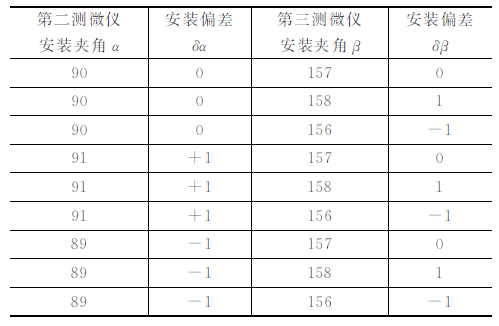
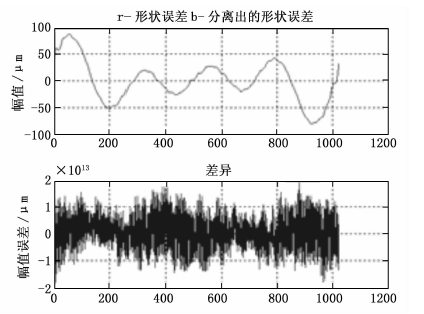
圖6 α=90°,β=1 5 8°圓度誤差設定與分離結果
仿真表明,在實際安裝夾角α、β 偏離理想安裝夾角± 1°時,安裝夾角的偏差δα、δβ 對主軸圓度誤差與徑向回轉誤差
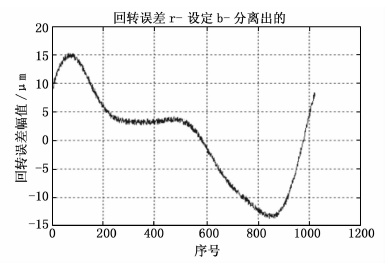
圖7 α=90°,β=1 5 8°回轉誤差設定與分離結果
分離有一定影響,但影響較小,圓度誤差分離誤差量級通常在1 0 -1 3 以上,可忽略。其中,僅在α=90°、β=1 5 6°時圓度誤差的分離誤差達到了0.03 μm 左右, 這是由于安裝夾角引起的分離過程諧波抑制,多次仿真發現,這種諧波抑制現象引起的分離誤差最大均控制在0.05 μm 以下, 這對于本項目的主軸徑向回轉誤差分離影響較小可忽略。因此,在實際測微儀安裝
時可適度降低安裝精度,允許一定安裝角度偏差,并可根據角偏差的不確定度評估出主軸圓度誤差和徑向回轉誤差的分離不確定度。
投稿箱:
如果您有機床行業、企業相關新聞稿件發表,或進行資訊合作,歡迎聯系本網編輯部, 郵箱:skjcsc@vip.sina.com
如果您有機床行業、企業相關新聞稿件發表,或進行資訊合作,歡迎聯系本網編輯部, 郵箱:skjcsc@vip.sina.com
更多相關信息