弧比變化對電火花沉積Ni201修復層界面行為的影響
2016-12-14 來源:江西理工大學 作者:趙運才 劉宗陽 楊雷雷
摘要:再制造修復設備工藝參數(shù)選擇是決定修復層質量的關鍵因素。利用電火花沉積技術,在Q235鋼表面制備Ni201修復改性層,對比分析弧比取不同值時對修復層質量的影響,并利用掃描電鏡(SEM)、能譜儀(EDS)、X射線衍射(XRD)等檢測方法,研究了修復層與基體結合界面的微觀結構、元素分布及相組成。結果表明:弧比取值在35%~45%之間時,修復層組織均勻致密,基體元素與修復層元素相互擴散形成冶金結合,修復層主要由Fel9Ni、C03Fe7、Fe0.9Si0.1和CO.055Fel.945相組成。
關鍵詞:電火花沉積;弧比;Q235鋼;界面行為
0. 引言
電火花沉積(electro—spark deposition,ESD)技術實質上是一種微弧焊接工藝Ⅲ,是在惰性氣體環(huán)境中,利用旋轉電極與基體接觸形成的微弧脈沖放電產生高密度能量,瞬間產生高溫,將電極材料熔滲到金屬表面形成合金強化層的一種表面修復強化技術。利用電火花沉積技術在機械零件受損部位沉積修復改性層,可以修復并提高受損零部件的機械使用性能,從而延長機械產品的使用壽命,降低制造成本,因此,電火花沉積技術在軍工、航空航天、醫(yī)療、礦山、汽車行業(yè)等領域得到了廣泛的應用口。3]。隨著表面工程領域技術的不斷發(fā)展,電火花沉積技術已經成為再制造技術中一項重要的制造工藝。
由于電火花沉積技術在再制造領域具有重要意義,許多學者采用不同的電火花沉積工藝參數(shù),對修復層的微觀組織及力學性能等進行了不同角度的研究,但目前針對不同電火花沉積工藝參數(shù)下制備Ni201修復層界面行為影響的研究較少,且Ni201抗腐蝕、耐高溫性能良好,用作修復工件表面缺陷的材料可以得到表面質量高、加工性能好的修復層,因此,本文利用電火花沉積技術,采用不同的弧比(微弧放電時間長短的百分比)作為主要對比參數(shù),在Q235鋼表面沉積Ni201修復層,對不同參數(shù)下的修復層質量進行對比研究,并對修復層與基體結合界面的顯微組織、物象組成、元素分布進行研究分析,以期為電火花沉積技術在再制造領域的實際應用與推廣提供理論依據。
1.實驗材料和方法
1.1沉積材料及工藝參數(shù)
電火花沉積工藝采用DHD一6000型電火花沉積設備,修復層由人工手持沉積槍在氬氣保護下制備完成,放電脈沖輸出頻率40~1200 Hz可調,弧比、轉速0~100%連續(xù)可調。電極材料為$2 mm的Ni201,主要化學成分(質量分數(shù))見表1基體材料為Q235鋼,沉積時基體試樣尺寸為50 mm×50 mm×10 mm。實驗前,先用400目砂紙將基體待沉積面的氧化層除去,再用丙酮溶液對基體進行清洗去污并風干,依據沉積設備使用說明書,按照表2中的沉積工藝參數(shù)進行電火花沉積,沉積時電極伸出沉積槍的長度為10 mm。
表1 電極材料的主要化學成分(質量分數(shù)) %

表2 沉積工藝參數(shù)
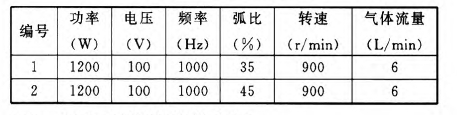
1.2 Q235鋼焊接性能分析
基體Q235鋼的化學成分如表3所示,根據國際焊接學會(IIW)推薦的碳當量公式:
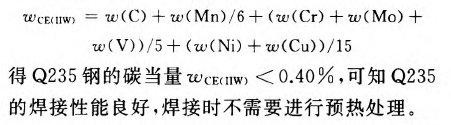
表3 Q235鋼的主要化學成分(質量分數(shù)) %

1.3 實驗方法
