[摘要] 本文介紹了德國產BFT125/5鏜銑床在加工大型機械零件時,需要經常變換速度來達到加工要求,但在長期頻繁換檔變速進行加工時,導致工作臺進給與主軸箱進給速度部分缺失,影響了設備的正常使用。為使設備能夠在不大修情況下,發揮其重要作用,因此對該設備傳動進給進行改造。
關鍵詞 傳動鏈 進給速度 變速箱改造 進給量與電機轉速表
一、BFT125/5鏜銑床工作描述
BFT125/5鏜銑床是某廠重要大型機械加工設備之一,自該設備購入至今,經過幾十年的使用,機床各部位已經有嚴重的磨損,在日常操作中會經常出現故障而影響加工效率。隨著近幾年該廠的加工業務不斷拓展,該設備經常處在長期超負荷工作狀態下進行日常的生產加工時,因故障而經常維修;且有時因加工零件因設備進給原因而影響到零件的加工精度要求,從而又得需要修復加工零件而影響交貨時間。為能夠正常使用該設備,用戶迫切需要對該設備電氣控制與機械傳動部分進行改造。
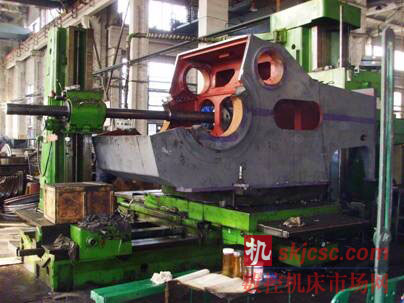
圖1 BFT125/5鏜銑床外形與加工零件圖
二、BFT125/5鏜銑床改造技術要求
由于該廠計劃任務緊張且該設備承擔加工任務量較多,無法較長時間停機進行設備大修。故在目前設備狀態下,要求對該設備機械進給傳動部分進行改造,保持原有進給量0.5mm/min~1600mm/min之間范圍,并實現無級變速;主軸箱內實施項修改,恢復傳動精度要求;電氣部分更換電控柜及其落后的控制方式,改用PLC做為主控制器,結合590+全數字直流調速裝置來實現自動化控制模式。該設備工作臺進給傳動與主軸箱進給傳動相同,因此本文主要從工作臺進給傳動改造方案的確定與現場安裝實施進行論述。
三、BFT125/5鏜銑床的進給運動描述
工作臺進給傳動鏈為: 雙速電機-→皮帶-→變速箱-→電磁離合器-→齒輪減速器-→工作臺運動
-→橫向電磁離合器--→經蝸輪蝸桿減速器--→齒輪齒條進給--→工作臺橫向移動
方式選擇----→縱向電磁離合器--→雙頭螺桿旋轉--→工作臺縱向移動
-→旋轉電磁離合器--→花鍵軸旋轉--→工作臺旋轉運動
變速箱內共有八個電磁離合器,其中變速箱輸入軸上有三個小型電磁離合器,第二個軸上有兩個電磁離合器,輸出軸上有三個電磁離合器。當同時吸合三個軸上的不同電磁離合器時,可變換出36種速度,從而實現工作臺進給與旋轉。工作臺進給量分別是0.5、0.63、0.8、1.0~1000、1250和1600mm/min。工作臺剎車制動是通過改變變速箱內另外兩個電磁離合器吸合來實現。
四、改造方案的確定論述
根據該公司提供的機械圖紙資料,并參照用戶技術要求,工作臺進給初步改造方案如下:
1、取消變速箱,將后續選型的電機通過聯軸器聯接到輸出軸端;
2、加裝聯軸器及電機支撐座,并固定在工作臺上,隨工作臺橫向一起移動;
3、拆卸工作臺防護罩,改造防護罩支撐架與工作臺的聯接;
根據原傳動方式,在拆除變速箱后工作臺進給傳動各軸所需轉速可以滿足進給量要求,且可以利用電機的轉速特性來控制;將原傳動路線上各傳動力矩進行計算后,發現每個速度所使用的力矩都比較大,不能采用直接聯接方式達到力矩要求,還必須使用變速箱變速傳動來達到各力矩要求。
通過使用變速箱傳動來增大傳動力矩,即可滿足要求,但變速箱內電磁離合器經常出現故障,必須要在傳動中不用或減少使用電磁離合器吸合次數,減少磨損。又分析若使用變速箱內傳動各軸,采用一種固定傳動路線來增大力矩可以滿足加工力矩的要求,但是不能滿足36種速度,只有增加到兩種傳動路線,通過電磁離合器來換速,可滿足力矩與速度要求。故在變速箱傳動路線中分析出兩條傳動路線,第一種傳動路線為電機經皮帶傳動至變速箱輸入軸,將輸入軸與第二軸上電磁離合器固定,使用輸出軸上兩個電磁離合器分別吸合進行變換傳動比,來實現速度的轉換,傳動的力矩也可保證。經分析傳動鏈,可有1:1(高速檔)和1:64(低速檔)的傳動比,經這兩個傳動比傳出力矩和速度可滿足要求;還有一種傳動路線1:1(高速檔)和1:100(低速檔)也能夠滿足傳動力矩與轉速進給要求,此種傳動鏈所選型電機功率要比前一種小一些。
