數控車削螺紋類零件的有效編程方法—以螺紋軸任務為例
2020-5-18 來源:- 作者:-
摘要:螺紋的編程和加工是機械制造業從業人員必須熟練掌握的一項技能。根據典型零件螺紋軸的加工實例,介紹螺紋加工指令的含義及編程格式,并探討指令之間的區別,然后編寫了螺紋軸的加工程序和注意事項。
關鍵詞:數控車削 螺紋 有效 編程 方法
螺紋的編程和加工是數控車削加工教學中的一項重要課程,也是數控車床加工的一項主要內容,更是學生必須要熟練掌握的一項操作技能。因螺紋的種類較多,涉及的加工編程指令和方法不盡相同,本文將以普通外圓柱螺紋軸為例,闡述螺紋類零件的編程方法。
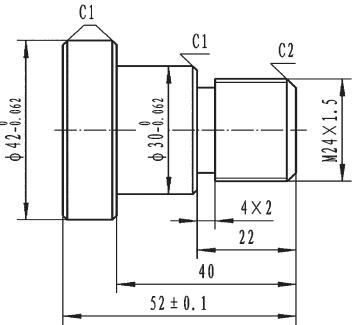
圖 1 螺紋軸
1、螺紋軸任務
如圖 1 所示,螺紋軸零件坐標系原點設在其右端面和軸線的交點上,機床的刀架是前置刀架。外圓柱面與退刀槽均已加工到尺寸要求,分別用 G32、G92、G76 指令編寫螺紋部分的數控加工程序。
2、任務實施
2.1 車削螺紋編程指令
編程指令如表 1 所示。
表 1 編程指令
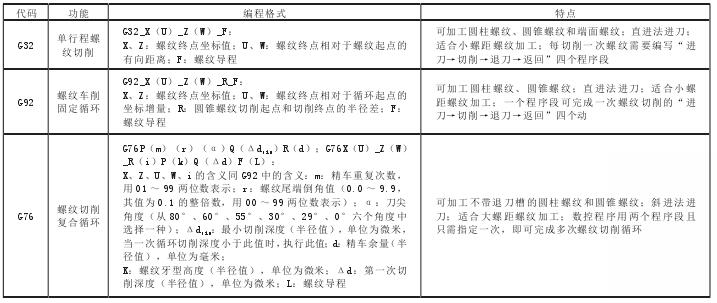
2.2 確定切削外螺紋的基本參數
2.2.1 確定背吃刀量和切削次數
切削螺紋時,背吃刀量遵循依次遞減的分配原則。加工螺紋時,背吃刀量和切削次數可以根據螺距的大小選擇,如表 2 所示。
表 2 公制螺紋加工切削次數與背吃刀量(直徑值)
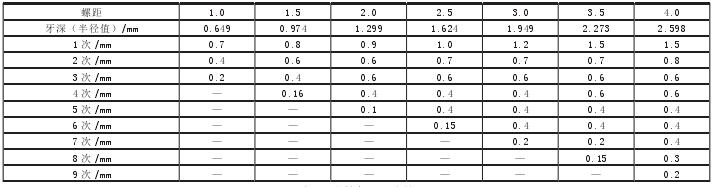
由表 2 可知,本例加工 M24X1.5 普通外螺紋,螺距為1.5mm 的螺紋牙深(半徑值)為 0.974mm,編程是按照直徑方式編程,所以總的切深量是 1.948mm。切削次數為 4 次,第 1 次背吃刀量為 0.8mm,第 2、3、4 次背吃刀量分別為0.6mm,0.4mm,0.16mm。
2.2.2 確定外螺紋小徑 d1外螺紋小徑 d1可根據經驗公式 d1=d-2h=d-1.3P 來確定,式中,d 為螺紋大徑,mm;h 為螺紋牙深,mm;P 為螺距,mm。對于本任務計算外螺紋小徑 d1=φ22.05mm。
2.2.3 確定每次切削直徑值(X 值)
每次切削直徑值根據切削次數和對應的背吃刀量來確定。由上文可知本任務第一次切削直徑(徑向終點坐標)為 X23.2,第二次切削直徑為 X22.6,第三次切削直徑為X22.2,第四次為切削到螺紋小徑值為 X22.05。
2.2.4 確定螺紋起點和終點軸向尺寸(Z 值)
加工過程中為保證螺紋螺距均勻,因此車削時在螺紋長度的兩端設置足夠的升速進刀段 δ1和減速退刀段 δ2,其中 δ1可取 2 ~ 5mm,δ2為退刀槽寬度的一半左右,取1 ~ 3mm。本例中取 δ1=3mm、δ2=2mm。
2.2.5 確定主軸轉速
螺紋切削時要選擇較低的主軸轉速,來降低刀具的進給速度。在實際教學中主軸轉速一般可按公式 n ≤ 1200/P-80 來確定。式中,P 為螺距,mm;n 為主軸轉速,r/min。取P=1.5mm,由公式計算 n ≤ 720r/min,這里取 n=500r/min。
2.3 編寫數控加工程序
編寫螺紋部分的加工程序如表 3 所示。
表 3 數控加工程序單

3 、注意事項
3.1 選擇直徑
刀具的擠壓會使螺紋大徑變大,因此外圓直徑要比螺紋大徑小些,一般比公稱直徑小 0.1P,P 為螺距。
3.2 選擇起點
使用 G92、G76 指令編程時需要設定循環起點,循環起點應設在加工螺紋的外部,本例將循環起點設在(X28,Z3)位置。
3.3 選擇格式
在 G32、G92、G76 指令編程格式中,F 為導程,不是進給量。
3.4 選擇進給量
螺紋加工時主軸旋轉一周,螺紋車刀的進給量必須等于螺紋的導程,因此螺紋加工過程中主軸轉速要保持恒定,并且不使用恒線速度控制功能。
3.5 減小誤差
為保證螺紋加工質量,螺紋加工前先設一定的磨損量,加工完畢后,在用螺紋環規、塞規等進行檢測。
4、結語
加工普通螺紋可以采用 G32、G92、G76 指令進行編程加工。G32 指令加工螺紋時,刀具的移動切削需要通過編程來完成,這會導致編寫的程序段較多,教學中不經常使用。G76 指令編程效率較高,一般適用大螺距螺紋,在螺紋精度要求不高的情況下,使用較多,本例僅介紹其編程方法。G92 指令簡化了編程,與 G32 指令相比提高了編程效率,因此應用更為廣泛,但 G92 指令受進刀方式的影響,螺紋中徑誤差大,加工時要經常檢測以保證螺紋的加工精度。總之,加工螺紋時選擇合理的編程指令和加工方法不僅能提高螺紋加工效率,還能保證螺紋的加工質量,更能降低生產成本。
投稿箱:
如果您有機床行業、企業相關新聞稿件發表,或進行資訊合作,歡迎聯系本網編輯部, 郵箱:skjcsc@vip.sina.com
如果您有機床行業、企業相關新聞稿件發表,或進行資訊合作,歡迎聯系本網編輯部, 郵箱:skjcsc@vip.sina.com