修復層制備完成后,利用線切割將沉積試樣制成10 mm×10 mm×10 mm的檢測試樣,依次分別用800、1500、3000目的砂紙和金相拋光機將檢測試樣橫截面拋光至光亮的鏡面。對于用于金相組織觀察的試樣,其基體Q235鋼部分用4%的硝酸酒精溶液腐蝕,Ni201修復層部分用王水腐蝕。對于用于其他檢測項目的試樣,最后統(tǒng)一用4%的硝酸酒精溶液腐蝕,以備檢測。
采用MLA650F型掃描電子顯微鏡(SEM)對修復層與基體結合界面的顯微組織進行觀察分析,結合能譜儀(EDX)分析修復層元素分布情況,采用Empyrean型X射線衍射儀對修復層物相成分進行分析。
2. 實驗結果與討論
2.1 修復層界面形貌分析
電火花沉積參數(shù)弧比取值35%和45%時所獲得的修復層界面形貌分別如圖1a和圖1b所示。由圖1a可以看出,修復層光滑致密,沒有細微的孔洞、裂縫等微觀缺陷,修復層與基體緊密結合。圖1b則表現(xiàn)出明顯的修復缺陷,結合界面處的基體一側存在一條顯微裂縫(約3~5μm),這可能是由于多次單點沉積后釋放的熱量產生的熱應力經疊加后超過基體強度導致的。由于修復層制備完成后基體殘余熱量的大小是由沉積過程中單次微弧脈沖放電釋放的能量決定的,而單次微弧脈沖放電釋放的能量大小與弧比取值大小有關,弧比代表的是微弧放電時間長短的百分比,因此隨著弧比取值的增大,微弧放電時問得到延長,電極與基體每次接觸釋放的能量增加,多次單點沉積后對基體的累積熱輸入量也隨之增加,導致熱應力增大,當熱應力大小超過基體自身的強度時,將會在靠近熔合線的基體一側產生顯微裂紋。因此修復層質量的好壞與電火花沉積時弧比取值范圍的控制緊密相關。由以上分析可知,在Q235鋼表面沉積Ni201修復層時,弧比取值應在35叱左右.不宜韶討45%。
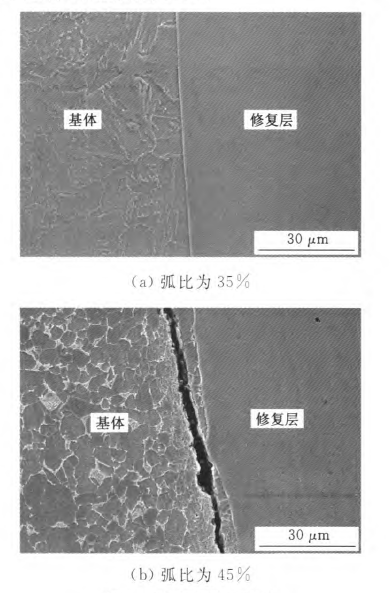
圖1 修復層界面形貌
2.2 結合界面顯微組織分析
以下均為其他參數(shù)不變的情況下,弧比取值為40%時獲得的實驗結果。圖2所示為基體Q235的金相組織,可看出,組織中主要分布著片狀鐵素體和珠光體,由于放大倍數(shù)較小(20倍),因此珠光體呈現(xiàn)為一團黑色。圖3所示為電火花沉積Ni201的修復層組織,主要是呈柱狀晶形態(tài)的鑄態(tài)組織,其中含有少量的夾雜。圖4所示為弧比取值40%時得到的修復層結合界面。由結合界面宏觀形貌(圖4a)可看出,修復層與基體結合緊密,結合處沒有出現(xiàn)縫隙等熔合缺陷,基體一側零星分布著一些黑色物質,這是沉積過程中析出的碳化物因腐蝕過度而變黑。圖4b為電火花沉積Ni201修復層與基體結合處
橫截面的SEM照片,可看出,在修復層區(qū)域,修復
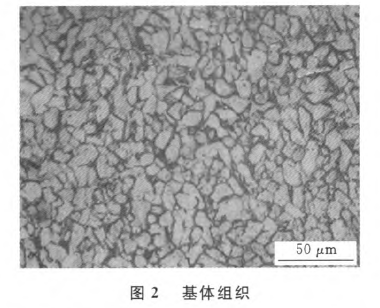
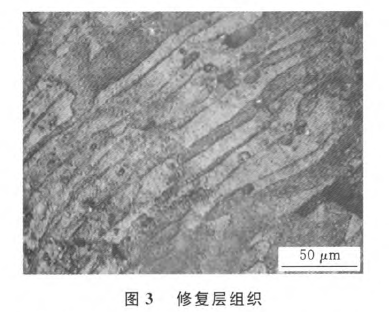
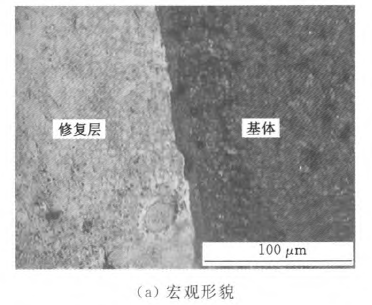
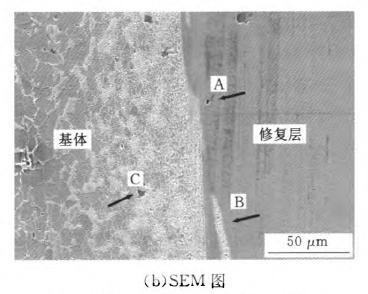
圖4 修復層橫截面圖(弧比40%)
層組織均勻致密,部分區(qū)域留有少量拋磨的劃痕,沒有明顯被酸腐蝕的痕跡,與基體相比,修復層的耐腐蝕性較好,由于修復層中的主要元素為Ni,容易被鈍化形成鈍化膜,所以可有效降低腐蝕敏感性,提高被修復零件的抗腐蝕性。