在現場了解到,經常使用的進給量在中間段31.5mm/min~630mm/min 之間,這段進給量對應轉速變換是為滿足工件的不同部位加工;進給量在10mm/min以下與1250mm/min以上很少使用但必須有此進給量。經拆卸變速箱發現,輸入軸上傳動齒輪、離合器與第二軸上齒輪磨損較大,常用進給量對應電磁離合器摩擦片磨損嚴重,外表面燒黑。考慮為減緩或避免傳動進給時造成此現象,需要增加一個中速檔來滿足日常加工進給量要求。再次分析變速箱內傳動路線,發現輸出軸上中間電磁離合器能夠滿足中速檔的要求,其傳動比1:4;通過使用此傳動鏈,一則可以在經常加工工件時,只改變電機轉速來改變進給量;二則可以減少電磁離合器的吸合次數;三則可以針對中速檔(常用進給量范圍)加工力矩要求,最終確定出直流電機功率。這樣在變速箱內可將其中兩軸更改為固定傳動比傳動,與輸出軸相鄰的傳動軸進行改造,改變內部傳動路線,通過分別吸合三個電磁離合器得到三種傳動路線,及高速檔1:1、中速檔1:4和低速檔1:64。
另外一種改造方式雖然可使選用電機功率再選小一些,但是其在變速箱內改造時,輸入軸上要使用到電磁離合器進行吸合,且高速檔1:1與中速檔1:6、低速檔1:100的傳動路線不一樣,故從減少使用電磁離合器和傳動路線一致上考慮不使用此種傳動比進行改造。
通過利用原先輸出變速箱軸的最大需用扭矩進行電機功率的初步計算,在結合目前加工零件超出工作臺承載能力的40~50%,確定出電機功率與轉速。此次改造未選用交流電機,是因為在低頻率時,其輸出扭矩特性不如直流電機,若選擇在低頻率下滿足扭矩要求則選型功率會更大,且不經濟;故此次改造是以直流電機做為工作臺與主軸箱進給改造的動力源。 變速箱內部改造與原先傳動鏈如下圖。
圖2 變速箱內布局圖與傳動鏈圖
五、變速箱改造傳動鏈對應電機轉速范圍
高速檔傳動鏈:=1:1 輸出變速箱轉速:20~2500r/min
中速檔傳動鏈:=1:4 輸出變速箱轉速:5~625r/min
低速檔傳動鏈:=1:64 輸出變速箱轉速:0.3~35r/min
六、改造后的使用效果
通過采用上述確定的工作臺進給與主軸箱進給傳動改造實施方案,并配合電氣控制改造,經現場空車調試與帶載調試,均滿足設備加工要求。經設備一周滿負荷操作,并為滿足零件加工要求,不斷變換直流電機轉速來測試加工性能,均符合改造要求。該設備從改造使用至今,已使用六年多時間,均未出現傳動故障。
七、改造總結
1、通過此次鏜銑床進給改造,熟悉了德國進口BFT125/5鏜銑床的內部結構,掌握了各個傳動機構的具體功能與使用方法;該設備在增大加工能力上有很大的拓展空間,完全經過局部功能的增加可擴充更大的加工范圍;
2、通過此次鏜銑床進給改造,發現該設備傳動設計非常精巧,結構緊湊;各傳動操作獨立;維修操作時需要有很好的規劃性,特別是改造中需根據其部位具體結構進行合理設計和安裝布局,否則在安裝時會帶來很大困難;例如:將進口電磁離合器更換為國產電磁離合器時,由于型號與外形不一樣,要想使用就必須對整個傳動位置與布局進行合理設計與安裝布局,受傳動軸位置的影響其它傳動件必須也相應進行改造,盡可能在緊湊的布局中安排出合理的位置來進行改造;
3、通過此次鏜銑床進給改造,從中體會到改造的重要思路與根本的改造方法;并且得出結論:在設備改造時必須要以原傳動路線為依據,滿足工作進給速度的同時,還必須滿足各種加工能力的要求,否則不滿這兩個條件將會在改造中失去理論依據;
4、通過此次鏜銑床進給改造,感覺相關改造經驗相當不夠,在安排傳動路線過程中不能完全考慮到操作使用方面的因素,導致到現場了解后才能做出完善的改造方案;
5、改造方案中所設計的零件必須要求加工精度準確,減少在改造中的修改;現場施工過程中,需現場加工和安裝的零件、工作盡量安排出確切的加工時間與先后順序,減少等待時間,節約現場安裝時間;
6、以下是變速箱與工作臺進給電機新舊安裝改造、新懸掛箱圖。
圖3 工作臺進給改造前、后傳動方式對比
圖4 變速箱改造后傳動鏈 圖5 懸掛箱改造前、后對比
八、改造實施原則與注意事項
1、 無論采用哪種改造方案必須滿足每檔速度之間均有交叉;原先所有進給速度再改造后均需實現, 不能缺失。
2、 通過計算每檔傳動速度中均會有力矩不能滿足的情況,考慮經常所使用轉速的力矩均能達到要求,故將不能達到力矩的各速度做為調整設備時使用;且每種進給量對應力矩均有增大,小部分進行調整時使用。
3、 工作臺進給改造電機、傳動與支撐架安裝和主軸箱進給改造電機、傳動安裝與支撐架安裝現場實地進行,各變速箱中齒輪傳動改造與加工零件現場全部拆解后進行。
4、改造后的工作臺進給量對應直流電機轉速表內容略。
如果您有機床行業、企業相關新聞稿件發表,或進行資訊合作,歡迎聯系本網編輯部, 郵箱:skjcsc@vip.sina.com