修復層區(qū)域A處是電火花沉積過程中形成的微小孔洞(約1 gm),可能與下面兩個因素有關:一是沉積時電極材料與基體接觸瞬間產生的高溫將電極和基體材料熔化甚至汽化,保護氣體流量在某一時刻的不穩(wěn)定可能導致空氣溶解于熔融的金屬中,在迅速凝固過程中,空氣沒有及時排出導致形成微小氣孔;另一因素是受到電火花沉積加熱、熔化、凝固過程中產生的拉伸熱應力影響,導致產生微孔。經4%的硝酸腐蝕后,區(qū)域B的組織結構與基體相同,電火花沉積時,在脈沖放電瞬間釋放的高密度能量的作用下,放電區(qū)域中的電極材料和基體材料被熔融成流體金屬,并相互熔合,冷卻之后形成區(qū)域B的組織結構,由此說明電火花沉積是電極材料與基體材料合金熔合的過程。從圖4b中可以看出,部分區(qū)域出現(xiàn)低于基體原始界面的不規(guī)則熔合線,由于沉積過程采用人工手持沉積槍操作,不可避免地在一些微小區(qū)域發(fā)生脈沖放電能量不均勻的情況,導致基體表面熔化程度不同,因此熔合線并非理想的直線。熔合線靠近基體一側出現(xiàn)密集而又細小的白色晶體組織,由于基體中的鐵素體受到電火花微弧放電瞬間產生高溫的影響,發(fā)生再結晶現(xiàn)象,故而使得此處的組織被細化而形成了細小的晶體組織,該組織可以起到改善基體硬度和強度的作用。從圖4b還可以看出,基體部分也出現(xiàn)了少量的微孔(區(qū)域C),C處的微孔形成原因不同于修復層A處,電火花沉積在冷卻凝固階段的冷卻速率約為105K/s,由于快速冷卻,在沉積過程中會有少量的元素偏析,使已凝固部分的晶界前沿生長受到阻礙,導致基體產生微小孔洞。
2.3 結合界面主要元素分布
圖5所示為電火花沉積層界面結合處主要元素的線掃描能譜結果,掃描長度為41,am,可以看出Fe、Ni、Co三種主要元素相互擴散明顯,元素的質量分數(shù)呈梯度變化的趨勢,主要元素的質量分數(shù)的梯度分布表明修復層與基體的結合方式為冶金結合。元素Fe的質量分數(shù)由修復層到基體逐漸增大,說明Fe主要是由基體向修復層擴散,而在修復層中Fe的質量分數(shù)也很高,可能是由于沉積過程中產生的高溫使沉積點處的基體處于熔融狀態(tài),當旋轉電極與基體接觸時,部分液態(tài)基體金屬附著凝固在電極表面形成一層包裹層,一方面阻礙了電極元素向基體擴散,另一方面也使得元素Fe隨著電極材料沉積到修復層中,導致Fe元素在修復層中的質量分數(shù)較高。元素Ni的質量分數(shù)由修復層到基體逐漸減小,說明Ni主要是由修復層向基體方向擴散,在深入基體一定距離時,Ni元素的質量分數(shù)減小到2%左右,雖然這些元素在基體與修復層都有分布,但分布區(qū)域很小,這是由于沉積時基體與修復層材料熔合區(qū)域的溫度雖然很高,但大部分熱量是通過基體釋放,冷卻凝固的速度極快,導致元素擴散不夠充分。Co元素分布的變化不明顯,由于沉積過程中作為溶質的Co金屬半徑(o.125 nm)與溶劑Fe金屬半徑(0.126 nm)接近,兩者易于形成置換固溶體,產生固溶強化作用,因此在基體與修復層中都分布著一定質量分數(shù)的Co元素。元素Fe和Ni的線掃描曲線在熔合線靠近修復層一側出現(xiàn)了一段狹小的緩沖平臺區(qū)域,由此表明在界面結合處必然存在一個修復層與基體熔合的過渡區(qū),過渡區(qū)域的存在證明沉積過程中基體元素與修復層元素之間確實發(fā)生了相互擴散的現(xiàn)象。結合元素質量分數(shù)變化曲線與電火花沉積的特點分析,過渡區(qū)域的形成可能與修復層被基體元素稀釋和熔融合金快速凝固有關。
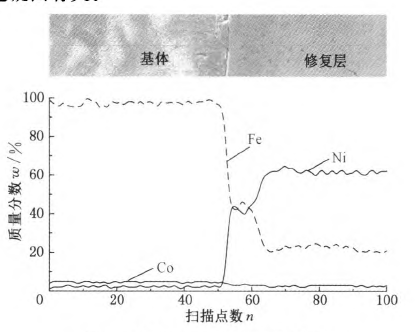
圖5結合界面兀素線掃描結果
2.4修復層界面的物相分析
對Ni201修復層與基體的結合界面進行X射線衍射分析,結果如圖6所示。分析圖中物相衍射峰可知,修復層界面結合處主要由Fel9Ni和C03Fe7以及少量CO.055Fel.945和FeO.9Si0.1等相組成。CO.055Fel.945相的產生可以證明在修復層界面處有馬氏體相的存在。修復層中含有的過渡族元素Fe與Si形成的硬質相FeO.9Si0.1可以提高修復層的硬度。在電火花沉積過程中,作為電極材料的Ni201與基體Q235鋼表面接觸瞬間會產生5000~25 ooo K的高溫,電極與基體在高溫的作用下熔化,此時在結合界面處的基體一側會有大量的Fe元素隨著熔化的過程擴散到熔融的電極材料中,在凝固階段,基體與修復層結合界面處形成了大量的Fel9Ni、C03Fe7與少量的FeO.9Si0.1,可以幫助改善基體Q235鋼的耐蝕性能。經分析,上述新相的存在證明電極材料中的元素與基體元素發(fā)生了冶金化學反應。這個過程中可能發(fā)生的主要反應方程式如下:
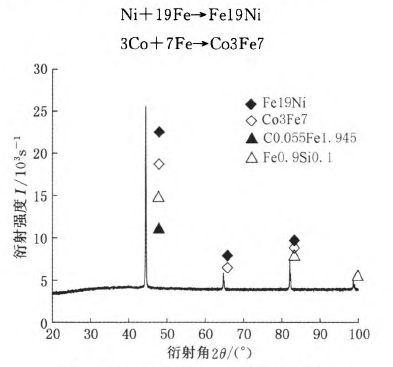
圖6修復層結合界面XRD衍射圖
可見,沉積到Q235基體上的Ni201修復層,兩者不僅微觀組織發(fā)生了變化,而且也發(fā)生反應形成了新的產物,說明Ni201修復層不是在Q235基體表面簡單的機械堆積,由此也證明Ni201修復層與基體Q235鋼的主要結合方式為冶金結合。
3. 結論
(1)電火花沉積Ni201改性修復層,弧比取值35%時,修復層與基體結合緊密,修復層界面熔合線處實現(xiàn)光滑過渡,無明顯修復缺陷;而弧比取值45%時,結合界面處出現(xiàn)明顯沉積裂紋。弧比取40%時,修復層界面狀況與弧比取值35%時相似,修復層組織均勻致密,修復層組織為柱狀晶形態(tài)。
(2)修復層與基體結合處發(fā)生了以元素Fe和Ni為主的相互擴散現(xiàn)象,表明電火花沉積是一個合金熔合的過程。
(3)Fel9Ni、C03Fe7及少量CO.055Fel.945和硬質相FeO.9Si0.1等新相的產生,說明Ni201修復層與Q235基體中的元素發(fā)生了冶金反應,修復層為冶金結合層。
投稿箱:
如果您有機床行業(yè)、企業(yè)相關新聞稿件發(fā)表,或進行資訊合作,歡迎聯(lián)系本網編輯部, 郵箱:skjcsc@vip.sina.com
如果您有機床行業(yè)、企業(yè)相關新聞稿件發(fā)表,或進行資訊合作,歡迎聯(lián)系本網編輯部, 郵箱:skjcsc@vip.sina.com
更多相關信息
業(yè)界視點
| 更多
行業(yè)數(shù)據
| 更多
- 2025年1月 新能源汽車銷量情況
- 2024年12月 新能源汽車產量數(shù)據
- 2024年12月 基本型乘用車(轎車)產量數(shù)據
- 2024年12月 軸承出口情況
- 2024年12月 分地區(qū)金屬切削機床產量數(shù)據
- 2024年12月 金屬切削機床產量數(shù)據
- 2024年11月 金屬切削機床產量數(shù)據
- 2024年11月 分地區(qū)金屬切削機床產量數(shù)據
- 2024年11月 軸承出口情況
- 2024年11月 基本型乘用車(轎車)產量數(shù)據
- 2024年11月 新能源汽車產量數(shù)據
- 2024年11月 新能源汽車銷量情況
- 2024年10月 新能源汽車產量數(shù)據